Ever wonder about the first-time computers were used to manage phone calls? Have Nancy get you to dreaming as you learn about Bell Labs Electronic Switch
THE ELECTRONIC SWITCHING SYSTEM
Straiey, n. vw
The Electronic Switching System
TRIAL INSTALLATION, MORRIS, ILLINOIS
GENERAL DESCRIPTION
Strafey, H. Dean
Switching Systems Development Department
BELL TELEPHONE LABORATORIES, INCORPORATED
WHIPPANY, NEW JERSEY
X-63940
PRIVATE EDITION
Copy No. ^ 9 ^
This book is for the use of Bell System employees
only, and no portion thereof shall be reproduced
in any form without the written permission of
Bell Telephone Laboratories, Incorporated
PRINTED IN THE UNITED STATES OF AMERICA
APRIL 1960
Preface
An electronic switching system employs principles and techniques that are
new to telephony. The fundamental objectives are the same as for any dial
telephone system, namely, to enable customers to make their calls quickly,
accurately, and economically. Achieving these objectives by electronic rather
than by electromechanical means, however, involves the use of certain new
devices that in many instances replace the familiar relays and other components
of previous switching systems.
The electronic switching system (ESS) in Morris, Illinois, is a Laboratories
trial installation of the first Bell System all-electronic central office to provide
customers with dial telephone service. As with any new system, this trial pre-
sents many problems. One of these is the question of how to give maintenance
people an understanding of the new concepts introduced.
The ESS can diagnose most of its own troubles and can identify the sources
of trouble. But it still needs a maintenance staff well trained in the basic prin-
ciples of the system. This book constitutes part of the educational material
required for training such a staff; it is intended to be used as the text for the
ESS plant training courses to be given by the Illinois Bell Telephone Company.
The study of this book will prepare the maintenance craftsman for on-the-job
training in the new method of simplified maintenance used in the ESS.
This book gives a general description of the ESS, and tells how electronic
switching resembles and how it differs from electro-mechanical switching. It
describes the apparatus elements used, and shows how they operate indivi-
dually and together. It explains the respective functions and operations of the
major components and of the power equipment. It traces the progress of calls
through the system, telling how the customer's dialed instructions are analyzed
and carried out. In short, this book presents a perspective of the principles,
equipment, and operation of electronic switching.
The material in this book is presented in the order considered most suitable
for learning and understanding how ESS works. Chapter I, An Introduction to
the Morris Electronic Switching System, gives a broad over-all view of the ESS
vi Preface
installed in Morris. It describes features and arrangements that are common
to most of the equipment in the system. Chapter 2, Method of Operation, tells
how various calls are handled by tracing their progress through the system
and describing briefly the functions of the circuit units encountered. The chap-
ters that follow give more details about the operation of separate circuit units,
as well as information on power supplies and maintenance. The new technical
terms that are introduced and explained in the course of the text are sum-
marized and again defined in the Appendix, which constitutes a glossary.
The electronic switching system was developed through the cooperation of
many people whose contributions are recognized elsewhere. Appropriate ac-
knowledgment should also be made to those who prepared this book. Some of
the material here is original; the rest was gathered from numerous sources. All
of it was compiled under the supervision of George H. Duhnkrack, whose
co-authors included Robert E. Eberhardt and Darwin T. Osmonson of the
Illinois Bell Telephone Company as well as Francis J. Herron, John N.
Mackessy, John V. Pinney, Frederick J. Raile, and Earl R. Williams, all of
Bell Telephone Laboratories. The authors are in turn indebted to those
anonymous scientists, engineers, and other counselors whose penetrating and
constructive comments added to the accuracy of the text.
The typography, printing, and binding were handled by Kenneth M. Collins.
The ESS emblem on the title page was based on a design suggested by Sih Hsuin
Tsiang. It was selected from many ingenious devices proposed.
It is hoped that the general description of the ESS presented in this book
will form the background for a more detailed study of electronic switching.
This volume itself is an integral portion of the training program for the Morris
trial installation. Your comments on the book will be appreciated and will help
in the preparation of training material for electronic switching systems of
the future.
CLARENCE A. LOVELL
Director of Switching
Systems Development
Whippany, New Jersey
January I960
Contents
CHAPTER 1
An Introduction to the Morris Electronic Switching
FIG. 1-1. Location of the Morris ESS
TABLE 1-1. Customer services to he provided in the Morris ESS
1.1 THE ESS COMPARED WITH NO. 5 CROSSBAR
TABLE 1-2. Features to be provided in the Morris ESS
FIG. 1-2. The ESS trunking plan ....
TABLE 1-3. New techniques introduced in the Morris ESS
1.2 FUNCTIONS OF THE MAJOR COMPONENTS
1.2.1 The Scanner
FIG. 1-3. ESS equipment schematic
FIG. 1-4. Scanner connections to lines and trunks
1.2.2 The Signal Distributor
1.2.3 The Barrier Grid Store
1.2.4 The Flying Spot Store
1 .2.5 The Switching Networks .....
FIG. 1-5. Switching network plan
1 .2.6 The Central Control
1.2.7 The Stand-By Transfer
1 .2.8 The Administration Center .....
TABLE 1-4. Functions of the Administration Center .
1 .2.9 The Announcement System .....
FIG. 1-6. Floor plan for the Morris ESS .
1.3 EQUIPMENT ARRANGEMENTS ....
1.3.1 Cabinet Design .......
FIG. 1-7. Front view of cabinet line-up .
FIG. 1-8. Front view of marker and network cabinets
1.3.2 Wiring and Local Cabling .
Page
1
System
Page
2
Page
2
Page
i
Page
3
Page
4
Page
5
Page
5
Page
5
Page
6
Page
7
Page
8
Page
8
Page
9
Page
10
Page
11
Page
12
Page
12
Page
13
Page
13
Page
13
Page
14
Page
14
Page
15
Page
15
Page
16
Page
17
VII
Vlll
1.4 APPARATUS ELEMENTS ....
1.4.1 Circuit Packages . .
1.4.2 Connectors
1.4.3 Locating Packages .....
FIG. 1-9. Typical circuit packages .
FIG. 1-10. Circuit package co-ordinate system
1.4.4 Electron Tubes
FIG. 1-11. Gas diode crosspoint
FIG. 1-12. Gas diode module
FIG. 1-13. Gas tetrode ....
1.4.5 Inventory of Major Apparatus Elements
TABLE 1-5. Inventory of major apparatus elements
1.5 POWER EQUIPMENT
1.5.1 Motor Alternators— Source of A-C Power
FIG. 1-14. Motor-alternator set with d-c and a-c drive motors
and fly wheel ....
FIG. 1-15. A-C power plant ....
1.5.2 A-C Distribution for D-C Power Supplies
FIG. 1-16. Primary a-c distribution
FIG. 1-17. Diesel engine alterator .
FIG. 1-18. A-C distribution for d-c power supplies
FIG. 1-19. 48-volt d-c power distribution
1.5.3 Tone Power Supplies .....
FIG. 1-20. Connection of audible ringing tone generator to
the signal switching network .
FIG. 1-21. Connection of dial, busy, and re-order tone generator
the tone points in the distribution switching network
TABLE 1-6. Tone power supplies
FIG. 1-22. Tone ringer power supplies
1.5.4 Tone Ringing Power Supplies
1.6 STATION SETS
FIG. 1-23. Low-current tone ringer telephone set
FIG. 1-24. Telephone set, internal view .
FIG. 1-25. Sound radiator ....
1.7 TESTING AND MAINTENANCE PHILOSOPHY
to
Contents
Page
17
Page
18
Page
18
Page
19
Page
19
Page
20
Page
21
Page
21
Page
22
Page
23
Page
23
Page
24
Page
24
Page
25
Page
25
Page
26
Page
26
Page
27
Page
27
Page
28
Page
28
Page
29
Page 29
Page 29
Page 30
Page 30
Page 31
Page 31
Page 31
Page 32
Page 32
Page 33
Contents
chapter 2
Method of Operation
FIG. 2-1. Connections for dial tone and for dialing .
FIG. 2-2. Connections for an intraoffice call, showing the paths
for regular ringing, audible ringing, and talking
FIG. 2-3. Connections for a reverting call: ringing and
talking paths ......
FIG. 2-4. Talking connection for an operator call or an
outgoing call ......
FIG. 2-5. Connections for an incoming call, showing the paths for
regular ringing, audible ringing, and talking
FIG. 2-6. Skew ringing and talking connections for an intraoffice
call or an incoming call .....
2.1 ESTABLISHING THE DIALING CONNECTION- FIG. 2-7
FIG. 2-7. Establishing a dialing connection
2.1.1 Dial Tone Connection -Fig. 2-7 .
2.1.2 Dialing Connection
2.2 INTRAOFFICE CALL- FIG. 2-8
FIG. 2-8. Establishing an intraoffice call
2.3 REVERTING CALL- FIG. 2-9 .
FIG. 2-9. Establishing a reverting call
2.4 OUTGOING CALL- FIG. 2-10
FIG. 2-10. Establishing an outgoing call
2.5 INCOMING CALL-FIG. 2-11 .
FIG. 2-11. Establishing an incoming call
2.6 CALLS TO THE 3GL SWITCHBOARD- FIG. 2-12
2.6.1 Recording-Completing (Zero Operator)
FIG. 2-12. Establishing calls to the 3CL switchboard
2.6.2 Permanent Signals
2.6.3 Partial Dial ....
2.6.4 Vacant Codes ....
2.6.5 Denied Service ....
IX
Page
35
Page
36
Page
37
Page
38
Page 39
Page 40
Page 41
Page 42
Page 43
Page 44-
Page 45
Page 46
Page 46
Page 48
Page 49
Page 50
Page 51
Page 52
Page 53
Page 55
Page 55
Page 56
Page 59
Page 60
Page 60
Page 60
CHAPTER 3
The Switching Networks
FIG. 3-1. A typical 3-by-3 switch and a typical 10-by-10 switch .
FIG. 3-2. Four-stage network wiring pattern ....
3.1 THE DISTRIBUTION SWITCHING NETWORK
FIG. 3-3. Distribution switching network, six-stage wiring pattern
FIG. 3-4. Junctor slip wiring pattern: A, Frame 0; B, Frame 1;
C, Frame 2 .
TABLE 3-1. Formula for junctor slip pattern
FIG. 3-5. Distribution switching network, wiring pattern .
3.2 CONCENTRATION SWITCHING NETWORK .
FIG. 3-6. Concentration switching network, 40-by-10 switch
3.3 SIGNAL SWITCHING NETWORK .
3.4 EQUIPMENT ARRANGEMENTS
3.4.1 Switching Networks .....
FIG. 3-7. Switching networks cabinet, front view
FIG. 3-8. Office concentrator line terminal package
FIG. 3-9. Junctor package ....
TABLE 3-2. Packages used in the switching networks
FIG. 3-10. Crosspoint module
FIG. 3-11. 2-by- 10 crosspoint module
FIG. 3-12. Switching networks cabinet, front equipment
FIG. 3-13. External wiring to switching networks cabinet .
FIG. 3-14. Switching networks cabinet, rear equipment
FIG. 3-15. Switching networks cabinet, rear view
TABLE 3-3. Typical assignment of trunks on the distribution
switching network .....
3.4.2 Distributing Frames . . . .
FIG. 3-16. Trunk distributor
3.5 METHOD OF OPERATION
3.5.1 Establishing a Talking and Signaling Path in the Concentration
Switching Network
FIG. 3-17. Talking and signaling path through concentration
switching network .....
Contents
Page
61
Page
62
Page
63
Page
64
Page
64
Page
66
Page
67
Page
68
Page
69
Page
69
Page
70
Page
70
Page
70
Page
71
Page
72
Page
73
Page
74
Page
75
Page
75
Page
76
Page
77
Page
78
Page
79
Page
80
Page
81
Page
82
Page
83
Page
83
Page
84
Contents
XI
3.5.2 Establishing a Talking and Signaling Path in the Distribution
Switching Network .......
FIG. 3-18. Talking and signaling path through distribution
switching network .....
FIG. 3-19. Ringing trunk connection ....
FIG. 3-20. Talking connection .....
3.5.3 Establishing a Signaling Path in the Signal Switching Network
FIG. 3-21. Signaling path through ringing switch
FIG. 3-22. Talking path through skew ringing trunk
3.6 POWER
3.6.1 Power Requirements ....
3.6.2 Power Equipment ....
FIG. 3-23. Power supplies and their outputs
FIG. 3-24. Voltage divider . .
FIG. 3-25. Voltage divider assembly
FIG. 3-26. Power cabinets for distribution switching network and
distribution markers and 1; front view
FIG. 3-27. Individual power supply, front view .
FIG. 3-28. Individual power supply, internal view
FIG. 3-29. Power panel for distribution switching network and
distribution markers and I; front equipment .
FIG. 3-30. Power cabinets for concentration network, signal switching
network, and concentration markers and I; front view
3.7 MAINTENANCE
3.7.1 No-Connection Test
3.7.2 Low-Breakdown Test
Page 85
Page
86
Page
88
Page
88
Page
89
Page
90
Page
91
Page
92
Page
92
Page
92
Page
93
Page
94
Page
94
Page
95
Page
96
Page
96
Page 98
Page 99
Page 100
Page 100
Page 101
CHAPTER 4
Concentration and Distribution Markers
4.1 INTRODUCTION TO THE CM AND DM OPERATIONS
FIG. 4-1. Marker cabinets, front view . . . . .
4.1.1 Dial Tone Connections
4.1.2 The Ringing Connections ......
Page 102
Page 103
Page 103
Page 103
Page 105
Xll
Contents
4.1.3 The Called Customer Answers .....
4.1.4 Disconnect ........
4.2 EQUIPMENT ARRANGEMENTS
FIG. 4-2. Mounting arrangements for the \ l /i-inch packages
4.2.1 Apparatus Elements .......
4.2.2 Apparatus Mounting Arrangements— Figs. 4-2 and 4-3 .
4.2.3 Cabinet Layout of the Concentration Marker
FIG. 4-3. Mounting arrangements for the 1-inch packages, seen
from below .......
FIG. 4-4. Miscellaneous marker apparatus
FIG. 4-5. Concentration marker, front view
FIG. 4-6. Concentration marker, front equipment
FIG. .4-7. Concentration marker, rear equipment
4.2.4 Cabinet Layout of the Distribution Marker .
FIG. 4-8. Distribution marker, front view
FIG. 4-9. Distribution marker, front equipment
FIG. 4-10. Distribution marker, rear equipment
4.2.5 Cabinet Doors and Gates ......
4.2.6 Power Supply Cabinets
4.3 METHOD OF OPERATION OF THE CONCENTRATION MARKER
4.3.1 Network Orders
TABLE 4-1. Typical switching network orders to the markers
4.3.2 Functions of CM Circuits (Fig. 4-11) ....
TABLE 4-2. Functions of the circuits in the CM
4.3.3 Sequence Control, or 1 Marker (Fig. 4-11) .
FIG. 4-11. Concentration marker, block diagram
4.3.4 Line Selector Control, or 1 Marker (Fig. 4-11)
4.3.5 Line Selector, or 1 Marker (Fig. 4-11)
4.3.6 Line Selector Verifier, or 1 Marker (Fig. 4-11)
4.3.7 Trunk Level Enabler, or 1 Marker (Fig. 4-11)
4.3.8 Trunk Level Identifier and Match Detector, or 1 Marker
(Fig. 4-11)
4.3.9 Trunk Release Selector Control, or 1 Marker (Fig. 4-11)
4.3.10 Trunk Release Selector, or 1 Marker (Fig. 4-11)
Page
Page
Page
Page
Page
Page
Page
Page
Page
Page
Page
Page
Page
Page
Page
Page
Page
Page
Page
Page
Page
Page
Page
Page
Page
Page
Page
Page
Page
Page
Page
Page
Contents
xni
4.4 METHOD OF OPERATION OF THE DISTRIBUTION MARKER . Page 130
4.4.1 Functions of the DM Circuits (Fig. 4-12) Page 130
4.4.2 Sequence Control, or 1 Marker (Fig. 4-12) Page 130
TABLE 4-3. Functions of the circuits in the DM .... Page 131
FIG. 4-12. Distribution marker, block diagram .... Page 132
4.4.3 Trunk Selector Control, A or B Side, or 1 Marker (Fig. 4-12). . Page 138
4.4.4 Trunk Selector, A or B Side, or 1 Marker (Fig. 4-12) . . . Page 138
4.4.5 Trunk Identifier, A or B Side, or 1 Marker (Fig. 4-12) . . Page 139
4.4.6 Propagator Pulser, A or B Side, or 1 Marker (Fig. 4-12) . . Page 140
4.4.7 Junctor Enabler, or 1 Marker (Fig. 4-12) Page 140
4.4.8 Junctor Release Pulser, or 1 Marker (Fig. 4-12) .... Page 141
4.5 METHOD OF OPERATION OF MISCELLANEOUS CIRCUITS . Page 142
4.5.1 Marker Transfer Circuit— Distribution Marker .... Page 142
4.5.2 Marker Transfer Circuit— Concentration Marker .... Page 142
4.5.3 Power Interrupter Circuit-Interlocks— Distribution Marker . . Page 142
4.5.4 Power Interrupter Circuit-Interlocks— Concentration Marker . . Page 143
4.5.5 Trouble Detectors or 1, Concentration Marker (Fig. 4-13) . . Page 143
FIG. 4-13. Concentration marker, block diagram of trouble detector . Page 143
FIG. 4-14. Distribution marker, block diagram of trouble detector . Page 144
4.5.6 Trouble Detectors or 1, Distribution Marker (Fig. 4-14) . . Page 145
4.6 MAINTENANCE Page 145
CHAPTER 5
The Scanner
5.1 EQUIPMENT ARRANGEMENTS
FIG. 5-1. Scanner, front view.
FIG. 5-2. Scanner, rear view .
FIG. 5-3. Scanner equipment .
5.2 METHOD OF OPERATION
TABLE 5-1. Equipment designations
FIG. 5-4. Sequence of scanning modes
FIG. 5-5. Scanning cycle
FIG. 5-6. Matrix of transmission gates
FIG. 5-7. Scanner block diagram .
FIG. 5-8. Input selector
Page 147
Page 147
Page 148
Page 149
Page 150
Page 150
Page 151
Page 152
Page 153
Page 153
Page 154
Page 156
XIV
Contents
FIG. 5-9. Input translator
FIG. 5-10. Operation of gate matrix
FIG. 5-11. Output selector
FIG. 5-12. Output translator .
5.3 DUPLICATION AND TRANSFER .
FIG. 5-13. Circuit identification marking {tracking voltage
FIG. 5-14. Circuit identification marking {transfer units)
FIG. 5-15. Circuit identification marking {output amplifiers
and transfer)
FIG. 5-16. Scanner transfer .
5.4 POWER
FIG. 5-17. Scanner power equipment, SC-0
FIG. 5-18. Scanner power equipment, SC-1
FIG. 5-19. Power supply, —50 volts
TABLE 5-2. Scanner power distribution .
FIG. 5-20. Power supplies and paralleling units
FIG. 5-21 . Relay contact patching .
5.5 MISCELLANEOUS
5.6 MAINTENANCE
TABLE 5-3. Packages used in the scanner
regulators)
Page 157
Page 158
Page 160
Page 162
Page 162
Page 163
Page 163
Page 164
Page 165
Page 166
Page 166
Page 167
Page 168
Page 169
Page 170
Page 170
Page 171
Pa^e 171
Page 172
CHAPTER 6
77ze Stand-By Transfer
6.1 GENERAL
6.2 EQUIPMENT ARRANGEMENTS
FIG. 6-1. ESS transfer paths
FIG. 6-2. Stand-by transfer, front view ....
FIG. 6.3. Stand-by transfer, front equipment, Bay and Bay 2
FIG. 6-4. Stand-by transfer, rear view ....
FIG. 6-5. Stand-by transfer, rear equipment, Bay 3 and Bay 1
TABLE 6-1. Packages used in the stand-by transfer .
6.3 POWER
6.4 MAINTENANCE
Page 174
Page 174
Page 176
Page 176
Page 178
Page 179
Page 180
Page 181
Page 182
Page 182
Page 183
Contents
xv
CHAPTER 7 Page 185
The Signal Distributor
7.1 EQUIPMENT ARRANGEMENTS Page 185
FIG. 7-1. Signal distributor, functional diagram .... Page 186
TABLE 7-1. Operations directed by signal distributor outputs . . Page 186
FIG. 7-2. Signal distributor, front view and front equipment . . Page 187
FIG. 7-3. Signal distributor, rear view and rear equipment . . . Page 188
TABLE 7-2. Packages used in the signal distributor . . . Page 189
F\G. 7-4. Signal distributor, block diagram Page 190
7.2 METHOD OF OPERATION Pa^e 190
7.2.1 General Description of Operation Page 190
7.2.2 Selector Drive A or B Page 191
7.2.3 Matrix (Flip-Flop Groups 00 through 31) . Page 192
FIG. 7-5. Matrix, FF Groups 00 through 31 Page 193
FIG. 7-6. Typical output from a point assigned to an outgoing trunk . Page 194
7.3 DUPLICATION AND TRANSFER Page 194
FIG. 7-7. Signal distributor, transfer of duplicated equipment . . Page 194
7.4 POWER Page 195
7.5 MISCELLANEOUS Page 196
CHAPTER 8
The Barrier Grid Store
8.1 DESCRIPTION OF THE BARRIER GRID STORE .
FIG. 8-1. Central control and barrier grid store interconnections
8.2 EQUIPMENT ARRANGEMENTS ....
8.2.1 BGS-0, Front Bay (Fig. 8-2) ....
FIG. 8-2. Barrier grid store and power cabinets, front view
FIG. 8-3. Barrier grid store, gate bay
8.2.2 BGS-0, Rear Bay (Fig. 8-4)
FIG. 8-4. Barrier grid store, rear equipment
8.2.3 BGP-0, Front Bay
TABLE 8-1 . Packages used in each barrier grid store
Page 198
Page 198
Page 199
Page 199
Page 199
Page 200
Page 201
Page 202
Page 202
Page 202
Page 203
XVI
Contents
8.3 APPARATUS ELEMENTS Page 203
8.3.1 The Barrier Grid Tube (BGT) Page 203
FIG. 8-5. Barrier grid tube Page 203
FIG. 8-6. Barrier grid tube elements ...... Page 204
FIG. 8-7. Barrier grid tube and read pre-amplifier .... Page 204
8.3.2 The Raster Reference Tube (RRT) Page 205
FIG. 8-8. Raster reference tube Page 205
FIG. 8-9. Raster reference tube elements ...... Page 206
FIG. 8-10. Relation of reference edges in RRT to raster in BGT . . Page 206
8.4 METHOD OF OPERATION OF THE BGS Page 207
FIG. 8-11. Barrier grid storage unit, rear view . .... Page 201
8.4.1 Address and Beam Positioning ....... Page 207
FIG. 8-12. Barrier grid store, control circuits ..... Page 208
FIG. 8-13. Barrier grid store, vertical address and deflection circuits . Page 209
8.4.2 The Sequence Control Page 209
FIG. 8-14. Barrier grid store, sequence control . .... Page 210
FIG. 8-15. Barrier grid store, operation cycle ..... Page 210
8.5 REGISTERS Page 211
TABLE 8-2. Registers in the barrier grid stores .... Page 212
FIG. 8-16. Barrier grid store, register layout LRT-0 . . . . Page 21 4
FIG. 8-17. Barrier grid store, register layout LRT-1 . ■ . . . Page 215
FIG. 8-18. Barrier grid store, normal operating mode . . . Page 216
FIG. 8-19. Barrier grid store, operating modes under
various abnormal conditions ...... Page 217
8.5.1 Register Description Page 217
TABLE 8-3. Line spot memory assignments ..... Page 218
TABLE 8-4. System action during supervisory scan of lines . . Page 218
TABLE 8-5. Trunk spot memory assignments ..... Page 219
8.6 POWER Page 223
8.6.1 Power Control Page 223
8.6.2 Rectifier Units Page 224
8.7 MAINTENANCE Page 224
Contents xvii
CHAPTER 9 Page 226
The Flying Spot Store
9.1 THE FSS INFORMATION SYSTEMS Page 226
FIG. 9-1. Flying spot store information channel .... Page 221
9.2 THE SYSTEM PROGRAM Page 227
FIG. 9-2. Main program sequences . ...... Page 230
FIG. 9-3. Order word structure ....... Page 234
9.3 EQUIPMENT ARRANGEMENTS Page 235
9.3.1 Cabinet FSS-0, Front Bays (Fig. 9-4) Page 235
TABLE 9-k Order coding Page 236
TABLE 9-2. Packages used in each FSS Page 239
FIG. 9-4. Flying spot store, front view ...... Page 240
9.3.2 Cabinet FSS-0, Rear Bays (Fig. 9-5) Page 241
FIG. 9-5. Flying spot store, rear view ...... Page 241
9.3.3 Cabinet FSS-0, Bay 6 (Fig. 9-6) Page 242
FIG. 9-6. Flying spot store, end view ...... Page 243
FIG. 9-7. Flying spot store manual control and meter panels . . Page 244
9.3.4 Cabinet FSS-0, Bay 0; Manual Control and Meter Panel (Fig. 9-7) . Page 244
9.4 APPARATUS ELEMENTS Page 245
9.4.1 The Optics System Page 245
FIG. 9-8. Flying spot store multiple information channels . . . Page 246
FIG. 9-9. Flying spot store optics system elements .... Page 246
FIG. 9-10. Flying spot store CRT and vertical shutter assembly . . Page 247
FIG. 9-11. Flying spot store lens and plate assembly . . . . Page 248
FIG. 9-12. Horizontal shutter and code plate assembly . . . Page 249
FIG. 9-13. Flying spot store photomultiplier assignments . . . Page 250
9.4.2 The Photomultiplier Tube Page 251
FIG 9-14. Photomultiplier tube, schematic diagram .... Page 251
9.5 METHOD OF OPERATION Page 252
9.5.1 Major Functional Units of the FSS (Fig. 9-16) .... Page 252
FIG. 9-15. Flying spot store and central control interconnections . . Page 252
FIG. 9-16. Flying spot store block diagram ..... Page 253
9.5.2 Address and Beam-Positioning Circuits (Fig. 9-17) .... Page 253
FIG. 9-17. Flying spot store horizontal address and position circuits . Page 254
FIG. 9-18. Flying spot store servo code plates ..... Page 255
FIG. 9-19. The effect of low light intensity on beam positioning . . Page 256
9.5.3 The Sequence Control Page 257
xviii
Contents
9.6 POWER . Page 260
9.6.1 Power Controls ....
. Page 260
FIG. 9-20. Flying spot store power bays
. Page 261
9.6.2 Rectifier Units (Fig. 9-20) .
. Page 262
9.7 MAINTENANCE ....
. Page 262
9.7.1 Routine Tests ....
. Page 262
9.7.2 Diagnostic Tests ....
. Page 263
9.7.3 Marginal Tests ....
. Page 263
9.7.4 Demand Tests ....
. Page 264
CHAPTER 10
The Central Control
10.1 EQUIPMENT ARRANGEMENTS
FIG. 10-1. Central control, front view ....
FIG. 10-2. Central control, rear view ....
FIG. 10-3. Central control equipment, front
FIG. 10-4. Central control equipment, rear
TABLE 10-1. Abbreviations for equipment functional designations
10.2 METHOD OF OPERATION
FIG. 10-5. ESS clock timing
10.2.1 Circuits Associated with the Flying Spot Store (Fig. 10-7)
FIG. 10-6. Central control block diagram
FIG. 10-7. Central control circuits associated with the flying spot store
FIG. 10-8. ESS clock timing for transfers
10.2.2 Decision- Making Circuits (Fig. 10-9) ....
FIG. 10-9. Decision-making elements ....
10.2.3 Parity-Check Circuits and Error-Correction Circuits (Fig. 10-10)
FIG. 10-10. Parity-check circuits and error-correction circuits .
10.2.4 Internal Flip-Flop Groups of the Central Control (Fig. 10-11)
FIG. 10-11. Internal flip-flop groups or registers
10.2.5 External Unit Registers within the Central Control (Fig. 10-12)
FIG. 10-12. External unit registers within the central control
10.2.6 Repeat-Order Circuits (Fig. 10-13) . ...
FIG. 10-13. Repeat-order circuits .....
Page 265
Page 265
Page 266
Page 267
Page 268
Page 268
Page 269
Page 270
Page 271
Page 271
Page 272
Page 274
Page 275
Page 276
Page 276
Page 278
Page 279
Page 279
Page 280
Page 281
Page 282
Page 283
Page 284
Contents
xix
10.2.7 Circuits Associated with the Scanner (Fig. 10-14) .
FIG. 10-14. Circuits associated with the scanner
10.2.8 Circuits that Control BGS Operation (Fig. 10-15) .
FIG. 10-15. Circuits associated with the barrier grid store
10.3 POWER
10.4 MISCELLANEOUS
10.5 MAINTENANCE
TABLE 10-2. Packages used in the central controls .
Page 284
Page 285
Page 285
Page 286
Page 287
Page 288
Page 290
Page 292
CHAPTER 1 1 Page 295
Trunk Circuits
11.1 EQUIPMENT ARRANGEMENTS Page 295
FIG. 11-1. ESS trunking plan Page 296
TABLE 11-1. Trunks initially assigned in the Morris ESS ... . Page 291
11.2 METHOD OF OPERATION Page 297
FIG. 11-2. Trunk cabinet, rear view and rear equipment . . . Page 298
FIG. 1 1-3. Typical transmission path from a customer telephone set
to a trunk Page 299
11.2.1 Operator Call, Recording-Completing Trunk (Fig. 11-4) . . . Page 299
1 1 .2.2 Trunk Connection to Two Sides of Distribution Switching
Network (Fig. 11-5) Page 299
FIG. 11-4. Incoming or outgoing trunk to the 3CL switchboard,
single-sided termination ...... Page 300
FIG. 11-5. Incoming or outgoing trunk to the 3CL switchboard,
double-sided termination ...... Page 300
11.2.3 No-Test Trunks (Fig. 11-6) Page 301
FIG. 11-6. Outgoing trunk from the 3CL switchboard arranged
for no-test, double-sided termination .... Page 301
11.2.4 Two-Way Trunk Circuit for PBX Tie Line (Fig. 11-7) . . . Page 302
FIG. 11-7. Two-way trunk with E and M lead signaling for
PBX tie line, single-sided termination .... Page 303
11.2.5 Trunk Circuit to the No. 5 Crossbar Office (Fig. 11-8) . . . Page 304
FIG. 1 1-8. Incoming or outgoing trunk to No. 5 crossbar office
with E and M lead signaling, single-sided termination . Page 305
11.3 MAINTENANCE . Page 306
XX
Contents
CHAPTER 12
The Administration Center
12.1 EQUIPMENT ARRANGEMENTS
FIG. 12-1. Administration center, front view
FIG. 12-2. Typing reperforator and tape ....
FIG. 12-3. Cabinet AC-O, front view, Bay
FIG. 12-4. Cabinet AC-O, rear view, Bay 1
FIG. 12-5. Cabinet AC-O, front view, Bay 2
FIG. 12-6. Cabinet AC-O, rear view, Bay 3
12.2 METHOD OF OPERATION
FIG. 12-7. Administration center display panel and associated
equipment .......
12.3 MAINTENANCE
Page 307
Page 307
Page 308
Page 310
Page l\\
Page 312
Page 313
Page 314
Page 315
Page 316
Page 318
CHAPTER 13
The Ringing and Tone Supply
13.1 EQUIPMENT ARRANGEMENTS ....
13.2 METHOD OF OPERATION
FIG. 13-1. Ringing and tone supply cabinet, front view
of front bay {gate) ....
FIG. 13-2. Ringing and tone supply cabinet, rear views
of front bay (gate) and rear bay
FIG. 13-3. Ringing tone supply, block diagram
FIG. 1 3-4. Tone supply, block diagram .
FIG. 13-5. Interruption timing supply, block diagram
13.3 DUPLICATION AND TRANSFER ....
13.4 POWER
13.5 MAINTENANCE
Page 320
Page 320
Page 320
Page 322
Page 324
Page 325
Page 326
Page 327
Page 328
Page 328
Page 329
CHAPTER 14
Page 330
Power Distribution
14.1 EQUIPMENT ARRANGEMENTS Page 330
14.2 METHOD OF OPERATION Page 331
Contents
xxi
14.2.1 A-C Power Distribution -Figs. 14-1, 14-3
14.2.2 D-C Power Distribution- Figs. 14-1, 14-3
FIG. 14-1. Power distribution cabinet, front view
FIG. 14-2. Power distribution cabinet, rear view
FIG. 14-3. A-C and D-C power distribution
Page 331
Page 331
Page 332
Page 333
Page 334
CHAPTER 15
The Alarm System
FIG. 15-1. Floor layout of alarm systems and alarm zones
FIG. 1 5-2. Trouble-indicating lamps and control keys at
the administration center
Page 335
. Page 336
. Page 337
CHAPTER 16 Page 342
Customer Group Service and Bridged Extension Service
16.1 UNATTENDED CGS Page 342
16.1.1 Method of Operation Page 342
16.2 ATTENDED CGS Page 343
TABLE 16-1. Indications received on "add-on" calls .... Page 344
TABLE 16-2. Visible and audible signals to the CGS attendant . . Page 344
16.2.1 Equipment Arrangements Page 345
16.2.2 Method of Operation Page 345
TABLE 16-3. Codes dialed by the CGS attendant .... Pa^e 346
FIG. 16-1. Attended CGS, block diagram Page 347
FIG. 16-2. Attendant's telephone set Po^e 348
16.2.3 Maintenance Page 348
FIG. 16-3. Announcement system ....... Page 349
FIG. 16-4. Lamp control unit and power unit ..... Page 350
TABLE 16-4. Ringing codes for bridged extension service . . . Page 350
16.3 BRIDGED EXTENSION SERVICE Page 351
APPENDIX
Glossary of ESS Technical Terms
Page 352
The Electronic Switching System
Chapter 1
An Introduction to the Morris
Electronic Switching System
The first Bell System all-electronic central office to provide customers with
dial telephone service has been installed to serve as part of the WHitney 2
exchange in Morris, Illinois. It is a trial installation, furnishing service initially
to certain individual and group service business stations as well as individual,
two-party, and eight-party residential lines.
Morris is about 65 miles southwest of Chicago, as shown on Fig. 1-1. It was
chosen for the trial of the first electronic switching system (ESS) because it is
an isolated local central office that is nevertheless large enough to try out the
high-speed control and nonmetallic switching network features of the ESS.
Also, there is no apparent need of developing, at this time, all the service fea-
tures required for a larger office.
The Illinois Bell Telephone Company decided to replace the manual system
in Morris by a No. 5 crossbar system in 1959. The crossbar system, which
will be in operation before the ESS is installed, will handle all the traffic in
Morris before and after the ESS trial. During the trial, some six hundred cus-
tomer lines will be transferred to the ESS. A summary of these lines, with the
services to be provided, is given in Table 1-1. The ESS is designed to handle
most of the kinds of customer services currently furnished in Morris.
The features provided in the Morris ESS were dictated by the telephone needs
of the community and by the characteristics of the electronic switching system.
Those features are summarized in Table 1-2.
All traffic to and from the ESS in Morris will be carried over trunks con-
necting with either the Morris 3CL switchboard or the Morris No. 5 crossbar
system. The trunking plan is shown in Fig. 1-2, on page 4. The trunk numbering
plan is described in Chapter 3 of this book, Switching Networks. Miscellaneous
service trunks and trunk groups are discussed in Chapter 1 1 , Trunks.
An Introduction to the Morris ESS
Chap. 1
FIG. 1-1. Location of the Morris ESS.
TABLE 1-1. CUSTOMER SERVICES TO BE PROVIDED
IN THE MORRIS ESS
Services
Lines
Main Stations
Customer Group Service (CGS)
370
50
159
64
12
370
PBX, Key Systems, and Wiring Plans
50
159
115
86
TOTALS
655
780
VG 102
Sec. 1 . 1
The ESS Compared with No. 5 Crossbar
1.1 THE ESS COMPARED WITH NO. 5 CROSSBAR
Like the No. 5 crossbar system, the electronic switching system (ESS) is
based on the concept of common control. The No. 5 crossbar, however, uses
mainly electromechanical devices and several common-control circuits; while
the ESS uses chiefly new electronic and solid-state devices, with only one
common-control circuit.
Both systems are in a sense special-purpose computers*: their special purpose
is the switching of telephone calls between customers. The main difference
between the two systems is in the method by which they are controlled. The
No. 5 crossbar rises wired relay logic, while the ESS uses stored photographic
logic. In other words, the crossbar system operates according to the way its
relays are wired, but the ESS operates according to written instructions stored
on photographic plates. A change in the written instructions will change the
machine operation without any change in wiring.
The chief advantages the ESS has over other switching systems are its high
speed of operation, its need for very few moving parts, and its longer trouble-
free operating life. Less equipment is required, which also means less building
TABLE 1-2. FEATURES TO BE PROVIDED IN THE MORRIS ESS
1. A new-type low-current telephone set
equipped with a tone ringer and a 20-pps
dial (20 pulses per second).
2. A two-five numbering plan.
3. Seven-digit customer dialing of flat-rate local
calls and extended area calls.
4. Full selective party ringing.
5. Operator handling of inward and outward
calls.
6. In and out dialing by operators.
7. Automatic completion of calls from the Chi-
cago Toll Center via No. 5 crossbar.
8. Outward dial pulsing to step-by-step satel-
lite offices via No. 5 crossbar.
9. Automatic measuring of traffic.
10. Automatic testing, trouble locating, and
trouble recording.
11. Administration controlled by teletypewriter.
12 Customer Group Services (CGS) for both PBX
and wiring plan customers.
13. Combined switchboard for DSA and toll calls
(Dial 0, inward calls and outward calls).
14. Reverting calls.
15. Special services code (0, XII).
16. Service observing (manual).
VG 103
*Computers are machines capable of performing sequences of internally-stored instructions.
An Introduction to the Morris ESS
Chap. 1
space. We expect that these and other advantages will make it possible in the
future to give better service to our customers at lower cost.
The ESS uses only a single central control because it performs repetitive
operations at very high speeds— many times faster than is possible with electro-
mechanical devices, which are in turn faster than human abilities. In a manual
system, several operators are required to handle a number of calls at one
time. The ESS operation, however, is so rapid that it can take care of all calls
one at a time without perceptible delay. At any instant, one and only one cen-
tral control operation is taking place in the ESS; but each operation is carried
out at a speed that is many times faster than any previous method can achieve.
The high speed of operation of the ESS is attained by the use of a number of
new devices and techniques. These are summarized in Table 1-3.
INCOMING
INTERCEPT
j
7A
DESK
LOCAL
TEST
CABINET
OUTGOING
INFORMATION
(7 DIGITS)
EXTENDED
AREA
SERVICE
(EAS)
POINTS
RECORDING EPttS
COMPLETING
LOCAL (4 DIGITS)
(4 DIGITS')
-OCAL (4 DIGITS)
3 CL
SWITCH-
BOARD
PERMANENT
":■'''"■
SIGNAL
PARTIAL DIAL
Jj|
NO. 5
CROSSBAR
SYSTEM
DENIED SERVICE
EAS AND TOLL
I
REPAIR AND
"ANDEM (4 DIGITS)
BUSINESS OFFICE
NIGHT TRANSFER j
*
DIAL
TOLL
POINTS
EAS TANDEM
(7 DIGITS)
( 7 DIGITS)
»
1
* 20 PPS DIAL PULSING BETWEEN ESS
AND NO. 5 CROSSBAR
10 PPS DIAL PULSING BETWEEN EAS
3 LINE
CONFERENCE
CIRCUIT
CGS
TIE LINE
CGS
INDICATOR
SIGNAL
TRUNK
20 PPS DIAL PULSING BETWEEN THE
DIAL TOLL POINTS AND NO. 5 CROSSBAR
VG 104
FIG. 1-2. The ESS trunking plan.
Sec. 1 . 2 Functions of the Major Components 5
TABLE 1-3. NEW TECHNIQUES INTRODUCED IN THE MORRIS ESS
1. The use of electronic devices and photographic memory instead of electromagnetic
elements.
2. Continuous scanning of all supervision and pulsing.
3. The use of serial operation instead of parallel operation.
4. Time-sharing of a single central control.
5. The use of a common electronic switching unit for supervisory switching functions
formerly performed in each trunk circuit.
6. Simplified maintenance through the use of plug-in units in the major portion of the
equipment.
7. Automatic diagnosis of troubles, and automatic prediction of possible sources of
trouble.
VG 105
1 . 2 FUNCTIONS OF THE MAJOR COMPONENTS
The major components of the ESS are shown schematically in Fig. 1-3.
Their functions are described briefly in this section; following chapters explain
their operation in more detail. The drawing numbers of the components and
the connecting circuits are shown on Key Sheet ES-1A000-01. The terminology
used in this book is summarized in the Appendix, which constitutes a glossary
of technical terms applying to the electronic switching system.
1.2.1 The Scanner
If you think of the ESS as a robot operator, then the scanner is its
"eyes and ears." With a human operator, her eyes and ears detect information
on switchboard lines and trunks. This it passes on to her brain. So with ESS
the scanner detects the voltage condition of lines and trunks. This it passes on
to the central control— the robot's "brain."
The central control must be able to detect the condition at any time of any
line (or trunk) in the office. To do this, periodically and at high speeds, the
An Introduction to the Morris ESS
Chap. 1
CALLING
CUSTOMER
CONCENTRATION
SWITCHING
NETWORK
CN
SCANNER
S
SIGNAL
SWITCHING
NETWORK
SN
CONCENTRATION
MARKER
CM
CENTRAL
CONTROL
CC
BARRIER GRID
STORE
BGS
DISTRIBUTION
SWITCHING
NETWORK
DN
1 v.' '
STAND-BY
TRANSFER
ST
TRUNK
T
DISTRIBUTION
MARKER
DM
FLYING SPOT
STORE
FSS
SIGNAL
DISTRIBUTOR
SD
ADMINISTRATION
CENTER
AC
FIG. 1-3. ESS equipment schematic.
scanner "looks" at each line. By information from the scanner, and that stored
in other parts of the system, the central control can determine that a customer
has begun to originate a call, that a call is in progress, or that the call has been
disconnected. The scanner checks the voltage of each line ten times a second—
that is, every 100 milliseconds. When a request for service is detected, the
scanner is further directed to the line every 10 milliseconds (100 times a second).
This is necessary in order to recognize changes in line voltage resulting from
dial pulses (the dials used in Morris operate at 20 pulses per second, or 20 pps).
After the connection has been set up to the called customer and no more dial
pulsing is expected, the 10-millisecond scan is stopped. The scanner detects an
answer by the called line in the regular 100-millisecond scan. When it does,
the ringing of the called line is stopped by the release of the connection from
the ringing switch.
Sec. 1 . 2
Functions of the Major Components
Leads from the scanner are connected to two resistors in the loop circuit of
each ESS line, as indicated in Fig. 1-4. When a customer originates a call, the
closing of the switch hook causes current to flow in the line loop. The current
passes through these resistors, where a d-c voltage drop is developed. The
voltage disappears whenever the line current is interrupted. This happens
during dial pulsing, and again at the end of a call when the switch hook opens
the line. The scanner input circuit detects the presence or absence of this volt-
age, and passes this information to the central control. This gives the central
TELEPHONE
SET
-vw
Ky3 HEAT
COILS J
CARBON
BLOCKS
' :: : ::: :/J
-vw
-T
_3L
-50 V
TO SWITCHING
NETWORK
TO
SCANNER
SCANNER CONNECTION TO A CUSTOMER LINE
TIP
TO SWITCHING
NETWORKS
I A
I
RING
B
TO SCANNER
SCANNER CONNECTION TO A TRUNK
FIG. 1-4. Scanner connections to lines and trunks.
TO 3CL
SWITCHBOARD
TRUNK
8 An Introduction to the Morris ESS Chap. 1
control the supervisory information it needs to process the call. The scanner
input circuit likewise detects the presence or absence of a signal voltage on a
trunk.
1.2.2 The Signal Distributor
The signal distributor can be compared to the "hands" of a telephone
operator. The operator inserts the plug of a cord circuit into the switchboard
jack of a trunk, and then dials to complete the connection. Likewise, the signal
distributor, which acts as the "hands" of a robot operator, connects to a trunk
and generates the dial pulses of the called number.
The signal distributor's job is opposite to that of the scanner. The scanner
gathers information for the central control; the signal distributor distributes
information it obtains from the central control.
The signal distributor (SD) consists of a large number of flip-flops (two-state
electronic circuits). These are either set (operated) or reset (released) by directions
from the central control. The SD is used to distribute signals to one of a number
of circuits, such as trunk circuits. To these slow-speed circuits it sends signals
from the high-speed central control. The high-speed signals from the central
control are received and translated in the signal distributor. From here they
are retransmitted at a speed slow enough to operate relays or other devices
used on trunks for signal control purposes. For example, the signal distributor
is used to operate a relay in an outgoing trunk circuit to outpulse to a distant
office.
The signal distributor, among other functions, generates dial pulses on a
trunk circuit for transmission to other switching systems. In generating these
pulses, the signal distributor receives instructions from the central control at
the dial pulse rate. These instructions tell the signal distributor to open or close
the trunk loop, or to start or stop a particular pulse. This function of the
signal distributor is similar to that of a crossbar sender.
1.2.3 The Barrier Grid Store
The barrier grid store (BGS) is the short-term or temporary erasable
memory* of the ESS. It is used to record the status of each call as it progresses
through the system. This is the unit that, among other functions, remembers
the number dialed by the calling customer. It can be compared to a slate or
*A memory is a medium for retaining information.
Sec. 1 . 2 Functions of the Major Components 9
scratch pad on which notes are jotted down for future reference. After the
notes have been used, the note is erased.
The major component of the barrier grid store is the barrier grid tube (BGT),
which is an electrostatic storage tube. This tube is built somewhat like a tele-
vision tube with an electron gun at one end and a target at the other. The
electron gun generates and shoots a pencil-like beam of electrons toward the
target. The principal difference between the barrier grid tube and the TV tube
is in the target. The target of the TV tube is a phosphor screen of various sizes
up to 30 inches in diameter; the target of the barrier grid tube is a piece of mica
about 2 inches in diameter.
This "screen" or target area is divided into smaller areas or "spots"; at each
of these spots or memory cells it is possible to store an electrical charge. Thus,
each spot can record one bit of information.* There are four BGS's in Morris,
and each tube (BGT) has a capacity of 16,384 separate bits. Groups of spots
in the BGT record information about each call as it progresses through the sys-
tem. These groups of spots are known as "registers." They work a lot like the
relay registers in the No. 5 crossbar system. Some of these spots in the register
take the place of certain relays in the trunk circuits of existing systems. For this
reason, the trunk circuits in the ESS are relatively simple.
1.2.4 The Flying Spot Store
The flying spot store (FSS) is the second memory component in the
system. It is the long-term or semipermanent memory of the ESS. In this mem-
ory is stored the entire office service program, the office test program, and the
translation data necessary to convert a directory number to an equipment
location, to give the type of ringing, etc.
In comparison, a manual telephone system has part of the above informa-
tion stored in the operator's memory and part in written records. The records
provide the reference material that supplements the operator's memory.
In the No. 5 crossbar switching system, the office program is stored in the
wiring of the marker, and the translation functions are handled by the number
group.
♦The term "bit of information" is taken from the language of computer designers. A "bit"
is a unit in a binary numbering system; it is always a single digit, either "0" or "1". A bit
may be indicated by one of two possible conditions. For example, a bit may be represented
by an electrical charge or no electrical charge at a specified position on an electrostatic
plate; or by an opaque or a transparent spot on a photographic plate.
10 An Introduction to the Morris ESS Chap. 1
The operation of a manual system depends on human memory and reasoning
power. In present-day automatic switching systems, the memory and reasoning
are "wired-in" and the action is performed by electromechanical devices.
In place of this "human" and "wired-in" memory, the memory media of
the ESS are photographic plates; the coded information placed on the plates is
called the "stored program." It appears as an array of transparent and opaque
areas on the photographic plate. There are two flying spot stores provided in
Morris; each one contains about 2^ million storage spots. From the analogy
with the manual and the No. 5 crossbar systems, an important difference in
the ESS is evident. In the manual system, the records can be changed. In the
No. 5 crossbar system, wiring can be altered to make changes. But in the ESS,
new photographic plates are prepared and inserted in the FSS.
The FSS focuses a spot of light from the face of a cathode-ray tube on the
plates through a system of lenses. The light from one spot on the screen of
the cathode-ray tube is imaged simultaneously on several photographic plates.
From these it is imaged on a corresponding number of photo-multiplier tubes*.
The output from each photo-multiplier tube makes up one bit of information.
Consequently, a parallel set of bits is read out of the plates simultaneously
for each location on the face of the cathode-ray tube. The sets of bits read out
of the plates are relayed to the central control for use as needed.
1.2.5 The Switching Networks
The unit in the ESS that provides the connections among customer
lines (and trunks) is called the switching network. There are marked similarities
between this network and the No. 5 crossbar switching network. The talking
paths through both systems networks are connected by means of cross-points
and several stages of switching. However, the ESS network uses gas tube cross-
points instead of metallic, and a single-wire talking path in place of the con-
ventional two-wire circuit.
The ESS switching network consists of the concentration, distribution, and
signal switching networks. The controls for the networks are in the concentra-
tion and distribution markers, as shown on Fig. 1-3. On command, they can
set up or take down connections between trunks or between lines and trunks.
*Photo-multiplier tubes are light-sensing tubes in which the initial photoemission current is
multiplied many times, before being extracted at the anode.
Sec. 1 . 2
Functions of the Major Components
11
CONCENTRATION
SWITCHING NETWORK
DISTRIBUTION
SWITCHING NETWORK
LINE
T
DISTRIBUTION
MARKER
>+262V
SIDE A
FIG. 1-5. Switching network plan.
In the ESS, the switching network operates under the direction of the central
control. However, the choice of call paths through the network is selected by
the network itself. The markers apply the voltage to the proper network ter-
minals to operate the crosspoints.
Only one side of a talking or ringing connection is switched in the switching
networks. The other side uses a common-ground return path (see Fig. 1-5).
This simplifies switching, and halves the number of crosspoints used in a con-
nection. But transformers must be used to match the two-wire lines and trunks
to the single- wire circuits in the sections of the switching networks.
The matching transformers prevent the use of twenty-cycle ringing through
the networks. This means that the ringing signal used in the No. 5 crossbar
system won't work in the ESS. Therefore, a new telephone ringing arrangement
using a tone ringer instead of a bell is used in the ESS. Instead of the usual
twenty-cycle ringing, a tone signal is sent through the switching network over
the line to call a customer. The ringing tone is applied through a concentrator-
like network called the signal switching network. This network (Fig. 1-3) is
12 An Introduction to the Morris ESS Chap. 1
controlled by the concentration marker. Two connections are set up through
the switching network whenever a line is being rung. One of these is for sending
tone ringing to the called customer; the other is for sending audible ringing
tone to the calling customer.
1.2.6 The Central Control
The central control (CC) is the "brains" of the ESS. It makes all
decisions that control the flow of orders to the various parts of the system.
The Morris ESS has two central controls. One is in active service, while the
other is serving as a monitor or check ready to take over at any time.
Upon orders from the flying spot store, the central control directs the opera-
tion of the barrier grid store, scanner, distribution marker, concentration
marker, signal distributor, and flying spot store. For example, the central
control directs the scanner in inspecting the present condition of a line. By
comparing this condition with the last recorded condition in the BGS, the cen-
tral control knows whether or not a change has taken place; it can now decide
what to do next. On the basis of such decisions, different "program addresses,"*
are sent to the FSS. This is the place where instructions are received so that
appropriate changes are made in the system.
1.2.7 The Stand- By Transfer
Certain critical equipment components in the ESS are duplicated to
insure trouble-free telephone service. When one unit of such equipment is in
use, a duplicate unit is in reserve or stand-by condition. If a failure occurs in
the working or active equipment, that equipment is immediately taken out of
service, and the stand-by equipment is substituted. Part of this transfer opera-
tion is performed by the stand-by transfer circuit.
The stand-by transfer (ST) circuit includes the equipment for the switching,
matching, and marginal voltage test functions of the central control. It also
includes miscellaneous apparatus for CC, such as the master clock and the FSS
control circuit. The major functions of the stand-by transfer (ST) are the
switching functions. These control the transfer of the regular and stand-by
equipment on orders from the central control. This transfer takes place between
the central control and the following components:
*A program address is a set of characters that identify a register, location, or device in
which information is stored.
Sec. 1 . 2
Functions of the Major Components
13
Flying Spot Store (FSS)
Barrier Grid Store (BGS)
Signal Distributor (SD)
Administration Center (AC)
Distribution Marker (DM)
Concentration Marker (CM)
Ringing and Tone Supply (RT)
,M>
TABLE 1-4. FUNCTIONS OF
THE ADMINISTRATION CENTER
1 . Programming of routines for automatic
trouble location.
2. Trouble recording.
1.2.8 The Administration Center
The administration center (AC) is used to extract information de-
scribing the performance of the office, and to control certain aspects of its
operation. It includes the manual con-
trols for the system, a maintenance and
traffic recorder, and certain automatic
test equipment. The broad functions of
the administration center are shown in
Table 1-4.
The maintenance information gath-
ered by the ESS is typed out on a tele-
typewriter controlled by the system.
After the system analyzes the trouble,
the teletypewriter prints the result in a
code. This code is interpreted with the
aid of a maintenance manual, or "die- Z7TZ
VG 109
tionary," which points out the location
and number type of the packages involved. The teletypewriter also records
traffic data. In addition it is used to send input signals to the ESS to request test
or translation information from the system. For example, to take a unit out of
service for maintenance or repair, the order requesting this action is fed into
the system by typing it on the teletypewriter.
Two teletypewriter machines are provided. One is used to monitor the sys-
tems operation; the other is used for recording data for traffic studies. If one
of the machines becomes inoperative, the second machine will carry on the
normal functions of both machines.
3. Manual control of office functions.
4. Recording of traffic data.
5. Preparation of FSS photographic plates.
1.2.9 The Announcement System
The information that indicates call conditions to the PBX attendant
can be in the form of voice announcements or lamp signals. Both methods
will be tried in Morris to determine customer preference. Since the announce-
14
An Introduction to the Morris ESS
Chap. 1
1
5
4
H
6
1 3 1 1
FSS-1
,2,0
3 1 1
FSP-1
2 ,
1
BGS-0
!
BGP-0
i
BGS-1
1
BGP-1
t
BGS-2
i
BGP-2
i i
BGS-3 BGP-3
AS-0
AS-I
_J
1
1 3 l"'""5
CC-0
, 2 1 4
7
6
1 1 3
ST-0
, 2
I i
CC-t
i
SD-0
i
T-0
T-1
SPARE
ACCT
-0
5
4
~|
6
1 3 1 i
FSS-0
,2,0
3 I 1
FSP-0
2
1 i 3
CP-0
2
1 1 3 1 5
NP-0
0,2,4
RT-0
PD-0
1
S-0
S-(
1
TD-0
J
2
AC-0
1. 3, 5. 7 I 1 1
CM-0 CM-1 DM-0 DM-I
0, 2, 4, 6
' I
I
"i — 5 — i — r
SN-0
AC ADMINISTRATION CENTER
ACCT AUTOMATIC CENTRAL
CONTROL TEST
AS ANNOUNCEMENT SYSTEM
BGS BARRIER GRID STORE
BGP BARRIER GRID POWER
CC CENTRAL CONTROL
CM CONCENTRATION MARKER
CP_ CONCENTRATOR POWER S__
DM__ DISTRIBUTION MARKER SD_
FSS__ FLYING SPOT STORE SN_
FSP__FLYING SPOT POWER ST_
NP NETWORK POWER T__
PD POWER DISTRIBUTION TD.
RT RINGING AND TONE
SUPPLY
__SCANNER
__SIGNAL DISTRIBUTOR
..SWITCHING NETWORKS
_ .STAND-BY TRANSFER
__TRUNK
TRUNK DISTRIBUTOR
TTY TELETYPEWRITER
CONSOLE vcno
FIG. 1-6. Floor plan for the Morris ESS.
ment system is used on attended customer group services, it will be explained
more fully in Chapter 16.
1 . 3 EQUIPMENT ARRANGEMENTS
The location of the ESS cabinets in the Morris central office is shown in
Fig. 1-6. The cabinets are placed to simplify the cabling between them. Thus
the power cabinets are placed adjacent to their associated equipment cabinets
wherever possible. Also, cabinets that are closely related in operation are placed
together. For example, the cabinet containing the concentration and distri-
bution markers is located adjacent to the cabinet containing the switching net-
works. The administration center and the switching networks are located in a
central spot so that you can get to them easily. The cabinets are placed in rows
with a 3 foot 6 inch aisle between them.
Sec. 1 . 3
Equipment Arrangements
15
1.3.1 Cabinet Design
The ESS uses new types of cabinets and new arrangements for mount-
ing equipment. These are quite different from any used in previous telephone
switching systems.
The cabinets shown in Fig. 1-7 are the smaller of the two types used. They
are made of steel and aluminum, and have an attractive blue-and-gray vinyl
finish. Each cabinet is 7 feet high, 2 feet deep, and 28 inches wide. This permits
the use of standard 23-inch mounting plates.
These cabinets have magnetically latched aluminum hinged doors on the
front and rear. The equipment is mounted in both the front and rear to reduce
floor space and to shorten leads between large numbers of packages. Local
cabinet wiring is in the center. You get to the equipment wiring by swinging
open hinged bays. The equipment in the front of the cabinets is mounted on
these bays. The 230-volt a-c power leads and the various d-c and pulse leads
FIG. 1-7. Front view of cabinet line-up.
16
An Introduction to the Morris ESS
Chap. 1
FIG. 1-8. Front view of marker and network cabinets.
are carried overhead in the tops of the cabinets. The 110-volt a-c power leads
for the appliance receptacles are carried in the ducts in the cabinet base.
The cabinets shown in Fig. 1-8 are the larger of the two types used. These
have the same construction and finish as the smaller cabinets; only the size is
different. Each cabinet is 7 feet high, 3 feet deep, and 12 feet wide, and is
arranged for both 16-inch and 31 -inch mounting plates. The markers and
switching networks are contained in these cabinets.
These cabinets are equipped with aluminum doors hinged on the rear of
the cabinets. Sliding glass doors are used on the front of the cabinet housing
the switching network equipment. Vinyl finished aluminum sliding doors are
used on the front of the cabinet housing the marker equipment. Both cabinets
are equipped with fluorescent lighting in the front bays. This is required for
the proper functioning of the gas diode elements. As in the smaller cabinets,
the equipment is mounted on both front and rear to reduce lead lengths and
Sec. 1 . 3 Equipment Arrangements 17
floor space. Hinged bays are provided only on the rear of the cabinets con-
taining the markers.
Overhead ducts carry the wiring across the aisles. For the benefit of tem-
perature-sensitive electronic equipment, conditioned air is blown upward from
the base of the cabinets. It passes the circuit packages in the front and rear,
and goes out into the room through grilles in the top. Separate adjustable
grilles near the base in both front and rear of each cabinet direct the air from
a common supply. The amount of air is regulated according to the amount of
heat to be dissipated in each area.
The front and rear of each cabinet is stamped with its unit abbreviation
and number designation. These cabinet designations are listed in Fig. 1-3. In
addition, bay numbers are stamped on the front and rear; the even numbers
are on the front bays and the odd numbers are on the rear bays. Each cabinet
has apparatus designation charts mounted on the inside of the doors to help
you identify and locate the equipment. Since the larger 12-foot cabinets have
sliding doors on the front, the apparatus designation charts are kept in a book
located on the side of each cabinet. A copy of all charts is available at the
administration center.
Some of the cabinets have duplicate equipment. This is identified by color
coding.
1.3.2 Wiring and Local Cabling
Surface wiring is used throughout all cabinets. Local cable is also
required, however, particularly to connect equipment on the swinging bays with
the stationary parts of the cabinets. The local cables contain single conductors
of various gauge sizes, small-diameter coaxial cable, and twisted pairs. Solder-
less wrapped connections and small-gauge surface wiring allow an orderly
arrangement of wiring.
1 . 4 APPARATUS ELEMENTS
Many of the apparatus elements in the ESS are solid-state semiconductor
devices, such as diodes and transistors. A large number of gas diodes and elec-
tron tubes are also used. These, along with resistors, capacitors, and trans-
formers, make up the bulk of the circuitry in the ESS. Most of the apparatus
is mounted on plug-in wiring boards called circuit packages.
18 An Introduction to the Morris ESS Chap. 1
1.4.1 Circuit Packages
The smaller components of the circuits used in the ESS are mounted
on circuit packages. Three varieties of such packages are shown in Fig. 1-9.
Package (a) is a narrow phenol fiber board, 1 .6 inches wide by 7 inches long,
which is used with small functional circuits. On this type of board are mounted
the small components, with one or two transistors mounted in holes near the
outer end. Leads from these transistors are attached to printed conductors
that run directly to the end of the board. These conductors are connected with
the rest of the circuit pattern through a special shorting connector. This inter-
connects the conductors on both sides of the board. When you remove this
connector, the transistor is isolated, so that you can make electrical checks
without removing the transistor from the board. This type of narrow package
is an amplifier, used in the central control, scanner, and signal distributor,
and to a lesser extent in other cabinets. About 70 per cent of the packages
are of this type. These packages are mounted in connectors having code teeth.
This permits only packages with coded slots to be inserted.
Package (b) is larger, 3.6 inches by 9 inches. This type of package is used in
electron-tube circuits. As many as 66 components may be mounted on one of
these boards. This package needs two connectors of the type used with the
smaller package. As with the smaller package, the contact end is slot coded,
so that you cannot insert the package into the wrong connector. The circuit
in this package is a flip-flop* used in the storage systems. Such a package is
representative of most packages in the barrier grid store and the flying spot store.
Package (c) varies in size up to 3.3 inches by 10 inches. It is used for mounting
more and larger components in a given mounting space. The board mounts up
to 14 terminals. These mate with wires strung between molded supports. The
wires are gold plated and the terminals are palladium coated to assure low
resistance and noise-free contacts. The circuit in this kind of package is a
junctorf circuit. It is the type of package most commonly used in the switching
network.
1.4.2 Connectors
With the exception of the 14- terminal package mentioned above, the
packages plug into connectors of a special design. These connectors have 12
*A flip-flop is a device capable of assuming one of two stable states and storing a bit of
information. A relay or knife switch does a similar job.
fA junctor is a circuit between the two central stages of the switching network.
Sec. 1 . 4
Apparatus Elements
19
FIG. 1-9. Typical circuit packages.
terminals each. They are used singly for the narrow packages and in pairs for
the wider packages. The spring contacts and mating conductors are gold
plated. This assures low contact resistance. To avoid errors in replacing pack-
ages, the connectors contain code teeth. Thus, only those packages that have
code slots in the corresponding positions can be inserted.
1.4.3 Locating Packages
An important advantage of the connector and package design philos-
ophy is that you can readily locate individual connectors or packages. This is
because they are mounted on a co-ordinate basis, as illustrated in Fig. 1-10.
The location of a mounting plate in a cabinet is indicated by a three-digit
number. The first digit is the number of the bay, and the other two digits show
the location of the mounting plate in that bay. For example, if the front of a
cabinet is designated bay 0, the mounting plates on it are prefixed by a 0, and
20
An Introduction to the Morris ESS
Chap. 1
the numbers marked on the frame (00 through 31) give the plate location. The
rear of this cabinet is designated bay 1, and all of its mounting plate locations
(00 through 32) are prefixed by a 1.
The connectors have their locations stamped on the package supporting bar
(see Fig. 1-10). They are designated by letter from left to right, A through Y
and AA through AF, omitting the letters I, O, S, and Z. This gives a maximum
of 28 connector locations. The connector has twelve terminals, two vertical rows
of six terminals each, for wire wrapping. Looking at the wiring side, these ter-
minals are numbered 1 through 6 from the bottom up, and left (L) or right (R).
With this method of designation, any terminal in the cabinet may be identified.
For example, the designation 120-AF 6L indicates the following:
Bay
Location
20
Mounting Plate
Location
AF
Connector
Location
61
Connector
Terminal
WWHW ■ l P" *"
mm
PACKAGE
04 G
kdiilillfll
\ wm
°^rm
unmnamxm
4.4 4 w\ imm:t*l'4
>.,.&T^W; .... ^.. *...»* r Wrifr %*-; wr: My. .. ~
FIG. 1-10. Circuit package co-ordinate system.
Sec. 1 . 4
Apparatus Elements
21
1.4.4 Electron Tubes
Both vacuum and gas-filled electron tubes are used in the ESS. Gas
tubes are used to a greater extent than vacuum tubes. The vacuum tubes used
in the BGS and the FSS are quite complex in their construction. They are de-
scribed in the chapters covering these stores. The use of gas tubes in the ESS
is described below.
Gas tubes are used mainly in the switching networks. They are used in the
following manners:
(1) As crosspoint elements in the main distribution network and line con-
centrator units.
(2) In the selector to set up and release the talking connections.
(3) In the propagator to maintain the switching margins.
(4) In the junctor units at the center of the main distribution network.
- -L-Allu
FIG. 1-11. Gas diode crosspoint element.
Gas Diode Crosspoint Elements
The transmission path through the switching network has no metallic con-
tacting elements like those in crossbar switches. Instead, each crosspoint is a
two-element gas tube or gas diode; the construction is illustrated in Fig. 1-11.
In these tubes the gas breaks down when sufficient voltage is applied across
22
An Introduction to the Morris ESS
Chap. 1
the electrodes. An electrical path is set up through this gaseous discharge. The
speech current and the control signals for the connection are transmitted over
this path. The diode has small amplification properties at talking frequencies.
This makes up for transmission losses elsewhere in the switching network.
FUSE
p fl '■"■^■'1 l,l'1| I
ii~— DIODE
RESISTOR
-TERMINALS
VO 116
FIG. 1-12. Gas diode module.
Gas Diode Switch Modules
The gas diode crosspoint elements described above are assembled into plug-
in packages or modules; a typical module is shown in Fig. 1-12. These packages
range up to 5.5 inches by 6.5 inches in size. They contain terminals that mate
with wires strung between molded supports, in a manner similar to that for
package (c) described in subsection 1.4.1. One module constitutes a 2-by-10
switch; five of these switches are assembled to form a 10-by-10 switch.
Sec. 1 . 4
Apparatus Elements
23
-MAIN ANODE
-MICA ELECTRODE
SUPPORT
FIG. 1-13. Gas tetrode.
Gas Tetrode
The gas tetrode is constructed as shown in Fig. 1-13. It is used in the junctor
units at the center of the distribution switching network. The tube has three
anodes. A pulse on both starter anodes and the main anode puts the junctor
in the talking path. Pulses received by the starter electrodes from either side of
the network release the junctor. This in turn disconnects the talking path.
1.4.5 Inventory of Major Apparatus Elements
The quantities of apparatus elements used in the ESS are shown in
Table 1-5 (on page 24). This table shows the approximate number of major
apparatus elements used in each of the ESS cabinets.
24
An Introduction to the Morris ESS
Chap. 1
TABLE 1-5. INVENTORY OF MAJOR APPARATUS ELEMENTS
The quantities given in this table are approximate, and do not include spare apparatus.
Cabinet
Circuit
Package
Gas Diode
Cross-
points
Gas
Tube
Modules
Vacuum
Tubes
Relays
Tran-
sistors
Silicon
Junction
Diodes
Other
Diodes
Switching Network
3,600
60,000
3,000
—
—
—
30,000
—
Markers
6,883
—
—
—
49
2,234
—
4,280
Scanner
1,504
—
—
—
37
964
—
3,828
Signal Distributor
1,162
—
—
—
14
1,804
—
5,754
Central Controls
6,880
—
—
6
—
5,914
200
40,606
Standby Transfer
879
—
—
—
142
598
—
4,938
Barrier Grid Stores
180
—
—
576
—
36
—
13,890
Flying Spot Stores
220
—
—
522
19
—
—
Trunks
75
—
—
—
185
107
—
195
Administration Center
94
—
—
—
135
86
—
375
FSS Plate Preparation
332
—
—
—
8
293
—
2,120
TOTALS
21,719
60,000
3,000
1,104
589
12,116
30,200
75,986
VG 118
1 . 5 POWER EQUIPMENT
The principal devices in the No. 5 crossbar system are relays and cross-
bar switches. These require 48 volts for their operation. For this system a cen-
tralized power plant is the most economical. Reliability is assured by floating
the 48-volt storage battery. However, this type of power plant is not feasible
for the ESS. The ESS uses chiefly transistors requiring low voltages and small
amounts of power; electron tubes requiring filament, plate, and screen supplies
in the range of IV2 to 547 volts; and cathode-ray tubes requiring filament and
accelerating voltages in the range of 1,000 to 10,000 volts. This number of
voltages (80 different voltages, 247 power supplies), ranging from IVi volts to
10,000 volts, is best supplied by regulated rectifiers. These rectifiers, in many
Sec. 1 . 5
Power Equipment
25
cases, must be associated closely with the equipment they serve. For these
reasons a decentralized power system is used to secure the reliability and
precision required for the ESS.
The regulated power rectifiers, which are associated with the cabinets they
serve, are explained in the chapters describing these cabinets. This section
describes only the power equipment common to the electronic central office.
1.5.1 Motor Alternators — Source of A-C Power
Supplying d-c power with rectifiers requires an uninterrupted source
of a-c power. To obtain continuous a-c power, the gap between commercial
power failure and the starting of the stand-by diesel engine is bridged by motor
alternators; a photo of this equipment is reproduced in Fig. 1-14. The motor
alternators are arranged in a reliable a-c power plant to supply the three a-c
buses, shown schematically in Fig. 1-15. The d-c motors of the motor alter-
nators are driven from the 1 30- volt battery. This battery has sufficient capacity
to drive three of the four motor alternator sets. The battery is recharged
through a rectifier run from the commercial power.
The commercial a-c supply (208-volt, 3-phase, 60-cycle) for the motor alter-
nators is divided into two buses, as shown in Fig. 1-16. Two automatically
DC MOTOR
FLYWHEEL-
ALTERNATOR
EXCITER
AC MOTOR
mm 8« WTZZZr
ipk
-TERMINAL BOXES '
ALTERNATOR
FIG. 1-14. Motor-alternator set with d-c and a-c drive motors and fly wheel.
26
An Introduction to the Morris ESS
Chap. 1
MOTOR ALTERNATOR SETS
NO. t
VOLTAGE
REGULATORS
AC
MOTOR
ALT
'" BUS 1
! MOTOR
V
AC BUSES
.
_|
^
BUS2i
> —
NO. 2
B
J
COMMERCIAL
V
TO
OR
I
L DC
POWER
SUPPLIES
ENGINE <
60-CYCLE
SERVICE
NO. 3
i 1 I
c
I
1
V
1
1
+ I3(
NO. 4
J
1
SPARE
|
)V
SUPPLY
VG 120
FIG. 1-15. A-C power plant.
started diesel engine alternators supply the power if the commercial supply
fails (see Fig. 1-17). The a-c plant converts the input power to nominal 230-
volt, single-phase, 60-cycle power. If either of the diesel engines fails to start,
the office can still continue to operate on the d-c motors.
A manually started diesel engine supplies the power for the building air-
conditioning equipment when the other a-c sources fail.
1.5.2 A-C Distribution for D-C Power Supplies
The cabinets of switching and power equipment are arranged in rows,
as indicated by the plan shown in Fig. 1-18. Power feeders from the three
single-phase 230-volt buses in the a-c and d-c power distribution cabinet are
run overhead in each row. These buses supply the power to the rectifiers.
Regular and spare rectifiers are connected to different buses. By distributing
the rectifiers over the three buses, any one bus can fail without disabling the
office. Three 48-volt d-c buses distribute d-c power from the No. 5 crossbar
battery via the a-c and d-c power distribution cabinet. These supply the relays
in the ESS equipment; Fig. 1-19 shows the arrangement.
Sec. 1 . 5
Power Equipment
27
60-IW
ENGINE
ALTERNATOR
(AUTOMATIC)
NO. I
60-KW
ENGINE
ALTERNATOR
( AUTOMATIC )
NO. 2
60-KW
ENGINE
ALTERNATOR
(MANUAL)
1
TO COMMERCIAL
AC POWER
FIG. 1-16. Primary a-c distribution.
AIR
CONDITIONING
EQUIPMENT
L ; 1 , 1
MOTOR ALT
NO. 1
MOTOR ALT
NO. Z
MOTOR ALT
NO. 4
(SPARE)
MOTOR ALT
NO. 3
AIR
CONDITIONING
EQUIPMENT
130V. PLANT
AIR
CONDITIONING
EQUIPMENT
FIG. 1-17.
Diesel engine alternator.
28
An Introduction to the Morris ESS
Chap. 1
i — r
SD-0 ACCT-0 R.T-0
NETWORK
LIGHTING
3 SINGLE-PHASE 230-VOLT BUSES
TO POWER DISTRIBUTION CABINET
SEE FIG. 1-6 FOR
MEANING OF
ABBREVIATIONS
FIG. 1-18. A-c distribution for d-c power supplies.
BGP-0 BGP-1 BGP-2 BGP-3 AS-0 AS - 1
T-1 ACCT-0 RT-0
TEST ALARM
BLOCK CIRCUIT
AC-0 CM-0 CM-1 DM-0 DM - 1
3 48-VOLT BUSES
TO POWER DISTRIBUTION CABINET
NOTE: SEE FIG. 1-6 FOR
MEANING OF
ABBREVIATIONS
FIG. 1-19. 48-vo/r d-c power distribution.
Sec. 1 . 5
Power Equipment
29
SIGNAL
SWITCHING
NETWORK
(SEE FIG. 2-2)
+ 128 V
SIDE A
DISTRIBUTION
SWITCHING
NETWORK
r
SIDE B
DISTRIBUTION
SWITCHING
NETWORK
* INDICATES CROSSPOINTS VG I26
FIG. 1-20. Connection of audible ringing tone generator to the signal switching network.
1.5.3 Tone Power Supplies
The five tones required for the ESS are supplied by electronic tone
generators. The tones and their frequencies are summarized in Table 1-6, on
page 30. The method of applying the audible ringing tone is shown in Fig. 1-20.
Here the tone generator is connected to 55 ringing switch terminations through
900-ohm matching resistors. The method of applying the dial, busy, and
reorder tones is shown in Fig. 1-21. The generators for these tones are connected
through 900-ohm matching resistors
directly to the distribution switching
network tone points. About fifteen tone
points each are provided for
dial, busy, and reorder tones. tone
GENERATOR
FIG. 1-21. Connection of dial, busy,
and re-order tone generator to the
tone points in the distribution
switching network.
DISTRIBUTION
SWITCHING NETWORK
A + 262 V
B SIDE
30
An Introduction to the Morris ESS
Chap. 1
TABLE 1-6. TONE POWER SUPPLIES
Frequencies are given in cycles per second, cps.
Tones
Frequencies
Audible Ringing
430 cps + 454 cps;
2 seconds on, 2 seconds off
Dial Tone
560 cps + 690 cps; steady
Alert Tone
591 cps; steady
Busy Tone
560 cps + 690 cps;
0.5 second on, 0.5 second off
Re-order Tone
560 cps + 690 cps;
0.3 second on, 0.2 second off
VG 125
FREQUENCY
GENERATORS AMPLIFIERS
RING CODE
SW PA AND
GATES AMPLIFIERS PARTY
DIGIT
478 'I*
>
~>
\. 8
L>"
J
y^"
-.
^\_ 1
532^
J
/~~
59t a.
>
^
\^_ 2
l^
V
r\
656^1
\
/^
J-
N.
f SWITCHING
72901
J>
^
^\^ 4
J
(SEE FIG.
2-2)
B\0'\i
"^>
^
^\^ 5
*^
J
900^0
\ \ «
1
> --
j
y /
\
1000 -V
>
^
> "^
//
J
'
/
INTERRUPTER
FIG. 1 -22. Tone ringer power supplies.
Sec. 1 . 5
Power Equipment
31
1.5.4 Tone Ringing Power Supplies
A frequency-selective tone ringer in the customer telephone set is
used to receive the tone ringing signal. This signal tone is obtained from eight
frequency generators, as shown in Fig. 1-22. The ringing signal is a low-level
interrupted (12.5 pulses per second) audio frequency with a duty cycle of 60
per cent "on" and 40 per cent "off." Ringing is tripped during the 40 per cent
"off" period. The ringing cycle is 2 seconds on and 2 seconds off; in No. 5
crossbar it is 2 seconds on and 4 seconds off. It is applied to the customer's
loop through the switching network. Eight different frequencies (478, 532, 591,
656, 729, 810, 900, and 1000 cps) are provided to operate tone ringers on single
party, two-party, and eight-party lines.
1 . 6 STATION SETS
The power level of the audio signals that may be sent through the ESS
is limited by the switching network. Therefore, a new telephone set is needed.
This set, shown in Fig. 1-23, is like the 500-type set except for grilles in the side
to emit tone. A partially disassembled view is given in Fig. 1-24. The set is
FIG. 1-23. Low-current tone ringer telephone set.
32
An Introduction to the Morris ESS
Chap. 1
VG130
FIG. 1-24. Telephone set, internal view.
equipped with a tone-ringer circuit and a low-current transmission circuit. The
dial is constructed to operate at 20 pulses per second.
The tone ringing signal on the line is received in the tone ringer circuit. A
transistorized tuned-circuit amplifier and the sound radiator, Fig. 1-25, are a
part of this circuit. The speech circuit uses the conventional carbon transmitter
connected in a low-current transistorized transmission circuit.
VG 131
FIG. 1-25. Sound radiator.
Sec. 1 . 7 Testing and Maintenance Philosophy 33
1 . 7 TESTING AND MAINTENANCE PHILOSOPHY
There is a distinct difference between the No. 5 crossbar system and the
ESS in maintenance and trouble-locating procedures. The No. 5 system has
considerable duplicate equipment, such as senders, registers, and markers. It is
possible, in the event of trouble, to stop a portion of the system, punch out a
trouble recorder card, and even physically examine the apparatus before it is
restored to service. In the ESS, where serial rather than parallel operation is
used, this type of trouble locating is impossible. Testing and trouble locating
must be done while the equipment is in operation. For this reason, the ESS
has its testing features built right into the system.
Actually, the ESS is a dual system. It can detect any difference in operation
between its duplicated units by making checks at a few critical points. From
these checks it decides which unit is in error. Any disagreement in results
triggers a test call and test patterns. These can locate at least the half of the
system that is in trouble. Further diagnostic techniques using the equipment
associated with the administration center help to locate the faulty equipment.
As previously stated, the major portion of the ESS equipment consists of
plug-in packages. This greatly simplifies the maintenance.
Two basic testing and maintenance units are furnished for the ESS: the
administration center and the ESS local test cabinet. The administration center
is used for testing within the office. The ESS local test cabinet is used for testing
the outside plant facilities, in addition to some in-office testing. The admin-
istration center is described in subsection 1.2.8; the ESS local test cabinet is
briefly described below. The office alarm system used in maintaining the office
is described in Chapter 15.
ESS Local Test Cabinet
This cabinet is similar in physical appearance to the No. 3 local test cabinet
used in the No. 5 crossbar system. Many of the testing operations of the ESS
cabinet are the same as those of the No. 3 local test cabinet. The local test
cabinets are located near each other in the No. 5 crossbar central office.
The ESS switching network does not provide a metallic path for testing cus-
tomer lines. When a metallic path is needed, the ESS local test cabinet is used.
It is connected to the customer's outside plant and station facilities, and to
the central office equipment, by means of patching shoes. These are set up at
34 An Introduction to the Morris ESS Chap. 1
the vertical main distributing frame. The method of operating the local
test cabinet is described in CD 1A037-01, Telephone and Test Circuit, and
CD 1A062-01, Jack, Key, and Lamp Circuit.
Service Observing
Service observing for the ESS is handled in the same room as the service
observing for the No. 5 crossbar system. Three No. 4A service observing sets
are provided for observing on ESS lines. Each 4A set has a capacity of 40 S.O.
lines. These lines terminate on jacks in the set. Thus, the three 4A sets will
provide 120 S.O. lines for observing on 120 ESS lines.
The ESS lines terminate on the main distributing frame (MDF) on the first
floor. These lines are connected by patching cords to a jack box at the MDF.
Each patching cord has a shoe on one end for connecting to ESS lines at the
MDF. The other end of the cord terminates in a jack in the jack box at the MDF.
A second set .of jacks in this box is wired directly to a set of jacks in the jack
box in the service observing room on the second floor. This box is located
close to the 4A S.O. sets.
You can easily connect any of the ESS lines to any of the S.O. lines. This is
done by connecting a patching cord between the proper jacks in the box at
the MDF, and then connecting another patching cord between a jack in the
S.O. jack box and a jack in the 4A service observing set.
An incoming or outgoing call will light a lamp at the No. 4 S.O. set. The
observer operates a key associated with the S.O. line to monitor both the
conversation and the dialing. A tape recorder may be connected to the No.
4 S.O. sets.
For customer group service (CGS) installations, seven lines are provided so
that one line out of seven can be connected automatically to a monitoring
and dial pulse register.
Chapter 2
Method of Operation
A
Perhaps the best way to describe the operation of the ESS is to trace various
types of calls through the system. This chapter tells, without detailed reference
to circuit operations, how calls are handled by the ESS. Such descriptions are
given for five types of calls, namely: an intraoffice call, a reverting call, an
outgoing call, an operator call, and an incoming call. These calls are defined
briefly in the paragraphs below. Dial tone and dialing connections, shown in
Fig. 2-1, are set up for all but the incoming calls.
An intraoffice call is a call between two customers who are served by the
ESS on different lines. Figure 2-2 shows the connections for regular ringing,
audible ringing, and talking.
A reverting call is a call between two party-line customers served by the
same line. The ringing and talking connections for this call are shown in Fig. 2-3.
An outgoing call from a customer to another office is connected to an out-
going trunk. The talking connection for such a call is shown in Fig. 2-4.
An operator call is a call or call condition that results in calling in the operator
at the 3CL switchboard. Operator calls include calls for assistance (zero
operator) and such call conditions as permanent signal, partial dial, vacant
code, and denied service. The talking connection is like that shown for an
outgoing call in Fig. 2-4.
An incoming call is connected to the called customer over an incoming trunk
from the connecting office. Figure 2-5 shows the connections for regular and
audible ringing, and for talking.
Generally the calling and called customers are connected to opposite sides
of the distribution switching network. Sometimes this cannot be done, and
two A sides or two B sides must be used. In this case, a skew ringing connec-
tion is set up, as shown in Fig. 2-6. When the called customer answers, the
skew connection is then used as the talking path.
35
36
Method of Operation
Chap. 2
DIAL TONE CONNECTION
CALLING
CUSTOMER
CONCENTRATION
SWITCHING NETWORK
LINE
TERMINAL
TRUNK
TERMINAL
DISTRIBUTION SWITCHING NETWORK
TRUNK
TERMINAL
A SIDE
! ■* ■ »<><: '
TRUNK
C pOUCJ TERMIN,
O
RJ B SIDE
3Hh
_J
DIALING CONNECTION
(SEE FIG.1-21)
CALLING
CUSTOMER
CONCENTRATION
SWITCHING NETWORK
LINE
■*-
-^- INDICATES CROSSPOINTS
SCANNER
CENTRAL
CONTROL
BGS
FIG. 2-1. Connections for dial tone and for dialing.
Chap. 2
Method of Operation
37
@ NORMAL TALKING CONNECTION
(SEE FIG 1-5)
(r) REGULAR AND AUDIBLE
RINGING CONNECTION
@ ALTERNATIVE TALKING CONNECTION
■^ INDICATES CROSSPOINT
AUDIBLE
RINGING TONE
(SEE FIG 1-20)
FIG. 2-2. Connections for an intraoffice call, showing the paths for
regular ringing, audible ringing, and talking.
38
Method of Operation
Chap. 2
CALLED
CUSTOMER
CALLING
CUSTOMER
CONCENTRATION
SWITCHING NETWORK
LINE
TERMINAL
m
TRUNK
TERMINAL
CENTRAL
CONTROL
DISTRIBUTION SWITCHING NETWORK
TRUNK
TERMINAL
A SIDE
J
. U
N
i X >< >( ■'! c
I r
o
! R
w ^ ,, TRUNK
' X ' X ' X TERMINAL
B SIDE
6
BGS
RINGING
FREQUENCY
(SEE FIG.1-22)
SIGNAL
SWITCHING NETWORK
(?) TALKING CONNECTION
® RINGING CONNECTION
-X" INDICATES CROSSPOINT
FIG. 2-3. Connections for a reverting call: ringing and talking paths.
Chap. 2
Method of Operation
39
CALLING
CUSTOMER
CONCENTRATION
SWITCHING NETWORK
LINE
TERMINAL
A
TRUNK
TERMINAL
CENTRAL
CONTROL
DISTRIBUTION SWITCHING NETWORK
-,
TRUNK
TERMINAL
A SIDE
[)()()(
J l
u !
N
c i X) ' H ' (" I t
T
o
R
TRUNK
ERMINAL
B SIDE
OUTGOING
TRUNK
TRUNK
TO
CONNECTING
OFFICE
-^- INDICATES CROSSPOINT
FIG. 2-4. Talking connection for an operator call or an outgoing call. VG204
40
Method of Operation
Chap. 2
FROM TRUNK IN
CONNECTING OFFICE
CALLED
CUSTOMER
INCOMING
TRUNK
CONCENTRATION
SWITCHING NETWORK
HLINE
TERMINAL p rr ^
TRUNK
TERMINAL
CENTRAL
CONTROL
(?) NORMAL TALKING CONNECTION
(SEE FIG 1-5)
® REGULAR AND AUDIBLE
RINGING CONNECTION
® ALTERNATIVE TALKING CONNECTION
.*- INDICATES CROSSPOINT
DISTRIBUTION SWITCHING NETWORK
A SIDE
TRUNK
TERMINAL
**H*
TRUNK
TERMINAL
■***•
B SIDE
T
(R.T'J
JUNCTORS
B SIDE
TRUNK
TERMINAL
*H*X
TRUNK
TERMINAL
A SIDE
RINGING | 2 ■
FREQUENCY ■
(SEE FIG 1-22)1 5 ■
AUDIBLE
RINGING TONE
(SEE FIG 1-20)
SIGNAL
SWITCHING NETWORK
■®
INPUT
TERMINAL
i x ^ > r trunk
" ^TERMINAL
FIG. 2-5. Connections for an incoming call, showing the paths for
regular ringing, audible ringing, and talking.
Chap. 2
Method of Operation
41
J CALLED
| CUSTOMER
H
CALLING
CUSTOMER
INCOMING
TRUNK
CONCENTRATION
SWITCHING ^NETWORK
LINE
TERMINAL
H TRUNK
TERMINAL ""
LINE
TERMINAL
m-
OISTRIBUTION SWITCHING NETWORK
A SIDE
TRUNK
TERMINAL
XX ' Xv
mm-
B SIDE
TRUNK !
TERMINAL
' H ' >0( l
TERMINAL
SCANNER
CENTRAL
CONTROL
BGS
RINGING
FREQUENCIES -
(SEE FIG 1-22) 5 .
ft
SIGNAL
SWITCHING NETWORK
i INPUT
! TERMINAL
6
I 7
, v v trunk i
~7 /"terminal ""
(?) SKEW TALKING CONNECTION
(fi) SKEW RINGING CONNECTION
■i^. INDICATES CROSSPOINT
AUDIBLE
RINGING TONE
(SEE FIG 1-20)
INPUT I \\, TRUNK
ERMINAL P '/j TERMINAL
FIG. 2-6. Skew ringing and talking connections for an intraoffice call or an incoming call.
.42 Method of Operation Chap. 2
The Stored Programs
Chapter 1 was concerned mainly with the actions of the major components
used in handling a telephone call. These actions are tied together by a series of
instructions known as the stored "programs." Before tracing a call, let us
discuss the programs for a moment.
These programs contain orders or instructions for handling a particular sys-
tem routine and for processing calls. They determine the sequence and time
limitations, if any, for the individual routine and instructions. A main program
acts as a timetable and priority list for the other programs that control the ESS.
The instructions in the programs can be compared to the instructions in a
"do it yourself kit" manual. Like the manual, the programs in ESS consist of
a number of simple instructions. The instructions given by the programs might
be, "Look at line so-and-so. If it is off-hook do this; if it is on-hook do that."
Another instruction might be, "Write a 1 in a certain address, or read a partic-
ular address in the barrier grid store." It is these stored instructions that give
the ESS flexibility. To make changes in the method of handling calls, you need
only to change the set of instructions.
The programs also contain the instructions for making tests of the system.
All programs are stored on photographic plates in the flying spot store (FSS).
The FSS also contains the translation information that makes it possible to
translate directory numbers into equipment numbers, class of service, etc. The
stored programs are organized into "words" consisting of combinations of l's
and O's. Each word is identified by an "address." Upon receiving an address
from the central control, the program storage (FSS) reads out the correspond-
ing word and transmits it back to the central control. The central control
interprets the word and transmits an appropriate request to the other units in
the system. The programs are described in more detail in Chapter 9.
2 . 1 ESTABLISHING THE DIALING CONNECTION— FIG. 2-7
Each customer line has two spots assigned to it in the barrier grid tube
(BGT). We will call these the line spots, LI and L2. By a charge or no charge
on these spots, the ESS can determine the state of the customer line. In the
language of the ESS, which is all in terms of l's (charge) and O's (no charge),
we use the combination 00 to mean "the line is idle"; the combination 10 to
Sec. 2 . 1
Establishing the Dialing Connection
43
mean "the line is in the busy or talking state"; and the combination 01 to
mean "the line is presently being served by the system."
The system is not designed to look at any one line continuously, but to
look at all the lines periodically. The stored program directs a scan of each
customer line on a one-at-a-time basis every 100 milliseconds. The system
compares the line to the line spots in the BGT. The system then knows whether
any change has occurred on a customer line since the last previous look. If no
change has occurred, it proceeds with the scan of the other lines. Suppose
the scanner detects a change (off-hook) in a customer line, and a comparison
of the line spots with the scanner reading indicates that on the last previous
look the line was idle. From this change, the system now concludes that this
line has just made a service request; see Fig. 2-7, connection 1.
H
CALLING
CUSTOMER
-DIAL TONE CONNECTION
CONCENTRATION
SWITCHING NETWORK
LINE
TERMINAL
TRUNK
TERMINAL
DIALING
CONNECTION
DISTRIBUTION SWITCHING NETWORK
TRUNK
TERMINAL
*•*•*
A SIDE
v >( x TRUNK
H TERMINAL
B SIDE
CONCENTRATION
MARKER
SCANNER *
DISTRIBUTION
MARKER
(SEE FIG 1 -21)
CENTRAL CONTROL
*■ BGS
FSS
-X- INDICATES CROSSPOINT
NUMBERS INDICATE ORDER OF CONNECTION
ARROWS INDICATE DIRECTION OF CONNECTION
FIG. 2-7. Establishing a dialing connection.
44 Method of Operation Chap. 2
Some way is needed to keep track of this line and to record the information
received from it. This is done by taking a vertical column of spots in the erasable
memory (BGT) and giving it the job of recording the information on the origin
of a call. This column of spots is called an originating register. Enough origi-
nating registers are provided to handle all the calls that are in the originating
state at the same time. The system selects an idle originating register, makes it
busy, and assigns it to the customer line; this is done through connection 2 in
the figure. The calling customer scanner address (equipment number) is stored
in this originating register. Now the central control directs the scanner to
continue with a 100-millisecond scan of the next line.
2.1.1 Dia\ Tone Connection — Fig. 2-7
The central control starts to prepare the dial tone connection as soon
as the equipment number of the calling line is stored in the originating register.
The dial tone trunks have T3 spots assigned to them in the BGT. These spots
are used by the central control to find and select an idle dial tone trunk. A
translation program using the FSS gives the central control the network address
of the dial tone trunk selected; connections 2 and 3 in Fig. 2-7. The next step
is to connect the calling customer to the dial tone trunk in the distribution
switching network. With respect to other functions in the ESS, the operations
that take place in the concentration and distribution switching networks are
quite slow. A single network register is provided in the BGT to care for all
functions associated with these slower actions, so the more rapid functions
in the office can continue.
On a program order from the FSS, the central control directs the concentra-
tion marker to set up a connection in the concentration switching network,
connection 4. The concentration marker places a voltage on the calling cus-
tomer line terminal address, and places ground on the idle concentrator trunks
to either the A or B side of the distribution switching network, as directed. A
gas diode crosspoint fires and sets up a path from the customer line terminal
to the concentrator trunk; connection 5. The figure shows the connection to
the A side of the distribution switching network. The distribution marker sets
up the connections in the distribution switching network, through connection
6. The addresses of the concentrator trunk and the dial tone trunk selected
are known by the central control. Voltages are placed on these address points.
These points are the concentrator trunk, A side, and the dial tone trunk, B
Sec. 2 . 1 Establishing the Dialing Connection 45
side, of the distribution switching network. All idle gas diode crosspoints
between the marked ends fire. However, only one junctor is made active for
this connection; thus only one complete path is set up. The concentrator trunk
is connected to a dial tone trunk through six fired gas diode crosspoints and
one junctor; this is connection 7.
2.1.2 Dialing Connection
Having given the calling customer dial tone, and having assigned an
originating register to the line, the system now waits to record the dial pulses.
As mentioned before, each customer line is scanned every 100 milliseconds.
But during dialing, the pulses have a width of some 50 milliseconds. Scanning
the line every 100 milliseconds is not often enough to be sure that all pulses
are detected. Some pulses might slip through the 100-millisecond scanning rate.
So the program must prescribe that the system scan, every 10 milliseconds,
each line that is in an originating register. Changes on the line due to dialing
are detected by providing a "last look" spot in the originating register. Here
is recorded the state in which the line was when last seen. The "last look"
spot is compared with the line condition as found by the scanner. When a
change is found, the system takes appropriate action. Thus, it can detect and
count the pulses of a digit; and by timing, it separates the pulses of one digit
from the pulses of the next digit. These digits are stored in a group of spots
in the originating register called digit slots.
After the first digit is dialed, the central control consults the "recent change"
register in the BGT and the translation area of the FSS, to determine the class
of service of the calling customer. This information is then stored in the orig-
inating register. The central control also examines the digit slots in the orig-
inating register after each digit to see whether any action need be taken.
While the calling customer is receiving dial tone, a follow-up procedure is
undertaken by the system. The distribution marker reports back to the central
control that the connections in the distribution switching network have been
set up. When the first dial pulse is detected, the program directs the central
control to knock down the dial tone connection. This prevents the calling
customer from hearing dial tone while dialing.
The basic operations for starting any type of call now have been completed.
The operations that set up the connections for different types of calls are de-
scribed in the following sections of this chapter.
46
Method of Operation
Chap. 2
CALLING
CUSTOMER
CALLED
CUSTOMER
CONCENTRATION
SWITCHING NETWORK
LINE
TERMINAL
LINE
TERMINAL
TRUNK
TERMINAL
TRUNK
TERMINAL
CONCENTRATION
MARKER
-CONCENTRATOR TRUNKS
DISTRIBUTION
MARKER
CENTRAL CONTROL
FSS
BGS
DISTRIBUTION. SWITCHING NETWORK
8 SIDE
-RINGING TRUNKS-
SIGNAL
SWITCHING NETWORK
TRUNK
TERMINAL
10
xti
INPUT
TERMINAL
81234567 AUDIBLE RINGING
V TONE
RINGING FREQUENCIES
-*■ INDICATES CROSSPOINTS.
NUMBERS INDICATE ORDER OF CONNECTION.
ARROWS INDICATE DIRECTION OF CONNECTION.
FIG. 2-8. Establishing an intraoffice call.
2 . 2 INTRAOFFICE CALL— FIG. 2-8
Now let us trace an intraoffice call within the ESS. The calling customer
connection to the A side of the distribution switching network, via a con-
centrator trunk, Fig. 2-8, connection 1, was described in subsection 2.1.2 on
the dialing connection. The following description covers the action after the
seventh digit has been dialed.
Sec. 2 . 2 Intraoffice Call 47
Through a translation program, the system consults the "recent change"
register in the BGT and the translation area of the FSS. Here the directory
number of the called customer is translated to an equipment number. This
translation also informs the central control of the class of service and ringing
code of the called customer. The called customer line spots in the BGT are then
examined. Their address is also found from the translation. The condition of the
line spots informs the central control of the state of the called customer line,
such as idle, busy, or dialing. If the called customer line spots show "idle"
(00), they are put in the "line being served" condition (01). This temporary
record tells the central control that this address is being served by the system;
connections 2 and 3, Fig. 2-8.
If the called customer line is idle, the central control orders the concentration
marker, via address leads, to set up a connection in the concentration switching
network, using connection 4. A talking and signaling path is now set up be-
tween the called customer line terminal and a concentrator trunk having an
appearance on the B side of the distribution switching network; this path is
connection 5. The next step is to set up a ringing frequency to the called cus-
tomer, and audible ringing tone to the calling customer.
The central control consults the FSS to locate the activity (T3) spots of the
ringing trunks and then directs this number to the BGT. By selectively looking
at the activity spots of the ringing trunks, the central control is able to obtain
the address of an idle one. The central control takes this address and orders
the distribution marker to set up, through connection 6, the ringing connec-
tions in the distribution switching network. A voltage is placed on the con-
centrator trunk terminal on the B side of the distribution switching network,
and on the ringing trunk terminal on the A side. The gas diode crosspoints
fire, and a path is set up between them, connection 7. The same action takes
place between the concentrator trunk terminal on the A side and the ringing
trunk terminal on the B side of the distribution switching network. Again,
gas diode crosspoints fire, and a connection is made, connection 8. The central
control then directs the concentration marker to set up, through connection 9,
the proper ringing frequencies to the ringing trunk. The concentration marker
first sets up the proper ringing frequency to the called customer and audible
ringing tone to the calling customer. Conducting gas diode crosspoints connect
the ringing frequency and the audible tone to the ringing trunks, through con-
nections 10 and 11. When the ringing connection is set up, the calling customer
48 Method of Operation Chap. 2
line spots in the BGT are put in the "talking" state. The called line num-
ber js put into a ringing register in the BGT, and the originating register is re-
leased. The program specifies that any line in a ringing register shall be scanned
periodically for an answer.
When the called customer answers, the network is requested to take down
the ringing connections, connections 7 and 8, and put up a talking connection.
This is done in a series of steps under control of the network programs in the
FSS. The distribution marker places a mark voltage on the called and calling
customer concentrator trunk terminals on the A and B sides of the distribution
switching network. The mark voltage on each concentrator trunk terminal
causes the gas diode crosspoints on many idle paths to fire. But only one
junctor is made active; thus only one complete path through the distribution
switching network is set up, connection 12. The line spots of the called customer,
in the BGT, are put in the "talking" state. During the "talking" state, no
registers are needed for the call.
After the talking path is set up, the program directs the concentration
marker to release the ringing frequency and audible tone connections to the
ringing trunk terminals, connections 10 and 11. If no idle paths are available
through the distribution switching network, the ringing trunk is used as the
talking path (see Fig. 2-2).
A scanner comparison of the customer line with the line spots in the BGT
indicates when a disconnect occurs on a line. To make sure this is a valid
disconnect and not a hit, a disconnect register in the BGT is assigned to the
disconnecting customer. The disconnect register contains the disconnecting cus-
tomer's scanner address. If, after three 100-millisecond scans, a disconnect
condition still exists, the network register is directed to remove the talking
connection.
i
2 . 3 REVERTING CALL— FIG. 2-9
As mentioned previously, a reverting call is a call between two cus-
tomers (parties) on the same line. This call differs from other local calls in that
eight digits are dialed. The last digit identifies the calling party. The calling party
connection to a concentrator trunk was described in subsection 2.1.2 on the
dialing connection; this connection is shown in Fig. 2-9 as connection 1. The
calling party line is assigned to an idle originating register in the BGT, which
stores the dial pulses.
Sec. 2 . 3
Reverting Call
49
After receiving the seventh digit, the system consults, via the translation
program, the "recent change" register in the BGT and the FSS. This translation
informs the central control of the line equipment number and the ringing code
of the called party. These it stores in the originating register, connections 2
and 3. The called party line spots in the BGT are examined, using the address
obtained from the translation. If the scanner addresses (equipment numbers)
of both the calling and called parties match, the central control knows that this
is a reverting call. The originating register is directed to wait for ten to twenty
seconds for the eighth digit. This digit gives the central control the ringing
CALLED
CUSTOMER
CALLING
CUSTOMER
--CONCENTRATOR TRUNK
CONCENTRATION
SWITCHING NETWORK
LINE
TERMINAL
DISTRIBUTION SWITCHING NETWORK
J
RINGING FREQUENCIES
(SEE FIG. 1-22)
->£- INDICATES CROSSPOINT.
NUMBERS INDICATE ORDER OF CONNECTION.
ARROWS INDICATE DIRECTION OF CONNECTION.
FIG. 2-9. Establishing a reverting call.
50 Method of Operation Chap. 2
code of the calling party. If the eighth digit is not dialed, the calling party is
directed to a partial dial trunk. After the eighth digit, the information stored
in the originating register is transferred to an idle reverting call register, and
the originating register is released.
When the calling party hangs up, the scan of the calling line detects the on-
hook condition and informs the central control. The central control directs
the distribution marker, over address leads, to set up the ringing connection,
connection 4. A mark voltage is put on the calling party's concentrator trunk
terminal on the A side and the idle ringing trunk terminal on the B side of the
distribution switching network. Gas diode crosspoints fire and set up a path
between them, connection 5.
The central control directs the concentration marker to set up the correct
ringing frequency in the signal switching network, connection 6. Gas diode
crosspoints connect the ringing frequency to the called party, connection 7.
After one ringing interval, the connection in the signal switching network is re-
leased and a different ringing frequency is connected to the ringing trunk, con-
nection 7. This rings the calling party. This action continues until the answer
is detected or the connection times out and releases.
A directed scan of the customer's line informs the central control of the
answer condition. The line spots in the BGT are put in the talking state. The
reverting register, and the connections in the concentration, distribution, and
switching networks are released. The talking path is shown by the heavy line,
connection 8.
2 . 4 OUTGOING CALL— FIG. 2-10
Outgoing calls are calls that originate in the ESS and terminate in another
office. Calls to the Morris extended area offices, and to Morris customers not
assigned to the ESS, are switched by the No. 5 crossbar office. The signaling
and talking path between the two offices is set up over an outgoing trunk.
For example, let us assume an ESS customer dials the number of a customer
terminating in the No. 5 crossbar office. The calling customer connection to a
concentrator trunk, connection 1 in Fig. 2-10, was described in subsection 2.1.2
on the dialing connection. After receipt of the seven digits, the central control
consults the "recent change" register in the BGT and the translation area of
the FSS, through connections 2 and 3 in Fig. 2-10. The translation it receives
Sec. 2 . 4
Outgoing Call
51
CALLING
CUSTOMER
CONCENTRATOR
TRUNK
CONCENTRATION
SWITCHING NETWORK
LINE
TFRMINAL
-*-
TRUNK J vtfwJcbcKjC TRUNK
TERMINAL ! M n ' K ! i ! -"■ ' K H ! TERMINAL
A SIOE
T
I
R
I
B SIDE
CONCENTRATION
MARKER
SCANNER
DISTRIBUTION
MARKER
CENTRAL
CONTROL
3
2
■
FSS
BGS
SIGNAL
DISTRIBUTOR
-^- INDICATES CROSSPOINT.
NUMBERS INDICATE ORDER OF CONNECTION.
ARROWS INDICATE DIRECTION OF CONNECTION.
FIG. 2-10. Establishing an outgoing call.
informs the central control that this is a customer in the No. 5 crossbar office.
The information stored in the originating register, the originating line class of
service, the scanner address, and the dialed digits are now transferred to an
outpulsing register in the BGT. The originating register is then released. A
translation program gives the location of the activity spots (T3) in the BGT of
the outgoing trunks. The activity spots (T3) of the outgoing trunks to the No.
5 office are then examined to find an idle trunk. An idle outgoing trunk is
found, made busy, and its equipment address determined from the FSS. The
central control passes the outgoing trunk address to the distribution marker
to set up a connection in the distribution switching network, connection 4.
A connection is set up from the calling customer's concentrator trunk terminal
on the A side to the outgoing trunk terminal on the B side of the distribution
switching network, connection 5. Another translation program (using the out-
going trunk terminal address) provides the central control with the scanner
52 Method of Operation Chap. 2
address and the signal distributor address of the trunk. The network connec-
tion (connection 5) is then released. This is to prevent the calling customer
from hearing the dial pulses sent to the No. 5 crossbar office.
The central control now directs the signal distributor to operate the trunk
relay in the outgoing trunk, connection 6. Operation of the trunk relay places
ground on the E lead, which in turn seizes an incoming register in the No. 5
crossbar office. A battery pulse, or "wink," is sent back to the outgoing trunk
from the No. 5 crossbar office over the M lead, connections 7 and 8. The
central control directs the scanner to scan the outgoing trunk (through con-
nection 9) every 50 milliseconds for the wink signal. The presence of the wink
signal tells the central control that the No. 5 crossbar office equipment is ready
to receive dial pulses. After a delay of 70 to 80 milliseconds, the system directs
the signal distributor to pulse the digits stored in the out-pulsing register. Only
the last four digits are outpulsed. The signal distributor pulses the trunk relay
in the outgoing trunk at 20 pulses per second, through connection 6. The relay
operation in turn transmits ground pulses over the E lead to the No. 5 crossbar
office. Before pulsing the last digit, the central control directs a scan of the
calling customer line to check whether it is still "off-hook."
After the last digit has been pulsed, the central control directs the distribu-
tion marker to set up, through connection 4, a connection in the distribution
switching network. A path is set up again between the calling customer con-
centrator trunk terminal and the outgoing trunk terminal, connection 5. The
network register and outpulsing register are then released. On EAS point calls,
seven digits are outpulsed.
A directed scan of the outgoing trunk by the scanner informs the central
control of the answer and disconnect of the called customer in the No. 5
crossbar office. This answer or disconnect signal is given through connection 9
by the presence or absence of battery on the M lead from the No. 5 crossbar
office.
2 . 5 INCOMING CALL— FIG. 2-1 1
Since there are no direct trunks from other offices terminating in the
ESS, all incoming calls are routed through the No. 5 crossbar office. Connec-
tions are set up to the ESS over incoming trunks. A call from a customer in
the No. 5 crossbar office or from an operator to a customer in the ESS is also
treated as an incoming call.
Sec. 2 . 5
Incoming Call
53
A No. 5 crossbar customer dials the directory number of an ESS customer.
The number group translation in the No. 5 crossbar office directs its com-
pleting marker to route advance from an intraoffice to an outgoing call and to
seize an idle outgoing trunk to the ESS. This seizes an incoming trunk in the
ESS by placing battery on its M lead. The scan of the incoming trunk by the
scanner detects this battery, through connection 1 on Fig. 2-11. The ESS now
knows that this is an incoming call.
The central control examines the activity spots of the incoming registers in
the BGT, selects one, makes it busy, and assigns it to the incoming trunk;
H
CALLED
CUSTOMER
CONCENTRATOR
TRUNK
CONCENTRATION
SWITCHING NETWORK
LINE
TERMINAL
TRUNK
TERMINAL
SCANNER
CONCENTRATION
MARKER
DISTRIBUTION
MARKER
CENTRAL CONTROL
13
SIGNAL
DISTRIBUTOR
BGS
FROM NO. 5
CROSSBAR
OFFICE
— I
INCOMING
TRUNK
DISTRIBUTION SWITCHING NETWORK
A SIDE
B SIOE
•2 rri <2 ,
TRUNK iXXX '^l XXX
-^c 1 !^
TRUNK Lat^ftl O ^^
SIGNAL.
SWITCHING NETWORK
TRUNK
TERMINAL
TRUNK f
TERMINALI
'<:
XlO
INPUT
TERMINAL
INPUT
TERMINAL
fl
AUDIBLE RINGING ,B I 234 5 6 7 ,
TONE RINGING FREQUENCIES
-^- INDICATES CROSSPOINTS.
NUMBERS INDICATE ORDER OF CONNECTION.
ARROWS INDICATE DIRECTION OF CONNECTION.
FIG. 2-11. Establishing an incoming call.
14
54 Method of Operation Chap. 2
connection 2. The incoming trunk spots (T1-T2) in the BGT are marked to
indicate that it is being served by the system. Four digits are outpulsed from
the No. 5 crossbar office. These pulses are stored in digit slots in the incoming
register in the BGT. After receiving the fourth digit, the central control examines
the "recent change" register in the BGT and the translation area in the FSS;
connections 2 and 3. The directory number is translated to obtain the scanner
address, class of service, and ringing code of the called customer. The line
spots of the called customer in the BGT are examined to see whether the called
customer line is idle. If idle, the line spots are marked to indicate the line is
being served by the system.
The central control seizes the network register and gives it the scanner address
of the incoming trunk. A translation of the scanner address is made to obtain
the address of the incoming trunk in the distribution switching network. This
information is stored in the central control.
The central control passes the line terminal address of the called customer
to the concentration marker, which in turn sets up the connection in the con-
centration switching network, connection 4. A path is set up between the called
customer line terminal and a concentrator trunk with an A appearance on the
distribution switching network, connection 5. The distribution marker sets up,
through connection 6, the connections in the distribution switching network-
These connections are between the concentrator trunk terminal and the ringing
trunk terminal of the idle ringing trunk selected by the central control, con-
nection 7. The incoming trunk terminal is also connected to a ringing trunk
on the opposite side of the distribution switching network, connection 8. The
selection and operation of the ringing trunks are the same as described in
Section 2.2 for an intraoffice call. The concentration marker sets up the con-
nections in the signal switching network, connection 9. Operated gas diode
crosspoints connect the proper ringing frequency to the called customer, and
audible ringing tone to the calling customer in the No. 5 crossbar office, con-
nections 10 and 11.
After setting up the ringing connections, the information stored in the in-
coming register (the called line address, the signal distributor address, etc.), is
all transferred to a ringing register, and the incoming register is released. The
incoming trunk spots in the BGT are put in the "talking" state. The called
customer line is scanned periodically for an answer.
When the scanner detects the answer of the called customer, the central
control directs the network to take down the ringing connections, connections
Sec. 2 . 5 Incoming Call 55
7 and 8, and set up the talking connection, connection 12. This connects the
called customer to the incoming trunk as shown by the heavy lines on Fig. 2-11.
The called customer line spots in the BGT are put in the "talking" state. The
central control now calls upon the signal distributor to indicate an answer
condition to the No. 5 crossbar trunk, connection 13. The signal distributor
address of the incoming trunk is stored in the ringing register. The signal dis-
tributor operates the trunk relay in the incoming trunk, connection 14. The
trunk relay places ground on the E lead to hold up the connection in the No. 5
crossbar office. The signal switching network, connections 10 and 11, and the
ringing register are released.
If the called customer disconnects first, the comparison of the called line
condition with the called line spots in the BGT indicates a disconnect. A dis-
connect register is then assigned to the disconnected customer. If the discon-
nect condition still exists after three 100-millisecond scans, the network register
is directed to remove the talking connection.
If the No. 5 crossbar customer disconnects first, battery is removed from
the M lead and the incoming trunk scan point. A comparison of the incoming
trunk scan address with its trunk spots in the BGT indicates a disconnect from
the No. 5 crossbar office.
2 .6 CALLS TO THE 3CL SWITCHBOARD— FIG. 2-12
2.6.1 Recording -Completing ("Zero" Operator)
When an ESS customer dials "0" (zero), he is connected through the
distribution switching network over a separate group of recording-completing
trunks to the 3CL switchboard. The operator answers these calls in the same
manner as the No. 5 crossbar customer calls.
The calling customer connection to a concentrator trunk, shown as connec-
tion 1 in Fig. 2-12, was described in subsection 2.1.2 on the dialing connection.
After the first digit has been dialed, the central control examines the digit
slots in the BGT originating register. It finds that a "0" has been dialed. This
tells the system to proceed with the program that deals with the handling of
operator calls.
The central control consults the "recent change" register in the BGT and the
translation area of the FSS, connections 2 and 3 of Fig. 2-12. This translation
gives the central control the class of service of the calling customer. The central
56
Method of Operation
Chap. 2
CALLING
CUSTOMER
CONCENTRATOR
TRUNK --•
3CL
SWITCH
BOARC
HI T 10 r
TRUNK ..
CURCUIT H "
TRUNK
PACKAGE
CONCENTRATION
SWITCHING NETWORK
SCANNER
CONCENTRATION
MARKER
DISTRIBUTION
MARKER
CENTRAL CONTROL *-l
SIGNAL
DISTRIBUTOR
-RINGING TRUNKS-
SIGNAL
SWITCHING NETWORK
8(234567 AUDIBLE RINGING
Y TONE
RINGING FREQUENCIES
-X- INDICATES CROSSPOINTS.
NUMBERS INDICATE ORDER OF CONNECTION.
ARROWS INDICATE DIRECTION OF CONNECTION.
* REPRESENTS AN OPERATOR TRUNK, DENIED SERVICE TRUNK,
PARTIAL DIAL TRUNK, OR PERMANENT SIGNAL TRUNK.
FIG. 2-12. Establishing calls to the 3CL switchboard.
10
control looks at the activity (T3) spots of the ringing trunks in the BGT. These
spots are used to tell the busy-or-idle condition of the trunks. The central
control selects an idle trunk, makes it busy, and consults the FSS to obtain the
address in the distribution switching network of the ringing trunk it has selected.
In addition to the trunk spots (Tl and T2), a T3 spot is assigned to the
operator trunks. The central control selects an idle operator trunk in the same
manner that it selected a ringing trunk. Now it has the addresses of the ringing
Sec. 2 . 6 Calls to the 3CL Switchboard 57
trunk and the operator trunk, and it directs the distribution marker to set up
the ringing connection, connection 4.
The distribution marker, via marking leads, places mark voltages on the
ringing trunk terminals, the concentrator trunk terminal, and the operator
trunk terminal in the distribution switching network. Gas diode crosspoints
fire and set up a connection between the customer concentrator trunk and a
ringing trunk, connection 6; they also set up another connection between a
ringing trunk and the operator trunk, connection 5.
The concentration marker directs the connections in the signal switching net-
work, connection 7. A voltage on the ringing trunk terminal and on the input
terminal causes a gas diode to fire. This connects the audible ringing tone to
the calling customer, connection 8. The connection between the ringing fre-
quency input terminal and the ringing trunk terminal is not made on this call
because we don't want to send ringing toward the 3CL switchboard.
A translation program determines the scanner address and the signal dis-
tributor address from the network selector address of the selected operator
trunk. The trunk spots (Tl and T2) in the BGT are put in the talking state,
and the central control directs the signal distributor to signal the operator,
connection 9. A ground from the signal distributor, through the trunk package
and over the tip lead, operates a relay in the 3CL trunk circuit, connection 10.
The operated relay lights the incoming lamp at the 3CL switchboard. The calling
customer line spots (LI and L2) in the BGT are put in the talking state.
A ringing register is assigned to the call, and a directed scan is made of the
trunk scanner address every 80 milliseconds. When the operator answers the
signal, ground is placed on the trunk lead to the scanner, connection 1 1 . The
scan of the trunk, with the presence of this ground, tells the central control that
the operator has answered. The ringing register is then released. The central
control directs the distribution marker to release the ringing connections and
to set up a talking path, connection 12. The ringing connections 5 and 6 are
released; and the talking path, connection 13, is set up between the calling
customer and the operator trunk. If a talking path cannot be set up through
the distribution switching network, the ringing trunk is used for the talking path.
An operator trunk register in the BGT is permanently associated with each
operator trunk, each denied service trunk, each partial dial trunk, and each
permanent signal trunk. It stores the information concerning an operator call
such as the address of the connected line. Calls to the operator require a com-
plete disconnect of both the line and the associated trunk to release the connec-
58 Method of Operation Chap. 2
tion. This arrangement is made so that the operator can hold a connection
while attempting to complete a call.
When the calling customer disconnects, it is detected by the supervisory
scan of the customer line. A disconnect register in the BGT is assigned to the
call, and the system enters a program to release the talking connection. The LI
and L2 line spots of the customer line are put in the "line being served" state
(01). The disconnect register waits through three 100-millisecond scans to see
that it is an actual disconnect and not an accidental hit. However, in the
process of releasing the talking connection, the system learns that the customer
was connected to an operator. An operator disconnect timing register is then
assigned to the call, and the disconnect register is released. The talking path
through the network between the customer and the trunk is set up again. The
signal distributor removes the ground from the 3CL trunk circuit, connection
10. This causes a disconnect signal on the operator's cord. The operator trunk
register is informed of the customer disconnect. The operator removes her cord,
and the supervisory scan of the trunk tells the system that she has disconnected.
Another operator disconnect timing register is assigned to the operator trunk
end of the call. The Tl and T2 trunk spots are put in the "trunk being served"
state (01). After a timing interval, the operator trunk register finds that the
customer has disconnected, but the talking connection through the network still
exists. Now the network connections are released, and the operator trunk
register is informed that the operator has disconnected and that the network
connections have been released. The customer line spots and the trunk spots
are put in the "idle" state (00), and the operator disconnect timing registers
are released.
When the customer disconnects, and after an operator disconnect timing
register is assigned to the call, the program directs a scan of the customer line
every 100 milliseconds. This is to see whether the customer goes off-hook again
to flash the operator. If the off-hook condition is noted within 700 to 800
milliseconds, a one-half second on-off flashing of the operator trunk is started.
The timing continues for another second, and if the customer is still off-hook,
the flashing is stopped. The operator disconnect register is released and the
network connections retained. If the scan of the customer line does not show
an off-hook condition within 800 to 900 milliseconds (not flashing), a dis-
connect is assumed. The program continues with the disconnect operations
as previously described.
Sec. 2 . 6 Calls to the 3CL Switchboard 59
There is no re-ring feature provided in the ESS. On delayed calls, therefore,
the operator must recall the calling customer over a No. 5 crossbar toll switch-
ing trunk by dialing the last four digits of the customer's telephone number.
2.6.2 Permanent Signals
As mentioned before, the scan of the customer line informs the ESS
of a request for service. If, after 10 to 20 seconds, the scan of the line shows
no change (no dialing taking place), a time-out occurs, and the system enters
a program to direct the line to permanent signal. The dial tone connection
is released, and the customer line is connected through the distribution switching
network to a permanent signal trunk. The selection and operation is the same
as for the recording-completing trunks, subsection 2.6.1, Fig. 2-12. The ESS
trunk circuit for permanent signals is the same as that used on the zero operator
calls.
The operator answers a permanent signal trunk by plugging a cord into the
switchboard ANS jack. Only the regular cord circuit is used. The permanent
signal cord circuit which provides for testing, ringing, and howler tones to the
permanent signal trunks in the No. 5 crossbar office should not be used with
ESS trunks. If the customer is contacted, he is instructed to hang up. When he
hangs up, the operator removes her cord and the line is restored to normal. If
the customer can not be contacted, or in case of line troubles, the operator
plugs another cord into the switchboard TST jack associated with the trunk.
This causes the teletypewriter at the administration center to print a trouble
record. This tells the maintenance man which line has a permanent signal.
The operator then removes both her cords. The permanent signal connection
is released, but the line spots in the BGT are put into the "busy" state. The
line will remain in the busy state until the customer hangs up, or until the
trouble is corrected. If the customer line number is desired, and if the operator
wants to hold the permanent signal trunk, she does not remove the cord from
the ANS jack. If she wants the line number of the permanent signal, she calls
the administration center.
If all the permanent signal trunks are busy, or if the connection in the net-
work is blocked, the system tells the teletypewriter to print a record of all the
permanent signals.
60 Method of Operation Chap. 2
2.6.3 Partial Dial
If an ESS customer fails to dial the required number of digits within
the time-out period (10 to 20 seconds), the call is routed to a partial dial trunk.
The same type of ESS trunk circuit is used as for the zero operator trunks. The
selection and connections through the switching networks are also the same.
The partial dial trunks terminate in the miscellaneous answering jacks at
the 3CL switchboard. Two sets of jacks are provided, ANS and TST, so the
operator may hold the connection and signal the teletypewriter to print a
trouble record.
2.6.4 Vacant Codes
A separate group of trunks for vacant codes is not provided in the
Morris ESS. When the system translation finds that a vacant code has been
dialed, the call is routed to the operator over a regular ESS zero operator trunk.
The operator answers, and decides how the call should be handled. The con-
nection is released when the customer hangs up and the operator removes
her cord.
2.6.5 Denied Service
The same type of ESS trunk circuit is used for the denied service as
for the zero operator calls. If an ESS customer, to whom outgoing service is
denied, attempts a call, he will be routed, after dialing, to a denied service
trunk. The operator answers, and follows the usual method for handling these
calls. The connection is released when the customer hangs up and the operator
removes her cord.
Chapter 3
The Switching Networks
The concentration switching network, the distribution switching network,
and the signaling switching network are collectively called the switching net-
works. These networks provide the voice transmission and signaling paths
between telephone customers.
The concentration switching network has direct access to every customer
line. Through gas diode crosspoints, it can connect any customer line to a
concentrator trunk on either the A side or the B side of the distribution switch-
ing network.
Each concentrator trunk has an appearance in the distribution switching
network. The distribution switching network has two sides called A and B
(see Fig. 1-5, Chap. 1). There are 135 concentrator trunks appearing on the A
side and 135 concentrator trunks appearing on the B side. The calling customer
and called customer lines terminate on opposite sides of the distribution switch-
ing network (A and B). Operated gas diode crosspoints connect them together.
The transmission and signaling path through the concentration switching net-
work and the distribution switching network is over one wire to ground.
Other trunks, such as the dial tone, busy, and ringing trunks, as well as
trunks to the 3CL switchboard and the No. 5 crossbar office, also have
appearances on the A and B sides of the distribution switching network.
Operated crosspoints connect them to the customer via a concentrator trunk
on each side of the distribution switching network.
The signal switching network connects the ringing frequencies to the called
customer line. The concentration, distribution, and signal switching networks
are each described separately in this chapter.
The network plan objective, traffic-wise at least, is to permit connections
among many lines or trunks with as few crosspoints as possible. A crosspoint
61
62
The Switching Networks
Chap. 3
3 OUTPUTS J —
3X3 SWITCH
9 CROSSPOINTS
10 OUTPUTS <
10 INPUTS
_A
f
~\
c
r~
\
i
^
«■- —
*■
V
j
I I I I
10 X 10 SWITCH
100 CROSSPOINTS
FIG. 3-1. A typical 3-by-3 switch and a typical 10-by-10 switch.
is simply a switch element. In No. 5 crossbar offices this is a metallic contact
at the intersection of a horizontal and vertical in a crossbar switch. In the
Morris ESS the crosspoint is a gas diode.
Two typical gas diode switches are shown on Fig. 3-1. Here you see a 3-by-3
switch that will switch between 3 inputs and 3 outputs. It contains 9 cross-
points. By selectively making these crosspoints conducting, paths are set up as
desired between any input and any output. Likewise, a 10-by-10 switch con-
structed in this manner contains 100 crosspoints. As the number of inputs and
outputs greatly increases, the number of crosspoints required becomes enor-
mous. For example, a switch to handle a thousand input terminals and a
thousand output terminals in this way would require a million crosspoints.
Chap. 3
The Switching Networks
63
The number of crosspoints required can be reduced substantially, however,
by using switches in successive stages. The method of achieving such a reduc-
tion can be demonstrated with the aid of Fig. 3-2. This figure represents a
network with 27 inputs and 27 outputs. To give each input terminal access to
each output terminal through a single switch would require a total of 27 x 27
or 729 crosspoints.
In the figure (Fig. 3-2) are shown thirty-six 3-by-3 switches organized in four
stages. There are nine of those switches in each stage. Each input terminal has
access, through its first-stage switch, to three switches in the second stage.
Each switch in the second stage has access to three switches in the third stage.
Thus each input terminal has access, through the switches in the first and
second stages, to any switch in the third stage. The lines connecting the switches
in the drawing show these access paths. One set of lines has been made heavy to
indicate that three paths exist between any input terminal and any output
terminal in this four-stage arrangement.
/
ft . ?? /
hf iyf
y
LINKS FOR
STAGES 314
27
OUTPUTS
FROM
- > CONCEN-
TRATOR
OR
TRUNKS
FIG. 3-2. Four-stage network wiring pattern.
64
The Switching Networks
Chap. 3
The thirty-six switches in the network of Fig. 3-2 have nine crosspoints each.
This makes a total of 36 x 9 or 324 crosspoints to take care of 27 input terminals
and 27 output terminals, instead of the 729 crosspoints which would be needed
in a single-stage 27-by-27 switch. For a thousand input terminals and a
thousand output terminals, a four-stage network could be designed with four
hundred 10-by- 10 switches, using 40,000 crosspoints instead of the million
crosspoints required by a single-stage switch. Such an arrangement would
represent a 25-to-l reduction in the number of crosspoints required.
3.1 THE DISTRIBUTION SWITCHING NETWORK
The Morris ESS contains a six-stage switching network. Stages 1, 2, 5,
and 6 contain 10-by- 10 switches (ten inputs and ten outputs in each switch).
There are twenty switches to a frame, and four frames (numbered 0, 1, 2, and
3). Stages 3 and 4, which make up the junctor wiring, each contain ten half-
frames (numbered through 9). Stages 3 and 4 contain both 4-by-4 and 4-by-2
400
TERMINALS *■
*r— ^
6
*e— >e
*s-^e-
)(-^>-
*e— s-
8
■*- INDICATES CROSSPOINTS
Y —
5
CONCENTRATOR
TRUNKS
TO A SIDE OF
DISTRIBUTION
SWITCHING
NETWORK
:>, <., =>, o, ,, o,
Me-
Mh-
9
— V
5
CONCENTRATOR
TRUNKS
TO B SIDE OF
DISTRIBUTION
SWITCHING
NETWORK
FIG. 3-6. Concentration switching network, 40-by-10 switch.
70 The Switching Networks Chap. 3
trunks 0, 2, 3, and 5, 7, 8. Fig. 3-6 shows the pattern for the five groups of
customers. Normally, calls are handled so that the calling customer is con-
nected to either the A side or the B side of the distribution switching network,
and the called customer to the opposite side. Should blocking occur at any
stage, the order of connections may be reversed, or the order may be modified
in a search for idle paths.
3 . 3 SIGNAL SWITCHING NETWORK
The signal switching network is a one-stage network containing ten
60-by-10 switches. The switches are located in the switching network cabinet
in bay 2 between the concentration and the distribution switches. The outputs
of the ringing switches are evenly distributed on the A and B sides of the
distribution switching network. They provide the tone ringer frequencies to ring
the called customer, and the audible ringing tone to the calling customer. Two
ringing trunks are used on each ringing connection. The inputs to the ringing
switches are wired to the ringing frequencies, voice announcements, and audible
and miscellaneous tone supplies. A multiple arrangement of gas diode cross-
points permits any frequency or tone to be connected to any trunk.
Dial, busy, reorder, and alert tones have direct appearances from their
source to appearances on the distribution switching network. Chapter 1 pro-
vides information on the ringing frequencies and the other tones for alerting
or signaling.
3 . 4 EQUIPMENT ARRANGEMENTS
3.4.1 Switching Networks
The switching networks are enclosed in one cabinet. The cabinet is
divided into eight sections called bays and numbered through 7. A front
view of the switching networks cabinet is shown in Fig. 3-7.
The construction of a switching network using gas diode crosspoints and
electronic control devices in large numbers was a major equipment problem.
It was further complicated by the possibility of crosstalk between paths within
the network. This is because switching is done with one conductor, unbalanced
to ground, rather than with a pair of conductors. As a result, the wiring is in
the form of spaced grids of wires, or shielded wiring.
The packages used in the switching networks are summarized in Table 3-2,
on page 74.
Sec. 3 . 4
Equipment Arrangements
71
FIG. 3-7. Switching networks cabinet, front view.
The electronic packages controlling the functions of the network (such as
the propagators, links, enablers, junctors, and input and output trunk terminal
packages) are mounted directly behind the gas diode switches. This keeps the
wiring leads short. The office concentrator line terminal package is shown in
Fig. 3-8. There are two circuits on a package. This is the package through
which the customer gains access to the concentrator trunks. A junctor package
is shown in Fig. 3-9.
The gas diode crosspoints are mounted on small frameworks called modules;
one such module is shown in Fig. 3-10, on page 75. Each module has two
inputs and ten outputs. Five of these modules stacked one on top of the other
make a 10-by-10 switch. A schematic of the 2-by-10 crosspoint module is shown
in Fig. 3-11. We can see how the two inputs have access to any of the ten out-
puts through the gas diode crosspoints. Using this arrangement, all the switches
in one stage can be stacked on top of each other. The outputs from each switch
72
The Switching Networks
Chap. 3
i; \
REAR FRONT
TWO CIRCUITS PER PACKAGE
FIG. 3-8. Office concentrator line terminal package.
Sec. 3 . 4
Equipment Arrangements
73
.Uji-it
REAR FRONT
ONE CIRCUIT PER PACKAGE
FIG. 3-9. Junctor package .
74 The Switching Networks Chap. 3
TABLE 3-2. PACKAGES USED IN THE SWITCHING NETWORKS
CONCENTRATION SWITCHING NETWORK
F-Spec. Number
CPS* No.
Quantity
Abbreviation
Name
F-51 899
101
500
LINE TERM
Office Concentrator Line Terminal Package
F-51'849(A)
F-51 984(B)
111
112
250
250
X PT
X PT
Concentrator Crosspoint Modules
F-51 850
121
56
TRK ENAB
Trunk Enabler Package
F-51851
122
56
RLS SEL
Release Selector Package
F-51 900
102
140
TRK TERM
Concentrator Trunk Terminal Package
DISTRIBUTION SWITCHING NETWORK
F-Spec. Number
CPS* No.
Quantity
Abbreviation
Name
F-51 805
103
190
TRK TERM
A
F-51 896
104
14
TRK TERM
B
Trunk Terminal Packages
F-51 897
106
162
TRK TERM
D
F-51 806
113
400
X PT
Crosspoint Module (Stages
1 or 6)
F-51 807
130
400
PROP
Propagator Package
F-51 809 (A)
F-51 985 (B)
114
115
200
200
X PT
X PT
Crosspoint Modules (Stages
2 or 5)
F-51 808
131
160
LINK
Link Package
F-51 81 1
116
250
X PT
Crosspoint Module (Stages
3 or 4)
F-51810
132
200
JCTR
Junctor Package
SIGNAL SWITCHING NETWORK
F-Spec. Number
CPS* No.
Quantity
Abbreviation
Name
F-51 852
117
45
X PT
Crosspoint Module
F-51 853
123
45
LINE SEL
Line Selector Output Package
F-51 901 (A)
F-51 902(B)
F-53038 (C)
107
108
110
200
40
30
IN TERM A
IN TERM B
IN TERM C
Input Terminal Packages
F-51 850
121
18
TRK ENAB
Trunk Enabler Package
F-51855
124
18
RLS SEL
Trunk Release Selector Package
F-51 934
109
45
TRK TERM
Trunk Terminal Package
*CPS means Circuit Package Schematic.
Sec. 3 . 4
Equipment Arrangements
75
FUSE
DIODE
r< RESISTOR
I y («— TERMINALS
FIG. 3-10. Crosspoint module.
TRUNK
SELECTOR
FIG. 3-11. 2-by- 10 crosspoint module.
5
a>
n
f)
CI
s
^
>
(/>
>
c7l
04
III
s
CD
cu
11J-
o
CVJ
o
O
<
<
V
F
(-
<
CD
l/>
o
CD
w
o
h
CQ
rn
o
O
o
O
a.
CD
rf>
r-
tf)
in
m
ftl
o
o <*
CD CO CO
ifl
in
in
aj
(M
ff>
r-
CD
r-
i--
01
S
cd
r-
en
F
CT>
r-
3> r-
CD
1-
>
1^
CD
i^
m
1
lil
a
(T
rr
en
h
n
<*>
ei
m
■£>
ci
*>n
CO
m
to ci
(0
£"
<*1
pi
r*)
n
h
V)
M
a
m
CO
r-
tfl
-
<
o
m
m
r0
4
£
V)
w
2
ID
III
o
CVJ
CD
MI
a
e>
<
<
p
o
CD
1-
o
OT
co-
|£
m
CT)
o
o
O
o
en
•S
w .
_i
<
cy
z
o
i
CO
r~
«>
0> m
*
M
N
O
ED
IO
■n
ttl
ft]
ft]
W
I
U-
O w
_
o
N
ftj
(/>
Oi
7
o
Q
■n
1- ■»
c\j
O
T^T
DISTRIBUTION
MARKER &
SEQUENCE
CONTROL
CONCENTRATOR
-X- INDICATES CROSSPOINTS
CENTRAL CONTROL
FIG. 3-20. Talking connection.
Sec. 3 . 5 Method of Operation 89
gized, which fires the gas diode A of the selected trunk. This pulse passes
through the three conducting gas diode crosspoint tubes. The selector pulse,
in combination with the junctor release pulse, fires the junctor release tube in
the junctor. This removes the current from the latch tube. No holding path
now exists for the A and B side termination, and the connection is released.
With this arrangement, a release pulse on only one trunk terminal causes the
entire connection through the distribution switching network to release.
3.5.3 Establishing a Signaling Path in the Signal Switching Network
A 12-by-2 ringing module in the signal switching network is shown
in Fig. 3-21. Each module has twelve inputs and two outputs. Five modules
make up one 60-by-10 switch. The ten ringing trunks are evenly distributed on
the A and B sides of the distribution switching network. The figure shows
trunk with an A and B appearance. Trunks assigned as skew ringing trunks
have both outputs assigned to only one side of the distribution switching net-
work. The eight ringing frequencies, audible ring, and miscellaneous tones are
the inputs to the module. The ringing frequencies connect to the trunk through
operated crosspoints. The ringing trunk has leads to the trunk-level enabler,
trunk release selector, and trunk-level identifier. Paths are set up in the signal
switching network by the line selectors in the concentration marker.
For example, let's connect a called customer to a ringing frequency on the B
side of the distribution switching network. The line selector in the concentration
marker receives a binary address from the central control. It in turn sends a
positive and a negative pulse to fire the line selector gas diode A. A mark
voltage now appears on the gas diode crosspoint B. The trunk-level enabler C
applies a negative pulse to the idle ringing trunk selected by the central control.
This pulse with the mark voltage from the line selector causes the gas diode B
to fire. The holding and signaling path is from the +128 volts, through the
gas diode crosspoint B, to ground in the trunk-level identifier. The ringing fre-
quency is induced, through transformers, to the B side appearance of the trunk.
The called customer is connected to it through the distribution switching net-
work. Audible ringing tone is then connected to the calling customer on the
A side of the distribution switching network. The audible ringing tone is selected
via the line selector gas diode E, gas diode crosspoint F, and trunk-level enabler
G. This holding and signaling path is from the +128 volts, through the gas
diode crosspoint F, to ground in the trunk-level identifier H.
90
The Switching Networks
Chap. 3
12
INPUTS
FROM
CONCEN-
TRATION
MARKER
RINGING
FREQUENCY
ssn line selector
Output package
tu
9 OTHER
FREQUENCY
INPUT
TERMINAL
PACKAGES
AND LINE
SELECTOR
OUTPUT
PACKAGES
q»
SSN LINE SELECTOR
OUTPUT PACKAGE
,E
4-AA/v
3+
ISSN LINE SELECTOR]
i OUTPUT PACKAGE
-f^VVV
*-*¥■
SSN INPUT TERM
PACKAGE
L v A/ v J_£f Y "
SSN 12 X 2
CROSSPOINT
MODULE
SSN IWPUT TERM
PACKAGE
UvJjf
AUDIBLE (X,>
RINGING 4<1J
TONE
SSN INPUT TERM
PACKAGE
LvvJ
- i
TRUNK
LEVEL
ENABLER
PACKAGES
TRUNK
RELEASE
SELECTOR
PACKAGES
TRUNK
LEVEL
IDENTIFIER
PACKAGES
INDICATES CROSSPOINTS
RINGING RINGING
TRUNK ! TRUNK
DISTRIBUTION SWITCHING
NETWORK
FIG. 3-21. Signaling path through ringing switch.
On a release order from the central control, a pulse from the trunk release
selector J causes the gas diode B to deionize and break the connection on the
ringing side. A release pulse on the audible ringing side from the trunk release
selector K causes the gas diode F to deionize and break its connection.
92 The Switching Networks Chap. 3
3 . 6 POWER
3.6.1 Power Requirements
All the power required by the switching networks is supplied by
direct current. This power may be sustained for long periods or applied in
pulses. The power supplies for the switching networks and the markers occupy
the same cabinets. This power is supplied by regulated and unregulated rectifiers
operating from a 230-volt, 60-cycle, single-phase, continuous a-c source. For
reliability in the d-c supply, all the rectifiers are furnished in duplicate. Some
of the d-c outputs are connected in parallel but are powered from separate a-c
buses. The . concentration and distribution switching networks are powered
from different supplies. The switching network cabinets contain only the IVi
volt rectifiers. All other power is supplied directly from the power cabinets
through fuses at the base of the switching network cabinets.
Some rectifiers have their d-c outputs connected in series with both terminals
above ground potential. This is called stacking supplies. An assembly of stacked
supplies is called a composite power supply. The use of composite power sup-
plies is illustrated by Fig. 3-23. For example, positive potentials of 276 volts
and 262 volts are required. By adding the auxiliary + 14- volt rectifier to the
+ 262-volt supply we obtain a + 276-volt supply. This system of stacking is
considerably cheaper than providing a separate rectifier for each voltage needed.
3.6.2 Power Equipment
A schematic diagram of part of the rectifiers and outputs used also
is shown on Fig. 3-23. Here we see the +262 volts and 1 feeding a common
bus bar through the switches S4-0 and S4-1 on the control panel. The manual
switches are shown in the open position, but with the system in operation all
these switches are closed. Certain packages in the network require a voltage
present at all times; any interruption may destroy the package. For this reason,
the +262 volts is further supplemented by a battery reserve, on switch 12. If
for some reason switches S4-0 and S4-1 are turned off, or if the a-c supply to
both rectifiers should fail, the +262 volts is still maintained to the switching
networks.
The reserve batteries are nickel cadmium; and, since they float across the
rectifier outputs, they are at full charge all the time. No maintenance is required.
Some outputs are not connected in parallel but are individual from each
rectifier, such as the + 276 volts and 1 . Failure of one of these rectifiers will
Sec. 3 . 6
Power
93
+ 4I7V-0
r
X
-i- BATTERY
-^- RESERVE
+ 262V
I
AC
BUS
C
I
AC
BUS
A
+ 14V
+ I55V
I
•
+ 14V
1
+ 262V
+ 262V
1
CONTROL
PANEL
.~-'o- t ~4
S7-I
Lxf
> +352V-0
>■
>
+ 276V-0
S5-0° 1 if
o^cJ-EL
s
lf&-
S4-! |
S-12
| +262V-0
TS2 -24
LOAD
LOAD
1
LOAD
1
LOAD
TS2-50 I LOAD
* 1
TERMINAL
STRIP NO. AND
PUNCHING NO.
LOAD TRANSFER
SWITCH
TO SWITCHING NETWORK
S4-I
FIG. 3-23. Power supplies and their outputs.
not affect service, because the duplicate load that is served by a different recti-
fier will still function. However, if a rectifier, and a marker not associated with
it, should fail, service is restored by the manual load transfer switch on the
panel. This transfers the good rectifier output to the good marker.
Extensive use of voltage dividers is possible in this power arrangement. A
voltage divider is simply a resistor with taps, connected across a power supply
output. The voltage at each tap then depends on the amount of resistance
across the circuit or the voltage drop: You can see in Fig. 3-23 how the use of
voltage dividers makes it possible to obtain a +352 volts. These outputs are
also through the panel switches and load transfer switch. A voltage divider is
shown in Fig. 3-24 and Fig. 3-25. Those rectifiers having their outputs con-
nected in parallel do not go through the load transfer switch. Diodes in the
rectifier outputs prevent reverse battery from the other rectifier in case of failure.
94
The Switching Networks
Chap. 3
FIG. 3-24. Voltage divider.
FIG. 3-25. Voltage divider assembly.
Sec. 3 . 6
Power
95
S
ii
•i* j
M
- i c=s ' ■ ' ' — '' f . s *v T *$'
J?. C i ! > * ". r 1 ]
i c
FIG. 3-26. Power cabinets for distribution switching network
and distribution markers and 1; front view.
Power Cabinets for Distribution Switching Network
and Distribution Markers
The power supplies for the distribution switching network and the distribu-
tion markers are shown in Fig. 3-26. These cabinets are designated NP-0
(Network Power-0). The cabinet bay numbers are stenciled on the metal frame-
work above the appliance outlets (not shown on the photograph). The two
end cabinets are identical. The center cabinet is the control cabinet. Each end
cabinet contains thirteen regulated rectifiers. Their outputs are wired to the
96
The Switching Networks
+ I55V
Chap. 3
&k-~ -J
oc oifmiT ^
ADJ VOITS
ALARM TEST
#
R£G DC OUTPUT
FUSE CURRENT XtO
FIG. 3-27.
Individual power supply, front view.
FIG. 3-28.
Individual power supply, internal view.
Sec. 3 . 6 Power 97
center control cabinet, and then distributed to the distribution switching net-
work and distribution markers. The rectifiers can be removed from the cabinets
by disconnecting the input and output plugs in the rear, loosening the retaining
bolt, and sliding the unit out the front.
A rectifier is shown in Fig. 3-27 and Fig. 3-28. A detailed sketch of the con-
trol cabinet is shown on Fig. 3-29, on page 98. At the upper left and right hand
corner of the control panel are the switches for the a-c circuit breakers. The
switch marked DIST in the upper left corner controls the a-c to the rectifiers
in the left cabinet, and the DIST switch on the right controls the a-c to the
right cabinet.
The NET CON switch on the left controls the a-c to the first five rectifiers
just below the control panel, and the NET CON switch on the right controls the
a-c to the next five rectifiers. The first five rectifiers supply group or distribu-
tion marker 0, and the next five supply distribution marker 1.
The panel switches control the outputs of the stacked rectifiers, and the
voltages are stenciled above the switch. In the test position, a test load is
placed on the outputs for measuring and adjusting the individual supplies.
When the power is turned on, the switches must be turned to the normal posi-
tion, beginning at the top and following the sequence shown by the arrows.
When removing a rectifier from service, the switches are returned to the test
position in reverse order. This holds for both groups and 1 .
Directly below these switches are the switches for the battery reserve, load
transfer switch, alarm switches for each cabinet, and the 48-volt d-c supply
for each cabinet.
Below the ten rectifiers mentioned previously we see the battery reserve
panels. Pin jacks are provided for voltage measurements. The bottom panel in
the cabinet contains the voltage dividers, each stenciled with the output voltage
and the jacks for voltage measurements.
Each rectifier has a high-voltage and a low-voltage alarm. A high-voltage
alarm trips the circuit breaker for that rectifier. This is a visual alarm on the
rectifier and the center control panel. The alarm is also given at the administra-
tion center. A low-voltage alarm does not trip the circuit breaker but it does
give an alarm. There is an alarm test switch in each rectifier to simulate a high
or low voltage. This lights the alarm lamp in the rectifier unit but does not
give an alarm at the administration center. The output voltage of each rectifier
is periodically monitored by the system.
98
II'
-205V
NOR o o o _o _o o
%
OFF
ON ON ON
OFF OFF OFF
e|g=i|e
"^3
2
3
4
o o
e|rr-T]«
S
a|g=i3|e
2
.[=].
©
a=B
$
<=m
o o
O
VOLTAGE DIVIDER
n n s 8 1
>i^i«
VOLTAGE DIVIDER
©
8
o o
1 1
3
4
5
*
o o
a[_n — lje
BATTERY RESERVE
57V 114V
| 109V | SPARE
© ® © @
o o o
11/3 '1/3 2*
BATTCRY RESERVE
158V 199V
| 177V | 211V
© © © ©
o o o
1 1 1/3 I 2A
Chap. 3
FIG. 3-29. Power panel for distribution switching network
and distribution markers and I; front equipment.
Sec. 3 . 6
Power
99
FIG. 3-30. Power cabinets for concentration network, signal switching
network, and concentration markers and 1; front view.
Power Cabinets for Concentration and Signaling Switching Networks,
and Concentration Markers
The power cabinets for the concentration and signaling switching networks
and for the concentration markers are shown on Fig. 3-30. These cabinets are
designated CP-0. Each cabinet contains five low-voltage nonregulated rectifiers,
seven regulated rectifiers, and fourteen voltage dividers.
100 The Switching Networks Chap. 3
The cabinet on the left with the load transfer switch is the main distributing
cabinet. The cabinet on the right has its outputs wired to the cabinet on the
left. These are also stacked supplies. The panel switches perform the same
function as those in the distribution switching network power cabinets and the
sequence followed as shown by the arrows. The alarm system is also the same.
There are no reserve batteries in these cabinets.
3 . 7 MAINTENANCE
Testing and trouble diagnosis programs are built into the ESS as an
integral part of the central control. Included in these are several tests of the
distribution switching network, namely, a "no-connection" and a "low-break-
down" test. These tests are performed during light load periods.
3.7.1 No-Connection Test
The no-connection test works in this manner. One input and output
terminal on each side of the distribution switching network, and one junctor,
are selected by the central control. A marking voltage placed on the terminals,
and an enable pulse on the junctor causes a path to be set up through the
network. By selecting a known terminal and junctor, each gas diode crosspoint
is tested for breakdown. This test is programmed by the system from test
information in the flying spot store. To test all the crosspoints in the network,
each terminal of each switch is tested ten times, and each junctor twenty times.
When a no-connection occurs, the system causes the information to be
printed out by the teletypewriter at the administration center. By taking the
typed information and referring to the "dictionary," the actual path and
packages in the network that failed can be determined. If a crosspoint in a
selected path is busy, a no-connection test read-out will occur. The test is
made twice at intervals of one half hour. One read-out on a particular no-
connection test is ignored as it assumed that on one of the tests the path was
busy. One tenth of the network is tested each night.
A typical typed read-out might be aSNRT HBT 399 891. The symbol a
indicates a trouble report. SNRT means a switching network routine test, and
HBT indicates that it is a high breakdown test (no-connection). The first three
digits (399) give the terminal number used, and 891 is the junctor number.
Sec. 3 . 7 Maintenance 101
3.7.2 Low- Breakdown Test
The low-breakdown test determines whether the gas diode crosspoints
fire on less voltage than specified. Such an action can cause false connections
and releases. The low-breakdown test requires a series of twelve tests during
the time when the test connection called for in the no-connection test is held.
It checks a specific gas diode crosspoint for low-breakdown into the already
established path. A failure is typed out at the administration center. Reference
is made to the dictionary to determine the location of the failure.
Chapter 4
Concentration and Distribution Markers
There are two markers in the ESS— the Concentration Marker (CM) and the
Distribution Marker (DM). The name "marker" comes from the operation of
marking terminals in the switching networks. The marking is done by applying
voltage pulses on the terminals between which a transmission path is to be
connected.
The CM. and DM, as a team, set up and take down all connections in the
switching networks. The marker operations are under the direction of the
central control. The markers may be thought of as robots, since they do not
know whether the connections being set up or released are a part of a dial tone
path, a ringing path, or a talking path.
On receipt of a connect or release order from the central control, the markers
translate the address into an equipment location in the switching networks.
After the markers have acted upon the network terminal, they translate its
equipment location back into the original address form, and return it to the
central control for verification.
The CM and DM are furnished in duplicate. Because all four markers are
electrically independent of each other, they can be used in any paired combi-
nation of one CM and one DM. While one pair is in service, the other pair is
in stand-by condition. The stand-by pair is continuously performing self-
checking operations which insure that it is trouble-free and ready for service.
If an in-service marker develops any trouble, a signal is sent to the system
via the scanner. On receiving such a trouble report, the ESS arranges to switch
into service a stand-by marker.
The cabinet line-up of the markers and their associated networks is shown
in Fig. 4-1. From left to right, the first two cabinets contain the two concentra-
tion markers, which are designated CM-0 and CM-1. The third and fourth
cabinets, which are designated DM-0 and DM-1, contain the two distribution
markers. The other cabinets shown in this view contain switching networks.
102
Sec. 4 . 1
Introduction to the CM and DM Operations
103
FIG. 4-1. Marker cabinets, front view.
VG 40 (
4 . 1 INTRODUCTION TO THE CM AND DM OPERATIONS
Perhaps the best way to introduce you to the CM and DM operations
is to describe their functions in setting up a typical call. An intraoffice call is
selected for this purpose and is briefly described in this section. The sections
following this one will describe in more detail the CM and DM operations.
4.1.1 Dial Tone Connections
Establishing a Connection
When a customer originates a call, the scanner notifies the ESS of the off-
hook condition. The ESS arranges to have dial tone connected to the line, by
104 Concentration and Distribution Markers Chap. 4
having the CM and the DM set up the needed paths in the switching networks.
To do this work, the markers must be given the connect orders as well as the
addresses of the line and trunk terminals to be connected in the switching
networks.
THE TASK OF THE CM— When the CM receives the customer line terminal
address and a "connect A trunk" order from the central control, the CM pro-
ceeds to set up a connection through the CSN. A mark voltage is placed on the
line terminal and the trunk terminal in the CSN. This marking causes a gas
diode crosspoint in the CSN to fire and to close a path to a trunk on the A side
of the DSN. The CM returns the CSN line terminal location and the trunk
terminal level to the central control. The central control uses this information
to form the address of the CSN trunk connected to the A side of the DSN.
THE TASK OF THE DM— When the DM receives the CSN trunk terminal
address with a "connect A side" order and the dial tone trunk terminal address
with a "connect B side" order, the DM proceeds to set up the path through the
DSN. A mark voltage is placed on the trunk terminals on both the A side and
the B side. This marking causes six gas diode crosspoints in the DSN to fire. A
path through the DSN is completed when the DM connects a junctor in the
path with the six diodes. Dial tone is now sent to the calling customer through
these seven crosspoints in the switching networks.
Releasing a Connection
When the customer starts to dial, the scanner detects the change in the line
condition and notifies the ESS. The ESS arranges to have the dial tone removed
from the line. The CSN path is not released at this time, since it is needed later
in the call, for the ringing and the talking connections. The DM, on receipt of
the dial tone trunk terminal address and a "release B side" order, proceeds to
release the DSN path. A release mark voltage is placed on the trunk terminal.
This causes a pulse to be sent through the three gas diodes forming this part
of the dial tone connection. This pulse, in combination with the junctor release
pulse, causes the release of the entire connection in the DSN, thus removing the
dial tone. The identity of the dial tone trunk appears in the DM and is passed
to the central control.
Sec. 4 . 1 Introduction to the CM and DM Operations 105
4.1.2 The Ringing Connections
After the calling customer has dialed seven digits, the ringing con-
nections are set up. There are two stages in this operation, namely: (1), con-
necting audible ringing tone to the calling customer; and (2), connecting tone-
ringing current to the called line.
Connection for Audible Ringing Tone
In connecting the audible ringing tone, the central control obtains the
address of an idle audible ringing trunk in the signal switching network (SSN).
It passes this information to the CM, which sets up a connection from the SSN
to a trunk on the B side of the DSN. The equipment location of this trunk is
identified by the CM and passed to the central control. When the central control
receives the equipment location, it passes this information to the DM, which
proceeds to set up the connection in the DSN. The calling customer now receives
audible ringing tone.
Connection for Tone- Ringing Current
To set up the ringing connection to the called line, the central control passes
"connect" orders to the CM and DM. The markers set up the connections for
tone-ringing current through the CSN and DSN. Tone ringing is thus connected
to the called line.
4.1.3 The Called Customer Answers
After the called customer answers, the central control passes to the
CM and DM orders to release the ringing connections. The calling customer
connection in the CSN is not released, however.
When the "release" orders have been carried out, the central control passes
the "connect" orders for setting up the talking connection. The conversation
between the two customers can now proceed.
4.1.4 Disconnect
When either the calling customer or the called customer hangs up,
the ESS detects this change in condition. The central control passes "release"
orders to the CM and DM to release the talking connection.
This completes the marker operations involved in setting up and releasing
an intraoffice call.
106
Concentration and Distribution Markers
Chap. 4
CLIP
MOUNTING BAR
VG 402
FIG. 4-2. Mounting arrangements for the V/i-inch packages.
4 . 2 EQUIPMENT ARRANGEMENTS
4.2.1 Apparatus Elements
Each marker consists of many small circuits interconnected in pat-
terns to perform desired functions. The small apparatus and components in
these circuits are packaged on printed-wiring boards. The markers use two
sizes of such packages, as listed below:
(1) A IVi-inch package is used for all transistor and miscellaneous cir-
cuitry. The method of mounting such packages is shown in Fig. 4-2,
and described below.
Sec. 4 . 2 Equipment Arrangements 107
(2) A 7-inch package is used for ferrite core matrices and gas-diode cir-
cuitry. The mounting arrangement for such packages is shown in
Fig. 4-3, and described below.
Other items of marker apparatus whose size makes it impracticable to mount
in packages are shown in Fig. 4-4.
4.2.2 Apparatus Mounting Arrangements — Figs 4-2 and 4-3
Various mounting arrangements are used in the markers. Two of the
methods used are shown in Figs. 4-2 and 4-3.
The U/i-inch packages are mounted vertically on their long edges and are
plugged into connectors. The packages are aligned and supported by a bar
and a clip on the end opposite to the connectors, as shown in Fig. 4-2. The
connectors are mounted into mounting plates and are spaced at intervals of
either % inch or 1 inch along the plate.
The 7-inch packages are mounted horizontally in vertical columns that con-
sist of horizontal shelves and guides. Fig. 4-3, in a view looking upward, shows
how they are arranged. The packages are plugged into rigid wire terminals
located on the shelves. Two edge guides and a center guide provide alignment
for the mating of the terminals on a package with the terminals on its shelf.
These guides also serve to hold the plate securely in position.
The transformers, relays, terminal strips, and other pieces of apparatus not
mounted as packages (some examples are shown in Fig. 4-4) are secured to
mounting plates.
4.2.3 Cabinet Layout of the Concentration Marker
Front View (Fig. 4-5, page 110) and Front Equipment (Fig. 4-6, page 111)
The apparatus layout is the same for both the upper and lower parts of the
cabinet. Therefore, only the upper apparatus layout is described.
The upper half of the cabinet consists of seven mounting plates for the 1 V2-
inch packages. The plates are numbered bottom to top, on the left frame up-
right. Each mounting plate has space for mounting twenty-eight U/i-inch
packages. The plate positions are lettered left to right, A to Y, and AA to AF,
omitting I, O, S, and Z.
Directly below these seven mounting plates are four vertical columns. Each
column has a capacity of twelve 7-inch packages mounted horizontally. The
shelves are numbered bottom to top. The columns are lettered left to right.
108
Concentration and Distribution Markers
Chap. 4
7 INCH
PACKAGE
MOUNTING
GUIDE
RIGID WIRE
TERMINALS
A -> VG 403
FIG. 4-3. Mounting arrangements for the 1 -inch packages, seen from below.
Sec. 4 . 2 Equipment Arrangements 109
The power cut-in relays in the power interrupter circuit (door interlocks) are
mounted on the bottom inside panel of the cabinet. This panel is hinged to
allow access to the wiring side and the voltage filter panel located behind it.
The wire-spring relays switch all power of 350 volt-amperes or less. The power
relays switch all power greater than this.
The bottom front cabinet panel, beneath the sliding door, is hinged to allow
access to the fuses.
The relays in the marker transfer circuit are mounted on the framework
between the pair of markers. These relays connect the markers to the CSN.
The two concentration markers contain identical pieces of apparatus. But
in order that the circuits in each marker be electrically the same as the circuits
in its mate, the apparatus layout of marker 1 is reversed; that is, it is a mirror
image of marker 0. Therefore, corresponding pieces of apparatus do not have
the same location designations. For example, the apparatus in mounting plate
position B in marker will be in mounting plate position AE in marker 1.
The layout of the circuits in the front portion of the cabinet is shown in
Fig. 4-6, on page 111.
■\
•,J^J?T •» POWER RELAY
.... „, ,;•» WtRE SPRING
— ' RELAY
.TERM INAL______--^ r
STRIPS " C A.B.&C-
f . PULSE TRANSFORMERS
FIG. 4-4. Miscellaneous marker apparatus.
110
Concentration and Distribution Markers
Chap. 4
GUARD LAMPS
TEL JACKS -
VG405
FIG. 4-5. Concentration marker, front view.
Sec. 4.2
Equipment Arrangements
111
20
19
IB
17
SEQUENCE CONTROL
AND
TROUBLE INDICATOR
CODER
-
16
IS
14
TROUBLE INDICATOR
1 1
- TRK -
- RLS -
_ SEL _
- LINE -
- SEL -
- TRK -
- RLS -
_ SEL _
10
09
OB
07
06
05
04
03
- LINE -
- SEL -
OP
1
00
19
18
1 7
16
1 5
- LINE-
SEL
_ TRK -
RLS _
SEL
VERIF^
LINE
SEL _
- TRK -
- RLS -
- SEL -
~ SEL ~
~VERIF"
-
/
r
14
13
1?
1 1
to
TRK
- LEV -
- ID -
09
08
MARKER
TRANSFER
RELAYS
A
B
C
D
E
F
_Gj
H
J
K
L
M
N
P
O
R
T
U
-.TERMINAL
STRIPS
/
AA
BB
CC
DD
EE
FF
GG HH
LINE SELECTOR CONTROL
TRK RLS SEL CONTROL
SELECTOR VERIF
AND
TRK LEV ID
LINE SEL- TRK RLS SEL
SEL VERIF
Vts
POWER INTERRUPTER
RELAYS
MERCURY
CONTACT
RELAY
FIG. 4-6. Concentration marker, front equipment.
112
Concentration and Distribuion Markers
Chap. 4
TERM STRIPS
TRK LEV EN
AND
TBL DET
TRK LEV EN
AND
TBL DET
UPPER
GATE
A
B
13
TERM STRIPS
1?
11
10
09
-
08
07
06
05
04
03
02
0!
00
LOWER
GATE
FIG. 4-7. Concentration marker, rear equipment.
Rear Equipment {Fig. 4-7)
The rear equipment is mounted on an upper and a lower hinged gate, as
shown in Fig. 4-7. This arrangement allows easy access to the wiring side of
the equipment. The mounting arrangement of the top and bottom gates are
the same. Therefore, only the top gate arrangement is described.
There are fourteen mounting plates. Terminal strips are mounted on the
top plate, and the l^i-inch packages are mounted on the other thirteen plates.
The plates are numbered bottom to top. The bottom seven plates extend across
the width of the gate. The top seven plates are half-length plates. There are
Sec. 4.2 Equipment Arrangements 113
two vertical columns to the right of those seven half-length plates. The 7-inch
packages are mounted horizontally in those columns.
4.2.4 Cabinet Layout of the Distribution Marker
Front View (Fig. 4-8, page 114) and Front Equipment (Fig. 4-9, page 115)
The apparatus in the upper half of the cabinet controls the A side of the
distribution switching network (DSN). The apparatus in the lower half of the
cabinet controls the B side of the DSN. The apparatus layout in the upper
part is the same as the layout in the lower part. Therefore, only the upper
apparatus layout is described.
The upper half of the cabinet consists of four vertical columns. Each column
has a capacity of twelve 7-inch packages mounted horizontally. The shelves
are numbered from bottom to top. The columns are lettered left to right.
Directly below these four columns are seven mounting plates for 1^-inch
packages. The plates are numbered from bottom to top, on the left frame
upright. Each mounting plate has space for mounting twenty-eight 1^-inch
packages. The plate positions are lettered left to right, A to Y, and AA to
AF, omitting I, O, S, and Z.
The power cut-in relays in the power interrupter circuit (door interlocks)
are mounted on the bottom inside panel of the cabinet. This panel is hinged
to allow access to the wiring side and the voltage filter panel located behind it.
The wire-spring relays switch all power of 350 volt-amperes or less. The power
relays switch all power greater than this.
The bottom front cabinet pane], beneath the sliding door, is hinged to allow
access to the fuses.
The relays in the marker transfer circuit are mounted on the framework
between the pair of markers. These relays connect the markers to the DSN.
The two distribution markers contain identical pieces of apparatus. But, in
order that the circuits within each marker be electrically the same (as to wire
length, capacities, etc.), the apparatus layout of marker 1 is reversed. Marker 1
is a mirror image of marker 0. Therefore, corresponding pieces of apparatus
do not have the same location markings. For example, the apparatus in mount-
ing plate position B in marker will be in mounting plate position AE in
marker 1.
The layout of the circuits in the front portion of the cabinet is shown in
Fig. 4-9, on page 115.
114
Concentration and Distribution Markers
Chap. 4
TEL JACKS
GUARD LAMPS
-RED-
VG 408
FIG. 4-8. Distribution marker, front view.
Sec. 4.2
Equipment Arrangements
115
A
B
C
D
20
19
18
17
16
15
A-TR
< SEI
- A-TRK ID -
V
14
13
12
10
09
_ _
-
_
08
06
A-TRK SEL CONT
05
04
03
A-TRUNK SELECTOR
AND
A-TRUNK IDENTIFIER
-
02
01
A-"F" TRK SEL TBL DET
00
A-K"TRK SEL TBL DET
MARKER
TRANSFER
RELAYS
A
B
C
D
E
F
TERMINAL
STRIPS
G
H
J
K
L
M
N P
B- TRK SEI
_ B-TRK ID
B-TRK SEL CONT
B-TRUNK SELECTOR
AND
B-TRUNK IDENTIFIER
TERMINAL
-" STRIPS
AA
BB
CC
DD
EE
FF
GG
HH
J J
KK
LL
MM
FIG. 4-9. Distribution marker, front equipment.
116
Concentration and Distribution Markers
Chap. 4
13
TERM STRIPS
26
A
PROP
PULSER
15
25
14
12
1 1
10
-A- PROP PULSER -
AND
TBL DET
09
08
-A- PROP PULSER -
07
TBL DET CD
UPPER
06
05
04
03
0?
01
00
SEQUENCE CONTROL
GATE
A B
13
TERM STRIPS
26
B
PROP
PULSER
JTR
ENABLER
15
25
JTR
ENABLER
14
12
JTR RLS PULSER
1 1
10
B-PROP PULSER
- AND -
TBL IND
09
08
07
-B-PROP PULSER-
AND
-JTR EN TBL DET -
LOWER
06
05
04
03
02
01
00
- JUNCTOR ENABLER
AND
JTR EN TBL IND
GATE
VG 410
FIG. 4-10. Distribution marker, rear equipment.
Rear Equipment (Fig. 4-10)
The rear equipment is mounted on an upper and a lower hinged gate, as
shown in Fig. 4-10. This arrangement permits easy access to the wiring side
of the equipment. The equipment layout of the top and bottom gates are the
same. Therefore, only the layout of the top gate is described.
There are fourteen mounting plates for the IVi-inch packages. The plates
are numbered bottom to top. The bottom seven plates extend across the full
width of the gate. The top seven plates are half-length plates. There are two
vertical columns to the right of the seven half-length plates. The 7-inch packages
are mounted horizontally in these columns.
Sec. 4.2 Equipment Arrangements 117
4.2.5 Cabinet Doors and Gates
Door interlocks are provided on the rear gates and on the front
sliding doors of all markers. When a door or gate on an in-service marker is
opened, a signal is sent to the central control. An open door or gate on a
stand-by marker shuts off the power. A "door open" report is recorded on
the teletypewriter at the administration center.
4.2.6 Power Supply Cabinets
The power cabinets are used jointly by the switching networks and
the markers. Chapter 3, Switching Networks, covers the operation and use of
these power supplies.
4 . 3 METHOD OF OPERATION OF THE CONCENTRATION MARKER
The concentration marker (CM) controls the connections through the
concentration switching network (CSN) and the signal switching network (SSN).
The connections through these two networks are covered in Chapter 3, Switch-
ing Networks.
4.3.1 Network Orders
The concentration marker operations described in this section are
based on the network orders received from the central control. These orders
are: "connect"; "release"; "clear"; "trace"; "override busy"; and "reset".
The marker handles such network orders in a basic operational sequence as
follows :
(1) The marker receives a network order from the central control.
(2) Returns a check signal to the central control indicating receipt of
an order.
(3) Completes the order work in the switching networks.
(4) Returns an "operation successful" signal to the central control.
(5) Returns an "operation ended" signal to the central control.
(6) Returns a signal indicating whether the network terminal is idle or
busy.
118
Concentration and Distribution Markers
Chap. 4
(7) Receives a "reset" order (clear out) when the central control recog-
nizes the "operation ended" signal. This order resets all marker cir-
cuits that returned to the central control all such information as
"operation successful," "operation ended," "busy," etc. The marker
does not return a signal to indicate receipt of the "reset" order. The
"reset" order is sent in advance of all orders except the "clear" order.
Typical switching network orders required by the marker when setting up a
normal connection between two customers are shown in Table 4-1.
TABLE 4-1. TYPICAL SWITCHING NETWORK ORDERS TO THE MARKERS
Call Sequence
Orders to Markers
Customer starts call
(Scanner detects the off-hook condition).
Connect order and line address to CM.
Connect orders and trunk addresses to DM, to give dial tone to
calling customer.
First dial pulse
No action in CM.
Release order and trunk address to DM, to take down dial-tone
connection in DSN.
Called customer number
translated by ESS
Connect order and ringing tone terminal address in SSN to CM.
Connect orders and trunk terminal addresses in DSN to DM, for
ringing tone connection.
Connect order and audible ringing terminal address in SSN to CM.
Connect orders and trunk terminal addresses in DSN to DM, for
audible ringing connection.
Called customer answers
Release order and ringing tone terminal address in SSN to CM.
Release orders and trunk terminal address in DSN to DM (for
ringing tone connection).
Release order and audible ringing terminal address in SSN to CM.
Release order and trunk terminal address in DSN to DM (for
audible ringing connection).
Connect order and outgoing trunk terminal address in DSN to DM,
to set up a talking path between the customers.
Operation successful in setting
up talking path through network
No further operations required until the customers hang up.
Sec. 4.3 Method of Operation of the CM 119
4.3.2 Functions of CM Circuits (Fig. 4-11)
The major units within the CM are shown in Fig. 4-11, on page 120,
and their functions are listed in Table 4-2 below.
TABLE 4-2. FUNCTIONS OF THE CIRCUITS IN THE CM
Name of Circuit
Function of Circuit
Line Selector Verifier
Returns the customer line equipment location in the switching
network to the central control.
Line Selector
Marks the customer line network equipment location in the
switching network.
Line Selector Control
Controls the operating sequence of the line selector and line
selector verifier.
Trunk Level Enabler
Marks idle trunks between the CSN and the DSN
Trunk Release Selector
Marks the trunk equipment location to be released.
Trunk Release Selector Control
Controls the operating sequence of the trunk release selector
Trunk Level Identifier
and Match Detector
Detects when the customer line is connected to an idle trunk, and
identifies the equipment location of the trunk.
Trouble Detector Coder
Returns detected marker trouble to the scanner.
Sequence Control*
Furnishes pulses in sequence to the marker circuits, to set up
and take down network connections.
CONNECTING CIRCUITS
Marker Transfer
The relays in this circuit switch the network leads to either
marker or marker 1.
Stand-By Transfer
The relays in this circuit switch the central control leads to
either marker or marker 1.
The sequence control is the key circuit of the CM.
4.3.3 Sequence Control, or 1 Marker (Fig. 4-11)
The concentration marker (CM) sequence control, on receipt of a
network order, furnishes pulses to control the various circuits within the
marker. These pulses tell the circuits when to set up connections in the CSN
and SSN, and when to release them.
120
TO TONE SOURCES -»
TO LINES ON MDF ■*
Concentration and Distribution Markers
Chap. 4
SIGNAL SWITCHING NETWORK
F ■* —
CONCENTRATION SWITCHING NETWORK
• .:,- ;.. .:.. '"' . . . .".'.-.
CONCENTRATION MARKER
MARKER TRANSFER RELAYS
TO TRUNKS
ON A & B SIDES
OF DSN
u
STAND-BY TRANSFER RELAYS
CENTRAL CONTROL
KEY TO CIRCUITS
1 -LINE SELECTOR VERIFIER
2 -LINE SELECTOR
3 -LINE SELECTOR CONTROL
4 -TRUNK LEVEL ENABLER
5 -TRUNK RELEASE SELECTOR
6 -TRUNK RELEASE SELECTOR
CONTROL
7 — TRUNK LEVEL IDENTIFIER
AND MATCH DETECTOR
e- TROUBLE DETECTOR
9 — SEQUENCE CONTROL
FIG. 4-11. Concentration marker, block diagram.
The speed with which the circuits in the switching network will operate is
much slower than that of the circuits in the central control. The sequence
control can, however, accept the high-speed signals (network orders) from the
central control. It passes them at a slower rate of speed to the marker circuits
that control the switching networks.
After leaving an order with the marker, the central control continues its
work with other system programmed tasks. The system program arranges
periodically for the central control to check the progress of the marker in
setting up the CSN connections. When the central control recognizes the
"operation ended" signal, it sends the next order for continuing the path
through the CSN.
Sec. 4.3 Method of Operation of the CM 121
The sequence control may be considered, for the purpose of illustration, as
consisting of a number of circuits each having its own input from the central
control. Also, for this purpose, it may be considered that all the circuits use
the same four common outputs to the central control.
The inputs (orders) to the sequence control are:
(1) Connect A trunk (i.e., a trunk to the A side of the DSN).
(2) Connect B trunk (i.e., a trunk to the B side of the DSN).
(3) Trace.
(4) Release.
(5) Override busy.
(6) Clear.
(7) Reset.
The outputs from the sequence control that report the progress of the
marker to the central control are:
(1) Check (indicates the receipt of an order).
(2) Operation successful.
(3) Busy.
(4) Operation ended.
In order that you may understand the operation of the sequence control,
each type of order it serves is described separately.
"Connect A Trunk" Order— Line-to-Trunk Connection
The first order described is a "connect A trunk" order: i.e., a line-to-trunk
connection in the CSN. This order enables a path to be set up from a customer
line through the CSN to a trunk leading to the A side of the DSN. It is assumed
that the central control has passed the binary address of the customer line to
the line selector, and the "connect A" order to the sequence control. The line
selector will translate the binary address into a terminal equipment location
in the CSN, on receipt of a signal from the line selector control which is under
command of the sequence control. Before describing how the sequence control
handles this "connect" order, one more job remains to be done. That is to
reset the sequence control flip-flops that are used to indicate "operation ended,"
122 Concentration and Distribution Markers Chap. 4
"operation successful," etc., to the central control. This resetting is done by
sending a "reset" order in advance of each order, excepting the "clear" order.
The "connect" order sequence of operations is as follows:
(1) The central control sends a positive voltage on the "connect A" input
lead to start the sequence control.
(2) A check (CK) signal is returned to the central control, indicating
receipt of the order. The central control, on receiving the CK signal,
removes the "connect" order input voltage. No change in the sequence
control takes place.
(3) The 2-millisecond timer is started (the "connect" order time-out).
(4) The 250-microsecond timer is started (the busy-test time-out).
(5) A voltage pulse is sent to the trunk level identifier and match detector
circuit, and to the line selector verifier control circuit, to clear out
these circuits.
(6) The line selector control is started. This circuit controls the operation
of the line selector. The line selector translates the binary address,
which it received from the central control, into the line terminal
equipment location in the CSN. The selector then causes a marking
voltage to be placed on the selected line terminal.
(7) If a busy condition exists, a surge current operates an amplifier in
the CSN trunk level detector.
A single pulse then operates gates in the sequence control. This sets
the busy flip-flop and starts an "internal clear" sequence.
The trunk level identifier operates and identifies the trunk level to
which the busy line is connected. The trunk level is coded into binary
form and returned to the central control.
(8) If the customer line is not busy, the sequence control recognizes this
condition, since it will not receive a busy signal during the busy-test
timing interval.
(9) The 250-microsecond busy-test timer resets.
(10) The trunk enabler circuits are started.
The line selector verifier monitors the outputs of the line selector to
obtain the translated line terminal equipment location. It translates
Sec. 4.3 Method of Operation of the CM 123
this information back into a binary address and returns it to the
central control for verification.
The trunk level enabler marks in sequence the level of each of the five
trunks in the A group to the DSN. The trunk level detector, in the CSN,
recognizes when the line-to-trunk connection is completed, and in-
forms the trunk level identifier and match detector. The trunk level
identifier codes into binary form the trunk level on which the connec-
tion was completed, and returns this information to the central control.
(11) A pulse from the trunk level identifier and match detector circuit
causes the sequence control to return the "operation successful"
signal to the central control.
(12) The sequence control "internal clear" sequence is started.
(13) The "operation ended" signal is returned to the central control.
(14) The sequence control is now ready for the next order.
"Connect B Trunk" Order— Trunk-to-DSN Connection
This network order is identical with that for the A trunk. The sequence
control may be considered as divided into three parts:
(1) The equipment to serve side A.
(2) The equipment to serve side B.
(3) The equipment to serve both the A and the B sides.
"Trace" Order
The purpose of the "trace" order is to find out whether a connection exists
from the line through the CSN, and if so, to what CSN trunk. The "trace"
order is given before a "release" order. To illustrate, assume that the first
customer hangs up. The line equipment number in the CSN is known by the
central control. The trace operation applied to the line identifies the CSN trunk,
and hence, the DSN connection. After these are determined, a "release" order
is given to take down all the connections from this trunk side.
After the second customer hangs up, the line will not test busy because the
connection has already been taken down. Thus, when the "trace" order is given
by the central control, there will be no match trace pulse from the trunk level
124 Concentration and Distribution Markers Chap. 4
identifier and match detector circuits within the busy-test interval. At the end
of the timing interval, the "internal clear" sequence is started.
The sequence of operations for a "trace" order is as follows: A "reset"
order is sent along with the "trace" order to reset the sequence control flip-flops
that indicate "operation ended," "operation successful," etc., to the central
control.
(1) The central control sends a positive voltage on the trace input lead
to start the sequence control.
(2) A.CK signal is returned to the central control indicating receipt of
the order. The central control, on receiving the CK signal, removes
the trace input voltage. No change in the sequence control takes place.
(3) The 2-millisecond timer is started.
(4) The 250-microsecond busy-test timing is started.
(5) A voltage pulse is sent to the trunk level identifier and match detector
circuit and to the line selector verifier to clear out these circuits.
(6) The fine selector control is started. This circuit controls the operation
of the fine selector. The line selector translates the binary address,
which it received from the central control, into the line terminal
equipment location in the CSN. The selector then causes a marking
voltage to be placed on the selected line terminal.
(7) During the busy-test timing interval, if a busy condition exists, the
trunk level detector circuit in the CSN sends a pulse to the sequence
control. The busy flip-flop is set and the "internal clear" sequence is
started.
The trunk level identifier operates and codes the trunk level into
binary form, and returns this information to the central control.
(8) If no path exists through the terminal traced, a match pulse is not
sent to the sequence control.
(9) At the end of the busy-test timing interval, the timer is reset and the
"internal clear" sequence is started.
(10) On a "trace" order, the "operation successful" flip-flop is not in-
volved, and the central control reads only the busy indication.
(11) The "operation ended" signal is returned to the central control.
Sec. 4.3 Method of Operation of the CM 125
"Release" Order
When a path through the CSN is to be taken down because of a completed
call or for some other reason, a "release" order is sent to the CM. The release
is always made from the trunk side and never from the line side of the CSN.
A "reset" order is sent along with the "release" order to reset the sequence
control flip-flops that indicate "operation ended," "operation successful," etc.,
to the central control. The sequence of operations for the "release" order is
as follows:
(1) The central control sends a positive voltage on the release input lead
to the sequence control to start the circuit.
(2) A CK signal is returned to the central control indicating receipt of
the "release" order.
(3) The central control, on receiving the CK signal, removes the release
input voltage. No change in the sequence control takes place.
(4) The 2-millisecond timer is started (the "release" order time-out).
(5) A voltage pulse sent to the trunk release selector, causes it to clear
out the line selector verifier circuit and the trunk level and match
detector circuit.
(6) The trunk release selector also causes a diode in the talking path of
the line to be back-biased. This deionizes the gas diode tube, and thus
opens the path through the crosspoint.
(7) The resulting current change is detected in the trunk level identifier
and match detector circuit. This causes a pulse to be sent to the
sequence control to start:
(a) The "operation successful" signal to the central control.
(b) The sequence control "internal clear" sequence.
(c) The "operation ended" signal to the central control.
"Over-Ride Busy Order with "Connect" Order
The necessity to use the "over-ride busy" order arises under special circum-
stances. Under ordinary operation, attempting to break into a busy path will
cause a busy indication, and the sequence control will clear itself. By the use
of the "over-ride busy" order, on "connect" orders, a special gate in the
sequence control prevents clear out during the busy-test interval. Thus, a pulse
126 Concentration and Distribution Markers Chap. 4
that comes because of a busy path cannot clear out the sequence control, and
the trunk enabler is started. This sets up a new connection into the busy path.
The pulse that is received when the new connection is made, causes the setting
of the "operation successful" flip-flop, and starts the "internal clear" sequence.
This order is used to set up a talking path through the SSN. A special SSN
input terminal is provided for each ringing trunk. When this input terminal
is connected to the two ends of the ringing trunk a "talking path" is set up
between the two ends of the ringing trunk. The first connection between the
input terminal and one end of the ringing trunk uses a standard "connect"
order. The second connection between the input terminal and the other end
of the ringing trunk requires the "over-ride busy" with a "connect" order.
"Clear" Order
A "clear" order is used for testing, or for analyzing trouble. The central
control does not require the return of a check signal to indicate the receipt of
this order. Unlike all other orders, a reset signal is not sent in advance of a
"clear" order.
The "clear" order consists of a positive voltage from the central control. It
resets the busy-test delay, and starts the "internal clear" sequence.
If an order is in progress in the sequence control, and the central control
wishes to cancel that order, a "clear" order can be given to the sequence control.
A "clear" order may also be given if the check (CK) output to the central
control remains positive (because of some circuit fault) after the operation is
ended.
"Internal Clear" Sequence
The "internal clear" sequence within the sequence control occurs under the
following conditions:
(1) When the marker has successfully completed its work in connection
with a network order.
(2) When the marker cannot complete its work within the time allowed
(a time-out starts the "internal clear" sequence).
(3) When the central control sends a "clear" order, as explained under
"Clear" Order.
Sec. 4.3 Method of Operation of the CM 127
The operational sequence of clearing the sequence control, when it receives
a "clear" order from the central control, is as follows:
(1) The trunk level enabler is turned off.
(2) The 2-millisecond timer is reset.
(3) A 250-miscrosecond timer is started.
(4) At the end of the 250-microsecond delay, the timer is reset.
(5) The release voltages are removed from the anodes of the release and
line selector gas tubes. Deionization of the gas tubes starts.
(6) Another 250-microsecond timer starts.
(7) At the end of the 250-microsecond delay, the timer is reset.
(8) Normal voltage is restored on the anodes of the gas tubes in the
release and line selectors.
The trunk and line identifier cores are read out.
(9) The 50-microsecond timer is started. This delay insures that the iden-
tifier cores are properly set before the "operation ended" signal is
returned to the central control.
(10) The 50-microsecond timer is reset.
(11) The "operation ended" signal is returned to the central control.
(12) The sequence control is now ready for the next call.
4.3.4 Line Selector Control, or 1 Marker (Fig. 4-11)
The line selector control consists of amplifiers, flip-flops, set gates,
ferrite cores, and release pulsers.
The line selector control acts on signal orders received from. the sequence
control to operate and control the line selector. It sets and reads the vertical
and horizontal translator cores, and turns on and off the memory amplifiers
in the F and K sections of the line selectors.
4.3.5 Line Selector, or 1 Marker (Fig. 4-11)
The line selector is used to mark the line terminal in the CSN or the
tone source terminal in the SSN. To do this, the selector translates a coded
128 Concentration and Distribution Markers Chap. 4
signal (a binary address) into a switch and terminal equipment location in the
CSN or the SSN. The translation is made through a combination of positive
and negative amplifiers, and core matrices. The selector is divided into two
parts, F and K, with F and K input leads from the central control, and F
and K output leads to the CSN and SSN. Signals through the F part of the
selector determine the network switch location. Signals through the K part of
the selector determine the terminal (level) within the network switch.
The central control sends a twelve-bit binary address over F and K leads to
the selector. This address is translated within the selector into two output
signals, F and K, to the network. These signals fire the gas diode crosspoint
associated with the selected network terminals.
4.3.6 Line Selector Verifier, or 1 Marker (Fig. 4-11)
The line selector verifier is used to monitor the line selector output
leads to the network. It translates this network terminal equipment location
back into a binary address, and returns it to the central control. The network
terminal equipment location is received by the line selector verifier as a two-
part input address, i.e., F and K. This address is passed through a combina-
tion of amplifiers, flip-flops, and translator core matrices. The translation pro-
vided by the verifier is passed as a twelve-bit binary address to the central
control. The central control can compare this address with that of the line
selector verifier in the stand-by CM. When a mismatch is recognized, the central
control arranges to have it recorded by the teletypewriter at the administration
center.
4.3.7 Trunk Level Enabler, or 1 Marker, (Fig. 4-11)
The trunk level enabler marks the first idle trunk in the CSN to which
the customer line has access. The enabler also serves the SSN in the same way,
marking the first idle trunk to which the selected tone ringing or audible ringing
tone circuit has access.
The trunk level enabler is under command of the sequence control. It con-
sists of amplifiers, core matrices, delay circuits, and pulse amplifiers. It applies,
in sequence, a negative pulse to each CSN trunk level in the A or B group. This
negative pulse appears with the pulse from the line selector on the gas diode
crosspoint to the idle trunk, firing the gas diode. The trunk level detector in
the CSN receives a surge of this current and sends it to the trunk level identifier
and match detector.
Sec. 4.3 Method of Operation of the CM 129
4.3.8 Trunk Level Identifier and Match Detector, or 1 Marker (Fig. 4-11)
On receipt of a pulse from the trunk level detector, the trunk level
identifier and match detector circuit recognizes that the customer line is matched
to an idle trunk, after which it identifies the equipment level of the trunk.
The circuit consists of a combination of amplifiers, flip-flops, positive and
negative identifier core matrices, and coupling and shunting networks. The
trunk level translation that this circuit provides is passed to the central control
as a binary address. This circuit also notifies the sequence control to stop all
operations, and to turn off the trunk level enabler and line selector.
The talking and signaling path to the customer through the CSN is now
complete. The path is held by a voltage through the gas diode crosspoint to
ground at the trunk level detector in the CSN.
4.3.9 Trunk Release Selector Control, or 7 Marker (Fig. 4-11)
The trunk release selector control is made up of amplifiers, flip-flops,
setgates, and release pulsers.
The trunk release selector control circuit acts on orders from the sequence
control to operate and control the trunk release selector. It sets and reads the
cores, and turns on and off the memory amplifiers in the trunk release selector.
4.3.10 Trunk Release Selector, or 1 Marker (Fig. 4-11)
The trunk release selector circuit starts the release of the connection
in the CSN. The selector does this work upon orders from the sequence control.
The trunk release selector translates a coded signal (a binary address) into
the trunk equipment location of the trunk to be disconnected. The translation
is made through a combination of positive and negative amplifiers, and core
matrices. The selector equipment is divided into two parts, F and K, with F
and K input leads from the sequence control, and F and K output leads to the
CSN and SSN. Signals through the F part of the selector determine the network
switch location. Signals through the K part of the selector determine the ter-
minal (level) within the network switch.
The trunk release selector receives a ten-bit binary address from the central
control over the F and K leads. The input address is translated into two output
signals. The two output signals are then passed to the network, as positive
and negative outputs, over the F and K leads. This "disconnect" mark causes
a back-bias to be placed on a diode in the talking path, thus deionizing the
crosspoint diode. This results in the release of the SSN or the CSN connections.
130 Concentration and Distribution Markers Chap. 4
4 . 4 METHOD OF OPERATION OF THE DISTRIBUTION MARKER
The distribution marker (DM) controls the connection and disconnec-
tion of the paths through the distribution switching network (DSN) under
command of the central control. The DSN has trunks connected to both its A
side and its B side. The connections through the DSN are covered in Chapter 3,
Switching Networks.
The two principal jobs handled by the DM in connection with the distribution
switching network are: (1), connections; and (2), disconnections.
The DM is also capable of reporting on the following:
(1) Whether a busy condition exists on a network connection.
(2) Whether the network operation was successful or Unsuccessful.
(3) Whether a trouble condition exists in the marker.
(4) And when the marker work is finished {operation ended).
The DSN paths set up by the distribution marker are:
(1) Dial tone.
(2) Ringing.
(3) Talking.
(4) Other signals and tones such as busy, reorder, etc.
A path through the DSN is obtained by putting marking voltages on the
equipment terminals between which a transmission path is requested by the
central control. As a result of these marking voltages, several possible network
paths are made available between the two marked terminals. However, only
one of these paths is set up by enabling only one junctor at a time.
4.4.1 Functions of the DM circuits (Fig. 4-12)
The major units within the DM are shown in Fig. 4-12, on page 132,
and their functions are listed in Table 4-3, opposite.
4.4.2 Sequence Control, or 1 Marker (Fig. 4-12)
The sequence control circuit in the DM is similar to the sequence
control circuit in the CM. However, in the following text no cross-referencing
has been used, although many of the features and circuit operations are the
same. The cross-referencing was omitted to provide continuity of reading.
Sec. 4.4 Method of Operation of the DM 1 3 1
TABLE 4-3. FUNCTIONS OF THE CIRCUITS IN THE DM
Name of Circuit
Function of Circuit
Trunk Identifiers, A or B
Return the trunk equipment location in the DSN to the central
control.
Trunk Selector, A or B
Mark the trunk network equipment location in the A or B side
of the DSN.
Trunk Selector Controls, A or B
Control the operational sequence of the trunk selectors.
Propagator Pulser, A or B
The A propagator pulser furnishes the fan-out current for the
linkage between switching stages 1 and 2. Propagator pulser
B similarly serves stages 5 and 6.
Junctor Enabler
Controls the completion of the path from the A to the B side
of the network by selecting a junctor to connect the two halves
of the network.
Junctor Release Pulser
Controls the release of the junctor path in the network.
Trouble Detector Coder
Returns troubles detected in the markers to the scanner.
Sequence Control*
Furnishes pulses required by the markers to set up and take
down connections in the DSN.
CONNECTING CIRCUITS
Marker Transfer
The relays in this circuit switch the network leads to either
marker or marker 1.
Stand-By Transfer
The relays in this circuit switch the central control leads to
either marker or marker 1.
The sequence control is the key circuit of the DM.
The DM sequence control, on receipt of a network order, furnishes pulses
to control the various DM circuits. These pulses cause the circuits to set up
and release connections in the DSN.
The operating speed of the circuits in the DSN is in milliseconds, whereas
the speed of the central control is in microseconds, a thousand times as fast.
To match the slow speed of the DSN to the high speed of the central control,
a sequence control circuit is used. The sequence control accepts the high-speed
signals from the central control, and then passes them in sequence (and at a
slower rate) to the marker circuits that control the DSN.
132
Concentration and Distribution Markers
Chap. 4
A SIDE
TO CSN
DISTRIBUTION SWITCHING NETWORK
STAGES
DISTRIBUTION MARKER
B SIDE
TO CSN
TO OGT
MARKER TRANSFER RELAYS
F=I
3 4 I 5 6 17 h— I 8 f— H
F-T J T T 1 ^-^
'0
STAND-BY TRANSFER RELAYS
CENTRAL CONTROL
FOR A SIDE DSN
I - TRUNK IDENTIFIER
2- TRUNK SELECTOR
3 -TRUNK SELECTOR CONTROL
4 -PROPAGATOR PULSER
KEY TO CIRCUITS
FOR B SIDE DSN
7- PROPAGATOR PULSER
8- TRUNK SELECTOR CONTROL
9- TRUNK SELECTOR
10- TRUNK IDENTIFIER
5 -JUNCTOR ENABLER
6 - JUNCTOR RELEASE PULSER
11 -TROUBLE DETECTOR CODER
12- SEQUENCE CONTROL
FIG. 4-12. Distribution marker, block diagram.
VG 412
After leaving an order with the marker, the central control continues its
work with other system programmed tasks. The system program arranges
periodically for the central control to check the progress of the marker in
setting up the DSN connections. When the central control recognizes the
"operation ended" signal, it sends the next order for continuing the path
through the DSN. The answer signals from the marker permit the central
control to follow the progress of the path through the DSN.
The sequence control may be considered, for the purpose of illustration, as
consisting of a number of circuits each having its own input from the central
Sec. 4.4 Method of Operation of the DM 133
control. Also, for this purpose, it may be considered that all the circuits use the
same four common outputs to the central control.
The inputs (orders) to the sequence control are:
(1) Connect.
(2) Release from the A side.
(3) Release from the B side.
(4) Connect for test.
(5) Clear.
(6) Reset.
The progress report returned to the central control covers three pieces of
information:
(1) The completion of an operation.
(2) Its success or failure.
(3) On unsuccessful connections, a progress report tells whether a failure
was caused by encountering a busy terminal, or by failure to make a
connection. This latter case may be caused by a fault in the system,
or by the inability to find an idle path from an available junctor to
the desired terminals (i.e., blocking).
To illustrate the operation of the sequence control, each type of order that
it handles is described separately. The first order described is a "connect" order.
This order enables a path to be set up from the A side of the DSN to the B side.
"A and B Side Connect" Order in DSN
Assume that the central control has passed a binary address to both the
A and B trunk selectors. The trunk selectors will translate these addresses into
trunk terminal equipment locations in the DSN, on receipt of a signal from
the trunk selector control circuits. These control circuits are under command
of the sequence control. Before the sequence control can handle the "connect"
order, one other job remains to be done. That job is to reset the sequence
control flip-flops that are used to indicate "operation ended," "operation
successful," etc., to the central control. This resetting is done by sending a
"reset" order in advance of each new order, excepting the "clear" order.
On receipt of the "connect" order, the sequence control sets the following
marker circuits in operation:
134 Concentration and Distribution Markers Chap. 4
(1) A and B propagator pulser;
(2) A and B trunk selector control; and
(3) A and B trunk identifiers (to clear out the identifier cores).
A positive voltage on the CK check lead notifies the central control that the
"connect" order has been received. The central control then removes the
"connect" order input voltage. During the busy-test delay interval, the A and
B trunk selector control circuits mark the end terminals of the trunk to be
connected. If these trunk network terminals test busy, a surge current sent to
the hold supply operates the junctor match and release detector circuit. This
causes a pulse to be sent to the sequence control to start an "internal clear"
sequence.
The junctor enabler is not started on a "connect" order when a trunk tests
busy. The sequence control sends a positive voltage signal over the busy lead
to the central control to indicate the busy trunk condition. At the end of the
"internal clear" sequence, the sequence control sends a positive voltage signal
to the central control over the OPE lead. At the end of this "operation ended"
indication, the marker is ready for a new order.
When the trunk to be connected is not busy, and no idle path from a junctor
to the selected trunk terminal is found, the busy-test delay interval passes. The
busy-test delay is reset without a busy indication being sent by the junctor
match and release detector circuit. The junctor enabler is started, since the
sequence control received a "connect" order. However, at the end of the 20-
millisecond time-out period, because the junctor enabler has not seized an idle
junctor, an "internal clear" sequence is started in the sequence control. The
sequence control returns the "operation ended" signal without an "operation
successful" or a "busy" signal. The central control recognizes this condition as
a block in the DSN. The DM is now ready for the next order.
When the trunk to be connected is not busy, and the junctor enabler has
seized an idle junctor, the junctor latch tube (in the DSN) receives the mark
voltages from both sides of the network; with the junctor enabler signal, it fires
the tube. This completes the path through the DSN. A match pulse (from the
junctor match and release detector in the DSN) is generated by the resulting
holding current. It indicates the successful completion of the connection. The
sequence control returns the "operation successful" and "operation ended"
signals to the central control. The DM is now ready for the next order.
Sec. 4.4 Method of Operation of the DM 135
"Internal Clear" Order
The "internal clear" sequence within the sequence control occurs under the
following conditions:
(1) When the marker has successfully completed its work in connection
with a network order.
(2) When the marker can not complete its work within the time allowed
(a time-out starts the "internal clear" sequence).
(3) When the central control sends a "clear" order, as explained under
"Clear" Order.
The "internal clear" sequences of operations within the sequence control,
for a "connect" order and for a "release" order, are outlined below to show
the circuits affected in each case.
"Internal Clear" Sequence for a "Connect" Order
(1) The sequence control sends a pulse to the A and B trunk selector
control circuits and the A and B propagator pulsers.
(2) This starts the deionization of the gas triode tubes in the output of
these circuits.
(3) The 20-millisecond timer is reset.
(4) The junctor enabler is turned off.
(5) The 250-microsecond delay timer is started.
(6) At the end of the 250-microsecond delay interval, the timer is reset.
(7) A pulse is sent to the A and B propagator pulsers and the A and B
trunk selector circuits to restore normal voltages.
(8) The 50-microsecond delay timer is started.
(9) At the end of this delay interval, a pulse is sent to the trunk identifiers.
(10) This causes the A and B trunk identifier cores to be read.
(11) The 1 5-microsecond timer is started to insure that the identifier cores
are read out before the "operation ended" signal is sent to the central
control.
(12) At the end of this delay interval, this timer is reset.
136 Concentration and Distribution Markers Chap. 4
(13) A positive voltage signal is sent to the central control over the OPE
lead to indicate "operation ended."
(14) The sequence control is ready to receive the next order.
"Internal Clear''' Sequence for a "Release" Order
(1) The sequence control sends a pulse to the A and B trunk selector
control circuits.
(2) This starts the deionization of the gas triode tubes in the output of
these circuits.
(3) The 2-millisecond timer is reset (the "release" time-out).
(4) The 250-microsecond delay timer is started.
(5) The 250-microsecond timer times out.
(6) A pulse is sent to stop the junctor release pulser.
(7) A pulse is sent to the A and B trunk selectors to restore normal
voltages.
(8) The 50-microsecond timer is started.
(9) At the end of this time interval, a pulse is sent to the A and B trunk
identifiers.
(10) The A and B trunk identifier cores are read.
(11) The 1.5-millisecond timer is started.
(12) The junctor release tube deionizes.
(13) The 1.5-millisecond timer times out.
(14) A pulse sets the "operation ended" flip-flops.
(15) The sequence control is ready to receive the next order.
An over-all 30-millisecond time-out interval is provided. This timer is started
upon receipt of an order. In the event that no voltage appears on the OPE
"operation ended" lead before the end of this time-out interval, the order flip-
flops will be cleared.
"Connect for a Test" Order
The junctors in the DSN may be tested by a programmed test. This involves
stepping the junctors one at a time. The order sequence of setting up the test
Sec. 4.4 Method of Operation of the DM 137
connections is the same as for a regular "connect" order with the exception
of the following:
(1) The "connect for test" flip-flop is set.
(2) The 1.5-millisecond busy-test timing is started.
(3) A test set gate starts the junctor enabler. This permits the junctor to
advance one step.
(4) The test time-out delay is 2 milliseconds instead of 20 milliseconds.
"Release A Side" Order
When a connection in the DSN is to be released from the A side, the central
control passes the binary address (of the trunk to be disconnected) to the A
trunk selector. This selector translates the binary address into a trunk terminal
equipment location on the A side of the DSN on receipt of a signal from the
trunk selector control.
A "reset" order is sent along with the "release" order. This order resets the
sequence control flip-flops that indicate "operation ended," "operation suc-
cessful," etc., to the central control.
The central control then sends the "release A side" order to the sequence
control. This order sets the RLA (release A side) flip-flop. The sequence control
then sends a signal to the A trunk selector control. The trunk selector control
signals the trunk selector to place a voltage mark on the trunk terminal to be
disconnected. A 2-millisecond timer and a 250-microsecond busy timing in-
terval is started. The junctor release pulser is started. The A and B trunk
identifiers are cleared. The tube in the junctor that receives the end terminal
mark is fired. This causes the hold current to shift to the release pulser. The
change in the hold current causes the junctor match and release detector circuit
to send a pulse to the sequence control.
During the first 250-microsecond time-out interval, if the marked terminal
is busy, a pulse from the junctor match and release detector circuit sets the
sequence control busy flip-flop.
The junctor match and release detector sends a signal to start the "internal
clear" sequence of the sequence control. It also causes the "operation successful"
flip-flop to be set. The operation of the "internal clear" signal is the same as on
a "connect" order, except that a 1.5-millisecond delay is used instead of a 15-
microsecond delay. The 1.5-millisecond delay is required to insure deionization
138 Concentration and Distribution Markers Chap. 4
of the junctor release tube. This tube starts to deionize when the release pulser
is turned off. On completion of this delay, a positive voltage is sent to the
central control indicating "operation ended."
If the trunk network terminal is not busy, the sequence control recognizes
this condition, since it will not receive a busy signal during the busy-test timing
interval.
The 250-microsecond busy-test timer times out.
The sequence control returns the "operation ended", "not busy", and "oper-
ation not successful" signals to the central control.
"Release B Side" Order
The "release B side" sequence is the same as the "release A side" sequence
except that the B trunk selector is energized instead of the A side trunk selector.
"Clear" Order
If an order is in progress in the sequence control, and the central control
desires to change it (without waiting for completion of the time-out period), a
"clear" order can be given to the sequence control. A "clear" order may also
be given if the check (CK) output to the central control remains positive (be-
cause of some circuit fault) after the operation is ended.
The "clear" order consists of a positive voltage from the central control. It
resets the busy-test delay, and starts the "internal clear" sequence. The "clear"
order positive voltage is removed by the central control within 200 microseconds.
4.4.3 Trunk Selector Control, A or B Side, or 1 Marker (Fig. 4-12)
A trunk selector control is connected to the A and B selectors. It is
made up of amplifiers, flip-flops, setgates, and release pulsers.
The trunk selector control acts on signal orders received from the sequence
control to operate and control the trunk selector. The trunk selector control
sets and reads the vertical and horizontal translator cores. It also turns on and
off the memory amplifiers in the F and K sections of the trunk selector.
4.4.4 Trunk Selector, A or B Side, or 1 Marker (Fig. 4-12)
The trunk selectors A or B control the connection of trunks on the
A and B sides of the DSN. Both selectors are identical.
Sec. 4.4 Method of Operation of the DM 1 39
The trunk selector receives a nine-bit binary address from the central control
corresponding to a particular network trunk terminal in the DSN. It places a
voltage mark on that network trunk terminal, and later removes it when
ordered by the sequence control.
The selector translates the coded signal (a binary address) into the trunk
equipment location in the network. The translation is made through a combi-
nation of positive and negative amplifiers, and core matrices. The selector is
divided into two parts, F and K, with F and K input leads from the central
control and F and K output leads to the DSN. Signals through the F part of
the selector determine the network switch location. Signals through the K part
of the selector determine the terminal (level) within this network switch.
The selector receives the nine-bit binary address from the central control
over F and K leads. The input address is translated into two output signals.
The two output signals are then passed to the network as positive and negative
outputs, over F and K leads, to make active the network terminals selected.
Each network terminal contains a resistor as well as a gas diode which com-
pletes the selected path.
4.4.5 Trunk Identifier, A or B Side, or 1 Marker (Fig. 4-12)
The primary use of the trunk identifier is to obtain the second trunk
terminal address in the DSN and send it to the central control. There are two
trunk identifiers in the DM. One serves the A side, the other the B side of the
DSN. The trunk identifiers, on obtaining the trunk terminal location in the DSN,
process this information in the opposite order to that of the trunk selectors:
i.e., the equipment location is translated back into the original order or address.
The central control can compare the information received from the in-service
marker trunk identifier with that received from the stand-by marker trunk
identifier. When the central control recognizes a mismatch, it is recorded on the
teletypewriter. Programmed routines are automatically started by the system.
The trunk identifier is made up of two sections, F and K. These consist of
a combination of amplifiers, flip-flops, identifiers, and core matrices.
The trunk identifier receives the trunk terminal equipment location in the
DSN as a two-part address over the F and K leads. The two-part input address
is then translated, in the F and K sections of the trunk identifier, and passed
as a nine-bit binary address to the central control. As previously explained,
the central control compares this address with that received from the stand-by
marker trunk identifier.
140 Concentration and Distribution Markers Chap. 4
4.4.6 Propagator Pulser, A or B Side, or 1 Marker (Fig. 4-12)
The description of the trunk selector covered the selection and
marking of network trunk terminals in stage 1 of the A side and stage 6 of the
B side of the DSN. The transmission path between these terminals is through
switching stages 1, 2, 3, on the A side and 4, 5, 6, on the B side of the DSN.
The propagator pulsers are made up of a combination of flip-flops, amplifiers,
and release pulsers. The propagator pulsers receive their signal orders from the
sequence control circuit. Ten A propagator pulsers furnish the fan-out current
for the linkage between stages 1 and 2. Ten B propagator pulsers serve the link-
age between stages 5 and 6. All ten A and ten B propagators are pulsed at
the same time.
When a mark voltage is applied to the network trunk terminal at either end
of the DSN, the voltage drop across the first tube exceeds the breakdown
potential so that it fires. Firing the first tube in stage 1 or stage 6 shifts the
input voltage to the associated propagator. This voltage shift is applied through
a capacitor and superimposed on the anode of the propagator tube, causing it
to fire. The propagator pulser then supplies a current into the link clamp. This
sets up a fixed marking voltage for the second-stage crosspoint tubes. The volt-
age applied to the second-stage tubes causes them to fire. The firing of the tubes
continues from each side of the DSN until the mark voltages reach the junctor
circuits. The gas diodes leading to busy paths are not fired.
A voltage pulse is sent to the trunk release selector. This causes the clearing
of the line selector verifier circuit and the trunk level and match detector circuit.
4.4.7 Junctor Enabler, or 1 Marker (Fig. 4-12)
The description of the propagator pulser covered the transmission
path from the opposite sides of the DSN through the intermediate stages of
the network. The junctor enabler in the DM controls the completion of this
path by selecting a junctor in the DSN to connect these two sides of the network.
The junctors in the DSN function with the following circuits:
(1) The junctor enabler (in the DM).
(2) The junctor release pulser (in the DM).
(3) The junctor match and release detector (in the DSN).
A general description of the junctor enabler operation is given in the following
unnumbered paragraphs.
Sec. 4.4 Method of Operation of the DM 141
The junctor enabler consists of amplifiers, core matrices, delay circuits, and
pulse amplifiers. One junctor enabler circuit is furnished per DM. The junctor
enabler acts on orders received from the sequence control.
When the sequence is started by an order from the central control, the propa-
gator pulsers are turned on, and the time-out pulser in the sequence control is
set. This pulser measures the interval in which to set up a connection. The busy-
check delay circuit in the sequence control is started. If either of the end trunk
terminals is busy within the check period, the junctor enabler is not started,
and the operation is concluded.
When both end trunk terminals are idle, the junctor enabler is set in opera-
tion. The junctor circuit in the DSN recognizes the arrival of marks (voltages)
from the two ends of the network. The junctor enabler tests the junctors, in
sequence, for the presence of the mark voltages. These two mark voltages in
combination with the junctor enabler signal fire the junctor latch tube. This
completes the paths from the marked trunk terminals through the six stages of
the DSN to the holding potential. A match pulse is generated by the resulting
holding current. It indicates the successful completion of the connection.
At the end of the time-out, if neither a successful match nor a busy signal
is received, the time-out pulsers report this to the central control. Also, the
network controls (selectors, identifiers, propagators, etc.) are cleared.
A clearing signal can be started by:
(1) The match and release detector (in the DSN).
(2) The connect or release time-out pulser (in the sequence control).
(3) The central control.
4.4.8 Junctor Release Pulser, or 7 Marker (Fig. 4-12)
The job of the junctor release pulser is to start the release of the
junctor path in the network upon receipt of orders from the sequence control.
The orders are carried out in sequence by a combination of flip-flops, amplifiers,
and passive delay circuits. The release pulse is applied to all junctors. This fires
a release tube in the junctor which received a pulse from the marked trunk
terminal. The fired release tube removes the hold current from the latch tube.
When the current in the latch tube has decreased below the minimum sus-
taining current, deionization takes place. Then the release tube in the junctor is
deionized by the removal of the common release pulse. This completes the
network release.
142 Concentration and Distribution Markers Chap. 4
4 . 5 METHOD OF OPERATION OF MISCELLANEOUS CIRCUITS
4.5.1 Marker Transfer Circuit — Distribution Marker
The DM transfer circuit consists of a group of wire-spring relays con-
nected in parallel. The operation of the relays is directed by the central control.
The leads from the DSN are wired to the fixed contacts. Markers and 1 are
wired to the break and the make contacts, respectively. This arrangement
permits switching all the network leads at the same time, to either marker
or marker 1 .
The transfer relays have two windings. If one winding goes open, the second
winding can be used. This eliminates the need to replace the relay during a
busy period.
A mercury-contact relay under control of the administration center controls
the operation of the transfer relays. The mercury-contact relay should be tested
or replaced only when distribution marker is in service. This is because the
network leads to marker are wired to the break contacts of the wire-spring
relays.
4.5.2 Marker Transfer Circuit — Concentration Marker
The operation of the relay transfer circuit for the CM and the SSN
network is similar to the operation described for the DM and the DSN.
4.5.3 Power Interrupter Circuit-Interlocks — Distribution Marker
The DM circuit contains twenty-five voltages ranging from +547
volts to —115 volts. To prevent hazardous maintenance conditions in the
stand-by marker, all high voltages are automatically removed when either the
front sliding door or one of the rear gates is opened. Green guard lamps in
the front and rear of the cabinet light to indicate when the hazardous voltages
have been removed. At this time, package changing and other maintenance
work may proceed.
The voltages are not removed from the in-service marker when a sliding
door or rear gate is opened. This is indicated by the absence of a lighted green
guard lamp. Marker operation is not interrupted. An "open door" signal is
recorded on the teletypewriter, in addition to visible and audible alarms at
the administration center.
The power interrupter relay circuitry is arranged to remove and connect
the voltages in a definite order. Removing the voltages in a definite order
Sec. 4.5
Operation of Miscellaneous Circuits
143
prevents false operation of the gas tube amplifiers in the trunk selector. Re-
connecting the voltages in a definite order insures that the flip-flops are put in
their idle state; in addition, this prevents false circuit operations.
The +1.5 and —4.5 volts used for transistor biasing are not removed by the
interlock circuit. This is done to prevent excessive current through the transistors
when other voltages are removed or connected.
4.5.4 Power Interrupter Circuit-Interlocks — Concentration Marker
The power interrupter circuit (interlocks) for the CM is similar to
that used in the DM.
4.5.5 Trouble Detectors or 1, Concentration Marker (Fig. 4-13)
Trouble-detecting circuits are provided with the following CM circuits:
(1) Line selector.
(2) Trunk enabler.
(3) Trunk release selector.
LINE
SELECTOR
HC
LJ
TRUNK
ENABLER
TRUNK RELEASE
SELECTOR
TROUBLE DETECTOR CODER
SEQUENCE
CONTROL
STAND-BY
TRANSFER
□
T D T D
A (0-4)
TO
CENTRAL CONTROL
FIG. 4-13. Concentration marker, block diagram of trouble detector.
144
Concentration and Distribution Markers
Chap. 4
TRUNK SELECTORS
PROPAGATORS
T D i TD I I TD • TO TD ! TD
r It TT TT D_J
TROUBLE DETECTOR CODER
RESET
SEQUENCE CONTROL
STAND-BY TRANSFER
JUNCTOR ENABLER
A (0-6')
CENTRAL CONTROL VG 414
FIG. 4-14. Distribution marker, block diagram of trouble detector.
The trouble-detecting circuits detect the failure of an output amplifier to
turn on or off; they also detect the condition that results when more than one
amplifier tube is turned on.
The sequence control programs the input orders from the central control to
the trunk selectors, propagators, and enabler, and their associated trouble-
detecting circuits. This circuit arrangement permits the trouble-detecting circuits
to check whether the circuits obeyed the orders. The logic circuitry within a
trouble detector transmits this information to the marker trouble-detector coder.
The coded information is picked up by the scanner and relayed to the central
control. The central control then notifies the administration center to type out
a trouble report. The stand-by marker is switched into service. A reset signal
restores the trouble-detector coder to normal. A test program is automatically
started to locate the trouble.
Sec. 4.5 Operation of Miscellaneous Circuits 145
4.5.6 Trouble Detectors or 1, Distribution Marker (Fig. 4-14)
Trouble-detecting circuits are provided with the following DM circuits:
(1) Trunk selectors A and B.
(2) Propagator pulsers A and B.
(3) Junctor enabler.
The DM trouble-detecting circuits operate in the same way as those described
for the CM in subsection 4.5.5 above.
4 . 6 MAINTENANCE
To avoid interruption of service, or contact with hazardous voltages in
the markers, it is recommended that the following rules be observed before
opening a marker cabinet:
(1) Check the status of the marker lamps at the administration center.
Marker Lamp Marker Status
White (lighted) Active (in service)
Red (lighted) Trouble (or made busy)
None Lighted Stand-by (matching)
(2) Upon opening a marker cabinet door, check that the green guard
lamp in the marker cabinet is lighted. The lighted lamp indicates that
the marker is inactive, and that the hazardous voltages have been
removed. Maintenance work can now be started.
(3) When the marker cabinet door is closed, the green guard lamp goes out.
(4) Depending upon the nature of the maintenance work to be done,
routine tests should be started at the administration center before
placing the marker in the stand-by condition.
Terminal Strips and Wiring
The terminal strips (at the front of the cabinets) are mounted in a vertical
column adjacent to the marker transfer relays (see Fig. 4-6). These terminal
strips are associated with the adjacent apparatus.
All input, output, and voltage leads of a unit are terminated on unit terminal
strips. One terminal strip on all units is used for the needed voltages and
146 Concentration and Distribution Markers Chap. 4
grounds. A group of punchings on the terminal strip is assigned to each voltage
and ground. This assignment is the same for all units. In the roof of the cabinet
are mounted the terminal strips used for all input and output leads that inter-
connect to other frames. Terminal strips are also used for the output leads to
the marker transfer. Terminal strips associated with the power interrupter circuit
relays (door interlock) are mounted at each end of the power relay mounting
plates located in the front lower section of the marker cabinet.
Chapter 5
The Scanner
A telephone switching system must know at all times what the state of each
line is. It is the job of the scanner to detect this state. The scanner enables the
central control to examine all lines and trunks that terminate in the central
office. It tells the central control when the line is "off-hook" and when it is
"on-hook." Besides lines and trunks, other points in the system have connec-
tions to the scanner. These are used for the system's self-checking program.
There are no "brains" built into the scanner. It works entirely under the
command of the central control. And, since its output consists only of "yes" or
"no" answers, these must be interpreted by the central control.
The scanning function requires no moving parts. Except for its transfer
features, the scanner is completely electronic.
5 . 1 EQUIPMENT ARRANGEMENTS
The scanner consists of two cabinets designated SC-O and SC-l*; see Figs.
5-1 and 5-2. These designations are marked near the bottom of the cabinets.
Each cabinet contains equipment mounted in two bays. One bay is fixed; the
other is movable to provide access to the inside of the scanner. The movable
bay is designated and the fixed bay is designated 1. These designations are
marked on the lower part of the frame and cabinet. The equipment consists of
apparatus assembled on mounting plates. Plate locations are designated by
numbers marked on the left edge of the bay frame (00 through 31 on Bay 0, and
00 through 32 on Bay 1). We refer to plates by the use of three-digit numbers,
in which the first digit indicates the bay, and the second and third digits identify
the plate. Thus 023 indicates plate 23 in Bay 0; 127 indicates plate 27 in Bay 1 ; etc.
The scanner equipment layout is shown in Fig. 5-3. The rear equipment (Bay
1) is identical in both cabinets, so only one view is shown. Functional designa-
tions are marked on the right side of the bay frame opposite the equipment.
Table 5-1 relates these equipment designations to the circuit designations.
*Since preparing the illustrations and text for Chapter 5, the designations for the cabinets
have been changed to S-0 and S-i.
147
148
The Scanner
Chap. 5
BULK RECTIFIERS AND
PARALLELING UNITS
TRACKING
REGULATORS
"\ ADDRESS TRANSFER
RELAYS
OUTPUT UNITS
(CIRCUIT "1")
OUTPUT UNITS
(CIRCUIT "0")
VOLTAGE REGULATOR
INPUT UNITS
(CIRCUIT "1")
VOLTAGE REGULATOR
INPUT UNITS
(CIRCUIT "0")
VG 501
FIG. 5-1. Scanner, front view.
Sec. 5.1
Equipment Arrangements
149
iHiimiiiMimii!iium<
aiiuiumimmiiiuMM.
•fwmumuuimiHHu
nitnmwiHiiiimtfiim a
iiniiuimuiiw mum , .
jnnnniimnuiiiiiiinit
MHIUHIHWiHHH IHIi;!^
flHimmmimiiniisH! -
MIIMIillllllllllilHIWII
mmiiiiuiiuiiiiHiiiiB:
ilfniiiHinuuiuHiiiiit;
innnnrrmiiiKiniiiiiii
■iBiiiHiiiuiniimiimm
" rFimmimimi*
u; k u::!„:;j:ji3jiiifHiiiH.i
ijiiMMifi': mm
■JWIE !■■
.•*•*■ Mnmny
\mvm\mmmmmamm
mwmvmm. BULK RECTIFIERS
OUTPUT AMPLIFIER
AND
TRANSFER UNIT
GATE MATRIX
VG 502
FIG. 5-2. Scanner, rear view.
150
The Scanner
Chap. 5
FRONT
RECT
-4.5 A
RECT
+ 15A
PAR
U
PAR
U
PAR
U
PAR
U
RECT
-4.5B
RECT
+ I5B
FUSE BLOCK
ADDRESS TRANSFER
OUTPUT
VOLTAGE REGULATOR
INPUT
VOLTAGE REGULATOR
INPUT
SC-0
RECT
+7.5A
RECT
+22.5A
PAR
U
PAR
U
RECT
+ 22.5B
RECT
+7.5B
FUSE BLOCK
+ 7.5 V TRACK. REG
ADDRESS TRANSFER
OUTPUT
OUTPUT
VOLTAGE REGULATOR
INPUT
VOLTAGE REGULATOR
INPUT
sc-t
REAR
RECTIFIER
-50
RECTIFIER
-50
TERMINAL STRIPS
FIG. 5-3. Scanner equipment.
OUTPUT AMPLIFIER
& TRANSFER
MATRIX
MATRIX
5 . 2 METHOD OF OPERATION
The scanner examines the state of all lines, trunks, and test points on a
one-at-a-time basis. Each line, trunk, or test point appears in the scanner as one
or two inputs to a transmission gate. These gates are usually referred to as "scan
points." They are biased in a forward direction by an "on-hook" condition of
the line. They are biased in the reverse direction by an "off-hook" condition of
the line. The scanner is directed by the central control, which says in effect,
"Look at such-and-such a scan point and let me know whether its line is in the
Sec. 5.2
Method of Operation
TABLE 5-1. EQUIPMENT DESIGNATIONS
151
Functional
Designations
Circuit Designations
A
D
D
T
R
Transfer Control Relays
Address Transfer Relays
N
Gate Input Transfer Relays
Input Translators
Input Selectors
Gate Amplifiers
Drivers
Pulsers
Cable Terminator
Load-Sharing Resistors
O
U
T
Lock-Up Amplifiers
Reset Amplifiers
Emitter-Follower Amplifiers
Output Translators
Output Selectors
Detectors
M
A
T
R
X
Gate Matrices (partial)
O
P
A
T
R
Part of Gate Matrices
Output Amplifiers
Gate Output Transfer Relays
on-hook or the off-hook state." The scanner examines the scan point as directed
and reports back to the central control a simple answer, "on-hook" or "off-hook."
Scanning— Fig. 5-4
This one-at-a-time sampling operation is carried on in two distinct types of
scan. One, called "supervisory scan," samples each scan point every 100 milli-
seconds. This is often enough to supervise those lines in which there are no
152
The Scanner
Chap. 5
SCAN- POINT
VOLTAGE
ON HOOK
A
OFF HOOK
A
DIAL 21
A
TALK
__A_
SAMPLING
PULSES
TIME
U 0.1 SEC J ->-) U-0.01 SEC
J I I I I I I I I I I I
Y
SUPERVISORY
SCAN
Y
DIRECTED SCAN
FOR DIAL PULSES
FIG. 5-4. Sequence of scanning modes.
SUPERVISORY
SCAN
rapid changes in state. The other scan, called "directed scan," is for lines having
rapid changes in state (dial pulsing). During this directed scan, the central
control directs the scanner to each dialing line every 10 milliseconds. It must
sample these lines ten times as often as during the supervisory scan, to be sure
that no changes in state representing dial pulses escape detection. With dialing
at the rate of 20 pulses per second, each dial pulse is about 50 milliseconds in
duration. You can easily see that a dial pulse could occur between scans at the
supervisory rate of one scan every 100 milliseconds.
The scanning cycle, which repeats every 100 milliseconds, is made up of
ten 10-millisecond periods (see Fig. 5-5). In each period, the central control
directs the scanning of all lines that are being dialed, and l/10th of all the scan
points in the system. The balance of the 10-millisecond period is taken up with
other functions of the central control external to the scanner.
We have said that the central control directs the scanner to look at these scan
points and report their state. How is this sampling accomplished? Essentially,
there are two things to be done: (1), a point must be selected; and (2), its state
must be detected. To do this, the central control sets up a route through the
point to be observed. It then sends out an interrogation pulse, called the
enable scanner pulse (ENS). This pulse follows the route laid out in the scanner.
If the line is on-hook, the pulse passes through the scan point and this will be
indicated to the central control. If the line is off-hook, the pulse is blocked;
this too is indicated to the central control.
Sec. 5.2
Method of Operation
153
*-
*
100 MILLISECONDS
, 10 MILLISECOND SEGMENT
-wmmm i i i i i
^'
i ^ 1
DIRECTED SCAN: -
ALL DIALING LINES
3.8 MS
MAX.
*CENTRAL CONTROL
PERFORMING
OTHER FUNCTIONS
■> CYCLIC SCAN:
1/10 OF ALL
SCANNER INPUTS
0.4 MS
APPROX.
FIG. 5-5. Scanning cycle.
The arrangement of the scan points is in the form of a grid or "matrix" (see
Fig. 5-6). Each scan point is connected between intersecting leads of the matrix.
There are 32 horizontal and 32 vertical elements in this matrix. These would
form 1024 points of intersection, or scan points, if completely equipped. But the
Morris equipment provides for only 904 scan points.
There are two such matrices in this scanner, together with their associated
input and output circuits. They have common input connections to the central
control, so they are always working in parallel. But they put out separate
answers, and the central control has the "sense" to pick the proper one. To
simplify the explanation of scanner operation, let us consider the working of
only one matrix. The other works in exactly the same way.
V)
XT
i i i i i i
X-00 X-01 X-02 X-25 X-26 X-27
TO
TRUNK, OR
TEST POINT
LINE,
.lis r\n J
'FIG. 5-6. Matrix of transmission gates.
154
The Scanner
Chap. 5
Matrix— Fig. 5-6
The matrix is the heart of the scanner. We have said that it consists of 32
vertical and 32 horizontal buses, with a transmission gate across each of the
working points of intersection. Each gate connects to a line, a trunk, or a test
point. The idle or busy condition of each of these parts of the system results in
a particular set of voltages at the input of its associated transmission gate in the
matrix. These sets of voltages bias the gates either in a forward direction (idle)
or in a reverse direction (busy). Forward biasing allows pulses to pass through
the gate. Reverse biasing blocks the pulses. This passing or blocking of the
pulse indicates to the central control the state of the line being scanned.
Now, how do we determine which one of the scan points will be interrogated
at any given instant? In Fig. 5-6, notice that each transmission gate combines
a particular horizontal bus with a particular vertical bus. So, when we inter-
rogate a horizontal bus together with a vertical bus, the gate, or scan point,
INPUT
SELECTOR
AM
RESET
AMPLIFIER
r^i
INPUT
TRANSLATOR
OUTPUT
TRANSLATOR
INTERROGATION
PULSE (ENS)
5 BIT Y-ADDRESS
5 BIT X -ADDRESS
Y
FROM CENTRAL CONTROL
FIG. 5-7. Scanner block diagram.
GATE MATRIX
- + - + +-+■
-+-+ -i V
OUTPUT AMPLIFIERS
LOCK-UP AMPLIFIERS
IELT
OUTPUT
SELECTOR
I
OUTPUT SIGNAL
V . . /
TO CENTRAL CONTROL
VO507
Sec. 5.2 Method of Operation 155
common to these two buses is placed in the active circuit. The part of the
scanner that steers the pulse to a particular horizontal bus is called the input
selector (see Fig. 5-7). The parts that set up the return path from the vertical
bus are the output selector and the detector.
Scan Point Selection— Fig. 5-7
The scan points are selected for interrogation by a coded signal from the
central control, called an "address." This address consists of d-c voltages on ten
pairs of leads. Each pair has a high-voltage lead (approximately 15 volts) and a
low-voltage lead (approximately 1 volt). These voltage pairs are referred to as
"bits." The ten bits of the scanner address are divided into two five-bit groups:
"X-address" and "Y-address." The Y-address is applied to an input translator.
This translator controls the input selector, which sets up a path to a horizontal
bus of the matrix. The X-address is applied to an output translator. This output
translator controls the output selector, which selects the output of the vertical
buses of the matrix. The arrangement of these units is shown in Fig. 5-7. Now,
let us see how these units operate to carry out the scanning function.
Input Selector— Fig. 5-8
The input selector sets up a path for the ENS pulse (enable scanner pulse) to
a particular horizontal bus in the matrix. It does this according to the pattern of
voltages received from the input translator. The input selector consists of a
two-stage transistor "tree" arranged as shown in Fig. 5-8. The first stage consists
of a group of eight transistors. It accepts pulses from the pulser. (The pulser
restores the shape and amplitude of the pulses sent by the central control.)
This stage performs a l-out-of-8 selection. Each transistor acts as a gate, which
is open when its base is at ground potential, and closed when a positive voltage
is applied to the base. The input translator provides eight voltages, seven of
which are high (+ lOv) and one of which is low (approximately ground). We
apply these voltages to the bases of the transistors. Thus seven of the transistors
are always cut off and one is conducting. Since the pulse is fed to all of the
transistors at once, we have now selected one out of eight paths— the one
through the conducting transistor.
The second stage of the transistor tree operates in a similar manner. It has a
group of four transistors for each of the eight transistors in the first stage. The
156
The Scanner
Chap. 5
STAGE Z
STAGE I
\\J7
TO
STAGE 2
TRANSISTOR
GROUPS
44>>i:
I I I
MULTIPLEO TO
SIX TRANSISTOR
GROUPS
i^i
Vi-O
7 LEADS HIGH
1 LEAD GROUND
I I I I
3 LEADS HIGH
I LEAD GROUND
FROM INPUT TRANSLATOR
FIG. 5-8. Input selector.
TO
GATE
>- MATRIX
VIA
DRIVERS
pulse from the first stage is fed to the paralleled inputs of one of these groups.
The base of each transistor is biased by another section of the input translator.
This provides four voltages, three high and one low. As before, we find that
there is one conducting path, while the rest are cut off. So we have selected one
path out of four, each of which represented a selection of one path out of eight.
Now we have made the required l-out-of-32 selection.
Input Translator— Fig. 5-9
The input translator converts the coded signals of the Y-address into the
proper voltage combinations to control the transistors of the input selector.
Sec. 5.2
Method of Operation
157
The input translator is essentially a type of matrix. It contains semi-conductor
diodes, which connect horizontal and vertical buses of this matrix in a particular
pattern. These diodes permit voltages appearing on the horizontal buses to be
transmitted to certain vertical buses.
The input translator operates in two sections: One controls stage 1 of the
input selector, and the other controls stage 2. The bits of the Y-address are
shown applied to the horizontal buses of the matrix. As we have said before,
each bit always has one lead at high voltage and one lead at low voltage. Three
bits of the Y-address are applied to the first-stage section. The arrangement of
diodes is such that one or more high-voltage address leads is coupled through
to each of seven vertical buses. Therefore, these seven verticals are at a high
potential. The remaining first-stage vertical is connected only to horizontal
buses having a low potential, so its potential is low. The second-stage section
TO INPUT SELECTOR
STAGE 1
A
J
ADDRESS
BIT
ADDRESS
BIT
ADDRESS
BIT
XXXX;
X
Y r.i
ADDRESS J
BIT *\
2 l- L -
xx;
x
X
xx:
x
H
n r~
J ,1 L.I
TO INPUT SELECTOR
STAGE 2
__A
xxxx.
xx;
x
x
x
\x.
x.
ADDRESS
BIT
x:
H
xx:
x
x
XX,
X.
FIG. 5-9. Input translator.
158
The Scanner
Chap. 5
works in the same way. Here we apply the two remaining bits of the Y-address
to the horizontals and get out one low and three high voltages from the verticals.
Changes in the Y-address take the form of reversals of potential between
leads of one or more address bits. These may occur in any random fashion, but
in no case can both leads of a pair be at the same potential at the same time.
The effect of these address changes, when applied to the input translator, is to
change the location of the low output in one or both sections of the unit. You
can see how this happens by observing (in Fig. 5-9), that, for any possible
arrangement of address bits, one— and only one— output vertical in each section
is connected only to low horizontals. All the rest are connected to at least one
high horizontal. But which one of the verticals will get the low potentials? This
is determined by the way in which the address bits are arranged at the time.
INTERROGATION
PULSE
(ENS)
_n__i
OUTPUT AMPLIFIERS
RESET PULSE
~LT
LOCK-UP AMPLIFIERS
CONDUCTING
NON-CONDUCTING
TO OUTPUT SELECTOR
FIG. 5-10. Operation of gate matrix.
Sec. 5.2 Method of Operation 159
Operation of Gate Matrix— Fig. 5-10
The ENS pulse, when fed to a Y-bus of the gate matrix, passes through all
of the active transmission gates connected to that bus. If all gates are active,
the pulse current is divided among the 32 X-buses. This could cause the current
on any one X-bus to be as small as 1 milliampere. Such small currents must be
amplified for effective use. We therefore provide a two-stage transistor amplifier
at the output of each vertical, or X, bus of the matrix. This amplifier also
discriminates against noise.
The amplified pulse is fed to one or more of the 32 lock-up amplifiers. This is
a standard gate amplifier, with external feedback added to provide bistable*
operation. It acts as a temporary memory by assuming a "set" state (+16v
output) when triggered by & positive pulse, and a "reset" state (+lv output)
when a negative pulse is applied to the input.
A pulse appearing on a Y-bus passes through the active transmission gates
to their associated X-buses. The pulses are then amplified and used to set their
respective lock-up amplifiers. A set amplifier, then, indicates an active scan
point between its X-bus and the Y-bus which was addressed with the interroga-
tion pulse. The lock-up amplifiers remain set until they receive a reset pulse.
In this way, they "remember" the condition of the addressed scan points until
told to "forget." The reset pulse is an inverted sample of the next ENS pulse.
It occurs after the scanning of the lock-up amplifiers, and is timed to reset the
amplifiers before the ENS pulse arrives. This is possible because the ENS pulse
is delayed in passing through the scanner.
Output Selector— Fig. 5-11
The output selector examines the state of the lock-up amplifiers one at a time
after each ENS pulse has been sent. On supervisory scan, it examines all lock-up
amplifiers between pulses. On directed scan, it examines only the amplifier
called for. It is controlled in this process by an output translator, which converts
the X-address into two groups of voltage levels.
The output selector is a two-stage device. The first stage provides an 8-to-l
reduction in the number of possible paths, and the second stage gives a 4-to-l
reduction. The output of each of the 32 lock-up amplifiers is fed to one of the
inputs to AND gates in the first stage of the output selector. (An AND gate
transmits signals only when all of its inputs are activated.) The other input of
*Having two distinct states of stability.
160
The Scanner
Chap. 5
FROM OUTPUT TRANSLATOR
A
7 LEADS GROUND
I LEAD HIGH
A.
FROM
LOCK-UP <
AMPLIFIERS
3 LEADS GROUND
LEAD HIGH
FIG. 5-11. Output selector.
Sec. 5.2 Method of Operation 161
these AND gates receives a group of eight signals from one section of the output
translator. These signals consist of eight voltages, one high and seven low. Each
of the eight signals is connected to a group of four AND gates. Only the group
receiving the high signal will pass information.
The output of these AND gates is connected to the second stage consisting
of four OR gates. (An OR gate transmits any signal that appears at its input.)
Since only one group of four AND gates is active at any given instant, only one
signal can appear at each OR gate. The l-out-of-4 selection of OR gates is done
by the signals from the second stage of the output translator. These consist of
a group of one high-level and three low-level signals. They are applied to the
output of the OR gates, the three low signals effectively grounding out the signals
at their gates. We now have only one signal left to give to the detector.
Detector
The detector and its associated amplifier have a simple function. This is to
convert the single-rail* output of the selector to an amplified twin-railt scanner
output. This is the required scanner output for use by the central control.
Output Translator— Fig. 5-12
The job of the output translator is a lot like that of the input translator. It
must take a five-bit twin-rail address and convert it to an eight-bit and a four-
bit single-rail address. However, its output potentials are inverted. To operate
the output selector we need a "one-high-and-seven-low" address for stage 1,
and a "one-high-and-three-low" address for stage 2.
To obtain this output, three bits of the X-address are connected to AND
gates. Note that each AND gate is connected to a different combination of ad-
dress input leads. This means that, for any combination of address potentials,
one and only one AND gate receives all three high voltages of the input address.
This gate puts out the high signal. The other seven gates will remain blocked,
their outputs being at about ground potential.
The other two X-address bits are connected to a group of four OR gates. To
understand this operation, remember that its purpose is to ground out three
of the four signals at the output of the selector. The way in which these gates
*A signal represented by the "voltage" or "no-voltage" state of a wire,
t A signal represented by a voltage appearance on one or the other of a pair of wires, the
opposite member of the pair being always in the "no-voltage" state.
162
The Scanner
Chap. 5
3 LEADS GROUND -1 LEAD HIGH
TO OUTPUT SELECTOR
5 BIT X ADDRESS
FROM
CENTRAL CONTROL
7 LEADS GROUND-] LEAD HIGH
TO OUTPUT SELECTOR
FIG. 5-12. Output translator.
are connected causes the flow of information to be opposite in direction to the
flow of current. The four signals from the output selector appear on the trans-
lator output leads. Two bits of the X-address appear at the output of the OR
gates. The low, or ground, part of each bit grounds out all signals passing
through the gate. Notice how these gates are connected to the output leads. You
will see that for any possible combination of address inputs, three of the four
output leads will be connected to gates having grounded outputs. Thus, we
achieve the desired address to be applied to the output selector: seven leads
ground and one high, and three leads ground and one high.
5 . 3 DUPLICATION AND TRAN5FER
To insure the continuous operation of the system, certain equipment and
apparatus are furnished in duplicate. Some power supplies are on a shared load
basis. Other duplicated units make up a stand-by circuit. When trouble occurs
in a duplicated unit in active service, the stand-by circuit is automatically
switched into the system. The circuit containing the faulty unit is switched to
stand-by. The fault can then be located and repaired without affecting service.
Sec. 5.3
Duplication and Transfer
163
The duplicated facilities are designated as "0" and "1". These are identified by
color coding. Zero circuits are identified by blue marking, and "1" circuits are
identified by yellow marking. The input, voltage regulator, and output units
have their functional designation markings color-coded. All other equipment
designations are marked in black. Some items of equipment contain duplicated
circuits. These are identified by blue or yellow dots, as shown in Figs. 5-13,
5-14, and 5-15.
UNIT DESIGNATION STAMPING
- BLACK CHARACTERS ^
PACKAGE TYPE
- NOT STAMPED
CIRCUIT IDENTIFICATION
- NOT STAMPED ~X
\
i
+
+
+
+
+
+
+
+
+
+
+
+
+
+
+
+
+
+
+
+
+
VR
1
At
+
VR
+
VR
r^r\r^r^^r^r^r^r^^r^r^/^r^r\r^r^r^r~\^r\rvsr^^r^ri\/^\fT\
A B i t-
AE
AF
TYPICAL SUPPORT BAR
BLUE DOT FOR "0" CIRCUIT^
YELLOW DOT FOR V CIRCUIT
w
1 1
1 1
i
BAY UPRIGHT
FIG. 5-13. Circuit identification marking (tracking voltage regulators).
UNIT DESIGNATION STAMPING
-BLACK CHARACTERS
RELAY FUNCTIONAL DESIGNATION
-BLACK CHARACTERS "V
++++++++++++++++
sc cc
_• • ••
1YO
OYO
txo
0X0
1
*
BLUE DOT AND YELLOW DOT_
FOR °/, RELAY CIRCUIT
\
\
I
I
I
I
I I
I I
y
FOR CIRCUIT IDENTIFICATION ONLY
-NOT STAMPED
,•' BAY UPRIGHT-
FIG. 5-14. Circuit identification marking (transfer units).
164
The Scanner
Chap. 5
PACKAGE TYPE
" NOT STAMPED
UNIT DESIGNATION STAMPING - s
BLACK CHARACTERS ^
"*
-*
OA
-
OA
OA
OA
OA
1
OA
1
OA
1
OA
1
+
+
OA
OA
OA
OA
OA
1
OA
t
OA
1
OA
1
+
+
OA
OA
OA
+
+
OA
1
OA
1
OA
1
OA
OA
OA
OA
OA
OA
OA
OA
DL
+
OA
OA
OA
OA
OA
OA
OA
OA
DL
+
OA
OA
OA
SG
SG
OR
OA
OA
,,>
-0
1
1
1
1
%
1
1
t
1
7,
7,
7
1
1
1
OA
OA
OA
OA
OA
OA
OA
OA
DL
DL
OA
OA
OA
OA
OA
OA
OA
OA
DL
DL
OA
OA
SG
SG
OA
OA
+
^>
-0
1
1
1
1
%
7,
1
1
1
1
°/l
7
%
7,
1
1
OGOO
IGOO
OGOI
1GOI
0G02
IG02-*
1
1
1
BLUE DOT FOR "0" CIRCUIT
YELLOW DOT FOR "l" CIRCUIT
NO DOT FOR n °/\" CIRCUIT
^^^VT>, ^/«\^^/WJN
TYPICAL
SUPPORT BAR
RELAY FUNCTIONAL DESIGNATION )
BLUE FOR "0" CIRCUIT - y
YELLOW FOR "T'CIRCUIT
BAY UPRIGHT
FIG. 5-15. Circuit identification marking (output amplifiers and transfer).
i i
i i
Duplication
All of the scanner circuits are duplicated except the gate matrix, the driver
dummy load, and the transfer relays. Since a fault in the gate matrix is not likely
to affect more than one line, this large portion of the scanner is not duplicated.
The driver dummy load is nothing more than a group of resistors which re-
place the matrix in the stand-by circuit. Each resistor bridges a horizontal ac-
cess lead to its corresponding vertical access lead. They match the impedance
of the drivers and allow pulses to be passed through the stand-by circuit during
routine tests. While the transfer relays, as such, are not duplicated, they have
dual-wound coils and twin contacts. This increases reliability.
Transfer— Fig. 5-16
The scanner stand-by circuit is normally switched into active service auto-
matically when the central control detects trouble in the active circuit. This
transfer may also be made by typing the proper order on the teletypewriter
in the administration center. In emergencies, the transfer can be made by oper-
ating keys at the administration center. In any case, the administration center
starts the transfer by operating the transfer control relays in the scanner. These
relays operate two other sets of relays, called "address transfer relays" and "gate
input and output transfer relays."
Sec. 5.3
Duplication and Transfer
165
Figure 5-16 shows the arrangement of transfers. The address transfer relays
and the gate input and output transfer relays have only "make" contacts. Half
of the contacts on the transfer control relays are normally closed. These put
the circuit of the scanner in active service when the transfer control relays are
in the released state. The other half of the contacts are normally open. When
the relays are operated we break the circuit contacts and close the 1 circuit
contacts. This makes the transfer through the various transfer relays.
Note that no switching of the scanner return leads to the central control is
shown. This transfer function is taken care of in the central control by a transfer-
sensing signal obtained from the gate output transfer.
t-<2 PAIRS)-
TRANSFERED IN
CENTRAL CONTROL
OUTPUT
CIRCUITS
"I"
OUTPUT
CIRCUITS
"0"
(32)
o/\o
X-ADDRESS
TRANSFER
5
PAIRS
GATE
OUTPUT
TRANSFER
Y-ADDRESS
TRANSFER
(6 PAIRS)
(« PAIRS) *-
FIG. 5-16. Scanner transfer.
CENTRAL
CONTROL
CENTRAL
CONTROL
1. NUMBERS IN PARENTHESES
INDICATE NUMBER OF LEADS
REPRESENTED BY A SINGLE
LINE.
2. CONTACTS DESIGNATED "0"
ARE CLOSED AND CONTACTS
DESIGNATED "I" ARE OPEN TO
PUT "0" CIRCUIT IN "ACTIVE"
POSITION THIS CONDITION
IS REVERSED TO PLACE THE
"1" CIRCUIT IN "ACTIVE"
POSITION .
3. ADDRESS AND GATE TRANS-
FER RELAYS ARE OPERATED
BY TRANSFER CONTROL RE-
LAYS , NOT SHOWN.
VG5I3
166
The Scanner
Chap. 5
230V(A)
230V (C)
-48 V
230V (A)
230V (C)
7.5 V
FROMSC-1
230V(A)
-48 V -■
230V (C)
{::
-4.5V
BULK
RECTIFIER
I -l/3 A
-4.5V
BULK
RECTIFIER
+ 15V
BULK
RECTIFIER
+ I5V
BULK
RECTIFIER
-50V
BULK
RECTIFIER
AND
PARA. CKT.
-50V
BULK
RECTIFIER
AND
PARA. CKT.
+
l/4 A
1-1/3 A
-cr\j>-
-4.5 V
PARALLELING
CIRCUITS
-4.5V (A) -s
+ 15V
PARALLELING
CIRCUITS
+ 15V(A)
TO
SCANNER
)>- CIRCUITS
SEE
TABLE 5-2
+ 4.5V
REGULATOR
(A)
+ 4.5V(A)
-50V(A)
JylULTIPLIED TO
FUSES A-BA
1/4A
+ 4.5V
REGULATOR
(B)
+ 4,5V(B)
FIG. 5-17. Scanner power equipment, SC-O.
5 . A POWER
The scanner gets its power through the power distribution cabinet. It
receives 230 volts alternating current from power buses A and C through 5-
ampere circuit breakers located in the power distribution cabinet. This power
is applied to bulk rectifiers located in both scanner cabinets. These supply the
various d-c voltages to the equipment.
This power system is arranged in duplicate. One complete set of rectifiers is
fed from bus A, and another complete set is fed from bus C, as shown in Fig.
1-18. The output from like units in each set is paralleled, either directly or by
Sec. 5.4
Power
167
connection to parallel loads. This means that failure of the power in either bus,
or failure of any rectifier unit, will not put the scanner out of service. In certain
cases, however, a circuit transfer may be necessary. The arrangement of power
equipment in the cabinets is shown in Figs. 5-1, 5-2, and 5-3.
In addition, — 48 volts direct current from the central office battery is supplied
through 5-ampere fuses located in the power distribution cabinet. This power
is used to operate the transfer relays in the scanner. It comes to the scanner on
d-c buses A and C, as shown in Fig. 1-19. The circuit is so arranged that failure
of either bus does not disable the scanner. Only its ability to transfer will be lost.
230V (A)
{:
TO SC-0 —
230V (C)
230V (A)
230V (C)
230V (A)
{::
{::
{::
{::
I-1/3A
230V (C)
{::
+ 7.5V
BULK
RECTIFIER
+ 7.5V
PARALLELING
CIRCUITS
+ 7.5V
BULK
RECTIFIER
+ 22.5V
BULK
RECTIFIER
+ 22.5V
BULK
RECTIFIER
-50V
BULK
RECTIFIER
AND
PARA. CKTS.
-50V
BULK
RECTIFIER
AND
PARA. CKTS.
1/2 A
1/4 A
1/2 A
1/2 A
1/4 A
+ 6V
TRACKING
REGULATOR
A
+ 6V (A) "N
+ 6V
TRACKING
REGULATOR
B
+ 6V(B)
+ 4.5V
REGULATOR
A
-t-4.5V(A)
+ 7.5V (A)
+ 6V
TRACKING
REGULATOR
C
+ 6V(C)
+ 6V
TRACKING
REGULATOR
D
+ 6V(D)
+ 4.5V
REGULATOR
B
+ 4.5V(B)
+ 7.5V(Al
+ 22.5V (A)
+ 22.5V (B)
MULTIPLED
TO FUSES
A-BA
1-1/3 A
-CTVD-
-50 V (A)
TO
SCANNER
V CIRCUITS
SEE
TABLE 5-2
FIG. 5-18. Scanner power equipment, SC-1.
168
The Scanner
Chap. 5
4E7" 1
•
output current
e
iflrS ■
AURM TEST
«
FIG. 5-19. Power supply, —50 volts.
Power equipment in the scanner consists primarily of the bulk rectifiers. They
contain solid-state rectifying devices, and regulating and filtering circuits. Other
units of power equipment are regulators and paralleling units. The general wir-
ing plan of this equipment is shown in Figs. 5-17 and 5-18. Table 5-2 lists the
power distribution by cabinet and circuit.
There are three types of bulk rectifiers used in the scanner. The — 50v rectifier
is shown in Fig. 5-19. It is fastened in its mounting bracket by quarter- turn
"Lion" fasteners, and connected to the circuits by plug-in connectors. It sup-
plies its rated voltage ± 2% at currents of up to 3 amperes with inputs of 226
to 233 volts, 57 to 62 cycles per second. It has a self-contained paralleling circuit
and alarm unit, which requires — 48v for operation.
The other types of bulk rectifier look exactly alike, except for marking. They
differ only in their operating voltage ranges. The rectifiers are adjusted to the
voltage required in each case. The voltage is marked on the designation strip.
Figure 5-20 shows two typical units, with their associated paralleling units
mounted between them. These are all plug-in units, secured to the rear plate
with quarter- turn Lion fasteners. They furnish their rated voltage at currents
of up to 3 amperes with inputs of 226 to 233 volts, 57 to 62 cps.
The paralleling units are used to isolate the outputs of two rectifiers operating
from separate a-c buses into a common load. Each paralleling unit consists
Sec. 5.4
Power
169
primarily of a silicon diode, which prevents trouble in either rectifier from short-
ing the load bus. A transistor monitors the diode drop and controls a relay and
associated lamps, which indicate circuit failures or maladjustments. Each unit
is for use at a particular voltage. They are mounted in the same manner as
their associated rectifiers.
The four voltage regulators (see Figs. 5-3, 5-17, and 5-18) each consist of two
circuit packages, one each of F-52657 and F-52658. They are located on plates
002 and 005 of each cabinet. They provide +4.5 volts ±1% at loads of up to
*/£ ampere.
The four tracking regulators each consist of an F-52656 package. All are
located on plate 024 of cabinet SC-1. They provide an output voltage which
TABLE
5-2. SCANNER POWER DISTRIBUTION
Power Lead
Designation
Connects to
Fig. No.
The Matrix
in Cabinet
Other Circuits
-50 (A)
SC-0
—
- 4.5(A)
SC-0
SC-1
SC-0, Circuits 0, 1
SC-1, Circuits 0, 1
Fig. 5-20
+ 4.5(A)
—
SC-0, Circuit
+ 4.5(B)
—
SC-0, Circuit 1
+ 15
SC-0
SC-1
SC-0, Circuits 0, 1
SC-1, Circuits 0, 1
—50 (A)
SC-1
—
+ 4.5(A)
—
SC-1, Circuit
+ 4.5(B)
—
SC-1, Circuit 1
+ 6 (A)
—
SC-0, Circuit
+ 6 (B)
—
SC-1, Circuit
Fig. 5-21
+ 6 (C)
+ 6 (D)
—
SC-0, Circuit 1
SC-1, Circuit 1
+ 7.5(A)
—
SC-0, Circuits 0, 1
SC-1, Circuits 0, 1
+22.5(A)
—
SC-0, Circuit
SC-1, Circuit
+22.5(B)
—
SC-0, Circuit 1
SC-1, Circuit 1
170
The Scanner
Chap. 5
4ft
• J, ^5>»
VG 517
FIG. 5-20. Power supplies and paralleling units.
tracks below the +7.5 volt input by 1.5 ±0.1 volts. The top rated load is 14
ampere.
There are 28 isolation networks, each consisting of an F-52631 package.
They provide filtering of the d-c power to those circuit packages that do not
have their own filters. They are located on plates 002, 005, 006, 007, 008, 010,
011, and 012 in both cabinets.
PLATE
014
r
YELLOW
CIRCUIT
BLUE
"I" ^'CIRCUIT'
o"\
'\
3
®
5
®
2
®
\
1
®
3
®
/
/ \
/ \
' I
i i
4 2
® ®
3
®
! \
® (
^
J
V
j 1
Y^
Y
1
CC
sc
I
1 _ JACKS NUMBERED "3" ARE GROUNDED,
2 _ ALL JACKS NOT OTHERWISE DESIGNATED ARE BLACK.
3 _ TO REMOVE "CC" RELAY : WHEN CIRCUIT "0" IS ACTIVE, PATCH JACK 3
TO JACK 5. WHEN CIRCUIT "1"IS ACTIVE, PATCH JACK 3 TO JACK 2.
4 _ TO REMOVE "SC" RELAY: WHEN CIRCUIT "0" IS ACTIVE, PATCH JACKS 3
TO JACK 4 AND JACK 5. WHEN CIRCUIT "1" IS ACTIVE , PATCH JACKS
3 TO JACK 1 AND JACK 2 .
FIG. 5-21. Relay contact patching.
VG 51
Sec. 5.5 Miscellaneous 171
5 . 5 MISCELLANEOUS
Cabinet SC-1 contains a relay designated RFA. This relay starts the
alarm circuits in the administration center whenever a fuse blows in the 7.5-volt
circuit feeding the regulators. It also causes the administration center to start
action to transfer the scanner to its stand-by circuit.
Each scanner cabinet contains three test blocks. All three blocks have a — 48v
test terminal, a ground terminal, and a high-resistance (12,000 ohms) ground
terminal. Two blocks have trouble indicator lamps and a — 48v test jack. The
trouble lamps show which of the scanner circuits is in trouble. The third block
has a +22.5v test terminal.
Each cabinet has four feed-through terminal strips, designated A, B, C, and
D. Power leads are connected to strip A; address leads to strip B; ENS, transfer
control, and administration center leads to strip C; and matrix diagonal test
point leads connect to strip D.
The scanner cabinets contain the alarm relays, alarm indicator lights, and
power receptacles common to all ESS cabinets. Also, one cabinet has a set of
jacks mounted near the alarm lamp. These are connected to similar jacks
throughout the system for intercommunication.
5 . 6 MAINTENANCE
Maintenance on equipment while in service is seldom needed because
of the extensive duplication of scanner circuits. The routine test program of
the system detects circuit failures and automatically switches the scanner stand-
by circuit into service. Indicator lamps, mounted on the test blocks at the front
and rear of each cabinet, show which of the duplicated circuits is in trouble. At
the same time, the teletypewriter in the administration center prints out a coded
message indicating the source of the trouble. This trouble report usually points
out the location of the fault within two or three units. Replacing these units
should correct the trouble.
The modular design used in the ESS permits us to perform primary mainte-
nance by replacing plug-in units. These may consist of circuit packages, fuses,
certain relays, or power supply units.
Circuit packages are described in Chapter 1 and shown in Fig. 1-9. Those
used in the scanner are all of the narrow, or "a," type. Table 5-3 lists these
packages.
172
The Scanner Chap. 5
TABLE 5-3. PACKAGES USED IN THE SCANNER
F-Spec.
Number
CPS*
No.
Quantity
Name
F-52603
48
168
Gate Amplifier
F-52605
50
20
Emitter-Follower Amplifier
F-52615
1
32
AND Gate 2-2-2-2 Input
F-52617
3
12
AND Gate 3-3-3 Input
F-52621
17
8
OR Gate (No Resistor) 2-2-2-2 Input
F-52622
18
16
OR Gate (No Resistor) 10 Input
F-52625
21
16
OR Gate (2610 Ohm Resistor) 10 Input
F-52631
155
28
Isolation Network
F-52635
56
64
Driver Amplifier
F-52637
83
40
Input Selector Transistors
F-52638
55
4
Pulser Amplifier
F-52639
57
4
Reset Amplifier
F-52640
58
128
Output Amplifier
F-52641
31
680
Line Gate
F-52642
84
8
Input Translator, Stage 1
F-52643
85
4
Input Translator, Stage 2
F-52646
145
4
Input Selector Resistors
F.52648
32
224
Special Gate
F-52649
183
4
Cable Terminator
F-52651
184
4
Detector
F-52652
68
4
Detector Amplifier
F-52653
149
12
Driver Dummy Load, Resistors
F-52655
186
8
Load-Sharing Resistors
F-52656
195
4
Tracking Voltage Regulator, +6.5v
F-52657
190
4
Voltage Regulator, +5 to +8 volts, Board A
F-52658
190
4
Voltage Regulator, +5 to +8 volts, Board B
*CPS means Circuit Package Schematic.
The thirty-two F-52725 wire-spring relays are not easily replaced. But they
have dual-wound coils, one winding being a spare. If a winding fails, we can
restore the relay to service by moving the connecting wires from terminal 1U
to terminal 2U. This places the spare winding in the active circuit.
The 276F and the four 275A mercury contact relays are of the plug-in type.
In replacing the 275A relays you must take special care. You may disable the
system by pulling out a relay, unless you first patch across the proper relay
contacts to maintain control of the circuit. Special pin jacks and patch cords
have been provided for this purpose. Jacks are mounted on the same plate as
Sec. 5.6 Maintenance 173
their associated relays. Note which of the scanner circuits is active and make
the proper connections, as per Fig. 5-21, to keep the circuit active. Then remove
the relay. Be sure to remove all jumpers after replacing the relay.
Failure of any power supplies or fuses is indicated by an alarm at the admin-
istration center. Alarm lamps are also provided on the — 50v bulk rectifiers and
the paralleling units. Replacement of this plug-in equipment is not difficult.
This is covered in the circuit descriptions of the various equipment items.
CAUTION The — 50v bulk rectifiers weigh 74 pounds each. When you remove any of them,
be sure to have enough help to prevent dropping the unit on the unprotected
equipment below.
Chapter 6
The Stand-By Transfer
6 . 1 GENERAL
To assure reliable service, some units in the ESS are duplicated completely;
others are partially duplicated. This allows the system to compare outputs from
duplicated units. Matching circuits and trouble-detecting programs tell the
system which unit is faulty. If the faulty unit is the active* unit, it is switched
out of service and its duplicate is put into service.
A Stand-by Transfer (ST) is used in the ESS to set up transfer paths between
the Central Control (CC) and other system units directed by CC. These paths
are shown in Fig. 6-1. The stand-by transfer uses relays and semi-conductor
devices to set up the transfer paths as required.
Besides the transfer function, ST carries out other functions that are really
part of central control operations. The circuits that perform these other func-
tions are:
(a) the central control matching circuit;
(b) the marginal voltage test circuit;
(c) the flying spot store (FSS) control circuit; and
(d) the master clock pulse generator circuit.
These circuits are located in ST because of electrical and equipment design
requirements.
Central Control Matching Circuits
In the Morris ESS, the central control is duplicated. At any given time, one
CC is active and the other is in stand-by condition. The central control match-
ing circuits match the following outputs from both central controls:
♦"Active" means providing customer service.
174
Sec. 6 . 1 General 175
(a) bus;
(b) parity check* and error correction;
(c) barrier grid store (BGS) orders; and
(d) flying spot store (FSS) orders.
If a mismatch is detected, the system quickly determines which CC is at fault.
If it is the active CC, it is switched out of service and the stand-byt CC is made
active. The system then continues with its business, and the CC taken out of
service can be worked on.
Marginal Voltage Test Circuits
The Morris ESS uses marginal voltage test circuits to test flip-flops and gate
amplifiers in CC and ST circuits. These marginal voltage tests are made to de-
tect possible sources of trouble. The tests are applied automatically once a day,
or at any time on the request of the maintenance craftsman.
Flip-flops are tested in groups of one to twenty-six. The +22v is lowered in
four steps to + 17v. The flip-flops are checked at each step; the time allowed for
each step is 1.5 seconds.
The gate amplifiers are checked in groups of one to ten. The — 4.5v is low-
ered in four steps to — 2.5v, and increased in four steps from -4.5v to — 6.5v.
Each step in this test takes 1.5 seconds.
Flying Spot Store Control Circuits
On the basis of information supplied by the two central controls, the FSS
control circuits determine which order lead is made active to the FSS's. There
are six order lead outputs from these circuits. The lead selected gives the next
order to the FSS's. The leads and orders are designated advance, transfer, rest,
scan, operate, and expose. The orders for the FSS's are explained in Chapter 9.
Master Clock Pulse Generators
The master clock pulse generators supply a 0.3-microsecond pulse at a rate
of 400 kilocycles per second. This pulse is fed to gating circuits, and amplified
for use in the central controls and stand-by transfer. There are two of these
pulse generators, one for each CC. The active CC determines which pulse gener-
ator supplies the controlling clock pulse. The pulse generators are connected so
that the one used with the active CC synchronizes the other.
*A check to determine whether the number of l's is odd or even.
fNot providing customer services, but ready to do so.
176
The Stand-By Transfer
Chap. 6
DUPLICATED EQUIPMENT
FIG. 6-1. ESS transfer paths.
ADMINISTRATION CENTER
BARRIER GRID STORE
CONCENTRATION MARKER
DISTRIBUTION MARKER
FLYING SPOT STORE
SIGNAL DISTRIBUTOR
RINGING AND TONE SUPPLY
VG601
6.2 EQUIPMENT ARRANGEMENTS
Two cabinets contain all the equipment needed for the stand-by transfer.
Each cabinet is divided into two bays, front (gate) and rear (fixed). The front
bay of each cabinet can be swung open to provide access to the wiring on the
front and rear bays. Both cabinets are stamped ST-o. The bays are stamped 0,
1, 2, and 3, near the base of each cabinet. The unit abbreviations are stenciled
on the right side of the bay frame.
Front Equipment— Bay 0, Fig. 6-2, Fig. 6-3
Twelve rectifiers and two paralleling units occupy the top third of bay 0.
This power equipment is arranged for plug-in unit replacement. To replace any
of the fourteen units, you simply loosen the fasteners on the wiring side of
the unit, disconnect the a-c cord, and unplug the unit from the front. Guide
pins aid you in replacing a power unit.
About one-half of the front bay is unequipped; other units may be added later.
Rear Equipment— Bay 1, Fig. 6-4, Fig. 6-5
At the top of the rear bay are four coaxial cable connectors. Coaxial cable
is used to send the high-speed clock pulse throughout the system. Below the
Sec. 6 . 2 Equipment Arrangements Yll
connectors are two rows of terminal strips. The upper row is used to connect
this ST cabinet to both central controls. The lower row of terminal strips is
marked MISC. These terminals are used to make connections with various other
system units.
On the left side of the rear bay are mounted two fuse blocks and one test block.
Front Equipment— Bay 2, Fig. 6-2, Fig. 6-3
At the top of bay 2 are mounted the rest of the rectifiers needed for the ST.
These rectifiers are of the same type as in bay (described above), and are
replaced in the same way.
Rear Equipment— Bay 3, Fig. 6-4, Fig. 6-5
At the top of this bay are mounted eight coaxial cable connectors. These
connectors are used as part of the clock pulse distribution system.
Below the sockets are two rows of terminal strips. Their use is the same as
for the two similar rows in bay 1 .
In addition, in the rear bay are mounted two fuse blocks and one test block.
Packages and Relays
The ST requires 142 relays for its transfer functions. It has about 879 pack-
ages for its electronic circuits. A breakdown of the circuit packages (CPS) and
the quantity of each is shown in Table 6-1. The location and designation of
packages in the ST are shown on a chart mounted on the door of each cabinet.
Note: Figures 6-2 through 6-5 are shown on pages
178 through 181. Table 6-1 appears on page 182,
and the text of Chapter 6 is resumed on page 182.
178
The Stand-By Transfer
Chap. 6
FIG. 6-2. Stand-by transfer, front view.
Sec. 6 . 2
Equipment Arrangements
179
BGS
TR
BAY
RECT
+22A
RECT
+22B
RECT
+22C
RECT
-16A
RECT
-16B
RECT
-I6C
RECT
+8A
RECT
+ 8B
RECT
+ 8C
RECT
+ I6A
RECT
+ 16B
RECT
+ 8D
PAR
-16A
PAR
-16B
VOLTAGE REGS & MISC
ISO KEYS & MISC CKT
o BGS TRANSFER RELAY
-*K
OU-
ST 0,
UNIT ABBREVIATIONS
ARE STENCILED
ON BAY FRAME
REMOTE
CONCENTRATOR -<
CONTROL
(NOT USED
AT MORRIS)
TRANSFER GATE
— CONT AND TONE
SUPPLY TRANSFER
BAY
DESIGNATION
APPLIANCE OUTLETS
-UNIT DESIGNATION-
BAY 2
RECT
+ 26A
RECT
+26B
RECT
+22F
NEON
BIAS
SUPPLY
RECT
+ 8E
REMOTE TRUNK
CONCENTRATOR CONTROL
VOLTAGE REGS 8. MISC
ISO KEYS 8. TEST POST
MARGINAL TEST RES
MARGINAL VOLTAGE
TESTER
REMOTE CONC TRANSFER
MANUAL CONTROL
SEQUENCE CONTROL
AND
CONTROL SELECTOR
REMOTE
NETWORK
CONTROL
REMOTE LINE
CONCENTRATOR CONTROL
LINE NUMBER MATCH
AND COUNTER
SYNCHRONISM CHECK
-9 9
ST
FIG. 6-3. Stand-by transfer, front equipment, Bay and Bay 2.
RTCC
VR
SEQ
CC
SEL
REM
NET
CONT
RLCC
0-1
LNM
C
sc
180
The Stand-By Transfer
Chap. 6
FIG. 6-4. Stand-by transfer, rear view
Sec. 6 . 2
Equipment Arrangements
181
BAY 3
CLK
GEN
PCK
MCH
FSS
O
MCH
BGS
MCH
TS
MEW
RM
RTC
TERMINAL STRIPS
TERMINAL STRIPS
MARG TEST RESISTORS
CLOCK PULSE
GENERATORS
BUS MATCH, PARITY
CHECK AND ERROR
CORRECTION MATCH
FLYING SPOT STORE
ORDER MATCH
AND CONTROL
BARRIER GRID STORE
ORDER MATCH
TONE SUPPLY MEMORY
REMOTE CONCENTRATOR
FF.OPE MEMORY & ACBI
START RECORDING MATCH
& REC TRANS CONTROL
V
BAY I
-FUSE HOLDERS--.
UNIT ABBREVIATIONS
ARE STENCILED
ON BAY FRAME
TEST BLOCKS-
MOUNTING
PLATE —
LOCATION
BAY
DESIGNATION
APPLIANCE OUTLETS
UNIT DESIGNATION
TERMINAL STRIPS
TERMINAL STRIPS
TRANSFER RELAY
DISTRIBUTOR TRANSFER
DISTRIBUTION MARKER
AND CONCENTRATION
MARKER TRANSFER
LAMP PANEL
BARRIER GRID STORE
ORDER TRANSFER, ORDER
GATE AND REPETITIVE
PULSE CONTROL
BARRIER GRID STORE
ADDRESS TRANSFER
BARRIER GRID STORE
SERVO TRANSFER
►9 9
ST
MKR
T
DG
RP
BGS
ADD
FIG. 6-5. Stand-by transfer, rear equipment, Bay 3 and Bay 1.
182 The Stand-By Transfer Chap. 6
TABLE 6-1. PACKAGES USED IN THE STAND-BY TRANSFER
F-Spec.
Number
CPS*
No.
Quantity
Name
F-52600
36
52
Flip-Flop
F-52601
46
39
Flip-Flop to Gate Amplifier
F-52603
48
18
Gate Amplifier
F-52604
49
18
Inverter Amplifier
F-52605
50
5
Emitter Follower
F-52615
1
74
AND Gate
F-52616
2
36
AND Gate
F-52617
3
44
AND Gate
F-52618
4
22
AND Gate
F-52619
5
20
AND Gate
F-52620
16
19
OR Gate
F-52621
17
46
OR Gate
F-52623
19
80
OR Gate with Resistor
F-52624
20
6
OR Gate with Resistor
F-52625
21
2
OR Gate with Resistor
F-52626
22
8
OR Gate with Resistor
F-52627
23
14
OR Gate with Resistor
F-52628
24
13
OR Gate with Resistor
F-52629
25
4
OR Gate with Resistor
F-52630
26
12
OR Gate with Resistor
F-52631
51
44
Isolation Network
F-52633
51
164
Cable Pulse Amplifier
F-52634
156
92
Cable Matching Network
F-52656
195
3
Tracking Voltage Regulator
F-52659
189A
l\
F-52660
189B
Voltage Regulator
F-52672
41
10
Clock Coupling Network A
F-52673
42
10
Clock Coupling Network B
F-52674
43
8
Clock Pedestal Network
F-52675
198
10
Voltage Divider
*CPS means Circuit Package Schematic.
6 . 3 POWER
The stand-by transfer uses two office power supplies, 230 volts of alter-
nating current and —48 volts of direct current. The 230-volt current is fed on
three buses, A, B, and C. The — 48-volt direct current is fed on two buses, A
and B. The office power is connected in ST in such a way that the ST circuits
Sec. 6 . 3 Power 183
associated with other units in the system are fed from the same bus that feeds
these other units.
The bulk rectifiers used in ST are marked: +22A, +22B, +22C, — 16A,
-16B, -16C, +8A, + 8B, +8C, +8D, +26A, +26B, + 16A, and +16B.
Two paralleling units are needed to insure voltage for some important trans-
fer relays. These paralleling units are associated with the — 16A and — 16B
rectifiers. If either the 230v A bus or the 230v B bus fails, the good bus supplies
its rectifier; the paralleling units shift the load to that rectifier. This keeps the
load supplied at all times.
6 . 4 MAINTENANCE
The stand-by transfer is not a duplicated unit. When you are maintain-
ing it, you are working in an active system unit.
CAUTION Don't do any maintenance in the stand-by transfer cabinets until you are positive
which circuits are active and which are stand-by.
There are two indicating lamps in each cabinet, one blue for the "0" func-
tional circuits, and the other yellow for the "1" functional circuits. The lighted
lamp tells which circuits can be worked on.
When directed to the match circuits in the ST, you may pull packages even in
the circuits where the indicating lamp is off. This is feasible, because the system
disregards the match circuits at this time. When maintenance is completed, the
maintenance craftsman must tell the system, via a teletypewriter message, that
the unit is again ready for service.
Several equipment features for locating troubles quickly are included in the
ST cabinets. For example, four panels of isolation keys (see Figs. 6-2 and 6-4),
are included to isolate bulk rectifier troubles in both cabinets. You are directed
to a faulty rectifier by a fuse alarm. This alarm also gives line-up lamp* and cab-
inet lamp indications. Also, a teletypewriter print-out of a voltage monitor test
specifies the location of the rectifier. The isolation key or keys associated with
a rectifier have the same designation as the rectifier followed by a 1, 2, or 3
(e.g., +22A1, +22A2). When you see which rectifier circuit breaker is tripped
(OFF), turn OFF the isolation key or keys associated with it. This disconnects
*A lamp at the end of an aisle, formerly called an aisle lamp.
184 The Stand-By Transfer Chap. 6
the load. Then reset (turn on) the rectifier circuit breaker. If it trips again, the
rectifier is faulty.
If the rectifier circuit breaker did not trip with the load removed, make sure
that the main breaker in the power distribution cabinet (PD) is reset. If it is
reset (ON), turn the first isolation key ON. If this trips the rectifier circuit
breaker, the trouble is in the load connected through that key. To determine
which mounting plate load causes the overload, turn the isolation keys ON and
OFF (one at a time) and remove the isolation networks associated with each
key, one at a time.
Another feature for locating trouble quickly is a lamp panel, shown on Fig.
6-4, Bay 1 . The lamps on the panel are associated with double-wound mercury
relays. There are two lamps for each relay, one for each winding. Each lamp has
the same designation as its relay, followed by a 1 or 2. Each lamp is in series
with a relay winding and across a current-limiting resistor. Therefore, with the
relay operated, both lamps should be ON; with the relay released both lamps
should be OFF. One lamp ON and one OFF indicates a trouble, either in a
lamp or in a relay winding.
CAUTION This kind of trouble is not detected by the system. Therefore, before you do any
maintenance, make busy, via the teletypewriter, the unit associated with the relay.
Now check the lamp. If the lamp is bad, replace it. If the lamp is good, re-
place the relay.
CAUTION Don't remove any mercury contact relays until the state (operated or released)
of the relay has been determined.
When the state of the relay is known, strap the proper contacts to keep them
made. Jacks for strapping the relay contacts should be used to keep the con-
tacts closed. Now replace the relay with another relay of the same code, and
remove the strap. Tell the system, via a teletypewriter message, that you have
finished.
CAUTION Handle mercury contact relays gently to prevent contact bridging.
Double-wound relay troubles are found by looking into the cabinet. They
should be cleared during slack periods. When removing mercury contact re-
lays, you may use the 603A tool.
Single-wound relays with open windings or open contacts are detected by
the system as open paths between units. You are directed to these troubles by a
teletypewriter print-out.
Chapter 7
The Signal Distributor
Not all parts of the ESS work at the same speed. And not all use the same
power. For instance, the central control works at microsecond speeds from
low milliwatt power signals. Relays in trunk circuits work at millisecond speeds
and from higher power levels. To make these different units work together a
Signal Distributor (SD) is included in the system. The SD converts and distrib-
utes the very fast signals from the central control to other units of the system.
It converts high-speed (microsecond) low-power signals received from the cen-
tral control to low-speed (millisecond), higher-power signals needed to direct
certain operations in the system. It distributes these signals to the other units
shown in Table 7-1.
The signal distributor consists of a selector and a large group of flip-flops,
with their associated amplifiers; see Fig. 7-1, a functional diagram of the signal
distributor. The selector translates the input information to a particular output.
Each flip-flop acts as a memory element and accepts two high-speed inputs from
the selector. These inputs indicate the beginning and end of an output signal.
The amplifiers provide the power needed to operate relays.
7 . 1 EQUIPMENT ARRANGEMENTS
Front and Rear Views— Figs. 7-2 and 7-3
The SD is a self-contained unit. All the electronic circuit packages, power sup-
plies, and relays are mounted in one enclosed cabinet. The cabinet is divided
into two bays, a front (gate) bay and a rear (fixed) bay. The front bay can be
swung open to provide easy access to the wiring on both the front and rear of
the cabinet.
Front Bay— Fig. 7-2
The upper half of the front bay is occupied by power rectifiers and paralleling
units. This power equipment is of the plug-in type. Any of the eighteen rectifiers
185
186
The Signal Distributor
Chap. 7
INPUT
FROM
CENTRAL "S
CONTROL
.
1024
SELECTOR
OUTPUTS
512
FLIP-
FLOPS
512
AMPLIFIERS
S
10 y^
PAIRS
SELECTOR
DRIVE
R
S
R
S
Ik.
y OUTPUT
' SIGNALS
>--
ENABLE |
R
\y
FIG. 7-1 . Signal distributor, functional diagram.
TABLE 7-1. OPERATIONS DIRECTED BY
SIGNAL DISTRIBUTOR OUTPUTS
Circuit
Operations
Trunk
Signaling
Dial Pulsing
Supervising
Controlling PBX Functions
Controlling Customer Group Services
Administration Center
Switching Major System Components
Applying Marginal Voltage Conditions
Operating Alarms
Aiding Voltage Monitor Circuit
Operating Teletypewriter Equipment
Central Control
Resetting Timers
Stand-By Transfer
Controlling the Photographic Store
Plate Exposure
Scanner
Comparing Trouble-Checking Circuitry
in Scanner and Signal Distributor
VG701
Sec. 7 . 1
Equipment Arrangements
187
BULK BULK
RECTIFIER RECTIFIER
ALARM
POWER
FOR < THRU
PLATES 119
100
THRU
109
DUPLICATED
RECTIFIERS ■{
FOR S DR A 4 B
RESET RELAY —
110
S DR A
(BLUE marking)
S DR B
(yellow marking)
TRUNK
GROUPS
FFA-
FFB — i
REL TST
TRANSFER.
RELAYS
^0
PLATE NUMBER-rH
BAY
designation -
appliance _
OUTLETS
COMPONENT
DESIGNATION
-16G
+ 16 E
-16 E
+ 16C
-16C
-16A
-16B
16G
16E
16E
+
16C
16C
I6H
I6F
16E
16D
I6D
+22A
+22B
-16H
+ 16 F
-16F
+ 16D
-16D
+ 16A
+ 16B
-HI
SELECTOR DRIVE
A
— SELECTOR DRIVE
B
— FF GROUP 30A, 3IA
— FF GROUP 30B, 3IB
TEST FIELD A, B
3 B|v.[v 8 [v.jVA| T |«B|H iB |„ S |« / |a.j r |,C
DUMMY LOADS
SD
J J
... *
' m*
'o#
t*«| MS
m
a 9
i : :
j 3 »
1 ," .'
m*
J mi
' «•
Q #
mm
. .! ■
■I
I >
i \ *
r ■
j MM
. MM
. .1
m
1 *»
. J ■
. m,
*»
fRflHE
HHMI
FIG. 7-2. Signal distributor, front view and front equipment.
188
The Signal Distributor
Chap. 7
CABLE
TERMINAL
STRIPS
FUSE
BLOCKS
TEST
BLOCK
APPLIANCE
OUTLETS
— FF GROUPS 28,29-
■n n n
AND GATE GROUP
FF
MATRIX
GROUPS 00-29
■FF GROUPS 00,0)
"99
SD
mmmwmmmrl
9ifi« wmmrnsm ,
' II
f
FIG. 7-3. Signal 'distributor, rear view and rear equipment.
Sec. 7.1
Equipment Arrangements
189
or twelve paralleling units can be replaced by loosening the fasteners on the
wiring side of the unit, disconnecting the a-c cord, and unplugging the unit
from the front. The lower half of this bay is made up of the various duplicated
units in the signal distributor.
Rear Bay— Fig. 7-3
The rear bay consists of the equipment shown in Fig. 7-3. On the upper left
side of the cabinet is mounted a fuse block housing six fuses. Directly below
the fuses is a test block for testing office battery voltages.
Packages
The electronic circuits of the SD use sixteen different types of packages. The
total number and types of packages are shown in Table 7-2. The location and
designation of the various packages are shown on a chart mounted on the doors
of the cabinet.
TABLE 7-2. PACKAGES USED IN THE SIGNAL DISTRIBUTOR
F-Spec.
CPS*
Number
No.
Quantity
Name
F-52600
36
546
Transistor Flip-Flop
F-52601
46
4
Flip-Flop to Gate Amplifier
F-52602
47
271
Flip-Flop to Relay Amplifier
F-52606
137
2
Delay Network
F-52607
6
33
Special AND Gate
F-52608
53
22
Translator Driver Amplifier
F-52609
54
64
Driver Amplifier (Signal Distributor)
F-52611
86
32
Translator Diode Matrix
F-52612
152
2
Bias Circuit
F-52613
150
22
H Dummy Load
F-52614
151
6
V Dummy Load
F-52620
16
16
Six-Input OR Gate
F-52622
18
102
Ten-Input OR Gate
F-52631
155
21
Isolation Network
F-52634
156
2
Cable Matching Network
F-52694
129
4
T Dummy Load
*CPS means Circuit Package Schematic.
190
The Signal Distributor
Chap. 7
SELECTOR DRIVE A OR B
r
FROM
CENTRAL
CONTROL y
VIA
STAND-BY
TRANSFER
TRANSLATOR
DRIVERS
5
PAIRS
5
PAIRS
V_ I — _< ~_
10 PKGS
20 AMPL.
,V
DRIVING
TRANS-
LATOR
CLAMPING
TRANS-
LATOR
DRIVE
CIRCUIT
32 PKGS
32 AMPL
DA
ENABLE
AND
DELAY
CIRCUIT
14 PKGS
ENABLE
H31
r-
HO
V0_
FIG. 7-4. Signal distributer, block diagram.
MATRIX
FF GROUPS 00-31
920 PACKAGES
HQf ' I
:t^ff GROUP[_
i££ 31
COMMON
*« — TO ALL H
GROUPS
M
FF GROUP
00
7.2 METHOD OF OPERATION
7.2.1 General Description of Operation
Because the scanner, administration center, central control, stand-by
transfer, and trunk circuits need d-c signals to help do their job, they are as-
signed to specific outputs of the SD; see Table 7-1. Each output is used to direct
only its assigned circuit. For example, one output controls the operation and
release of the supervisory relay in a particular outgoing trunk circuit. When the
central control wants to seize that trunk, it sends a ten-digit binary address to
the SD. The SD translates this to a specific location in the output matrix.
The address is received on ten pairs of input leads. Each pair has one lead
high (+16v) and one lead low (ground). The lead that is high we'll call +,
Sec. 7 . 2 Method of Operation 191
and the low lead, — . Thus, there are two states for the first pair of leads (H — ,
— h), and every additional pair doubles the number of states. Thus 1 pair =
2 states (2 1 ), 2 pairs =4 states (2 2 ), 3 pairs =8 states (2 3 ), and so on to 10
pairs or 1024 (2 10 ) possible states of input leads. Since relays must be operated
and released, each output needs two states. Thus from 1024 inputs we get 512
outputs, which can be used to operate or release a relay.
To simplify the understanding of the operation of the SD this description is
divided into six functional parts, as indicated on Fig. 7-4. The following para-
graphs describe each of these six parts and how they work together to perform
the functions of the SD.
7.2.2 Selector Drive A or B
Translator Drivers
Twenty Translator-Driver Amplifiers (TDA) make up this part of the SD.
There are two amplifiers on one package, so ten packages are needed. These
amplifiers accept the address from the central control, via the stand-by transfer.
Each amplifier applies either +16v or ground to the inputs of each translator.
Driving and Clamping Translators
There are two identical diode translators, driving and clamping, in the SD.
Each translator has eight 20-diode packages (160 diodes). The eight packages
for each translator are connected to form 32 five-input AND gates. The proper
arrangement of voltage and ground on the input leads makes one AND gate
output lead active. We now have one active output lead from each translator.
Drive Circuit
The drive circuit consists of 32 Driver Amplifiers (DA) one for each driving-
translator output lead. The active output lead from the driving-translator turns
on one driver amplifier. This amplifier output places 22v on one input lead of
one flip-flop in each of the 32 flip-fop groups of the output matrix. Now 32
flip-flops are prepared for a selection. Only one driver amplifier is active at a
time, because only one translator (driving) output lead is active at a time.
Enable and Delay Circuit
The enable circuit is a diode package group consisting of 32 diodes. The
diodes, one for each clamping translator output lead, clamp all the outputs to
192 The Signal Distributor Chap. 7
ground. This keeps the translator inactive, while the inputs to the SD are being
changed. It prevents the SD from translating these changing inputs into false
outputs of its own. To unclamp the enable-circuit diodes, the distributor re-
ceives a 0.3-microsecond pulse along with the address. It is called the "enable
pulse" because it unclamps the diodes of the enable circuit. The pulse is re-
ceived by the delay circuit. In the delay circuit this pulse is delayed 5.5 micro-
seconds and then passed as a 2-microsecond pulse. During the delay the trans-
lator is inactive. In the 2-microsecond period it is undamped or active. The sum
of these times, 7.5 microseconds, is the maximum speed at which the signal
distributor can operate.
7.2.3 Matrix (Flip-Flop Groups 00 through 31)
There are 32 vertical groups of flip-flops in the SD. Each group is
composed of fifteen flip-flops, fifteen flip-flop-to-relay amplifiers, one AND
gate and three OR gate packages. The matrix shown in Fig. 7-5 is a detailed
sketch of the one shown in Fig. 7-4.
The drive circuit prepares the matrix for a selection by applying +22v on
one of the 32 horizontal leads. Assume lead HO. You can see from Fig. 7-5 that
the HO horizontal lead is common to 32 flip-flops, one in each of the 32 groups.
The clamping translator, which feeds the verticals of the matrix, selects one of
its output leads; let's assume V31. This activates one flip-flop group.
The flip-flop controlled output circuit in Fig. 7-5 shows what an actual out-
put looks like. The outputs from two AND gates are connected to a flip-flop.
The outputs of the flip-flop are connected to a flip-flop-to-relay amplifier. When
the HI lead has the +22v on it, and the V31 lead is undamped by the clamping
translator, an output from AND gate 1 sets the flip-flop. The flip-flop's set out-
put lead activates the FR amplifier and its output lead goes to ground. This
ground is the signal from an output that operates the supervisory relay in a
trunk assigned to this output point.
To put this output in its reset state, the central control sends another address.
This address selects the HO lead and V31 lead in the matrix. AND gate trans-
mits an output, and the flip-flop resets. The FR amplifier turns off and removes
the ground. The relay in the trunk releases.
Though all outputs are selected in the manner explained above, not all out-
puts are controlled by flip-flops. AND gate Group 30 is made up of fifteen spe-
Sec. 7 . 2
Method of Operation
193
H1
TEST FIELD OUTPUT
"*\
J)
S 1
FF
R
J\ ■
\. OUTPUT
FR>~=^
HO
VI
V(
)
FLIP— FLOP CONTROLLED
OUTPUT
. -
-hTT-
S 1
FF
R
"fr>°- u - t
HO
^
^y
'■„;■'
V31
'
f
...:.„:.:,!.:■' ■.'!.
"AND'
HO
GATE GROUP
~\ OUTPUT
V30
^_
FIG. 7-5. Matrix, FF Groups 00 through 31.
cial diode-resistor AND gate packages. The outputs (a +22v pulse) from this
group activate electronic circuits in other units of the system.
The SD is a kind of buffer between the CC and the relays in the trunks. It
accepts very fast signals from the central control and transmits them to the
slower speed devices. Let's take an example to show how the signal distributor
acts as a buffer. The central control recognizes a request for service to out-pulse
on a trunk. It sends an address to the SD to seize a particular idle outgoing trunk.
Then it carries out its other office duties. Now the central control returns to
the SD to have it operate and release the trunk relay at the dial pulse rate. This
relay generates dial pulses on that trunk. These pulses are sent to the distant
office. This action is indicated by Fig. 7-6, on page 194.
194
The Signal Distributor
Chap. 7
TRUNK
SEIZED
DIAL
PULSES
START
ACTIVE STATE
NORMAL STATE
OF OUTPUT -
TALKING
DIAL
PULSES
END
DISCONNECT
FIG. 7-6. Typical output from a point assigned to an outgoing trunk.
7.3 DUPLICATION AND TRANSFER
The failure of a diode or transistor in either the delay or enable circuits
could affect all the circuits that are controlled by the SD. Such a failure would
result in no enable pulse and could not be allowed for more than a few milli-
seconds. Therefore, to insure the reliability of the SD, certain portions of it are
duplicated. This permits the transfer of duplicated units.
Duplicated units are marked blue and yellow to differentiate between and
1, or A and B, functional units, respectively. Also, there are yellow and blue
SELECTOR DRIVE
A
HA
LEADS
VA
LEADS
TRANSFER*
SECTION
* RELAY CONTACTS
CONTROLLED BY
CENTRAL CONTROL
DUMMY
LOADS
32 PACKAGES
HH
LEADS
SELECTOR DRIVE
B
HB
LEADS
VB
LEADS
VV
LEADS
MATRIX
FF GROUPS 00-31
FIG. 7-7. Signal distributor, transfer of duplicated equipment.
Sec. 7 . 3 Duplication and Transfer 195
trouble lamps. The lighted lamp always shows which unit can be worked on.
If no lamps are lighted, both units are OK.
The duplicated units are shown as selector drives A and B in Fig. 7-7. The
circuits of the selector drives are shown in Fig. 7-4.
When selector drive A is used for service calls in the system, selector drive B
is in the stand-by condition, and vice versa. For example, let us assume that
selector drive A is being used for service calls. Under this condition, the relays
associated with the contacts that control the HA and VA leads are operated,
and the information from selector drive A goes to the outputs. The relays as-
sociated with the contacts that control the HB and VB leads are released, so
selector drive B output leads work into the dummy loads. The dummy loads
insure that the selector drive in the stand-by unit is fully loaded for testing.
The dummy loads are about the same as the loads presented by the flip-flop
groups.
Now let us assume selector drive B is used for service calls. The central con-
trol starts a transfer signal that releases the relays controlling the leads of se-
lector drive A. Also, it operates the relays controlling the leads of selector drive
B. Selector drive B selects the outputs of the SD, and selector drive A works
into the dummy loads.
7.4 POWER
There are two office power supplies used by the signal distributor, 230
volts alternating current and —48 volts direct current. The —48 volts is used for
the operation of the transfer relays and to light lamps; the 230 volts is used
to supply the rectifiers mounted in the front bay of the cabinet, as shown in
Fig. 7-2. Since there is a duplication of equipment throughout the office, the
office battery to the SD is supplied on two buses, B and C, for both office supplies.
The rectifier units marked A and B, mounted on the front bay, are supplied
the 230v by office buses C and B, respectively. The rectifiers marked — 16 A,
+22 A, and +16A supply power for all the duplicated units marked A. The
rectifiers marked B supply all the duplicated units marked B.
The two vertical columns of rectifiers from C and D up are also supplied by
the 230-volt B and C buses. Looking at Fig. 7-2, the left column of rectifiers
marked -16C, .+ 16C, -16E, +16E, -16G, and +16G are supplied by
the 230v B bus. The right column marked - 16D, +16D, - 16F, +16F,
— 16H and +16H are supplied by the 230v C bus.
196 The Signal Distributor Chap. 7
The two vertical columns of rectifiers from C and D up have paralleling units
associated with them. These have the same voltage designation as the rec-
tifiers: for example, — 16C rectifier, — 16C paralleling unit; and — 16D
rectifier, — 16D paralleling unit. These four units work together to supply
— 16v to mounting plates 100-109 on the rear bay of the cabinet. When a trou-
ble occurs in one of the rectifiers, assume — 16C, it is detected by the parallel-
ing unit associated with it, and a lamp in the paralleling unit C is lighted. There
is no interruption of power because the paralleling units C and D are in parallel,
and the D rectifier supplies the power needed for the circuit. The — 16C recti-
fier may be turned off (by a switch on the unit) and replaced very easily. The
+ 16 C and D units also supply power to mounting plates 100-109.
The power units +16E and +16F, and — 16E and — 16F, supply power to
the equipment on mounting plates 110-119; and the power units +16G and
+ 16H, and — 16G and — 16H, supply power to the equipment on mounting
plates 120-129. All these groups of units work in the same manner as explained
for units C and D.
7 . 5 MISCELLANEOUS
Reset Switching Relay— Fig. 7-2
The reset switching relay determines the state of all the flip-flops that con-
trol outputs when the power is first turned on. The operation of this relay puts
all these flip-flops in the reset state. This means that no outputs are active.
Test Fields A and B— Fig. 7-5
The test fields are outputs used only for testing the SD and the scanner. They
form a diagonal line in the matrix, and therefore check each vertical and hori-
zontal line in the matrix. By addressing the SD to these outputs, the central
control can check the operation of the SD and the scanner.
A diagnostic test program, addressing the test field outputs, detects any
trouble in the SD, other than single output troubles in the matrix. The diagnostic
testing locates trouble in that section of the SD (a selector drive) where a trouble
would cause many false outputs. The other selector drive is then switched into
service, and the trouble cleared in the out-of-service selector drive.
Single output troubles in the matrix are detected by recognizing a failure in
the circuit assigned to that output. When a trouble is detected, it can easily be
cleared by replacing one or more of three packages associated with that output.
Sec. 7 . 5 Miscellaneous 197
The assignment for all of the outputs of the SD are shown on ES-1A076-01,
Signal Distributor Flip-Flop Group Lead Assignments— Morris. The circuit
drawing for the Signal Distributor is ES-1A013-01.
AND Gate Group 30— Fig. 7-5
AND gate group 30 is a group of outputs activated by AND gates. The out-
put signal is a +22v pulse. It is used to set or reset flip-flops in other electronic
circuits in the ESS.
The flip-flop groups 30A and 30B, though they are outputs, are duplicated
for reliability purposes. When the A side of the selector drive unit is in service,
flip-flop group 30A is used. When the B side of the selector drive unit is in serv-
ice, flip-flop group 30B is used. The AND gate group is used by both selector
drive units, because it is not duplicated. Either the FF group is used or the
AND gate group is used, never both or a combination of the two.
Chapter 8
The Barrier Grid Store
Storing information isn't new to the telephone art. The first operator to put
up a switchboard connection remembered the number called for, long enough,
at least, to search it out in the switchboard multiple and to make the connec-
tion. After this single task was completed, the operator erased the number
from her memory and was ready for the next call.
Relays are used to duplicate the operator's memory in present-day dial tele-
phone switching systems. They count pulses and store digits during the dialing
phase of the call. After the digits dialed are analyzed and the connection is
set up, the relays are released and ready to accept an entirely new set of pulses
and digits.
8 . 1 DESCRIPTION OF THE BARRIER GRID STORE
In the ESS, the barrier grid store (BGS) provides the erasable memory.
It has a cathode-ray tube with a mica plate target on which electrostatic charges
are stored. The tube is known as the barrier grid tube (BGT). When the electron
beam deposits a minute pile of electrons (an electrostatic charge) on the target,
a one (1) is stored; where there is no electron pile (no electrostatic charge), a
zero (0) is stored. Each memory cell (spot) may be compared to a relay. A "1"
represents an operated relay; a "0" represents a released relay. The BGS can
produce" 16,384 memory cells on the mica plate, each capable of storing a
1 or a 0.
Figure 8-1 shows how the central control (CC) and the barrier grid stores
(BGS's) are interconnected. Four BGS's furnish the temporary memory for the
ESS. Two stores are always active and two are in stand-by condition under
normal operations. The CC directs the BGS, via the control leads and the stand-
by transfer, to one of the 16,384 spots on the mica plate. Also, it orders the BGS
198
Sec. 8.1
Description of the BGS
199
ANSWER LEADS
CENTRAL CONTROL
BGS
-•--CONTROL-
LEADS
ANSWER LEADS
STAND-BY TRANSFER
ADDRESS
_ AND
ORDER
LEADS
FIG. 8-1 . Central control and barrier grid store interconnections.
to "read" or "write."* When the CC sends a "read" order to the BGS, the
answer, or 1 , is returned to the CC over the answer leads.
8 . 2 EQUIPMENT ARRANGEMENTS
Each BGS is a two-cabinet self-contained unit; one such unit is shown in
Fig. 8-2. The power cabinet, BGP-0, contains eight plug-in rectifier units, as
well as the alarm and control circuits. The storage cabinet, BGS-0, houses the
barrier grid tube, the electron-tube packages, the plug-in chassis units, and
miscellaneous other packages. All these devices are needed to operate the
barrier grid tube (BGT) as a memory unit.
8.2.1 BGS-O, Front Bay (Fig. 8-2)
A hinged plastic door covers the front of the storage cabinet; in
addition, a metal door covers the plastic door. The plastic door protects the
packages. Also, it helps to distribute the cooling air uniformly through the
cabinet even though the metal door is open. Holes in the plastic door permit
access to the equipment for adjustment.
*In the language of electronic computing devices, to "read" means to obtain information
from a memory unit, and to "write" means to insert information into a memory unit. In
the BGS, an electron beam is used to determine the state of charge on a spot in the mica
"memory" plate. This is the way we "read" a spot, or obtain information from the BGS
memory unit.
200
The Barrier Grid Store
Chap. 8
X-ADDRESS
REGISTER
X-DIGITAL
ANALOG
CONVERTER
X-DEFLECTION
AMPLIFIER
STORAGE UNIT
Y- DEFLECTION
AMPLIFIER
MISC UNIT B
DISCRIMINATO
MONITOR TEST
POINTS
RECTIFIER
UNITS
FIG. 8-2. Barrier grid store and power cabinets, front view.
The plug-in chassis have handles. These are adjacent to the locking levers
that secure the chassis to the mounting plates. Connectors on the back of
each chassis engage plugs on the mounting plates. These connectors carry
power and signal leads to each unit.
Above and below the storage unit are the X and Y address and deflection
systems. These two systems position the electron beam in the BGT. The storage
unit houses the BGT, the raster reference tube (RRT), and the circuits that must
be mounted near these tubes.
The miscellaneous unit B has a variable delay line and some minor compo-
nents. Two packages are mounted on the plate adjacent to the B unit.
A discriminator, which determines whether a 1 or a was read at a spot, is
mounted above the test monitor. Connectors for test sets, monitor jacks, and
filament supply fuses are mounted on the monitor plate.
Sec. 8.2
Equipment Arrangements
201
FIG. 8-3. Barrier grid store, gate bay.
The Gate Bay— Fig. 8-3
The equipment in the front bay is gate-mounted to permit access to the
wiring side of both the front and the rear bays. Fig. 8-3 shows the gate bay
swung out. Air, supplied through adjustable grilles, flows through the cabinet
and is vented out the top. Interlock switches and gate locks are mounted on
the edge of the gate.
202
The Barrier Grid Store
Chap. 8
8.2.2 BGS-0, Rear Bay (Fig. 8-4)
All wires and cables enter at the top of the cabinet and terminate
on the terminal strip. Manual and automatic controls for positioning the array
of memory spots on the BGT are located in the
servo chassis indicated in the upper part of Fig.
8-4. The next three positions contain the se-
quence control circuit packages. These circuits
control the reading and writing sequences.
A group of voltage dividers and their indi-
cator lamps are located in miscellaneous unit A.
Voltages derived from the dividers on the BGS
d-c supplies are sent to the administration center
voltage monitor. Any detected voltage variation
will be printed out on the teletypewriter.
At the bottom of the rear bay are filament
transformers and marginal test transformers.
When trouble occurs, and during a preventive
maintenance program, the administration cen-
ter, through the marginal test transformers,
causes the voltage on a selected circuit to vary
from a normal value. While the voltage is vary-
ing, the circuit is given a series of timed test
operations. If a failure occurs, the voltage at
the time of failure can be determined. With
this test, the system detects a weak package,
which can be replaced before it causes an in-
service trouble. Of course, preventive mainten-
ance tests cannot be made on active equipment.
The packages used in each BGS are listed in
Table 8-1.
VC804
FIG. 8-4. Barrier grid store,
rear equipment.
(
1
c
c
3
2 TERMINAL STRIP
>
5 SERVO
, ["« — PACKAGE
SEQUENCE
CONTROL
1
i
ID"
>
MISCELLANEOUS
UNIT "A"
, :0D
[=, MARGINAL f=f
11 TEST ^^^
J3 TRANSFORMERS ©_
□
-. . FILAMENT , , _
SUPPLY
1 ' TRANSFORMERS l >
99
BGS
8.2.3 BGP-0, Front Bay
The location of the equipment in the power cabinet is shown in
Fig. 8-2. The power features are described in Sec. 8.6 on page 223.
Sec. 8.2
Equipment Arrangements
TABLE 8-1. PACKAGES USED IN EACH
BARRIER GRID STORE
203
F-Spec.
No.
CPS*
No.
Quantity
Name
F-52704
F-52703
F-52702
F-52705
F-52717
F-52610
F-52716
F-52977
28
8
37
160
159
165
179
35
5
1
21
1
2
1
1
10
OR Gate
AND Gate
Flip-Flop
Blocking Oscillator
Blocking Oscillator
Back Plate Driver
Pulse Monitor
Input Buffer
*CPS means Circuit Package Schematic.
8 . 3 APPARATUS ELEMENTS
8.3.1 The Barrier Grid Tube (BGT)
The barrier grid tube (BGT) is a cathode-ray tube with a mica plate
target instead of a phosphor screen target. A photograph of the BGT is repro-
duced in Fig. 8-5, and a schematic diagram of its structure is shown in Fig. 8-6.
An electron beam is used in the BGT to remove or deposit electrostatic
charges on the mica plate (Fig. 8-6). When a "1" is to be written, the back
FIG. 8-5. Barrier grid tube.
204
The Barrier Grid Store
Chap. 8
CONTROL GRID-
CATHODE -~,
. FOCUS COLLECTOR
I APERTURES
I
DEFLECTION
I ANODE | ' PLATES ^
MICA
PLATE
TARGET
BARRIER_
GRID
. - BACK PLATE
TO
BACK PLATE
DRIVER
-1000V
TO
GRID DRIVER
TO
READ
PREAMPLIFIER
FIG. 8-6. Barrier grid tube elements.
OUTPUT TRANSFORMER
SECONDARY WINDING
READ PRE-AMPLIFIER
OUTPUT TRANSFORMER
COAXIAL PRIMARY
WINDING
BARRIER GRID TUBE' TARGET SHIELD
CONNECTOR
FIG. 8-7. Barrier grid tube and read pre-amplifier.
Sec. 8.3 Apparatus Elements 205
plate potential is raised above the barrier grid potential while the electron
beam strikes the target. After a short interval, both the back plate and the
control grid are shut off, leaving an electrostatic charge on the mica plate.
A "0" is written with the back plate at ground potential. No electrostatic
charge remains on the plate when the control grid is shut off.
When the beam strikes the target to read a spot, current flows to or from the
barrier grid. This current in the output transformer primary produces a low
secondary voltage at the read pre-amplifier input. After additional amplifica-
tion, the signal feeds a discriminator which produces the 1 or output.
The read pre-amplifier and BGT are shown in Fig. 8-7.
Hi
u
-APPROX. H-L"
FIG. 8-8. Raster reference tube.
8.3.2 The Raster Reference Tube (RRT)
The raster reference tube (RRT), shown in Fig. 8-8, is also a cathode-
ray tube. A schematic of the RRT is shown in Fig. 8-9. The RRT has four
pairs of over-lapping plates for the target. Each pair of plates has a reference
edge that is positioned to correspond to an edge of the raster* in the BGT.
Periodically the system deflects the RRT electron beam to these reference
edges. If there is a raster size or centering error, it is detected by the over-
lapping plates and their associated circuits. A voltage is developed to correct
the error; this voltage is sent to the address and deflection circuits. Since both
*A "raster" is a predetermined pattern of scanning lines that provide a uniform covering
of a specified area.
206
The Barrier Grid Store
Chap. 8
ELECTRON FOCUS
CATHODE GUN
DEFLECTION
CONTROL
GRID
• • •
^
e*
APERTURE TARGET
PLATES
t?
(I
t?
FIG. 8-9. Raster reference tube elements.
the RRT and the BGT are driven by the same deflection amplifiers, any raster
adjustment affecting the RRT will also appear in the BGT. In this way, the
spots in the BGT are held to a pre-adjusted spacing, and the square array is
kept centered within the target area. Figure 8-10 shows the relationships
between the target plates in the RRT and the BGT.
A rear view of the storage unit, Fig. 8-11, shows the BGT shield, the RRT,
and associated components.
REFERENCE
EDGES
\
REFERENCE;
EDGES
TARGET
PLATES
\
RASTER REFERENCE TUBE
BGT
FIG. 8-10. Relation of reference edges in RRT to raster in BGT.
Sec. 8.4
Method of Operation of the BGS
207
BARRIER GRID TUBE
CONTROL GRID DRIVER
*
BARRIER GRID
TUBE SHIELD
READ
PREAMPLIFIER
HOUSING
RASTER REFERENCE TUBE
ENCLOSED IN SHIELD
FIG. 8-11. Barrier grid storage unit, rear view.
8 . 4 METHOD OF OPERATION OF THE BGS
The barrier grid tube and its control circuits are shown schematically in
Fig. 8-12 on page 208.
An address circuit converts the fourteen-bit binary pulse address from the
CC to a deflection voltage that positions the electron beam on the target.
A sequence control circuit receives an order from the CC and directs the
read amplifier, back plate, and control grid in the correct sequence to carry
out the order.
8.4.1 . Address and Beam Positioning
The vertical address and deflection circuits are shown in the schematic
diagram of Fig. 8-13.
208
The Barrier Grid Store
Chap. 8
DYNAMIC FOCUS
BACK PLATE -.,
MICA PLATE-^ \
BARRIER GRID^ \ \
\ I
BARRIER GRID TUBE V ' ,
"I — fc>
111
OUTPUTS
Y
INPUTS
FIG. 8-12. Barrier grid store, control circuits.
An address is brought over from the CC via coaxial cables to the input
buffers. Cables from a test jack also terminate here. This jack provides access
by a test set to the BGS address circuits.
The input buffers convert the 0.3-microsecond pulses from the CC to the
0.1 -microsecond pulses required by the address register flip-flops.
The BGS takes an interval of time to perform its functions. Therefore, the
address is held in the address register flip-flops while an order is executed and
until the BGS receives a new address.
The address register output appears on seven pairs of leads; each pair has
+5v on one lead and — 13v on the other lead. This combination of voltages
cannot directly drive the BGT deflection system, so the digital address is changed
to an analog voltage in the digital-to-analog converter (DAC).
The DAC is a set of vacuum-tube diode switches that are operated by the
address register flip-flops. These diodes switch currents determined by the re-
sistors in their anode circuits. The resistance values are different for each
Sec. 8.4
Method of Operation of the BGS
209
TO
TEST JACK
FIG. 8-13. Barrier grid store, vertical address and deflection circuits.
switch. A low-value resistance is in the switch operated by the most significant
digit flip-flop, No. 6, while the highest resistance value is in the switch operated
by the least significant flip-flop, No. 0. Changing the state of flip-flop No. 6
causes the electron beam to move a distance equal to one half raster. If the state
of flip-flop No. is changed, the beam moves to an adjacent spot.
The output of the DAC drives the deflection amplifier; the deflection voltage
that results is applied to the BGT and RRT deflection plates. This positions the
electron beam for the vertical axis. An identical system generates the deflection
for the horizontal axis.
8.4.2 The Sequence Control
The orders from the CC are received by the sequence control, which
is shown schematically in Fig. 8-14. In normal operation, each address is
accompanied by one of the following orders:
210
The Barrier Grid Store
Chap. 8
BARRIER
GRID
TUBE
r
I 1
III'
""m / -
t
i
i
/
I
I
-J / 7
^RRG
SEQUENCE
CONTROL
GRID DRIVER
READ PREAMPLIFIER
FROM
CENTRAL -
CONTROL
RCH
RW1
1 READOUT
RWO
BACKPLATE
DRIVER
DISCRIMINATOR
DOWN
f ^ 21
*
SENSE
TO j
% "0"
CENTRAL -i.
CONTROL
"1"
FIG. 8-14. Barrier grid store, sequence control.
BACK
PLATE
DEFLECTION READ
■*■ .6(1 SEC -»-(■*- .75/K SEC
WRITE
75/U SEC -*\*-AMS^
ORDER AND
ADDRESS
ORDER AND
ADDRESS
1.0 1.5
CYCLE TIME /X SEC
FIG. 8-15. Barrier grid store, operation cycle.
Sec. 8.4
Method of Operation of the BGS
211
Order
Read— Regenerate
Read— Change
Read -Write 1
Read -Write
Abbreviation Meaning
RRG Read a spot, and regenerate it (that is, replace
the charge on that spot to overcome the effects
of decay, including any charge lost in the opera-
tion of reading it).
RCH Read a spot and change its state, either from
1 to or from to 1 .
RWI Read a spot and, no matter what is there, write
a 1 . (This order is also used simply to write a 1 .)
RWO Read a spot and, no matter what is there, write
a 0. (This order is also used simply to write a 0.)
The grid driver, shown as part of Fig. 8-14, pulses the BGT control grid on
and off, and thus controls the electron flow toward the target. The back plate
driver raises and lowers the back plate potential by 50 volts. The back plate
potential is +50v when a 1 is being stored, and at ground when a is being stored.
The read preamplifier and the discriminator together amplify and deter-
mine the BGT output. The 1 and output signals are not all equal in ampli-
tude; the discriminator is adjusted to a marginal area and produces a fixed
output for each read-out. The discriminator output is sent to the CC. It is also
combined with the read— change and read— regenerate orders in the sequence
control circuit to raise the back plate potential, if a 1 is to be written.
A BGS operation cycle is shown in Fig. 8-15. The diagram charts the sequence
of operations and shows the time required for each.
8 . 5 REGISTERS
The BGS memory spots are grouped to form various call and control
registers for the ESS. Twenty-nine types of registers are listed in Table 8-2,
which also tabulates the number of registers of each type, the number of
memory spots per register, and the symbolic abbreviation for each. The quan-
tity of spots per register varies with the different kinds of registers; the number
of spots assigned to a register is determined by the amount of memory required
for each register to perform its task. The number of customers served and their
212
The Barrier Grid Store
Chap. 8
TABLE 8-2. REGISTERS IN THE BARRIER GRID STORES
Number of
Registers
Memory Spots
per Register
Name of Register
12
64
Originating Register (OR)
8
42
Ringing Register (rr)
4
21
Disconnect Register (DR)
6
39
Incoming Register (|R)
6
88
Outpulsing Register (OPLR)
4
37
Reverting Register (RVR)
4
14
Blocked Dial Tone Register (BDTR)
35
16
Operator Trunk Register (OTR)
4
38
Operator Dialing Register (ODR)
4
32
Operator Disconnect Time Register (ODTR)
1
28
Operator No-Test Register (ONR)
2
63
Test Desk Register (TDR)
4
38
Bridged Extension Register (BER)
20
128
Full-Dial PBX Call Register (FXCR)
64
104
Half-Dial PBX Call Register (HXCR)
8
112
Supplementary PBX Call Register (SXCR)
8
141
PBX Attendant Register (XAR)
2
5
PBX Tie Line Register (XTLR)
64
11
Indicator Status Register (ISR)
6
33
Indicator Control Register (ICR)
6
32
PBX Reference Register (XRR)
128
Main Program Register (MPR)
256
Network Register (NR)
64
Translation Register (TR)
16
Regeneration Register (RER)
576
Diagnostic Register (DIR)
1112
Traffic Count Register (TFCR)
192
Teletypewriter Register (TTYR)
128
FSS Exposure Register (FSXR)
Sec. 8.5 Registers 213
calling habits determine how many call registers the system should have. Some of
the registers are in use on every call, for periods of less than a second; the
dialing registers are needed for perhaps 20 seconds on a call; the ringing reg-
isters, 5 minutes at the most. The main program register is always in use, since
it is used to coordinate the entire system operation.
Since two barrier grid stores are needed to supply enough spots for all the
registers and the administration data, this information is split up between
them. About half of the registers appear on the left side of each BGT, and
half of the administration information on the right side of each tube. This is
shown in Fig. 8-16 for line and register tube zero (LRT-o), and in Fig. 8-17 for
line and register tube one (LRT-l). The active stores are referred to as LRT-o
and LRT-l; the associated stand-by stores are referred to as SB-o and SB-i.
The CC sends the same address to all four BGS's. It sends an order to one
or more of the BGS's as specified by the system.
The BGS's can be operated in either a multi-tube or a single-tube mode. In
the multi-tube mode, an order may be sent to all BGS's; in the single-tube mode,
to only one in-service BGS and its stand-by BGS. During diagnostic programs,
the active and stand-by tubes are read independently, and their respective read-
ings are matched to detect errors. The circuits that control these operations are
in the CC and are explained in detail in Chapter 10, The Central Control.
The normal operating mode of the BGS is shown in Fig. 8-18. When the
system is operating with the four BGS's, the answers from each active store
are matched with the answers from its stand-by store. If the answers do not
match, the system enters a fault-checking routine to determine which store
gave the incorrect answer. During this time, the system does not process calls
but directs its entire facilities to isolating the unit in trouble (talking connec-
tions are not affected). The system determines which stand-by store will take
over the active status, if an active unit fails. It also switches one of the stand-by
stores to split-tube operation, as shown in Fig. 8-19. Here we see the positions
to which the tubes are assigned for several trouble conditions. A single-trouble
mode (a failure of BG-3) is diagrammed in (B) of Fig. 8-19. To meet this
situation, BG-2 is split so that it stores administration information from BG-o
in its left half and administration information from BG-l in its right half.
You can see that BGS answer matches are limited to BG-l administration
information.
214
The Barrier Grid Store
Chap. 8
if)
«l«
«
aojao o»|
127
XTLR 3
B_-RGR ,SR
5-
NON-PBX
TRAFFIC & NIGHT
ADMINISTRATION TRANSFER
SPOTS
\
L ^
REMOTE CONCENTRATORS
113
TDR
LI
^ONR
Tl
XAR
§8 ^
RECENT
CHANGE SPOTS J
/ 1
TT2
\ /
39 en
PBX
\ /
99 *■■
NIGHT
96
\
i
o
8s l/)
88 o
TRANSFER |
96
% §
-
95
E S
MPF
1
Bq
Ben
Q
cr
-
n cr
S3 °
89 <*
8S n
§8 ' Jl
88
ZZO
O
8s uj
OZ2
Kg _j
89 n
M 1-
>-^ z
5S - '
s8 =>
3S 3
FXCR
■
P
84
tr
KM
64
O
_
> UJ
tr
h-
o
tr
K
1-
O
a
c
c
cr
u
x
tr
m
r-
m
o
UJ
cr
z
o
k
hi
i-
RECENT
o
HXCR
o
UJ
F
CO
i-
o
CHANCE
to
z
<
CC
REGISTERS
_J
0-
O
Lj
lo
D_
V)
tr
<*
01
F
i-
Iz
_l
o
32
a
.
? 2
o
L
lo
z
<
I
r
>-
(0
(13
Z
D
tr
2
1-
L2
T2
tr
X
hi
Rj
H
tr
O
l-nj
88
UU1
go-
■ 5
a:*
ZZo
° >
On
81
OZ2
*~o
UO(Z
C0
tr
1-
Q
O
er
tr
a
c
c
HXCR
V)
FXCR
UJ
tr
Z
o
a
i-
<
tr
Z
o
RECENT CHANGE
(0
tr
o
REGISTERS
z
<
tr
0-
O
o
UJ
K
t-
32
o
2
32
UJ
a.
LZ
T2
X
o
CO
oj| O
1
■tf
<\j
FIG. 8-17. Barrier grid store, register layout LRT-1 .
216
The Barrier Grid Store
Chap. 8
BGO
LRTO
TRUNK
ADM :
AND
INFO ■
LINE
AND
SPOTS
MISC
AND
REGISTERS
REGISTERS |
64 12
1 1
T BG2 T
I :
TRUNK
AND
LINE
SPOTS
AND
REGISTERS
BG2
SBO
ADM
INFO
AND
MISC
REGISTERS
BG1
LRT1
TRUNK
AND
LINE
SPOTS
AND
REGISTERS
ADM
INFO
AND
MISC
REGISTERS
I 1
▼ BG3 T
BG3
SB1
TRUNK
AND
LINE
SPOTS
AND
REGISTERS
FIG. 8-18. Barrier grid store, normal operating mode.
Immediately upon switching out a faulty unit, the system returns to the task
of handling calls. During diagnostic program time, the administration infor-
mation is copied from the active BGS to the split BGS. When copying is com-
pleted, the split tube is ready for system use. The fault-check routine and switch
require less than two-tenths of a second (0.2 second) to complete.
The BGS that failed is now given a series of diagnostic tests that pinpoint the
source of trouble within the unit. Teletypewriter print-outs indicate the test
that failed. The diagnostic dictionary is used to translate the teletype message
to equipment that must be replaced.
After a BGS has been repaired, a request to return it to its normal system
position is started through the teletypewriter. The information to be stored is
copied from the active store or stores. When this is completed, the store returns
to system use.
Sec. 8.5
Registers
217
®
®
BG1
a!b.
Tt
r i
A IB
1 ;
1 1
1
X ! Y
Xi
X Y
I
NORMAL
MODE
BGO = LRTO
BG1 = LRTI
BG2 = SBO
BG3 = SB1
a| b
1
; T ;
Xj Y
] J. I
1
1
1
! T !
: 1 i
! I ■
i I i
i J ;
SINGLE
TROUBLE MODE
BGO = LRTO
BGI = LRTI
BG2 = SPLIT TUBE
BG3 = TROUBLE
SINGLE
TROUBLE MODE
BGO = LRTO
BGI = LRTI
BG2 = TROUBLE
BG3 = SPLIT TUBE
BG2
©
r
A ! B
...i..
BGO
A I B
X I Y
X I Y
BG3
©
DOUBLE
TROUBLE MODE
BGO = LRTO
BGI = LRTI
BG2 = TROUBLE
BG3 = TROUBLE
DOUBLE
TROUBLE MODE
BGO = TROUBLE
BGI = TROUBLE
BG2 = LRTO
BG3 = LRTI
DOUBLE
TROUBLE MODE
BGO = LRTO
BGI = TROUBLE
BG2 = LRTI
BG3 = TROUBLE
ARROWS INDICATE LOCATION OF DUPLICATED
INFORMATION AFTER SWITCH AND COPY IS COMPLETED
A AND X = LINE AND REGISTER INFORMATION
8 AND Y = ADMINISTRATION INFORMATION VG823
FIG. 8-19. Barrier grid store, operating modes under various abnormal conditions.
8.5.1 Register Description
A brief description of some of the functions of a few BGS registers
is given below.
Line and Trunk Supervisory Register
One of the functions of the ESS is to recognize supervisory signals. Service
requests and disconnects are supervisory signals. The scanner can only tell
when a line is off-hook or on-hook. Therefore, some memory is provided to
218
The Barrier Grid Store Chap. 8
TABLE 8-3. LINE SPOT MEMORY ASSIGNMENTS
State of
Line Memory Spot
Condition or State of Line
LI L2
Idle
line on-hook
1
Served by Register
Customer dialing
Served by originating register
Calls to No. 5 crossbar served by outpulsing register
Ringing
Called lines served by ringing register
1
Talking
Connection set up through distribution switching network
VG 819
TABLE 8-4. SYSTEM ACTION DURING SUPERVISORY SCAN OF LINES
Scanner
Output
Line Memory Spots
LI L2
State of
Line
System Action
On-Hook
No system action.
1
1
Off-Hook
No system action.
1
Off-Hook
Memory indicates that the line was idle
during last scan. Assign originating
register, and change memory spots to
L1=0, L2 = l.
or 1
1
Off- Hook
or
On-Hook
Memory indicates system is processing
information coming in from this line.
No system action.
1
On-Hook
Memory indicates talking during last
scan. Assign disconnect register, and
change memory spots to LI =0, 1.2 = 1,
until disconnect is completed; then
change to LI = 0, L2 = 0.
Sec. 8.5 Registers
TABLE 8-5. TRUNK SPOT MEMORY ASSIGNMENTS
219
Trur
Tl
State of
k Memory
T2
Spot
T3*
Condition or State of Trunk
Idle
1
1
Signal (Dialing)
1 1
Talking
1
Busy
Trunk not assigned.
Trunk busy for maintenance.
Trunk seized prior to register assignment.
a T3 spot is assigned to the trunk.
VG 821
enable the system to detect these line changes. Two line memory spots are
assigned in the BGS to each line in the office. These are the LI and L2 spots.
The spot states are changed when the line goes from on-hook to off-hook;
when the customer is dialing; when the customer starts talking; and when the
customer disconnects. The states of the LI and L2 spots for various line con-
ditions are shown in Table 8-3.
The system action, as a result of comparing the scanner output and asso-
ciated line spots, is shown in Table 8-4. The supervisory scan of all lines is
performed by the system ten times every second.
Trunks which have been assigned Tl and T2 spots are scanned in a similar
manner, and the spots are altered to agree with the states of the trunk. A T3
spot is assigned to each trunk within a group of trunks. Dial tone, ringing,
and outgoing trunks are examples. These spots are used when the system is
hunting an idle trunk within a group. Incoming trunks do not have T3 spots
because the ESS does not select a trunk of this type. The states of the Tl, T2,
and T3 spots for various trunk conditions are shown in Table 8-5.
220 The Barrier Grid Store Chap. 8
(1
(2
(3
(4
(1
(2
(3
(4;
(5
(1
(2
(1
(2
(1
(2
(3
Originating Register (OR)
Records all call originations.
Records dial pulses except on intra-PBX-WP calls.
Recorded digits are used to analyze the call type and to translate
the directory number to an equipment number.
Advance the control to another register to complete the call.
Ringing Register (RR)
Controls the call during ringing and until the called line answers.
Through the scanner, detects answers.
Times the maximum ringing periods: 5 minutes for non-PBX calls,
and 45 seconds for attended CGS calls.
Not used on calls to No. 5 crossbar or EAS offices.
Released when talking connection is set up.
Disconnect Register (DR)
Controls the release of lines that have returned on-hook after a
connection was set up in the system.
Times for line hits and disconnects.
Incoming Register (IR)
Detects, counts, and stores the digits dialed over incoming trunks
(the last four digits).
Advances control to the ringing register, RR, for call completion.
Outpulsing Register (OPLR)
Controls digits outpulsed to a connecting office.
Digits from lines recorded by the OR are transferred to the OPLR.
Records four digits for each call to the No. 5 office, and seven digits
for calls to EAS offices.
(4) Timing spots in the OPLR, as well as in the program, control various
timing intervals during outpulsing.
Sec. 8.5 Registers 221
(5) Starts a scan of the calling line prior to the last digit to determine
whether the line is off-hook. If the line is on-hook, the OPLR and the
line are released, and the No. 5 crossbar register times out.
Reverting Call Register (RVR)
(1) Receives eight digits from the OR, and controls the call until an
answer is detected. No network talking connection is set up for a
reverting call.
(2) Times 3.5 minutes; if no answer, the connection is released.
Blocked Dial Tone Register {BDTR)
(1) Times for retrials to dial tone connection for lines that have been
blocked in the concentrator and distribution switching networks.
(2) The OR must be available before a connection is set up on retrial.
Operator Trunk Register (OTR)
(1) An OTR is permanently assigned to each operator trunk, permanent
signal trunk, partial dial trunk, and denied service trunk. It provides
memory for the various trunk and associated line states.
Operator Dialing Register (ODR)
(1) Action similar to incoming register.
(2) Seized after a timed start by an operator disconnect timing register.
(3) The operator may dial a single-digit-directing code for no-test calls.
Bridged Extension Register (BER)
(1) Extensions on non-PBX lines are interconnected via BER action.
(2) Translation after the second digit in the OR, for lines with bridged
extension service, will result in the BER being assigned to the call.
(3) A code plus extension number is dialed.
(4) Detects hang-up, time-out, and answer.
(5) Controls code ringing; no distribution switching network connection
required for talking.
222 The Barrier Grid Store Chap. 8
Operator Disconnect Timing Register (ODTR)
(1) Times for switchhook flashes and disconnects. Also times a start-
dial interval from operators.
Test Desk Register (TDK)
(1) Works with the test trunks from the ESS local test cabinet to the
distribution switching network.
(2) Stores a directing digit 2, plus a four-digit directory number for
no-test calls.
(3) Stores a directing digit 4, plus a four-digit line selector address for
line circuit test calls.
(4) Stores a directing digit 5, plus a five-digit network selector address
for a trunk test.
(5) Stores a directing digit 3, plus the five-digit network selector address
for camp-on-busy connection. If a trunk is busy, the TDR starts
half-second scans until the trunk becomes idle, and then seizes it.
Main Program Register (MPR)
The main program oversees ESS operation. It allots time intervals to the
routines and programs which are necessary to process calls and to operate the
system. Some system jobs are more important than others and must be com-
pleted at regular intervals. The main program is, in a sense, the priority list
for these operations, and the MPR is the time keeper.
Network Register (NR)
The NR is a buffer between the CC and concentrator and distribution switch-
ing networks (CSN and DSN). When the network is given a job, the NR records
the information needed for the job; it oversees this operation until it is completed.
Translation Register (77?)
Called on when a translation is made on originating and terminating lines.
Sec. 8.5 Registers 223
Regeneration Register (RER)
The barrier grid stores must be regenerated at regular intervals to maintain
accurate information. A regeneration program in the FSS specifies how the
tube should be regenerated; the RER acts to administer this program.
Diagnostic Register (DIR)
Called upon to administer diagnostic programs, if a trouble occurs in the
system.
Teletype Register (TTYR)
A buffer is required between the CC and the teletypewriter because of the
difference in speed and operation. The TTYR buffers all messages in and out
of the system via the teletypewriter.
8 . 6 POWER
The d-c power for each BGS is supplied from eight plug-in rectifier units
in its associated power cabinet (BGP) (refer to Fig. 8-2). The a-c power for the
four power units is fed from the regulated 230v a-c buses as follows:
Bus A: BGP-0
Bus B: BGP-l
Bus C: BGP-2, BGP-3
The eight rectifier units supply negative and positive regulated d-c voltages
for the BGS circuits.
A 48-volt source is required for the control circuit relays. It is supplied
from the central office battery as follows:
Bus A: BGP-o
Bus B: BGP-l
Bus C: BGP-2, BGP-3
8.6.1 Power Control
The control circuit, Fig. 8-2, in the top of the BGP applies a-c power
in three steps. This brings the vacuum-tube filaments up to operating tem-
perature before the d-c voltage is applied. The sequence takes about 130 seconds.
224 The Barrier Grid Store Chap. 8
The d-c output switch, in the test position, delays application of the d-c power
to the BGS. When this switch is later operated to the normal position, the d-c
is switched to the BGS after a ten-second delay.
Red lamps indicate failures; white lamps indicate normal conditions. When
all control and power voltages are available, the white lamps are lighted; a
failure will bring in alarms and light a red lamp to indicate the source that failed.
8.6.2 Rectifier Units
All but the — 1 5v rectifier unit are automatically regulated. The regu-
lators keep the output constant by compensating for minor variations in input
voltage and load.
Each rectifier unit has its own high-low voltage alarm circuit. This alarm
circuit provides a signal when the voltage is 10 per cent high or 25 per cent low.
To test the alarm, you operate the test switch to either the high or the low
position. This raises or lowers the voltage to the alarm circuit only. If the
alarm lamp lights, the circuit is OK. In normal operation, high-low alarm
relays provide a holding path in the control circuit. If one of them operates,
the hold path is opened and the entire power cabinet is shut down.
Rectifier units may be removed from the cabinet for maintenance after the
power connectors and locking devices at the rear of the cabinet have been opened.
An interlock on the rear door opens the start and operate path in the control
circuit.
8 . 7 MAINTENANCE
Maintenance of the BGS's is simplified because most of the testing is
done by the system. The testing procedures include matching the BGS outputs,
as well as fault-checking and diagnostic programs. The test results are printed
out by the teletypewriter in the administration center. You look up the defini-
tion of the print-out in the maintenance dictionary, and then do whatever is
necessary to restore a faulty unit to service.
When the outputs of the active and stand-by BGS's do not match, the system
determines, through a fault-checking program, which unit gave an incorrect
output. If both units pass a series of tests, the mismatch is considered an error.
A print-out records the address of the error and the units involved.
A print-out reporting trouble follows the general form shown by the example
at the top of page 225:
Sec. 8.7 Maintenance 225
A ERROR BGSXX XXX XXX
A = trouble report.
BGSXX identifies the units in which the error occurred.
XXX XXX gives the BGS address at which the mismatch occurred.
When a unit fails to pass the fault-check test, it is removed from service,
and a print-out like the following is produced by the teletypewriter:
A FT PX BGSX
A = trouble report.
FT means a mismatch due to a fault.
PX indicates the fault-check test that failed.
BGSX identifies the unit that failed.
After the faulty unit has been given a series of diagnostic tests, the specific
location of the fault, together with other pertinent information, is given on a
print-out like the following example:
A DBX C XXXXXX
A = trouble report.
DBX indicates the unit which was given the diagnostic tests.
C indicates the test on which the failure occurred.
XXXXXX is coded information which, when translated with the aid of the main-
tenance dictionary, indicates the packages or chassis to be replaced. The translation
may, in some instances, indicate the need for minor adjustments.
The teletypewriter print-out, the lamps in the administration center, and the
alarm lamps in the BGS cabinet— all indicate which BGS is out of service (made
busy).
Packages in the BGS can be replaced without additional adjustment. When
certain chassis are replaced, however, you may need to adjust various controls.
Specification X-63953 outlines the procedures to be followed for this and
other detailed maintenance in the BGS. Additional maintenance procedures
are included in Specification X-63941.
CAUTION Before replacing any packages or chassis units in the BGS, shut down the BGS
power by operating the BGS power control STOP button.
Chapter 9
The Flying Spot Store
The Flying Spot Store (FSS) is the semipermanent memory of the ESS. In it
are stored all of the instructions that tell the system what to do for every possible
call condition and for every possible system situation. These stored instructions
include program and translation information. This information is stored in a
pattern of transparent and opaque spots on photographic plates. Light beams
from one spot of light on the face of a cathode-ray tube (CRT) are directed by
a lens system to read the information stored on the photographic memory
plates. Wherever light passes through a transparent spot on the plate, a photo-
multiplier tube (PMT) behind the plate produces an electrical signal at its out-
put. This signal is a binary "1." Wherever a light beam strikes an opaque
spot on the plate, the PMT will see no light, and will read a binary "0." The
same light beams that read information from a plate are used to write informa-
tion on unexposed film plates for the FSS.
Two flying spot stores are used in the ESS. One of them is always active,
while the other is in the stand-by condition ready to take over if the active unit
is removed from service, The stand-by FSS is also used to prepare new photo-
graphic plates.
Figure 9-1 shows a typical information channel in the FSS.
9.1 THE FSS INFORMATION SYSTEMS
Each FSS contains two distinct information systems. One is used, as
previously explained, to furnish program and translation information to the
system. The other is used by the FSS to help position the electron beam of
its CRT.
The program information is used by the central control (CC) to "spell out"
system operation. The translation information is consulted by the system when
a directory number is to be converted to an equipment number. It is also used
226
Sec. 9.1
The FSS Information Systems
227
-LIGHT BEAM
PHOTOGRAPHIC
PLATE
CATHODE RAY
TUBE
CONDENSER
LENS
PHOTOMULTIPLIER
TUBE
FIG. 9-1. Flying spot store information channel. vg
to determine a customer's class as well as his type of service and his ringing
frequency. Programming and translation are described in Section 9.2.
The beam positioning information is derived from the servo code plates;
it is used to determine the location of the CRT beam. Beam positioning is
explained in subsection 9.5.2.
9.2 THE SYSTEM PROGRAM
The system program is divided into many sections, and each section
deals with a separate phase of system operation. The sections are called the
"main program," "subprograms," and "subroutines." Most of the sections are
used to service customer calls on lines and trunks. Others care for internal
system actions, trouble diagnosis, and maintenance routines.
The FSS has programs common to each group of call registers in the BGS
(described in Chapter 8). For example, there are programs for the originating
registers, the test-desk registers, and the traffic registers, to name a few. These
registers are served on a time-sharing basis with all other registers, lines, and
trunks, and with other system actions. The lines are scanned every 100 milli-
seconds (ten times per second); operator and incoming trunks are scanned at a
228 The Flying Spot Store Chap. 9
50-millisecond rate. Call registers are served more frequently because the lines
and trunks associated with these registers are feeding information into the
system or out of it.
Most of the registers, while active, are served by more than one program.
The originating register, for example, is served by programs that deal with
recording dial pulses, with partial-dial and permanent-signal timing, and with
interdigital timing at periodic intervals. Network and translation programs are
entered when requested by the originating register.
Why are so many programs needed for one register? Let us look at a relay
system for a comparison. In a relay system, when dial pulses are coming in at a
regular rate, a slow-release relay is held up. But when the pulses stop while the
customer is setting up the dial for the next digit, the slow-release relay falls
back. This causes a circuit transfer that signifies the end of a digit and at the
same time prepares another circuit to receive the next series of pulses.
In the ESS there are no slow-release relays in the originating registers. Instead,
an electronic method is used to determine the last of a series of pulses forming
a digit. This is done by checking the originating register, or any dialing register,
every tenth of a second. A separate program performs this check. It checks a
counter (a group of spots) in the register that times the interdigital interval.
As long as dial pulses are coming in at a regular rate, this counter is set to zero.
When the dial pulses stop, the counter is free to advance. Each tenth of a
second, when the register is served by the interdigital timing program, this
counter is advanced. Interdigital time-out occurs when two-tenths of a second
have elapsed. Then a subprogram is called into action to find an appropriate
digit slot in the register, and to transfer the pulses in the pulse counter to this
digit slot. Now this register is ready to receive the next series of pulses.
Permanent-signal and partial-dial timing is performed in much the same
manner. When the digit counter shows that seven digits have been received, the
system knows that a complete directory number has been dialed. Now it must
find this number as it appears in the equipment so that a connection can be
set up. Here is where the translation programs come into action. When the
translation is completed, the network programs are called upon to set up a
path through the concentration switching network and the distribution switch-
ing network.
From this you can see that calls and other system functions are completed
by doing a whole series of small jobs. Similar small jobs are being done for other
Sec. 9.2 The System Program 229
calls in a sequential manner. All originating registers are scanned for one type
of work operation at a time. The active registers get more attention from
subprograms than the idle registers. After the originating registers have been
served, the system examines the incoming registers, then the operator registers,
and so on through the entire series. The more important jobs are completed
first; those of lesser importance are completed near the end of the series. This
is an example of the priority given to certain system tasks by the main program.
Within each tenth-of-a-second interval the system runs through a complete
program cycle. This interval is divided into ten segments, each ten milliseconds
long. Within each ten-millisecond interval, all of the high-priority jobs are
completed first; then portions of lower priority jobs are completed. During
extremely heavy traffic loads, some of the low-priority jobs are put off until the
following cycle.
The Main Program Sequences
The main program sequences are shown in the block diagram in Fig. 9-2.
At the top is a 100-millisecond scale divided into ten-millisecond and one-
millisecond intervals. The sequence shown below the scale begins at the upper
left and progresses through the high-priority jobs toward the less important jobs
in the lower right. A cycle begins at the start of each ten-millisecond interval,
and ends at about the end of the tenth millisecond interval. This is repeated
ten times during the 100-millisecond interval, after which the 100-millisecond
cycle is repeated.
An index of the jobs to be completed during a ten-millisecond interval is
included in the program along with an identifying job number. If the system is
pressed for time because of heavy traffic loads, these jobs may be put off for a
ten-millisecond interval or even longer. When time is again available, the index
is consulted and the job at the top of the list is completed.
You will note that at frequent intervals in the sequence the nine-millisecond
clock is checked. If nine milliseconds have elapsed since the beginning of the
cycle, a ten-millisecond time check is made, and portions of the sequence are
skipped. Also, the ten-millisecond time check is made more frequently toward
the end of the cycles to assure that the system leaves the present sequence on
time. An interval is never shorter than ten milliseconds, but it may be as much
as several hundred microseconds longer.
230
The Flying Spot Store
Chap. 9
100 MILLISECONDS
CO
Iffiffiffi.
(9) CO)
H 2 3 4 5 6 7 89 10 H 2 3 4 5 6 7 8 9 10
OUTPULSE
REGISTER
ORIGINATING
REGISTER
INCOMING
REGISTER
OPERATOR
DISCONNECT
REGISTER
TEST DESK
REGISTER
CHECK OK TO
SCAN FOR ANS
OK'
RING REG
BRIDGED EXT
REGISTER
REVERTING
CALL REG
ALARM
CHECK
9 MS TIME
CHECK
OK
READ
SUPERVISORY
SCAN INDEX
COUNTER
l.SCAN LINES
AND TRUNKS
2. CHECK 1SEC
CLOCK
3. DIAGNOSTIC
ROUTINE CHECK
9 MS TIME
CHECK
OK'
OK
CHECK 0.1 SEC
JOB COUNTER
JOB
CHECK LIST
OF JOBS TO BE
DONE EVERY
0.1 SEC IN SOME
10 MS INTERVAL
9 MS TIME
CHECK
OK'
CHECK REGENERATION
INDEX COUNTER . RE-
GENERATE BGS AREA
SPECIFIED
DOWN
15 MIN
FLAG
SPOT
TRAFFIC
RECORD
READ OUT
9 MS
TIME
CHECK
CHECK JOB
INDEX FOR
1 SEC TO I HR
JOBS. DO IN-
DICATED JOBS
9 MS
TIME
CHECK
OK'
► JOBS COMPLETED
CHECK MISCELLANEOUS INDEX
SPOTS. 8 MS 9 MS AND I0MS
CLOCKS . DO RECENT CHANGE
WORK. DIAGNOSTIC ROUTINES.
ROUTINE TESTS. REGENERATE
BGS AND RETURN TO BEGINNING
OF NEXT I0MS INTERVAL WHEN
10 MS. CLOCK IS SET
OK
NBI
OK'
10 MS
TIME
CHECK
"C
OK
REGENERATE
SPECIFIED
BGS AREA
J
9 MS AND
I0MS TIME
CHECK
WASTE TIME
OK = NOT OK
FIG. 9-2. Main program sequences.
Sec. 9.2 The System Program 231
The system can leave the main program to enter other programs to do jobs
for the call registers, or for other reasons. Each program has a job index number.
As each program is completed, the job index number is changed to correspond
to the number of the job about to be entered. At the beginning of each ten-
millisecond interval, this program job index is changed to show the number of
the first high-priority job shown in the outpulse registers.
Among other jobs done between the blocks in Fig. 9-2 is the BGS servo
check. At appropriate intervals, the program that cares for the servo check is
entered. The job index reference spots indicate which edge of the BGS raster
requires a check. One edge is checked every two milliseconds.
The letters NBI appear several times on the drawing, Fig. 9-2. This signifies
a network break-in. During such an interval, the network break-in flip-flop is
read. When the network completes a job, the markers set the network break-in
flip-flop. When it is set, the system enters a network sequence, does whatever
work is required, and returns to the main program as directed by the job
index number.
If trouble occurs, all call-processing actions stop and a program is entered
for locating and switching out of service the unit in trouble. When needed,
other programs are entered which diagnose and pinpoint the source of trouble
and perform maintenance routines. The main program allocates time for these
jobs. Some may be performed hourly, some only once a day, and others on the
demand of the maintenance craftsman through the administration center.
Decision Orders and Nondecision Orders
Each instruction in the program is called an "order word"; it specifies what
to do and where to go to carry out the instruction. The order words fall into two
categories, decision and nondecision.
The decision orders specify two alternative actions: either (1), proceed along
a prescribed series of actions or (2) transfer to a new and different series of
actions. These orders always specify a read or match operation — read the
scanner, a flip-flop, or the barrier grid store; or match two binary words. The
decision orders' can be modified to specify a particular condition to be met,
such as "transfer if a 1 is read"; or "proceed along the present series if a is
read;" or vice versa. The order may also specify which of two transfer registers
(in the CC) should be used if a transfer condition results. The transfer register
specified contains the address of the first word in the new program series to be
232 The Flying Spot Store Chap. 9
used in the event of a transfer. The address of the new series is placed in the
transfer register upon entering the series initially.
Nondecision orders do not provide alternative actions; they simply specify a
work operation. A few typical examples are:
(1) Write a 1 or at a specified BGS address.
(2) Write a 1 or in a specified F/F.
(3) Read the BGS at specified address, and store the reading in a
specified F/F.
(4) Transfer to a new program address (no decision).
(5) Gate (transport) information from a specified F/F group to a
second F/F group.
(6) Regenerate the BGS at a specified address.
The amount of information contained in the order word is not the same for
all orders. Some orders are more complex than others and require more informa-
tion in the instruction part of the order; others require more address informa-
tion. For example, to address the BGS to a particular spot requires a fourteen-bit
address. But since the registers in the BGS are arranged in columns and grouped,
it is possible to modify the address part of the BGS orders and specify only
one-half the address in the order. Some BGS orders will therefore specify that
either the X or the Y half of the address be set up in the BGS address register
located in the CC (pre-set address) before beginning a series of operations. If,
for example, the system is working with an originating register, the X address
of the register may be preset in the central control BGS address register. The
orders which follow contain only the Y address of the spot or spots to be
worked on.
Some orders require two addresses in the "where to go" part. Gating informa-
tion from one flip-flop group to another, and from the BGS to a flip-flop, are
examples of multiple address orders. The source and termination of the flow
of information is specified.
By now you are no doubt wondering about the length of the word or instruc-
tion that carries all of this information. You may have the impression that the
words are of different lengths because they carry different amounts of informa-
tion to the system. In spite of such variations in the quantity of information
carried, however, all the order words are of the same length; each instruction
is a coded order word of nineteen bits.
Sec. 9.2 The System Program 233
There is a language difference between the ESS and its designers and main-
tenance people that must be overcome. While the ESS uses the binary number
language with ease, it would be cumbersome for you to talk about its functions
or to communicate directly with it, using its own language. Therefore, a coded
language of symbols, letters, and numbers is used to abbreviate our rather long
descriptions relating to system operations. This abbreviated language is changed
to a series of numbers. These are then translated to the binary language, and
finally put on FSS plates. There are a few special situations, however, that
require you to communicate with the system in the binary form. These are the
special tests started through the teletypewriter at the administration center.
The order word structure, and the conversion of a typical order from a
detailed description to the binary equivalent on the photographic plate, are
shown in Fig. 9-3. An order word is coded in four parts, and each part yields
the following combinations:
The A Code: 3 Bits = 8 Combinations
The B Code: 3 Bits= 8 Combinations
The C Code: 5 Bits= 32 Combinations
The D Code: 8 Bits = 256 Combinations
The A, B, C, and D codes of the order are related to specific system operations.
Coding the order in this way makes it easier to work with. The eight possible
combinations of the A code are used to form the following seven types of orders:
(1) Decision.
(2) Nondecision.
(3) Transfer.
(4) Set up transfer register 1 .
(5) Set up transfer register 2.
(6) Set up access register 0.
(7) Set up access register 1 .
(8) The eighth combination is not used.
The B code is used to modify decision orders. It may also specify action when
used alone or combined with the C code. The B code carries address information
when a full sixteen-bit address is necessary. Transfer orders and set-up orders
are examples of the types which require a sixteen-bit address.
234
The Flying Spot Store
Chap. 9
E C
4
E C
3
EC
2
EC
1
EC
P
A 2 A 1
AO
B 2
B 1
B
C4
C 3
C 2 C 1
C
D 7
D 6
D 5
D4
D 3
D2
D 1
DO
v
f
v J\ J\ ;\
J
Y
Y Y Y Y
5 BITS
3 BITS 3 BITS 5 BITS 8 BITS
ERROR
CORRECTION
PARITY
CHECK
BIT
ORDER CODE ;
1. INSTRUCTION PART -WHAT TO DO
2. ADDRESS PART-WHERE TO DO IT
DESCRIPTION OF A TYPICAL ORDER :
WRITE 1 IN THE BGS AT THE Y ADDRESS SPECIFIED BY THE
CONTENTS OF D6 TO DO AND THE ADDRESS GIVEN BY THE
CONTENTS OF THE BGS ADDRESS FLIP FLOP GROUP
ABBREVIATED ORDER DESCRIPTION :
WRITE I AT Y, X PRESET
SYMBOLIC ORDER :
W1Y
DECIMAL EQUIVALENT :
A=1, B = 7, C=1,D7=0, D6TO DO = 6 (SPECIFIED ADDRESS)
BINARY EQUIVALENT AS STORED ON FSS PHOTOGRAPHIC PLATES:
11110 10
FIG. 9-3. Order word structure.
i o
VG 903
Address or action information is carried by the C code. The D code always
has information which is, in a sense, an address. It may be the location of a
particular memory spot, or it may specify a particular flip-flop in a flip-flop
group. In many cases, the number specified in the D code identifies a single
lead that is gated to a common "read" flip-flop* by the order. The common
flip-flop is read to determine the state of the lead.
Order types, abbreviated order symbols, and coding are shown in Table 9-1
on pages 236, 237, and 238. There are 78 types of orders and about 65,000
words in the ESS program. In addition, storage space is provided for 16,000
translation words consisting of thirty-two bits each.
*A "read" flip-flop shows by its output the state of any of several input leads that may
be gated to it.
Sec. 9.2 The System Program 235
Now let us go back to Fig. 9-3 and the order word structure for a moment.
A parity-check bit and five error-correcting bits are attached to and recorded
with each nineteen-bit word. The parity check bit may be either a 1 or a 0, and its
state is dependent on the number of l's in the order word. The number of l's
plus the parity bit must always equal an even number. The CC parity check
circuits check each word for an even number of l's. If an odd number of l's
is detected, the system enters a wired error-correcting program and uses the
five error-correction bits to locate and correct the bit that is in error.
9 . 3 EQUIPMENT ARRANGEMENTS
The FSS and its associated rectifier units are mounted in five cabinets.
The FSS bays are designated through 6. The front and end bays have even
numbers; the odd-numbered bays are in the rear. The packages used in each
FSS are listed in Table 9-2 on page 239.
The rectifier units and power control circuits are mounted in the cabinets
designated FSP-0 and in the lower half of FSS-0. The power sources, circuits,
and controls are described in Section 9.6, Power.
9.3.1 Cabinet FSS-0, Front Bays (Fig. 9-4, page 240)
Let us begin the description of the bays with bay 2. The lower half
of bay 2 contains the X and Y integrating amplifiers and the digital-to-analog
converters. These plug-in chassis are locked to their mounting plates. The
locking levers are located adjacent to the handles. Interconnections to other
equipment are made through connectors on the backs of the chassis and the
mounting plates. Air for cooling enters the cabinets through adjustable grilles
at the bottom, and is vented out at the top.
The tops of bays 2 and 4 provide a chamber for the elements of the optical
system. Also, at the top of bay 2 are the shutter control relays. These relays are
operated from the administration center; they control the operation of the
shutter solenoids.
You can view the face of the cathode-ray tube through the eyepiece to the
left of the shutter control relays.
The lower half of bay 4 contains the packages that make up the address
registers and the comparator circuits. The address leads from the CC terminate
(The text is continued on page 240.)
236
The Flying Spot Store
TABLE 9-1. ORDER CODING
Chap. 9
Type of
Order
Order
Symbol
A
B
D7
Group 1
c
Group II
D
RY—
0-2, 4-6
004
BG Y Address
RX—
0-2, 4-6
005
BG X Address
EY—
0-2, 4-6
000
BG Y Address
Read
EX—
0-2, 4-6
001
BG X Address
the
CY—
0-2, 4-6
006
BG Y Address
BGS
CX—
0-2, 4-6
007
BG X Address
RYB—
0-2, 4-6
010
BG Y Address
RXB—
0-2, 4-6
011
BG X Address
EYB—
0-2, 4-6
002
BG Y Address
EXB—
0-2, 4-6
003
BG X Address
RP—
0-2, 4-6
012
170
RPC—
0-2, 4-6
012
171
Read a
Flip-flop
RFA—
0-2, 4-6
1
016
FA Number
RFF—
RTB—
0-2, 4-6
0-2, 4-6
1
1
012
012
FF Number
174
Read the
RS—
0-2, 4-6
1
013
Scanner
Read the
RSY—
0-2, 4-6
020
BG Y Address
Scanner
RSX—
0-2, 4-6
021
BG X Address
and the BGS
RSL—
0-2, 4-6
022
Next BG Address
MY—
0-2, 4-6
1
034
FG Number
Match
MX—
0-2, 4-6
1
035
FG Number
MB—
0-2, 4-6
1
036
FG Number
RYMFA—
1
3
BGY Address
FA Number
RTW—
1
7
—
012
FG Number
Non-Modifiable
RTWS—
1
7
—
013
FG Number
Decision
RYOS—
2
024
BG Y Address
RYIS—
2
025
BG Y Address
MXTMM—
1
7
004
FG Number
Table 9-1 continued on page 237
Table 9.1
Order Coding
TABLE 9-1. ORDER CODING {continued)
237
Type of
Order
Order
Symbol
A
B
D7
Group 1
c
Group II
D
Transfer
T—
TFG—
3
1
7
—
FSS X Address
005
FSS Y Address
FG Number
Write
in the
BGS
WOY—
WIY—
WOX—
WIX—
WOP
WIP
WOPC
WIPC
RGY—
RGX—
CYMP—
7
7
7
7
7
7
7
7
7
7
7
1
1
1
1
1
000
001
000
001
006
006
006
006
002
002
003
BG Y Address
BG Y Address
BG X Address
BG X Address
170
170
171
171
BG Y Address
BG X Address
BG Y Address
Write
in a
Flip-flop
WOFA—
WIFA—
WOFF—
WIFF—
WISK
WOTB
SMTM
7
7
7
7
7
7
7
1
1
1
006
006
006
006
006
006
006
FA Number
FA Number
FF Number
FF Number
174
174
175
Access
Register
Operations
RYFA—
RXFA—
RYFAS—
WFAY—
WFAX—
RPFAY—
RPFAX—
WFAPY—
WFAPX—
7
1
1
4
4
5
5
1
1
1
1
1
BG Y Address
BG X Address
004
BG Y Address
BG X Address
FA Number
FA Number
BG Y Address
FA Number
FA Number
FA Number
FA Number
FA Number
FA Number
Gate
G—
1
3
1
FG Number (To)
FG Number (From)
Table 9-1 continued on page 238
238
The Flying Spot Store
Chap. 9
TABLE 9-1 ORDER CODING {continued)
Type of
Order
Order
Symbol
A
B
D7
Group 1
C
Group II
D
ST1 —
4
T1 X Address
Tl Y Address
ST2—
5
—
—
T2 X Address
T2 Y Address
Set-up
SAO—
6
—
—
AO X Address
A0 Y Address
SA1 —
7
—
—
A1 X Address
Al Y Address
SY—
6
BG Y Address
SX—
6
1
BG X Address
Repeat
RPTS—
7
007
Number of Exec.
RPTD
7
1
007
Number of Exec.
ENS
7
1
006
177
STD
7
1
006
176
GBN
7
006
176
AYBG
7
006
172
AXBG
7
1
006
172
Miscellaneous
HBG—
2
Hamming FF No.
BG Y Address
HFA—
2
1
Hamming FF No.
FA Number
HR
7
006
173
RPW—
7
—
010
FG Number
RPWS—
7
—
011
FG Number
EXCH—
7
—
014
FG Number
GAIOS—
1 7
1
006
173
End of Table 9-1
Table 9-2
Packages Used in each FGS
239
TABLE 9-2. PACKAGES USED IN EACH FSS
F-Spec.
CPS*
Number
No.
Quantity
Name
F-52703
8
14
AND Gate
F-52704
28
8
OR Gate
F-52706
27
8
Buffer Gate
F-52702
37
26
Flip-Flop
F-52978
87
1
Marginal Voltage Rectifier
F-52707
157
16
Switching Servo Logic
F-52713
161
9
Blocking Oscillator
F-52709
162
1
Gate Generator B
F-52718
163
1
Gate Generator A
F-52972
164
2
Analog Servo Logic
F-5271 1
166
3
Timer
F-52974
169
1
Transfer Timer
F-52976
174
3
Gate Generator C
F-52975
175
1
Gate Generator D
F-52973
176
1
Transfer Monitor
F-5271 5
178
11
Input Buffer
F-5271 6
179
3
Pulse Monitor
F-52960
241
68
Information Sampler
F-52961
242
18
Position Monitor Amplifier
F-52962
243
1
Activity Monitor Amplifier
F-52964
245
87
PMT Voltage Divider
F-52965
246
87
PMT Stabilizer
F-52966
247
2
Stabilizer Pulse Generator
F-52971
248
1
Intensity Monitor Amplifier
*CPS means Circuit Package Schematic.
240
The Flying Spot Store
Chap. 9
-OPTICS CHAMBER
SHUTTER CONTROL
RELAYS
INTENSITY STABILIZER
INTEGRATING AMPLIFIERS
AND CONVERTERS
ADDRESS REGISTERS
AND COMPARITORS
FIG. 9-4. Flying spot store, front view.
here. A plastic door covers the lower half of this bay; it protects the packages
and causes the cooling air to flow up past the packages even when the metal
door is open. Test points in the register are brought out to the jacks in the
fourth row of packages. Voltages required by the circuits in the end cabinet
(bays 4, 5, and 6) are distributed through five plugs mounted above the pack-
ages. When you remove these jumper plugs, you disconnect these voltages
from the end cabinet only.
Sec. 9.3
Equipment Arrangements
241
CRT SUPPORT
CRT SHIELD
PLATE POSITIONING^
LEVER
INFORMATION
PLATE SLOTS
QUADRANTS
HAND]!
FIG. 9-5. Flying spot store, rear view.
SEQUENCE
CONTROL
CIRCUIT
PACKAGES
VG 905
9.3.2 Cabinet FSS-0, Rear Bays (Fig. 9-5)
Here you can see the rear of the rectifier units in the power cabinets.
The CRT assembly extends from the right side of FSS-0, bay 1, into power
cabinet FSP-0, bay 3. This CRT assembly is supported at its center of gravity
by a spring-loaded device on a track. This support allows the tube to be pivoted
and moved out of the cabinet when making a replacement. It also allows the
tube to be moved by the wobbulator. The wobbulator causes continuous tube
242 The Flying Spot Store Chap. 9
movement to reduce phosphor wear, and thus to extend tube life. The tube is
securely mounted in its shield, and the shield is clamped to the wobbulator
assembly at the faceplate end of the tube. Immediately below the CRT are the
deflection amplifiers and the blowers.
In the lower half of FSS-0, bay 1, is the high-voltage supply for the CRT,
and an additional rectifier unit.
The lower half of FSS-0, bay 3, contains marginal voltage checking trans-
formers. These are mounted on a gate to permit access to the wiring side of the
front chassis mounting plate and the terminal side of the transformers.
The lower half of FSS-0, bay 5, contains the packages, the filament trans-
formers, and the equipment used in the sequence control circuits. This equip-
ment is gate-mounted, and the gate has a plastic door. Test points are brought
out to the jacks in the upper left corner of the gate. Just to the left of this jack
panel is an emergency stop button. Similar red buttons are placed in other FSS
cabinets to permit you to shut down the FSS during an emergency. These
buttons open the major interlock circuit that removes primary power from the
FSP control circuit.
The top halves of FSS-0, bays 3 and 5, contain the optic chamber. At the
left of the plate slots are levers that position and lock the photographic plates
in the slides. They are shown in the locked position.
9.3.3 Cabinet FSS-0, Bay 6 [Fig. 9-6)
In the upper half of bay 6 are the photomultiplier channels. Figure
9-6 is a view of a partially equipped cabinet. The position monitor channels
are fully equipped and form a cross in the center of the bay. Altogether, 87
photomultipliers are needed to equip each FSS.
In the lower right corner is a meter used to adjust the position monitor level.
Just to the left and below the meter is the selector switch that connects the
meter to one of the position monitors. The selector switch can be operated
electrically by the push button adjacent to the switch position indicator, or it
can be operated manually. The switch on the right selects vertical position
monitors; The switch on the left selects horizontal position monitors. A remote
meter and two selector push buttons are mounted on the control panel in bay 0.
Sec. 9.3
Equipment Arrangements
243
Controls and test points are brought out to a panel on each information
sampler and each position monitor plug-in package. The packages are plugged
into the connectors at the ends of the package guides. Through these connec-
tions all power and all input and output signals enter and leave the packages.
Common signal test points are brought out to the jack panel in the lower
left corner. On the gate in the lower half of the bay are filament and marginal
voltage checking transformers, and associated fuses.
An emergency stop button is located in the left center of the cabinet.
INFORMATION SAMPLERS
VERTICAL POSITION
MONITORS
TEST POINTS
HORIZONTAL POSITION
MONITORS
MARGINAL VOLTAGE
TRANSFORMERS
FILAMENT
TRANSFORMERS
FSfSHKSSSi
POSITION MONITOR
LEVEL METER
FILAMENT
SUPPLY FUSES
FIG. 9-6. Flying spot store, end view.
244
The Flying Spot Store
Chap. 9
□ □□
^?
□ mm ;l
mtt mxog
• • •
XiOEF
•• •
• • • i
t
m
IN
♦ * f4 * $ i I i $ * I \ \ l i r
* « » © « i
FIG. 9-7. Flying spot store manual control and meter panels.
9.3.4 Cabinet FSS-0, Bay 0, Manual Control and Meter Panel (Fig. 9-7)
The first chassis (VTG MON) at the top of Fig. 9-7 contains the
voltage monitor circuits. The voltages derived from the dividers in this circuit
are sent to a monitor in the administration center. Controls at the right are
used to adjust the levels sent to the monitor.
The second chassis (CLK) contains a variable clock or pulse generator, and a
wobbulator monitor. The clock output is used internally to address the FSS
Sec. 9.3 Equipment Arrangements 245
during a scan mode of operation. The wobbulator monitor detects a failure in
the wobbulator mechanism. Should the mechanism fail, a teletypewriter mes-
sage notifies you of the failure.
The third chassis (MTR-B) contains controls and meters associated with the
deflection systems. It also has the meter which indicates the CRT beam current.
The fourth chassis (MTR-A) contains a remote control and a meter circuit
associated with the position monitors. The remaining controls on this chassis
and on the fifth (bottom) panel are used for special tests. These are described
in the circuit description, CD-1A005-01.
At the left of bay is a hinged shield that covers the chassis fasteners. An
interlock switch is opened when the shield is opened. This causes the control
relays to release and to remove the d-c potentials from the FSS.
In the lower right corner of the bottom panel is an emergency stop button.
9.4 APPARATUS ELEMENTS
9 . 4. 1 The Optics System
Precautions
In any work involving the optics system, the precautions listed below should
be observed at all times.
(1) If tests and observations indicate a need to open the optics chamber,
a BTL representative should be notified. He will arrange for making
any adjustments needed.
(2) The position of each lens and code plate has been adjusted to a point
of optimum operation. They are locked and cemented in this position.
Under no conditions should field adjustments of these elements be
attempted. The lenses should require no cleaning during the life of
the FSS.
(3) The optics elements are housed in a light-tight chamber. Its interior
metal parts are coated with a dull-finish black paint to reduce reflec-
tions. Any external light entering the chamber can seriously impair
the FSS operation. In sufficient quantities, in fact, such light can ruin
the photomultiplier tubes (PMT's).
(4) When cleaning the photographic plate tracks, be extremely careful
to follow the procedure outlined in Specification X-63954. These
246
The Flying Spot Store
INFORMATION
LENS N
CRT RASTER
SERVO CODE PLATE
Chap. 9
INFORMATION
-- PLATE
FIG. 9-8. Flying spot store multiple information channels.
HORIZONTAL SHUTTERS
OBJECTIVE LENSES ^
VERTICAL SHUTTERS „ I
\ I
, — FILM PLANE
, CONDENSER LENSES
I
PHOSPHOR SCREEN --
CATHODE RAY TUBE
o
o
D [_
I i
11 I n
n s
n s
n e
n e
n e
□ E
PHOTOMULTIPLIER
TUBES
FIG. 9-9. Flying spot store optics system elements.
Sec. 9.4
Apparatus Elements
247
tracks, in two of the quadrants, are adjacent to the vertical code
plates. If any of these plates are moved, even slightly, the FSS will
fail to operate.
The Elements of the Optical Channels
The elements of the optical channels are shown in Fig. 9-8. All the channels
have a common light source: the spot on the CRT phosphor screen. Each
objective lens produces an inverted reduced image of the CRT face on a photo-
graphic plate. Behind each image is a condensing lens and a photomultiplier
tube (PMT).
There are ten vertical and ten horizontal shutters in the channels, as shown
in Fig. 9-9. The vertical shutters are placed between the CRT and the objective
lenses. The horizontal shutters are placed between the objective lenses and the
photographic plates. The vertical shutters and the CRT are shown in Fig. 9-10.
The shutters are used to select a channel during the exposure of a plate. When
exposing a plate, the shutters are closed in all the channels except the selected
FIG. 9-10. Flying spot store CRT and vertical shutter assembly.
248
The Flying Spot Store
Chap. 9
channel. At all other times, all the shutters are open. Notice that there are no
shutters in the beam-positioning channels.
Program and translation information is stored on four 10-by-12.5-inch
glass photographic plates. There are seventeen storage areas on each plate,
as shown on Fig. 9-11 (and more clearly indicated on Fig. 9-13). Each storage
area is about 1.4 inches square. The code plates are about 2 inches square;
they are mounted individually in the form of a cross on the center axes of the
film plane. The arrangement is shown in Fig. 9-11 and Fig. 9-12. Fig. 9-11
also shows some of the condensing lenses.
Figure 9-12 shows the horizontal shutter and code plate assembly, with light
passing through an objective lens. This figure indicates how a channel is selected
by opening vertical and horizontal shutters.
When the light falls on a clear spot in the photographic plate, it passes
through to the condensing lens and the PMT. The condensing lens focuses, on
the face of the PMT, a spot of light of % inch diameter. This spot remains fixed
INFORMATION
PLATE
QUADRANT
CODE PLATES
QUADRANT
11
CONDENSER
LENS
QUADRANT
EZ
FIG. 9-11. Flying spot store lens and plate assembly.
y
Sec. 9.4
Apparatus Elements
249
on the PMT for any position of the spot on the CRT screen. Holding the spot
in a fixed position offsets any variations in the sensitivity at different points on
the PMT photocathode.
The photomultiplier assignments are shown in Fig. 9-13. Each position is
identified by a letter and a number. For example, the position designated A20
is the third bit of the A code in the order word; it is in the "zero" or even group
of channels. The position designated E21 is the third bit of the error-correction
information, in the "one" or odd group of channels. In the translation area,
quadrant IV, position T8 is the ninth bit in each half of a translation word.
It is extremely important that the electron beam must not be permitted to
remain on any spot in the phosphor for an extended period of time. The in-
tensity of the electron bombardment will shorten the life of the phosphor coating
or cause a burnt spot. Timers in the sequence control cause the beam to move
off of the information storage area if no change in spot position occurs for
about one millisecond.
INFORMATION PLATE
AREA
OPTICAL CHANNEL
PREPARED FOR -
EXPOSURE
VERTICAL POSITION
CODE PLATES
OBJECTIVE LENS
HORIZONTAL POSITION
CODE PLATES
SHUTTER SOLENOID
SHUTTER
YA CODE PLATE
XA CODE PLATE
FIG. 9-12. Horizontal shutter and code plate assembly.
250
The Flying Spot Store
Chap. 9
II
10
n 9
8
7
6
5
4
IE 3
2
I
B20
C41
D41
TO TS YPMS SPGI
A B C D E
FIG. 9-13. Flying spot store ph
W.
G H J
.... . VG 913
otomultiplier assignments.
In normal operation, some sections of the stored program are used more
frequently than others. This extra use causes the phosphor to age more rapidly
in those areas than in other areas, and results in a corresponding reduction in
light intensity. To offset this effect, and to increase the life span of the CRT
tube, its mounting is driven by a system of cams that keep it constantly in
motion. Since the locations of the information spots are fixed by the code
plates, reading and writing are not affected. The movement is in a plane per-
pendicular to the optical axis. The primary movement is a spiral with a period
of 1.3 minutes. A second cam displaces the primary spiral; this second cam
requires 63.4 minutes to complete its cycle. The two movements combined
produce a circular area with a diameter of about 0.3 inch, the equivalent of
approximately 16 spots. The use of any single address is distributed over
this area.
Sec. 9.4
Apparatus Elements
251
PHOTO-
CATHODE
LIGHT BEAM
REFERE
LI
SO
ERENCE r
IGHT
URCE
_ PRIMARY
ELECTRONS
_ FOCUS
ELECTRODE
SECONDARY
ELECTRONS
"•- DYNODE
FIG. 9-14. Photomultiplier tube, schematic diagram.
9.4.2 The Photomultiplier Tube
The photomultiplier tube (PMT) is an electron tube with a photo-
sensitive cathode that emits electrons when exposed to light. A simplified
schematic diagram of the PMT is shown in Fig. 9-14. The electrons emitted by
the cathode on the inner surface of the tube face are directed toward a series
of ten dynodes. The primary electrons from the cathode strike the first dynode
in the series, and release secondary electrons from it. The dynodes are formed
and mounted to focus the secondaries successively on the next dynode in the
string, and to block or deflect spurious electrons. As the electrons propagate
down the string, at each dynode they release more electrons than arrive. The
electrons released from the final dynode are collected by the anode. They are
greater in number than the initial primaries released from the cathode. This
increase results in a large current gain. The output signal, developed in the
anode load, is further amplified in associated sampler circuits.
The flow of electrons down the dynode string can be regulated by adjusting
the potentials applied to the dynodes. This characteristic is used to regulate the
gain of the tube and to compensate for aging. A gain control, connected to
dynodes 5 and 6, is used to vary the potential difference between these two
dynodes. A potential difference of about 150 volts exists between the remaining
dynodes in the string.
A standard light reference source is attached, off center, to the face of the
PMT. The light emitted from this cell is used as a reference to adjust the gain
of the PMT.
252
The Flying Spot Store
Chap. 9
9 . 5 METHOD OF OPERATION
The interconnections between the flying spot stores (FSS's) and the
central controls (CC's) are shown in Fig. 9-15. Operating orders are sent from
the CC through the stand-by transfer to either FSS-0 or FSS-1 . The active FSS
is determined by the system; it can also be selected manually through the
administration center.
9.5.1 Major Functional Units of the FSS (Fig. 9-16)
The major functional units of the FSS are shown in Fig. 9-16. The
orders from the CC enter the sequence control circuit. This circuit controls the
internal operations of the FSS. Also, it sends to the CC such control information
as "good read" (GR), "transfer complete" (TRC), and "fixed transfer complete"
(FTRC).
The addresses enter the address registers. Each register drives its servo, its
digital-to-analog converter (DAC), its integrating and adder amplifiers, and its
deflection amplifiers, to position the CRT electron beam.
The CRT generates a spot of light that is seen through the lenses and photo-
graphic plates by the PMT's in the information samplers. They feed program
and translation information to the CC. They also send control information to
17 TRANSLATION^
CHANNELS
25 PROGRAM
CHANNELS
32 ADDRESS
LEADS
CENTRAL CONTROL
FSS ORDER
AND
CONTROL
STAND -8V TRANSFER
_3 CONTROL
LEADS
GOOD READ
TRANSFER
COMPLETE
FTRC
6 ORDER
LEADS
ADVANCE
TRANSFER
REST
SCAN
EXPOSE
OPERATE
17 TRANSLATION
CHANNELS
25 PROGRAM
CHANNELS
32 ADDRESS
LEADS
FIG. 9-15. Flying spot store and central control interconnections.
Sec. 9.5
Method of Operation
CENTRAL
CONTROL
ADDRESS
REGISTER
AND
SERVO
SEQUENCE
CONTROL
CONTROL
MANUAL
CONTROL
X-ADDRESS
INTEGRATING
AND ADDER
AMPLIFIER
DEFLECTION
AMPLIFIER
i
INTENSITY
STABILIZER
ADDRESS
REGISTER
AND
SERVO
DEFLECTION
AMPLIFIER
INTEGRATING
AND ADDER
AMPLIFIER
PROGRAM
INFORMATION
SAMPLERS (50)
GOOD -READ
SAMPLER (1)
TRANSLATION
INFORMATION
SAMPLERS (17)
POSITION
MONITOR
SAMPLERS (18)
INTENSITY
MONITOR (1)
PROGRAM AND TRANSLATION INFORMATION
253
FIG. 9-16. Flying spot store block diagram.
the beam-positioning circuits and the sequence control. The number of samplers
required for each type of information is shown in Fig. 9-16.
Manual controls provide a means for operating the FSS during routine tests
or trouble maintenance.
9.5.2. Address and Beam-Positioning Circuits (Fig. 9-17)
The address and beam-positioning circuits convert the binary address
from the CC to a deflection voltage to position the CRT beam. Each address
specifies a spot on the photographic plates at which information is stored.
These spots are arranged in a checkerboard pattern, thus providing more
space between the dots than would be possible if they were in a sequential
order. The use of two groups of program information channels makes up for
the spots lost in the checkerboard pattern. The XO address bit is used to select
one of the two information groups. This arrangement provides a total of
65,536 storage spots on the photographic plates.
254
The Flying Spot Store
Chap. 9
ADDRESSES
FROM
CENTRAL <
ORDERS
ADVANCE
INPUT
BUFFER
X
DAC
DIGITAL
TO
ANALOG
CONVERTER
ADDER
AMPLIFIER
Y7 .
INPUT
BUFFER
Y
YO f
DEFLECTION
AMPLIFIER
INPUT
BUFFER
DUPLICATED FOR VERTICAL SYSTEM
9 POSITION
MONITOR
SAMPLERS __
I INTENSITY
MONITOR (I M)
'^-9 SERVO
CODE PLATES
FIG. 9-17. Flying spot store horizontal address and position circuits.
The addresses and orders that affect the beam position enter the address
register and sequence control through the input buffers. The register remembers
the address while the beam-deflection circuits position the beam to it.
The address register drives a high-speed, coarse-positioning, digital-to-analog
converter. It also drives a slow-speed, fine-positioning circuit. The slow-speed
circuit uses a servo system with a beam encoder. Nine servo code plates in each
axis, with their associated position monitors, are the heart of the beam encoder.
The position monitors see the light beams through the code plates when the
beam is on the information storage area of the CRT. If the beam is off of this
area, they see no light. Since the code plates are alternate clear and opaque bars,
the position monitors will see light only when the beam is positioned to pass
through a clear area. The code plate bars have a binary-type configuration.
This causes the position monitor outputs also to be of the same binary type.
This information is fed to the comparator (servo logic).
The servo code plates in the center of the film plate plane are shown in Fig.
9-18. This is an enlarged view of a portion of the plates. Here you see the
vertical (Y) and the horizontal (X) positioning plates. The intensity monitor
Sec. 9.5
Method of Operation
255
(IM) channel is included. Beams are shown positioned at two addresses, (A)
and (B). The addresses generated by the light beams falling in these areas are
also shown. You will note that when the light beam settles on an address, it is
bisected by an edge of an opaque bar on the XA and YA code plates. The XA
and YA position monitors (Fig. 9-17) feed this half-light output signal to the
comparator. The remaining position monitors see either full light or no light,
and they supply their companion circuits in the comparator with this informa-
tion. The comparator takes the beam location address, as seen through the
code plates, and compares it with the desired address from the register. The
result of the comparison is a drive signal to the integrating amplifier. If the
COMPLETE X3
CODE PLATE
BEAM ADDRESS
Y3Y2Y_[Y0YAX3X2XI^X0XA
A=0001 I 000 I I
B ■ 1 10 1110
1
t t
A B
FIG. 9-18. Flying spot store servo code plates.
T
AREA
LLUSTRATED
256
The Flying Spot Store
Chap. 9
beam is to the right of the address specified in the register, it is deflected to the
left. If it is to the left of the address, it is deflected to the right.
When the beam position address is identical to the register address, the beam
movement is stopped. It remains locked to this address until the address in the
register is changed. A new address from the CC, an advance or rest order from
the CC, or a time-out signal from the sequence control, will change the register
address.
The integrating amplifier compensates for various limitations in the elements
of the servo loop and deflection system. Its output is combined with the DAC
output in the adder amplifier. The balanced output of the adder amplifier is
changed to a deflection voltage in the deflection amplifier to position the CRT
beam.
The intensity monitor, IM, is mounted near the center of the optical channels
with the position monitors. It detects variations in light intensity, and supplies
a reference voltage to the comparator and intensity stabilizers (see Fig. 9-17).
Light beams in ideal positions are shown in (a) of Fig. 9-19. Here you see a
beam bisected by the edge of a dark bar on the YA code plate, and another
beam centered on a spot on the information plate. If the beam settles on an
area of aged phosphor, it may be mispositioned as shown in (b) of Fig. 9-19.
The intensity monitor reference voltage instantly causes the comparator to
LIGHT BEAM HALF-ON,
HALF-OFF EDGE;
(HALF-LIGHT CONDITION SATISFIED;
NORMAL PHOSPHOR)
DESIRED SPOT WITH LIGHT
BEAM CENTERED IN EXPOSED
AREA (INFORMATION CHANNEL
OUTPUT= 1)
ADJACENT SPOTS ON
INFORMATION PLATE
(a) IDEAL POSITION
LIGHT BEAM RAISED
TO PRODUCE NORMAL -
HALF-LIGHT INTENSITY
DESIRED SPOT PARTIALLY
ILLUMINATED (INFORMATION
CHANNEL OUTPUT = 0)
LIGHT BEAM INTENSITY
REDUCED DUE TO AGED
PHOSPHOR
(b) BEAM MISPOSITIONED
FIG. 9-19. The effect of low light intensity on beam positioning.
Sec. 9.5 Method of Operation 257
correct for this mispositioned beam effect, and the beams finally settle as shown
in (a) of Fig. 9-19.
The intensity stabilizers (see Fig. 9-17) also feed a reference voltage from the
IM. The stabilizer varies the electron beam intensity by changing the grid bias
potential of the CRT. In doing this, it varies the intensity of the light emitted
by the phosphor. When a change in light level occurs, the reference voltage
shifts. This shift is sensed by the stabilizer, which alters the grid bias to return
the light intensity to a specified level. The stabilizer response to a change in
light is fast enough to hold the level constant for the information samplers.
9.5.3 The Sequence Control
An active FSS has two fundamental operating modes: advance and
transfer. The sequence control circuits direct internal operations of the FSS in
these modes on orders from the CC.
A stand-by FSS can be in one of three operating modes : rest, scan, or expose.
The sequence control in the stand-by FSS directs its action in these modes on
orders from the CC.
CC Orders That Initiate Modes
The orders that initiate the modes in the FSS's are these:
(1) Advance (ADV). The CC sends this order to the active FSS when it wants
the next order in a series. No address accompanies this order.
(2) Transfer (TR). This order, with an address, transfers the FSS beam to the
first word of a new series of orders. The CC operations cease until the first
word is in its order word register (OWR).
(3) Rest (RST). This order deflects the CRT beam behind a shield, off of the
phosphor. The address register is sent to the rest address through the
operation of the sequence control.
(4) Scan (SC). A stand-by FSS, when given this order, will scan sequentially all
the addresses under control of its internal clock. This mode of operation is
used to ease the phosphor aging, and to exercise the FSS.
(5) Operate (OPR). A stand-by FSS may be in either a scan or a rest mode,
and it must be alerted before it is given an order to read. This order takes
the address register out of rest, and provides an initial drive to the deflection
258 The Flying Spot Store Chap. 9
system. In doing this, the beam is deflected to the storage area of the
phosphor so that the position monitors can determine the beam location.
(6) Expose (EXP). This order is sent to a stand-by FSS which is preparing photo-
graphic plates from the exposure address and plate verification unit. The
address of the spot, and the channel designation, accompany the order.
This order is also used when verifying the exposed plate information.
Control Signals Returned to the CC
Three control signals are returned to the CC from the FSS sequence control.
They are:
(1) "Good Read" (GR). This signal is derived from an information sampler
with an information plate containing all l's. The spots on this plate have
diameters that are somewhat smaller than the diameters of the spots on the
program and translation plates. If a is read in the "good read" channel,
it is assumed that errors exist in other channels as well. The CC acts to
remove the word in its OWR, and it blocks any action other than sending an
advance order to the FSS. Since the FSS internal advance is blocked on a "bad
read", its address registers cannot change, and the beam remains at the
address of the "bad read" word. Upon receiving the advance order from
the CC, the FSS rereads the word. Repeated "bad reads" at the same address
cause the FSS to time-out (1 millisecond), and to deflect its beam to the
rest position. The CC continues to send advance orders to the FSS, but fails
to receive program orders from the FSS. The CC continues this action for
100 milliseconds, after which an emergency alarm switch occurs. This
switch makes active the stand-by FSS, CC, and SD.
(2) "Transfer Complete" (TRC). This control signal notifies the CC that a
transfer has been completed and that the word at this specified location is
in the OWR of the CC. The time between receipt of the transfer order and
transmission of the TRC signal depends on the time required to settle the
FSS beam on the new address.
(3) "Fixed Transfer Complete" (FTRC). During certain tests and maintenance
routines, it is necessary to read a word in the stand-by FSS. This action is
started by the active units. Because the system has no record of the beam
location in the stand-by FSS, a maximum time (12.5 microseconds) is
allowed for the words from the stand-by FSS to enter the OWR in the CC.
The timing is done in the active FSS; the word is read from the stand-by FSS.
Sec. 9.5 Method of Operation 259
Additional Functions of the Sequence Control
Some additional functions of the sequence control are:
(1) The XO address bit is used to determine which group of information
samplers will sample the information at a specified address.
(2) A transfer order or an advance order generates a pulse that samples the
information in the information samplers. The output is sent to the CC.
(3) Timers in the sequence control circuit control the length of time that the
beam is permitted to remain on any address. If the beam remains on an
address for more than one millisecond, time-out occurs and the beam is
deflected to the rest position. This is done to extend the life of the phosphor.
(4) The sequence control circuits produce a rest-address signal from an internal
time-out or an order from the CC.
(5) A "good read" signal is produced by combining the output of the GR
information sampler with a delayed order pulse. The resultant is sent to
the CC.
(6) When the FSS is in the advance mode of operation, a GR will produce an
ADD signal to the address register. This results in the beam being deflected
to the next sequential address.
(7) Signals from the beam-positioning circuits are combined with the transfer
order. This produces a "transfer complete" signal when the positioning
circuits indicate that the beam is locked on the address.
(8) The sequence control circuit controls the address register advances on
transfer orders. After the first word is in the CC, the beam is deflected to
the next serial address without any additional orders from the CC. The
word at this address is read into the CC buffer register, and the beam is
deflected to the next address. It remains at this new address awaiting
further orders from the CC.
(9) Pulses from the clock in the stand-by FSS, bay 0, are combined with the
scan order to cause sequential addressing of the stand-by FSS. When this
occurs, the address registers are set to zero. Then they are advanced serially
to the address with the highest number. The registers are then sent to the
rest address for 12 milliseconds, after which the above operation is repeated.
This scan mode may be started through manual controls.
260 The Flying Spot Store Chap. 9
9 . 6 POWER
The d-c power for each FSS is supplied by thirteen plug-in rectifier units
in its associated power cabinets, FSP-0 (see Fig. 9-20). The a-c power for the
units is fed from the regulated 230-volt a-c buses as follows:
Bus A: FSP-0
, See Fig. 1-18
Bus B: FSP-1 '
A 48-volt source is required for control circuits in cabinets FSS-0 and FSP-0.
It is supplied from the central office battery as follows:
Bus A: FSP-0 and FSS-0 ] „ „ , ,„
_ _ . See Fig. 1-19
Bus B: FSP-1 and FSS-1 6
9.6.1 Power Controls
These circuits, in the top of FSP-o, bay 0, control the application of
a-c and d-c power to the FSS. Relays are used to turn on power in a sequence
that slowly brings the tube filaments up to operating temperature. The a-c
power is applied to the rectifiers in three groups to reduce load effects on the
a-c buses. Power is removed from the equipment in steps for the same reason.
Red and white indicator lamps show the state of the power control circuit
and the power alarms. The white lamps indicate closed interlocks, the presence
of input voltages, and the steps in the switching sequence. The red lamps
indicate open interlocks, the absence of input voltages, and rectifier and
filament alarms.
To start a turn-on sequence, the circuit breaker is closed and the start button
is operated. It takes eighty seconds for the filaments to be brought up to operat-
ing voltage. After an additional time delay of forty seconds, the first group of
rectifiers have 230 volts a-c switched to their inputs. The remaining two groups
of rectifiers are switched on at two-second intervals. The application of the d-c
power to the FSS can be delayed through the operation of the d-c output switch.
When this switch is in the test position, the d-c power is not applied to the FSS.
A ten-second time delay occurs after the switch is operated to the normal
position before d-c power is applied to the FSS.
Each rectifier has a high-low voltage alarm which gives a signal to the power
control circuit when the voltage is out of limits. These limits are +10% or
—25% of rated value. A rectifier alarm causes the d-c potentials to be removed
from the FSS.
Sec. 9.6
Power
261
* flpM«i r" i •»"%
g«» i
J
'C
-INTENSITY STABILIZER
CONTROL AND INDICATING
PANELS -o^
D
Sis
W © ©W Q
•"; !
Q
• nh* . M
FIG. 9-20. Flying spot store power bays.
There are two interlock circuits in the FSS. Opening the minor interlock
circuit removes the rectifier d-c output voltages from the FSS. Opening the
major interlock circuit removes both the a-c filament voltage and the d-c
voltages from the FSS. In either case, the shut-down occurs in a series of steps
to eliminate surges on the power buses. The major interlock switches are located
on the back doors of the power cabinets, FSS, bay 1, and on the gates in bays
3, 5, and 6. The minor interlock switches are located on the plastic doors in
262 The Flying Spot Store Chap. 9
bays 4, 5, and 6, on the deflection amplifier blowers, and on the hinged shields
in bays and 2.
When you shut down an FSS, always operate the stop button on the FSP
control panel, or the emergency stop button in one of the FSS bays. Never open
the circuit breaker on the FSS control panel to shut down an operating FSS.
Opening the circuit breaker on an operating FSS causes line surges that will
affect other ESS equipment.
9.6.2 Rectifier Units (Fig. 9-20)
These units supply regulated d-c voltages between 7.5 volts and
10,000 volts to the FSS. There are alarm circuits, test points, and controls on
each unit. The circuit description of each unit covers its operation and main-
tenance.
Each plug-in unit may be removed from its bay after the fasteners and con-
nections in the rear have been released. Always disconnect input voltages from
the FSP before working on a rectifier unit. Always check the unit to be certain
that no voltage exists before starting to work on it. This can be done with a
voltmeter at the front of each unit.
9 . 7 MAINTENANCE
Most of the FSS testing is done by the system. It makes four types of
programmed tests, namely: routine tests, diagnostic tests, marginal tests, and
demand tests. The FSS testing not done by the system, together with other
maintenance procedures, is covered in Specifications X-63954 and X-63941.
9.7.1 Routine Tests
Routine tests are used to detect the presence of trouble in either the
active or the stand-by FSS, and to request a diagnosis. These tests are per-
formed at various intervals, such as 100 milliseconds, one second, one-half hour,
or one hour. The following list contains a brief description of each routine test
and gives the frequency with which it is repeated:
(1) A check of the read-out from the active FSS by means of program
test words is made every 100 milliseconds.
(2) A check of the "bad read" counter for the active FSS is made every
100 milliseconds.
Sec. 9.7 Maintenance 263
(3) A test that matches program words in the active FSS with those in the
stand-by FSS at various addresses is repeated every second.
(4) A check of the read-out from the stand-by FSS by means of program
test words is made every second.
(5) A check of the read-out from the active or stand-by FSS by using
translation test words is repeated every second.
(6) A check of the ability of the stand-by FSS to rest, scan, advance, and
transfer is made every second.
(7) A check of the wobbulator points in the active and stand-by FSS's
is made every half-hour.
(8) A check of the active and stand-by voltage supplies is made every
half-hour.
(9) A check of the stand-by servo is repeated every hour.
(10) A check for dust on the photographic plates in the active and stand-by
FSS's is made every hour.
9.7.2 Diagnostic Tests
The diagnostic tests make a thorough check of the various func-
tional units in the stand-by FSS. These tests, which are performed whenever
needed, consist of readings taken at :
(1) scan points associated with strategic points within the circuits;
(2) voltage monitor points;
(3) appropriate addresses on the plates; or
(4) central control flip-flops.
Special circuit conditions, when needed to administer any of these tests, are
set up before taking a reading. Print-outs identify all the tests that fail. For
each listed message, the dictionary will specify the faulty package or packages
to be replaced. Also, it will give other instructions where needed.
9.7.3 Marginal Tests
Marginal tests, made every night, are preventive maintenance tests.
In each test, a positive or negative 60-cycle sine-wave voltage is superimposed
264 The Flying Spot Store Chap. 9
on the voltage normally applied to a specified point in a circuit. The circuit is
examined at 100-microsecond intervals to determine its response while the
sine-wave voltage is applied. There are 136 marginal voltage tests made on each
FSS every night. Each failure is recorded on a print-out that identifies the test
and the point that failed.
9.7.4 Demand Tesfs.
Demand tests can be requested by the maintenance man through the
teletypewriter. The maintenance dictionary gives the exact form of the input
messages and the corresponding answers from the system. Only the specified
information should be used, because arbitrary addresses may cause improper
operation.
These tests may include a particular routine test or diagnosis at the begin-
ning of a series or at an intermediate phase. A complete series of marginal
voltage tests may also be started with these tests. A teletypewriter print-out
gives the results of any demand test.
Chapter 10
The Central Control
The central control (CC) has been called the "brains" of the ESS. To qualify
for this title, it would have to include the stores that provide the necessary
memory elements. It would be more accurate, perhaps, to call the CC the
"central nervous system" of the ESS. For, either directly or indirectly, the
central control regulates the actions of all the components in the system. The
CC senses changes in the traffic demands, and directs the system to handle
these changes in a manner predetermined by the program in the flying spot
store (FSS).
The central control (CC) is primarily a logic machine. It is continually inter-
rogating the system, making decisions, and giving orders. The program writers
have actually made the decisions beforehand, basing them on all possible
conditions of the system. But from the system's point of view, the central
control is the boss.
Ordinarily, the system operates without human direction, even checking
itself for errors, faults, and weaknesses. Only when faults are detected, or when
changes in customer service occur, is outside help needed.
The CC coordinates and directs the handling of office traffic on a time-sharing
basis. During the progress of a call, the calling customer, and all the other
customers in the office, will have received some kind of attention from the
system many times. But, because the CC operates at such tremendous speed,
the customers are not aware of this. Each customer feels that he is getting
undivided attention.
10. 1 EQUIPMENT ARRANGEMENTS
The central control (CC) is one of the completely duplicated component
sections of the ESS. The duplicate CC's are designated CC-0 and CC-1; these
265
266
The Central Control
Chap. 10
mmn-
""- ..M
MBIiliUMl.
HllllHIIIIIIItllUirUlllfl:
llUillHII!IHi!li!!lllll!il
I IliiS
t '■ -
«J injjl;
J ' tillflilS
»■■■'■'.
r miinmnii»««iiw
» :iHiniH Hwrx
vimniyiumiMMUiiM :
1 umBBBISHBBUW" 7 '
FIG. lO-l. Central control, front view.
designations are marked on the outside of the cabinets in which the equipment
is installed.
Each CC is housed in four cabinets, as shown in Figs. lO-l and 10-2. Each
cabinet contains equipment mounted in two bays. One bay is hinged to permit
access to the inside of the cabinet. The other is fixed. The bays are numbered
from through 7, and the number of each bay is marked on the cabinet designa-
tion plate and at the bottom of its frame within the cabinet. The even-
numbered bays are hinged; the odd-numbered bays are fixed.
Sec. 10.1
Equipment Arrangements
267
FIG. 10-2. Central control, rear view.
r »ttUHII»IU»:
mat
fiS"* iron
gggj nan
itniS
fnim
.^■^aa
Except for the clock pulse power supply and the terminal strips, all the
CC equipment consists of apparatus assembled on mounting plates.
Most of the apparatus in the CC consists of printed-wiring boards, commonly
called "packages." Each mounting plate can hold twenty-eight of these pack-
ages. The packages are designated A through AF from left to right. All the
packages in the CC are of the narrow type shown at (a) in Fig. 1-9 of Chapter 1.
RECT. RECT. RECT.
+ 16C + I6D + 22B
ISOL. KEYS 8. TEST BLK
MEM REG 3,4
MEM REG 1,2
BGS ADD REG
H CK MEM
E CORR
I I
CC
JACK PANEL
TS I TS
RECT
+ 26B
RECT
+ 16E
TS TS TS TS
TS
RECT
+ 22C
RECT
-16B
RECT
+ 16F
ISOLATION KEYS
ISOLATION KEYS
MARG TEST RESIST
AC REG 1
FSS A REG
FSS A CONT
T CONN
3
RECT.
-SA
RECT.
-4.5A
RECT.
+8A
RECT.
+ 16K
RECT.
-M6J
RECT.
+ 22F
RECT.
+ I6M
RECT
-I6C
ISOLATION KEYS
ISOL. KEYS 8, TEST BLK
MARG TST RES
ALARM & +6.5A REG
TR REG 1
TR REG 2
OVF REG
BUS REG T
SEL REG
NOC REG
RC REG
2
• 1
CC
RECT.
+22H
RECT.
+ 16P
RECT.
+ 8C
ISOLATION KEYS
ISOL. KEYS t. TEST ELk"
ALARM L VOLTAGE REG
M SYS TMR
SC A MCH
I I
CC
3
1
RECT.
+ I6H
RECT.
+22D
ISOL. KEYS &TEST BLK
RPT ORD
SEQ CONT
FCRT SW TMR
R A REG
6
It
CC
FIG. 10-3. Central control equipment, front.
JACK PANEL
TS TS T S
TS
RECT
-4.5B
RECT
+ 26D
RECT
+ 16N
RECT
-5B
RECT
+ 2 2G
RECT
-16D
ISOLATION KEYS
MARG TEST RESIST
CLK PWR
CLK P AMP
C P CONT
BGS MCH
JACK PANEL
JACK PANEL
TS
TS
TS
T S
ts|ts|ts|ts
T S
TS
T S
T S
RECT
+ I6A
RECT
+ 16B
RECT
+ 26C
RECT
+ 22E
RECT
+ 16L
RECT
+ 26A
RECT
+ 22A
RECT
-16A
ISOLATION KEYS
ISOLATION KEYS
Y BUS
MARG TEST RESIST .
BFR REG
REG BUS T
PC IN
OWR IN
X BUS
OWR OUT
M ORD T
P CK
SDA TS REG
3
1
FIG. 10-4. Central control equipment, rear.
268
Sec. 10.1
Equipment Arrangements
269
Figure 10-3 shows the layout of the central control equipment for the even-
numbered bays; Fig. 10-4 shows the layout for the odd-numbered bays.
Abbreviations for the equipment unit functional designations are marked on the
right side of the bay frame opposite the equipment. Table 10-1 lists the titles
of these abbreviations.
TABLE 10-1 ABBREVIATIONS FOR EQUIPMENT FUNCTIONAL DESIGNATIONS
Abbreviations
Equipment Functional Designations
AC REG
Access Register 0; also,
Scanner Cable Driver
AC REG 1
Access Register 1
BFR REG
Buffer Register
BGS ADD REG,
BGS Address Register; also,
Add-1 BGS Address Register
BGS ANS
BGS Answer
BGS MCH
BGS Match
BGS ORD
BGS Order Routing
BUS REG T
Bus to Register Translator
cc
Central Control
CD MEM
CD Memory
CD T
C Translator and D
Translator
CLK P AMP
Clock Pulse Amplifier
C OWR
Changed Order Word Register
E CORR
Error Correction
EM ALM
Emergency Alarm
FCRT SW TMR
Fault-Checking Routine Transfer;
also, Test Circuit and Switch
Timer
FF RDG
Flip-Flop Reading
FSS A CONT
FSS Address Control
FSS A REG
FSS Address Register; also,
Add-1
G P CONT
Gating Pulse Control
H CK MEM
Hamming Check Memory and
Memory Flip-Flops
MCH
BGS MM Match
MEM REG 1, 2
Memory Registers 1 and 2
MEM REG 3, 4
Memory Registers 3 and 4
Abbreviations
M ORD T
M SYS TMR
MT
NOC REG
ORD MEM
OVF REG
OWR IN
OWR OUT
PC IN
P CK
PROG CKG
R A REG
RC REG
REG BUS T
RPT ORD
SC A MCH
SDA TS REG
Equipment Functional Designations
SEL REG
SEG
CONT
T
CONN
TR
REG 1
TR
REG 2
TR
R REG
X
BUS
Y
BUS
Miscellaneous Order Translator
Main System Timer
Manual Test and Step-by-Step
FSS Advance
Network and Office Concen-
trator Control Register
Order Memory
Overflow Register
Order Word Register Input
Order Word Register Output
Program Channels Input
Parity Checker
Program Checking
Return Address Register
Remote Concentrator Register
Register to Bus Translator
Repeat Order
Scanner Answer and Match
Signal Distributor Address Reg-
ister and Enable Scanner; also,
Distribution Network Trunk Se-
lectors A and B Registers.
Line Selector Register and
Concentrator
Sequence Control
Test Connector
Transfer Register 1 ; also Add-1
Transfer Register 2
Transfer Record Register
X Bus Access
Y Bus Access
270 The Central Control Chap. 10
10.2 METHOD OF OPERATION
The central control has four major functions:
(1) It translates program orders.
(2) It uses the translated information to prepare itself to carry out
the order.
(3) It controls all other system units as directed by the program.
(4) It makes decisions based on program orders and on answers from
other system units.
The central control (CC) controls all the other system units on a time-sharing
basis. It is primarily a logic circuit which translates the stored program orders
on a one-at-a time basis. A program is a set of coded orders or instructions
specifying exactly what the system must do at all times and under all possible
customer input situations. The program orders are stored in the flying spot
store (FSS).
An order can be divided into two parts: (1), what to do; and (2), where to do
it (the address). Progress through the program, order by order, is controlled by
a system clock whose cycle time is about 3 microseconds. When a program
order is passed from the FSS to the CC on the occurrence of a clock pulse, the
CC translates the order and prepares itself to carry out the order before the
next clock pulse. The next clock pulse causes the execution of the order, and
also causes the next order in the program to enter the CC; this sequence is
shown in Fig. 10-5. The order-by-order progression just described is altered for
decision orders, as will be discussed later.
There are two types of orders in the program: nondecision orders and decision
orders. A nondecision order can lead only to one order in the program. A
decision order can lead to one of two orders in the program.
An example of a nondecision order is: "Write a in the BGS at the Y-
address specified, X-address preset" (WOY). This order is straightforward and
requires no answer from the BGS. The BGS writes a at the address given.
An example of a decision order is: "Read and regenerate in the BGS at
the Y-address specified, X-address preset, and transfer if you read a 0" (RYO).
The decision comes about when the answer is returned to the CC from the BGS.
If the answer is a 1, the CC directs the FSS to send the next order in the program.
If the answer is a 0, the CC sends the FSS to the location of the address stored
in the transfer register, as explained in detail later.
Sec. 10.2
Method of Operation
271
TIME
I
2
3
ETC.
ACTION
ORDER A ENTERS CENTRAL CONTROL (CC)
ORDER A IS EXECUTED; ORDER B ENTERS CC
ORDER B IS EXECUTED; ORDER C ENTERS CC
ORDER C IS executed; ORDER D ENTERS CC
ETC. V G 1005
FIG. 10-5. ESS clock timing.
Besides the program order information stored in the FSS, there is stored
translation information. This information includes translations pertaining to
classes of service, directory numbers to equipment numbers, and trunk-base
numbers.
The CC circuits shown on Fig. 10-6 can be divided into two general groups:
(1), circuits functionally associated with other system units; and (2), internal
control circuits and registers. Both groups of circuits are described in subsections
10.2.1 through 10.2.8, which follow.
70 . 2 . J Circuits Associated with the Flying Spot Store (Fig. 10-7)
Addresses for the location of a particular piece of information stored
in the FSS are passed from the CC to the FSS. Program orders and translation
information are passed from the FSS to the CC. This communication between
the CC and the FSS is controlled by the circuits shown in Fig. 10-7.
When the system is first turned on, the FSS is directed to the location of the
first order that the system wants. This starts system operation. The first order
in the program is passed around the Buffer Register* (BFR) into the Order Word
Register (OWR). The second order is put into the BFR before the first clock
pulse. On the occurrence of the first clock pulse, the order in the OWR is exe-
cuted, the order in the BFR is passed to the OWR, and the flip-flops in the BFR
are reset. Between clock pulses, the order in the OWR is translated by the Order
Word Translator (OWT). The OWT is made up of the following translators
*A "register" is a group of memory elements functionally
related.
5
f
-5
-S
-c
3
1
o
£
272
Sec. 10.2 Method of Operation 273
shown on Fig. 10-6; bus to register, register to bus, miscellaneous order, and
the C and D translators. The OWT has about 300 output leads. These leads are
the gating leads within the CC, and some of them are made active to carry
out each order processed.
So far, this story is true for both decision and nondecision orders. And, as
long as nondecision orders are processed by the CC, the procedure for executing
them is as described above.
Now let's take decision orders. Transfers may be expected as a result of the
decision orders, "read and match," and the nondecision order, "transfer."
"Transfer," here, means a jump from the location of one program sequence in
the FSS to the start of another sequence. When one of the decision orders is
specified, the address or location of the new program sequence is stored in one
of the Transfer Registers before the decision order is executed.
When a decision order transfer condition is met, the next clock pulse for the
CC is called a Conditional Transfer Pulse (CTR). This pulse will be explained
fully in the following section.
Now let's discuss, with the help of Figs. 10-7 and 10-8, the progress of a
decision order through the CC, and the timing in the CC for a transfer. At time
0, Fig. 10-8, the decision order A enters the BFR. Since this is a decision order,
the address for the new program sequence location is already stored in a transfer
register. We'll call the first order in this new program sequence,"order P." At
time 1, order A is passed to the OWR, and the BFR flip-flops are reset. Before
the next clock pulse, order B enters the BFR. The OWR serves as an inspection
and correction station, as well as a temporary storage area for program order
and translation information from the FSS. Before the next clock pulse, order A
is translated by the Order Word Translator, OWT. At time 2, order A is exe-
cuted, order B enters the OWR, and the BFR is reset. Shortly after time 2, order
C enters the BFR. The order memory retains the pertinent information about the
decision until the next clock pulse. Before the next clock pulse, the answer for
the transfer condition imposed by order A is returned to the CC. The transfer
condition is met. The next clock pulse, at time 3, is called the Conditional
Transfer Pulse, CTR. The transfer stops the clock and causes the following
actions:
(1) The address of order P is gated through the FSS address control to
the FSS and at the same time to the FSS address register.
(2) A transfer signal is sent to the FSS via the FSS control in the stand-by
transfer.
274
The Central Control
Chap. 10
FLYING
SPOT
STORE
BUFFER
REGISTER
FSS
ADDRESS
REGISTER
ADD
1
H
FSS
CONTROL
IN STANDBY
TRANSFER
ORDER
WORD
REGISTER
RETURN
ADDRESS
REGISTER
FSS ADDRESS
CONTROL
ORDER
WORD
TRANSLATOR
TRANSFER
REGISTER
2
ACCESS
REG
ACCESS
REG 1
TRANSFER
REGISTER
ADD
1
FIG. 10-7. Central control circuits associated with the flying spot store.
BUS
(3) The address for order B, that was stored in the FSS address register, is
gated to the return address register. This allows the system to go back
to order B after the transfer, if it wants to do so.
(4) The BFR and the OWR are cleared to accept the new orders, and
order P will be put right into the OWR, and order Q into the BFR.
(5) The order memory is reset.
(6) The transfer is reported to the sequence control.
At time 3+ , the CC receives a "transfer complete" (TRC) signal from the
FSS. To the CC, the TRC means that the FSS has sent order P to the CC. Before
the next clock pulse in the CC, which will execute order P, order Q is sent from
the FSS to the BFR. One cycle time (3 microseconds) after the TRC, the CC
generates its next gating pulse. Order P is executed.
One very important fact to remember is — The FSS address register always
contains the address of the order in the OWR. This is how the system always
knows where it is in the program.
On a direct transfer (a nondecision order to transfer), the timing in the CC
is the same as previously explained for conditional transfers of decision orders,
except that the transfer starts with the execution of the order. There is a differ-
ence in the circuit operation of the return address register. An EPO (execute
present order) clock pulse executes all orders. On direct transfer orders, EPO
activates the "add 1" circuit associated with the return address register. This
Sec. 10.2
Method of Operation
275
CYCLE
TIME
_ ANSWER FROM
' DECISION ORDER
TIME
ABOUT 3 CYCLE TIMES
L CYCLE
TIME
3t
T
TIME ACTION
ORDER A ENTERS BUFFER REGISTER (BFR)
1 ORDER A ENTERS OWR; ORDER B ENTERS BFR
2 ORDER A EXECUTED; ORDER B IN ORDER WORD REGISTER (OWR);
ORDER C ENTERS BFR
3 STOPS CLOCK; STARTS TRANSFER TO ORDER P
3+ TRANSFER COMPLETE FROM FSS; ORDER P IN OWR:
ORDER Q IN BFR; CLOCK STARTS
4 ORDER P EXECUTED; ORDER Q IN OWR VG
FIG. 10-8. ESS clock timing for transfers.
adds 1 to the Y part of the address coming from the FSS address register to the
return address register.
Very often the system needs translation information to complete calls. The
CC handles translation information somewhat differently from program orders.
As you probably know from reading a previous chapter, sixteen channels of the
FSS are reserved for translation information. All translation words are passed
from the FSS via the translation channel inputs directly into the OWR. They
are then gated over the BUS to an access register. Translation words require
two readings by the FSS; so it passes two words of sixteen bits each to the CC.
The first sixteen-bit word is stored in access register and the second in access
register 1 . They are then used as required by the program.
Parity for translation words is checked for all thirty-two bits, by examining
the first sixteen bits and then the next sixteen bits. This parity check* is good
if the number of l's in the word is even; it fails if the number of l's is odd. If
over-all parity is good, the address in the return address register is gated to the
FSS, and the system goes back to the original program. If parity fails on the
*A parity check determines whether a given word contains an even number or an odd
number of l's.
276
The Central Control
Chap. 10
over-all word, the address previously stored in the transfer register is gated to
the FSS, and a special program is used to correct the translation word.
One other very important signal from the FSS to the CC is called the GOOD
READ bit. This bit arrives in the CC shortly after the order word is received.
It is in the owr that the CC determines whether or not it has received a GOOD
READ from the FSS. If the bit indicates a GOOD READ, the order word is
processed. If the bit does not indicate a GOOD READ, the CC does not process
the order, but tells the FSS to read that same spot again. The GOOD READ
bit is ignored for translation words.
70 . 2 . 2 Decision-Making Circuits [Fig. 10-9)
When the order-by-order progression through the program is altered,
the decision-making circuits start the change. The clock pulse is amplified in
the CC and is passed to the gating pulse control circuit. This circuit, governed
by input information from the other circuits on Fig. 10-9, determines the next
kind of gating pulse for the CC. There are three kinds of gating pulse outputs
from the gating pulse control. They are:
(1) EPO (execute present order)— activates gating leads to execute the
order in the OWR (order word register.) This is the pulse most often
used in the CC.
(2) CTR (conditional transfer)— activates gating leads to cause a transfer
to a new program sequence in the FSS.
BGS
ANSWERS
SCANNER
ANSWERS
PARALLEL
MATCHER
ORDER
MEMORY
FLIP-
FLOP
READ
PARITY FAILURE, PARITY
CHECK AND ERROR
CORRECTION MATCH
MATCHES
BGS
ANSWER
SCANNER
ANSWER
FSS
ORDERS
BGS
ORDERS
BUS
i r
GATING PULSE CONTROL
) ) J
EPO CTR CKF
FIG. 10-9. Decision-making elements.
CLOCK
Sec. 10.2 Method of Operation 111
(3) CKF (check failure)— activates gating leads to start the system in a
fault-checking routine for locating trouble, or to start the error cor-
rection program. This is the pulse least often used in the CC.
The gating pulse control is made up of three groups of AND gates. The AND
gate output leads are connected by group to one of three OR gates. One OR
gate output lead, when active, transmits an EPO; another OR gate, the CTR;
and the last OR gate, a CKF output pulse. Since only one AND gate will be
active at any one time, the CC gets only one pulse.
The following circuits match the information of one CC against the same
information in the other CC:
(1) The BUS match circuit.
(2) The BGS order match circuit.
(3) The FSS order match circuit.
(4) The parity check match circuit.
(5) The error correction match circuit.
A mismatch in any one of these circuits causes a CKF in both the CC's
and starts the fault-checking routine to find out which CC caused the trouble.
A mismatch in either of the following two match circuits causes a CKF output
pulse:
(1) Scanner answers (one scanner against the other on test points only).
(2) BGS answers (one BGS against its stand-by).
A mismatch in either of these circuits also causes a transfer to the fault-
checking routine to determine which unit is at fault.
A parity failure in both the CC's (an odd number of 1's in the order word)
makes the gating pulse control put out a CKF, but this CKF starts error-cor-
rection action by both the CC's.
There are five more circuits shown on Figure 10-9, namely:
(1) The order memory circuit.
(2) The BGS answer circuit.
(3) The scanner answer circuit.
(4) The parallel matcher circuit.
(5) The flip-flop read circuit.
278 The Central Control Chap. 10
These circuits pass information to the gating pulse control which causes its
output pulse to be either a CTR or an EPO. The order memory stores order
information required to determine the next output pulse from the gating pulse
control. For example, here is an order previously mentioned: RYO, "read the
BGS at the Y address specified, and transfer if a 0." This order asks the BGS,
"Is this particular memory spot a or a 1?" It (the order) also tells the CC,
"if the answer is a 0, transfer to a new program sequence in the FSS." So the
order memory remembers for the CC: (1), that the question was asked of the
BGS; (2), to transfer, if the answer from the BGS is a 0; and (3), what transfer
register should be gated to the FSS.
If the answer from the BGS is a 1 , the next output of the gating pulse control
is an EPO. The EPO executes the order that is in the OWR. If the answer from
the BGS is a 0, the gating pulse control sends a CTR through the CC.
The BGS answer circuit, the scanner answer circuit, the parallel matcher
circuit, and the flip-flop read circuit, all help the gating pulse control to make
its decisions. The BGS answers and scanner answers are answers received by
the CC during the time between the execution of an order and the next clock
pulse. The parallel matcher circuit matches flip-flop groups against one another.
The flip-flop read circuit sends answers after reading miscellaneous flip-flops
in the CC. The order that uses these circuits specifies a transfer condition. If
the transfer condition is met, the next gating pulse will be a CTR. If the trans-
fer condition is not met, the next gating pulse is an EPO.
70 . 2 . 3 Parity-Check Circuits and Error-Correction Circuits (Fig. 10-10)
These circuits were partly covered in the preceding section where we
talked about what they did. Now, we'll discuss how they do it.
The order in the order word register is checked for parity (an even number
of l's in the order word). If the check reveals a parity failure (PF) by both the
CC's, one of two paths may be taken, depending upon the order previously
executed by the CC.
If the previous order was a decision order and the transfer condition was met,
the gating pulse control's next output pulse is a CTR. The CTR causes the
order in the OWR to be discarded, and its FSS address is stored in the return
address register. The FSS transfers to the new address sent by the CC, and the
CC follows the new program sequence.
Sec. 10.2
Method of Operation
ORDER WORD'
MATCH
ORDER WORD
SEQUENCE
F SS
CONTROL
REGISTER
CONTROL
.
.
ERROR
CORRECTION
CIRCUIT
PARITY
CHECK
CIRCUIT
GATING
PULSE
CONTROL
\ \
PF PG
EPO CTR CKF
279
FIG. 10-10. Parity-check circuits and error-correction circuits
If the previous order in the OWR was a nondecision order, or a decision
order resulting in no transfer, the parity failure causes a CKF in the CC, and
the CKF starts the error correction circuit in each CC to correct the order word.
After the word is corrected, a parity good (PG) signal is forced from the
parity check circuit, and an EPO is generated by the gating pulse control. The
sequence control stops all normal system action of the CC until the error cor-
rection is completed. It also stops any orders to the FSS control circuit.
When a parity check indicates PG from one CC, and PF from the other CC,
the gating pulse control sends out a CKF. This CKF starts the fault-checking
routine to determine which CC is at fault. If the active CC checks faulty, it is
put in the stand-by state.
10 . 2 . 4 Internal Flip-Flop Groups of the Central Control (Fig. 10-11)
These are the storage groups or registers within the CC. Some have
specific uses and others store information that will be used later. Also shown
in Fig. 10-11 is the BUS. Before discussing the registers, let's talk about the
BUS. The BUS is an electronic switching device for interconnecting two or more
equipment elements over a relatively large number of leads. It is similar to
"connectors" in electromechanical systems. It may also be compared to a
highway with many exits and entrances. You can get on the highway if its
entrance gate is open. You can get off, similarly, if its exit gate is open. In the
CC, the BUS is the highway. The internal and external flip-flop groups are the
entrances and exits. Some have two-way access. Information is transported
over the highway (BUS) by opening entrance gates one at a time to get the
information to an exit, and opening an exit gate at the same time.
280
The Central Control
Chap. 10
ADD
I
BGX I BGY
SCANNER -
FLIP-FLOP
READ
BGS
ACCESS
ACCESS t
OVERFLOW
PARALLEL
MATCHER
MEMORY
& MATCH
BUS
MEMORY 1
MEMORY 2
MEMORY 3
The BGS ADDRESS REGISTER is
used to store addresses for the BGS.
The X and Y halves of the register
store the corresponding parts of the
address. The "add 1" circuit is used
to add 1 to either the X or Y half of
the address. In orders for the BGS,
like RYO, the Y part of the BGS ad-
dress is given in the order. The X
part of the address was previously
put into the X half of the BGS
ADDRESS REGISTER by some previ-
ous order. In programming, this is
called presetting an address or part
of an address.
The ACCESS REGISTERS (0 and
1) are the most widely used registers
shown on Fig. 10-11. Translation
word information is always put into
an access register from the OWR.
And, since two readings of sixteen
bits each are always made, both
access registers are always used.
These registers have the following features that no other register in the
CC has:
The access registers are used to convert serial information into
parallel information, and vice versa. For example, the BGS sends to
the CC one bit at a time, which is stored in an access register. When
the CC has all the information stored in the access registers, it takes
the information out of the access registers all at once.
The CC can change one bit of information in an access register without
involving or affecting any of the other fifteen bits.
Both access registers are also used for shuffling information to other registers
in the CC via the BUS. For example, addresses for network points and for
trunks assigned to the SD (signal distributor) output points are set up in the
access registers, and then gated to the appropriate unit register. The scanner
addresses are always sent from ACCESS REGISTER 0.
MEMORY 4
FIG. 10-11. vc
Internal flip-flop groups or registers.
(1)
(2)
Sec. 10.2 Method of Operation 281
The OVERFLOW REGISTER, as its name implies, is used when the number
of bits of information for some other register exceeds the capacity of that
register. The overflow register is also used by the CC as a miscellaneous register.
The MEMORY REGISTERS (1,2, 3, and 4) are general storage registers for the
use of the programmer. Memory registers 1 and 2 can each store sixteen bits
of information. Memory registers 3 and 4 hold eight bits each.
The MEMORY AND MATCH REGISTER is used as a general storage register
for sixteen bits of information. It is also used to store information that will be
used by the parallel matcher to match it against another register to find out
whether both registers contain the same information. For example, on an
abandoned call that has progressed as far as ringing, the system starts to release
the connection. It gets to the ringing trunk connection on the network, and then
it doesn't know whether this is just a ringing connection or a talking path. So
the system puts the network address of the ringing trunk into the memory and
match register. The system then matches the network address of this ringing
trunk against the addresses of the ringing trunks in all the ringing registers.
If the system gets a match, it knows that the ringing trunk was not being used
as a talking path. The system then releases the ringing trunk and makes the
ringing register idle.
The FLIP-FLOP READING circuit allows the system to read information in
any flip-flop of the access registers or in some miscellaneous flip-flops of the CC.
To carry out its functions, the system must often find out the state of a particular
flip-flop or group of flip-flops. For example, suppose that the system gives an
order to a network. When the network finishes its task, it sends an answer to
the CC which puts information into the "operation ended" flip-flop. Every so
often the program tells the CC to read that flip-flop. When it is in one state,
the system knows that the network has completed its task. When it is in its
other state, the flip-flop tells the system that the network hasn't finished its task.
10 . 2 . 5 External Unit Registers within the Central Control [Fig. 10-12)
All these registers store information for the units with which they are
associated. Since information is gated to these circuits over the BUS in the CC,
it takes at least two program orders to fill these registers. Information is then
sent to the unit with which the register is associated. Some of these registers
send their information through the stand-by transfer to the other units. The
282
The Central Control
Chap. 10
t ANI - A NETWORK IDENTIFIER
BNI- B NETWORK IDENTIFIER
. SANI - STANDBY A NETWORK IDENTIFIER
SBNI -STANDBY B NETWORK IDENTIFIER
TLIMD -TRUNK LEVEL IDENT. & MATCH PET .
LSI - LINE SELECTOR IDENTIFIER
^TLIMD-STANDBY TRUNK LEVEL IDENT8. MAT. PE T.
SLSI - STANDBY LINE SELECTOR IDENTIFIER
BUS
FLIP-
FLOP
READ
L
N C
ATS
CRS
L S
TONE
SYNC
NET
RESPONSE
STAND
-BY
TRANS
-FER
DISTRIBUTION
MARKER
CONCENTRATION
MARKER
SIGNAL
DISTRIBUTOR
DISTRIBUTION
MARKER 0/1
(. CONCENTRATION
MARKER 0/1
TONE SUPPLY
MEMORY
MARKERS
(DIST AND CONC)
SD - SIGNAL DISTRIBUTOR
NC - NETWORK CONTROL
ATS - A TRUNK SELECTOR
BTS - B TRUNK SELECTOR
CRS - CONCENTRATOR RELEASE SELECTOR
LS - LINE SELECTOR vgk
FIG. 10-12. External unit registers within the central control.
stand-by transfer, as mentioned previously, sets up transfer paths between the
active and stand-by CC, and the active and stand-by markers and SD's.
The SD (signal distributor) REGISTER sends addresses and enable pulses to
the signal distributor.
The NC (network control) REGISTER sends orders (connect, release, trace,
etc.) to the markers.
Sec. 10.2 Method of Operation 283
The ATS and BTS ("A" trunk selector and "B" trunk selector) REGISTERS
send addresses to the markers for making connections to the A or B side of
the network.
The CRS (concentrator release selector) REGISTER sends addresses for con-
nections to be released at the concentration network.
The LS (line selector) REGISTER sends addresses for connections to be set up
at the concentration network.
The NETWORK RESPONSE circuit accepts signals from the markers. For
example, the system gives a network a task via the CC. The CC then goes on
with other office business. When the network finishes the task, it sends back a
signal called "operation ended" to the network response circuit in the CC.
Every so often the program tells the CC to read the flip-flop that receives the
"operation ended" signal. Thus the system learns whether the network has
finished its task. The marker also returns a signal to the CC that tells what the
result was — "busy," "successful," or "trouble." These answers also go to the
network response circuit. Again the system determines the next move by reading
through the flip-flop reading circuit the answers returned by the marker.
The TONE SYNCHRONIZATION circuit receives from the tone supply
memory (in the stand-by transfer), signals that tell it there is a tone being sent
out and what that tone is. The CC has access to this information via the flip-flop
reading circuit.
The eight lines with the arrows pointing to the BUS represent groups of leads
coming from the markers. When an order and address are sent to a marker,
the marker returns the same address to the CC on one group of leads. If the
system wants to match an address sent to the marker with the address returned
from the marker, it can do so. The reason for these groups of leads coming right
into the BUS in the CC is that the BUS provides access to other registers for this
information, if it is necessary.
10 . 2 . 6 Repeat-Order Circuits (Fig. 70-73)
A "repeat" order in the program tells the CC to execute the next
order a certain number of times. The next order specifies what to do and the first
location for where to do it. The repeat-order circuits in the CC take over and,
in a sense, manufacture orders by modifying the address for the repetition.
The maximum number of repeats that can be specified on any individual
order is 32.
284
The Central Control
Chap. 10
ORDEF
WORD ■
ORDER WORD
REGISTER
ADD 1
C AND D
ORDER WORD
TRANSLATOR
F SS
CONTROL
REREAT
ORDER
CIRCUIT
FIG. 10-13. Repeat-order circuits.
When a "repeat" order enters the order word register and is translated by
the order word translator, the repeat order circuit is alerted so that the following
order will be executed a certain number of times. A counter is set to indicate
the number of repeats. After the next order is executed, the FSS control receives
no more orders for the FSS. The counter is reduced by one; the ADD 1 C & D
circuit changes the address part of the order in the order word register; and the
order in the OWR is executed. This pattern is followed until the counter runs
out or a decision order transfer condition is met.
Let's assume that the system must write twelve l's in a BGS register. The
program specifies first, a "repeat" order that the next order be repeated twelve
times. The next order tells the CC to have the BGS write a 1 at the location
specified by the Y-part of the address, with the X-part preset. The repeat-order
circuits take over after the first order is executed. They follow the pattern
explained previously until the twelve l's are written. Then, the next clock pulse
causes a transfer to the next program order.
10 . 2 . 7 Circuits Associated with the Scanner (Fig. 70-74)
When the system program calls for communication between the CC
and the scanner, the circuits shown on Fig. 10-14 control this exchange of infor-
mation. The scanner is a little slower in operation than the CC, and two types of
program orders are used to compensate for the difference in speeds. One type is
an "enable scanner" order which prepares the scanner for readings by the CC.
This order is used every time the Y-part of the scanner address is changed. The
second type, a "read" order, tells the CC to read the scanner's answer for the
condition of the line it just looked at.
Sec. 10.2
Method of Operation
285
EPO-
CTR-
GATING
PULSE
CONTROL
ACCESS
REGISTER
ADDRESS >
SCANNER
ANSWER
AND MATCH
ENS
FLIP-FLOP
ORDER WORD
TRANSLATOR
RE
AD
>
> SCANNERS
FIG. 10-14.
VG 10t4
Circuits associated with the scanner.
Address information for the scanners is always sent from ACCESS REGISTER
(A0). The enable scanner lead is activated by the OWT for the scanner.
The scanner is continually inspecting lines and returning answers to the CC.
All these answers go to the SCANNER ANSWER AND MATCH circuit. This
circuit stores scanner answers for the CC. It also matches answers from the two
circuits when matching is called for. The matched answers are sent to the
FLIP-FLOP READ CIRCUIT, where they can be read by the CC.
"Read scanner" orders tell the CC when to use these scanner answers. De-
pending upon the answer (0 or 1) the gating pulse control puts out an EPO
or a CTR.
70 . 2 . 8 Circuits that Control BGS Operation [Fig. 70-75)
When program orders call for communication between the CC and
the BGS's, the circuits shown on Fig. 10-15 come into play. As mentioned in
Chapter 8, there are four BGS's used in the ESS. The ESS requires two working
stores at all times. The other two are used as stand-by units. From now on we
will talk about the two active BGS's. Since two stores are always active, we must
have a way of directing them singly or both at once.
Let's start with both BGS's receiving orders from the CC and both returning
answers to the CC as directed by the program. This is called "multi-tube mode"
of operation. In multi-tube mode, the program may specify either of two types
of decision orders for the BGS's— skip decisions or disjoin decisions. The CC
recognizes a skip or disjoin order by the transfer register specified in the order
286
The Central Control
Chap. 10
EPO -•—
GATINC
ORDER
ORDER
WORD
CTR -•—
CONTROL
MEMORY
TRANSLATOR
BGS
ANSWERS
BGS
ANSWER
MATCH
TUBE
CONTROL
READ-WRITE
CONTROL
BARRIER
GRID
AO
BUS
Al
BGS
REGISTER
STAND-BY TRANSFER
T"
BGO
1
BG1
1
BG2
\
BG3
VG 1015
FIG. 10-15. Circuits associated with the barrier grid store.
word. Skip decision transfers specify transfer register 1, and tell the CC to
transfer when all BGS readings meet the transfer condition. Disjoin decision
transfers specify transfer register 2, and tell the CC to transfer if one or more
BGS readings meet the transfer condition. A disjoin decision transfer always
puts the system into the single-tube mode of operation.
The transfer registers are shown on Fig. 10-7 and explained in subsection
10.2.1.
Some of the circuits shown in Fig. 10-15 have already been described in other
sections of this chapter. We will discuss them again here, however, in regard to
their relations with the BGS's.
Let's assume that we have a disjoin decision order RY02 ("read and regener-
ate the BGS at the Y-address specified, the X-address preset; transfer if a to
the address stored in transfer register 2") in the order word register. The order
word translator translates the "what to do" part of the order. It activates leads
in the CC that will execute the order on the next clock pulse. The OWT sends
to the order memory the following pertinent order information:
(1) Read the BGS's.
(2) Transfer if the answer from one or more BGS's is a 0.
(3) Transfer to the address stored in transfer register 2.
Sec. 10.2 Method of Operation 287
The order memory stores this information for use by the gating pulse control
when the answers are returned by the BGS. The OWT tells the BGS read-write
control to read the BGS. The tube control circuit tells the BGS read-write control
to read all active tubes; so the BGS read-write control sends the order to all
tubes via the stand-by transfer. The order word translator puts the Y-part of the
address on the BUS, and the X-part of the address is gated out of the BGS
address register onto the BUS. The BUS is directly connected to the BGS's, and
on the next clock pulse the order is executed. The BGS's return their answers
to the BGS answer circuit, which stores these answers. On a disjoin decision
order if one BGS answer is a 0, the tube control circuit is signalled. It then tells
the read-write control to work only in that tube (single tube mode).
Again the access registers (A0 and Al) are used when the system wants to
take one bit of information at a time from the BGS, store it in an access register,
and then read it out all at once. It (the system) can also put information into
the access registers all at once and send that information bit-by-bit to the BGS.
10 . 3 POWER
The primary power of the central control is 230 volts, 60 cycles. Power
bus A supplies CC-0; power bus B supplies CC-1. Each central control is pro-
tected by two 5-ampere and two 9-ampere circuit breakers in the power distri-
bution cabinet (one per cabinet).
Bulk rectifiers, 37 in each central control, provide filtered d-c voltages of
+ 26, +22, +16, +8, —4.5, —5, and —16 volts to the central control circuits.
You can see the arrangement of this equipment in Figs. 10-1, 10-2, 10-3, and
10-4. The rectifiers are of two types: J-86287A, LI , for voltages from to 10 volts,
and J-86287A, L2, for voltages from 1 1 to 26 volts. In each case the rectifier is
adjusted to its specified voltage. This voltage is marked on the designation strip.
These rectifiers are pictured in Fig. 5-20. Both types look exactly alike except
for marking. They are plug-in units, secured to the mounting plate with quarter-
turn fasteners. They furnish their rated voltage at currents up to 3 amperes,
with inputs of 226 to 233 volts, 57 to 62 cps. A circuit breaker in each rectifier
protects the rectifier bridge from overloads.
Each bulk rectifier is connected to its load through several "isolation keys."
These permit us to remove certain load circuits, one at a time. This aids in
trouble shooting. All isolation keys are mounted on plates just below the recti-
fiers (see Fig. 10-4).
288 The Central Control Chap. 10
There is a +4v voltage regulator in each central control. It provides ±1%
regulation at loads up to 14 ampere. Each regulator consists of two circuit
packages (F-52659 and F-52660) at locations 423J and 423L.
Each central control also has three tracking regulators, each of which is
assembled as an F-52656 circuit package. They provide a 6.5-volt output that
tracks 1.5 ± 0.1 volts below the +8v input at a current of M ampere maximum.
They are found at locations 222AA, 423N, and 423Q.
Ninety-two "isolation network" packages are used in each central control.
They provide extra filtering of the d-c power, and removing them isolates their
load circuits.
The clock pulse power supply is located in bay 5. It provides the following
voltages to the circuits indicated :
Voltage Circuit
6.3v a-c Clock Pulse Generator* and Amplifier (Filament)
[ + 150v d-c Clock Pulse Generator* and Amplifier (Screen)
Regulated \ + 250v d-c Clock Pulse Generator* and Amplifier (Plate)
[ + 400v d-c Clock Pulse Amplifier (P. A. Plate)
Relays in the clock pulse power supply prevent plate or screen power from
being applied to the tubes in the pulse generators and amplifiers until the
filaments have warmed up. They also prevent screen power from being applied
unless plate power is present. A circuit breaker in the input circuit protects the
supply from overloads.
10.4 MISCELLANEOUS
There are several 276-F plug-in mercury contact relays in the CC. These
are used for monitoring certain power applications.
Relays DD-0 and DD-1 are located on plate 424 of CC-0 and CC-1 respectively.
They are normally operated by the+ 1 6G power supply through key+ 1 6G4. Failure
of this power, either in the bulk rectifier or in the main a-c supply, will cause
the relay to release. If this occurs in the active CC, the relay action will cause
the control and indicating circuit in the administration center to take the faulty
CC out of service and put the stand-by CC into service, and to light the proper
alarm lamps. Should the stand-by CC be affected, it will be "made busy" and
the alarm lamps will be lighted.
""Located in the stand-by transfer.
Sec. 10.4 Miscellaneous 289
Relays marked RFA are located on plates 222 and 424, and relays RFC and
RFD on plate 424.These operate blown fuse alarms. The RFA relays indicate blown
fuses in the +8v circuits feeding certain +6.5v tracking regulators. The RFC
relays indicate blown fuses in the +8v circuits feeding other +6.5v tracking
regulators and some+4v regulators. The RFD relays indicate blown fuses in the
— 16v circuit feeding a +4v regulator. These relays are operated when the type
70 fuses blow and force their end caps against the alarm terminals of the fuse
blocks.
There are test blocks located on each bay. Each block contains four test posts,
designated +22G, +22CP, GRD, and HRG. Bays 1, 3, 5, and 7 have test blocks
mounted on both front and rear. The +22G is connected to the +22v supply
through a 3830-ohm resistor; the +22CP is connected to the +22v supply
through a 2610-ohm resistor; and the HRG is connected to ground through
a 12,000-ohm resistor.
Feed-through terminal strips are mounted at plate location 30 on bays 1, 3, 5,
and 7, and at location 29 on bays 3 and 7. These provide junctions for inter-
cabinet wiring. They also furnish access points for testing.
Coaxial connectors are mounted on plate 32 of bays 1, 3, 5 and 7. These
connect to cables for the inter-cabinet transmission of clock pulses.
Bay 7 contains a number of connectors used for a portable manual test
circuit (a "T-cart"). This is a manually operated substitute for the flying spot
store. Its connections to the system are via the CC, bay 7. On plate 700, coaxial
connectors marked PPF, RES, INS, and EXEC, and multi-contact connectors
marked MPP, MTA, and MTB are for this purpose. Some contacts of these con-
nectors are wired directly to pin jacks in the CC. You will find these jacks
mounted on plates directly behind the isolation keys on each hinged bay.
Special test leads plugged into these jacks can be clipped onto any desired place
in the central control circuit. This gives the "T-cart" access to any point in the
CC as needed. A 230-volt, 3-wire receptacle located in the base of bay 7 provides
power to the "T-cart."
Another item of test equipment connected to the central control is the central
control automatic tester (CCAT). Connectors for it are mounted on the side of
bay near the top. Mating cable-mounted connectors, wired into the central
control, are normally plugged into connectors marked "FSS1-A" and "FSS1-B."
When the CCAT is used, these connections are broken and the connectors are
plugged into the connectors marked CCAT-A and CCAT-B, respectively. There
are eight other connectors involved with the CCAT. Their fixed portions are
290 The Central Control Chap. 10
mounted in the bottom of the cabinets behind bays 2, 4, and 6. They are marked
CCl through CC7, and CCS. Mating portions are cable-mounted and are
marked CTl through CT7 and SCAT, respectively. These connectors are only
mated when the CCAT is used. At other times they are disconnected, and their
open ends are covered with plastic shields.
There are connectors in the central control for the tape plate preparation
equipment. This is the equipment used in preparing new photographic plates
for the flying spot stores. It is connected to the central control thru coaxial con-
nectors EXP, RST, and TPPCK, and multi-contact connector PP. These are located
on plate 700.
A multi-contact connector, marked UTS, is found on the left side of bay 7.
This is used for a portable test equipment called "FSS parity failure detector
circuit." When plugged in, this equipment uses the central control to check the
flying spot store alignment.
Below the UTS connector are two coaxial connectors, marked RS-1 and RS-0.
These are no longer used.
Below the test block on bay 7 are two keys. They are marked SXS and EXT CLK.
The SXS key permits you to operate the flying spot store via the central control
in one-at-a-time manually controlled steps. The EXT CLK key switches the
system to an external pulse generator in the manual test circuit. This gives us a
variable control over the speed of system operation.
We find many wire-wound resistors mounted on plates 124, 222, 223, 523,
and 721. Those marked with ?wo-letter or threeAsiiev code groups are voltage-
divider resistors in the d-c power circuits. These are associated with the marginal
voltage testing circuit located in the stand-by transfer. Resistors marked with
/owr-letter code groups are cable-terminating resistors used in clock pulse
circuits. These resistors are wired through a type D terminal strip mounted
on each plate.
The central control cabinets contain the alarm relays, alarm indicator lamps,
and power receptacles common to all ESS cabinets; two cabinets also have
jacks mounted near the alarm lamp. These are used for intercommunication
between cabinets.
10.5 MAINTENANCE
Since the central control is completely duplicated, it will rarely, if ever,
require in-service repairs. The system routinely checks the operation of the
Sec. 10.5 Maintenance 291
active CC against the stand-by unit. If a repetitive mismatch is detected, the
system at once goes into a fault-checking routine. This determines whether
the trouble is in CC-0 or CC-1. The faulty unit is automatically taken out of
service and "made busy" to the system; the alternate unit then runs the office.
A red light in the administration center tells which unit is out of service,
and the system starts a diagnostic test routine. This checks the out-of-service
unit to locate the source of the trouble. A print-out on the teletypewriter tells
us where to look for the fault. After repairs have been made, we must type a
"restore" order into the teletype. This starts another fault-checking routine to
make sure that the unit is OK before putting it back in service. If the unit checks
OK, it is placed on stand-by and the trouble lamp is put out.
Emergency Alarm Timer Resetting Routine
To check the proper operation of the active system, a special program is used.
Its end product is to reset the emergency alarm timer via the signal distributor.
This occurs once every 100 milliseconds. If the timer is not reset, it will "time
out," indicating that something prevented the program from resetting the timer.
If the timer is not reset, the flying spot store, the central control, and the signal
distributor will be switched from active to stand-by and vice versa. A diagnosis
of the various units will then follow.
Repair Procedure
When trouble is indicated in a CC unit, its location is given within a certain
area. Replacing all circuit packages or other conveniently removable units
within that area should clear up the trouble. Table 10-2 (on page 292) lists
the circuit packages used in the central controls.
WARNING Before doing any maintenance work in a central control unit, always put it
in the "busy" (trouble) state!
"Continuous diagnosis" is a procedure that aids the maintenance man when
the diagnostic print-out is not specific enough in pointing out the fault location.
This is a diagnostic mode that performs all normal tests, but prints a record
only when all tests pass. When a test fails, the phase of the diagnosis in which
the failure occurs is completed; then the sequence stops, the CC trouble lamp
lights, and the diagnosis repeats. The trouble lamp remains lighted for one-
half second; it is but during the tests. We start this procedure by a teletype
292
The Central Control
Chap. 10
TABLE 10-2. PACKAGES USED IN THE CENTRAL CONTROLS
The quantities shown are the totals for the duplicated units.
Designation
CPS* No.
Quantity
Name
F-52600
36
864
Transistor Flip-Flop
F-52601
46
816
Flip-Flop to Gate Amplifier
F-52603
48
476
Gate Amplifier
F-52604
49
102
Inverter Amplifier
F-52605
50
628
Emitter-Follower Amplifier
F-52610
146
2
Transistor Monostable Flip-Flop
F-52615
1
700
AND Gate, 2-2-2-2 Inputs
F-52616
2
468
AND Gate, 2-2-2-2-2 Inputs, with One Input Common
F-52617
3
540
AND Gate, 3-3-3 Inputs
F-52618
4
424
AND Gate, 3-3-3-3-3 Inputs, with Two Inputs Common
F-52619
5
98
AND Gate, 5-5 Inputs
F-52620
16
110
OR Gate, 1-1-1-1-1-1 Inputs
F-52621
17
152
OR Gate, 2-2-2-2 Inputs
F-52622
18
24
OR Gate (No Resistor), 1 Inputs
F-52623
19
46
OR Gate (2610-ohm Resistor), 2-2-2 Inputs
F-52624
20
88
OR Gate (2610-ohm Resistor), 2-3-3 Inputs
F-52625
21
8
OR Gate (2610-ohm Resistor), 10 Inputs
F-52626
22
216
OR Gate (3830-ohm Resistor), 2-2-2 Inputs
F-52627
23
88
OR Gate (3830-ohm Resistor), 2-2-3 Inputs
F-52628
24
170
OR Gate (3830-chm Resistor), 2-3-3 Inputs
F-52629
25
100
OR Gate (3830-ohm Resistor), 4-4 Inputs
F-52630
26
174
OR Gate (3830-ohm Resistor), 10 Inputs
F-52631
155
184
Isolation Network
F-52633
51
80
Cable Pulser Amplifier
F-52634
156
172
Cable Matching Network
F-52656
195
6
Tracking Voltage Regulator, +6.5v
F-52659
189
2
+ 3v to +5v Voltage Regulator, Board A
F-52660
189
2
+ 3v to +5v Voltage Regulator, Board B
F-52663
154
16
Steering Network
F-52664
69
24
Cable Buffer Amplifier
F-52665
70
2
Shaper Amplifier
F-52666
158
2
16-kilocycle Crystal Oscillator
F-52667
153
16
Pulse-Shortening Network
F-52668
138
6
Delay Network
F-52669
148
4.
Feedback Network
»
F-52670
181
12
Voltage Divider Resistors, 330 Ohms
F-52671
182
30
Voltage Divider Resistors, 510,000 Ohms
F-52672
41
30
Clock Coupling Network A
F-52673
42
40
Clock Coupling Network B
F-52674
43
22
Clock Pedestal Network
*CPS means Circuit Package Schematic.
Table 10-2 continued on page 293
Sec. 10.5 Maintenance 293
TABLE 10-2. PACKAGES USED IN THE CENTRAL CONTROLS (continued)
Designation
CPS* No.
Quantity
Nome
F-52675
F-52676
F-52679
F-52681
F-52693
F-52696
198
142
44
134
133
258
i
16
2
10
34
2
2
Voltage Divider, 1 0,000 Ohms
EPO Delay Network
Clock Coupling Network C
Voltage Shifting Network
Bias Network
Feedback Network B (Remote Concentrator Control
Circuit)
*CF'S means Circuit Package Schematic.
order; then we replace the packages in the trouble area, one at a time, mak-
ing sure to leave each package in its socket for two successive flashes of the
trouble lamp. When we have replaced the faulty package, the diagnosis will run
to completion and a teletype print-out will indicate that all tests passed. The
duration of a complete diagnosis is slightly over three seconds.
All circuit packages are plug-in units. The bulk rectifiers plug in and are
held in place by quarter-turn fasteners. The clock pulse amplifiers are simi-
larly mounted, but the quarter-turn fasteners are of the ring-handle type and are
operated from the front of the bay. The clock pulse power supply rests on a
mounting shelf and also is fastened with quarter-turn fasteners. The clock pulse
equipment and power supplies also have rear-mounted connectors that connect
them into the system.
WARNING The clock pulse amplifiers use voltages up to 450 volts d-c. Do not remove the
protective shields nor stick your fingers or any tools into these units when
the power is on !
Disconnecting a clock pulse generator or a clock pulse amplifier or an
associated bias network will automatically disable the clock pulse power supply.
Isolation Keys
Some troubles that show up as power supply failures can be localized by
using the isolation keys. When a fault causes the circuit breaker in a bulk
rectifier to trip, you should open all the keys in that rectifier circuit and reset
the breaker. If it trips again, the fault is in the bulk rectifier. If it does not trip,
294 The Central Control Chap. 10
you should check the breaker in the power distribution cabinet to make sure
that it has not tripped. Then, by closing the isolation keys one at a time until
the bulk rectifier breaker trips, you can locate the faulty circuit.
Voltage Monitor Test
An important means for detecting power supply troubles before they become
serious is the voltage monitor test. This test automatically monitors the output
of each CC power supply at regular intervals. If any output is found to exceed
the specified limits, an alarm is sounded and a teletype print-out identifies the
faulty unit. This test is also applied as the first step in the diagnostic test routine.
A failure here stops the rest of the routine and gives the location of the fault.
Marginal Voltage Test
Another important tool of preventive maintenance is the marginal voltage
test. This test checks the ability of certain critical circuits in the central control
and stand-by transfer to operate properly under abnormal d-c voltage conditions.
It is applied to certain flip-flops and gate amplifiers, which are grouped for this
test. The test consists of applying a marginal voltage, which either adds to or
subtracts from the normal d-c voltage (adding voltages are not applied to
flip-flop groups, however). This voltage is applied separately to each group
of packages in four discrete steps. The operation of these circuits is checked
at each step. A teletype print-out indicates which groups passed the test, and
which failed. When failures occur, the voltage margin at which the apparatus
failed is also indicated. At the minimum margin, any package that fails to
operate should definitely be replaced; at the maximum margin, a good package
should still operate.
This test can be made only on the stand-by CC, for it is matched against the
active CC that is handling office traffic. The marginal voltage test is programmed
automatically once a day. A marginal voltage test can also be called for via
the teletype. However, such a request must be followed, within 45 seconds, by
another order, such as diagnosis of the central control. At the end of such
diagnosis, or after the 45-second time-out, the marginal voltage is removed. A
complete marginal voltage test for one central control and the stand-by transfer
circuit takes about twelve minutes.
Chapter 1 1
Trunk Circuits
The ESS is connected to outside telephone facilities through a number of
different kinds of trunk circuits. These include incoming and outgoing trunks
to the No. 5 crossbar office, PBX tie lines, and one-way trunks to the 3CL
switchboard. The trunking plan is shown schematically in Fig. 11-1.
The trunk circuits in the ESS are relatively simple compared to those in other
switching systems. This is because the memory and logic functions are cared for
in other parts of the ESS rather than in the trunk circuits.
The types, quantities, and drawing numbers of the trunk circuits initially
assigned in Morris are shown in Table 11-1. The assignment of the trunks in
the distribution switching network is covered in Chapter 3.
11.1 EQUIPMENT ARRANGEMENTS
The trunk circuits are mounted in two cabinets, designated T-0 and
T-l. Each cabinet has a gate bay, designated 0, and a fixed bay, designated 1.
Most of the equipment is mounted in the fixed (rear) bay, as shown in Fig. 1 1-2.
Only one cabinet is shown in this figure, but the other one is essentially the
same. In each cabinet, the gate (front) bay is empty, except for sixteen fuse
blocks and two terminal strips.
The apparatus is mounted on standard mounting plates. Some apparatus is
of the permanently-wired type and some consists of circuit packages. Identifying
circuit numbers are stenciled on the mounting plates; bay and plate location
numbers are stenciled on the bay frames.
Trunk power is supplied by four bulk rectifiers mounted at the top of each
cabinet. The rectifiers in cabinet T-l are supplied from the 230-volt a-c bus
"B"; those in cabinet T-0 are supplied from the 230-volt a-c bus "C" (see Fig.
1-18). All rectifiers are of the plug-in type. Rectifier outputs are connected
through fuses to the trunk circuits. Each set of four rectifiers supplies power to
the trunks in its cabinet.
295
296
Trunk Circuits
Chap. 11
TEST
CABINET
INCOMING
OUTGOING
3 LINE
CONFERENCE
CIRCUIT
INTERCEPT
7A
DESK
INFORMATION
3 CL
: SWITCH -^
BOARD
RECORDING
NO. 5
CROSSBAR
SYSTEM
COMPLETING
PERMANENT
LOCAL (4 DIGITS)
1 LOCAL (4 DIGITS)
SIGNAL
PARTIAL DIAL
DENIED SERVICE
REPAIR AND
EAS AND TOLL
1 TANDEM (4 DIGITS)
BUSINESS OFFICE
NIGHT TRANSFER
EAS TANDEM
( 7 DIGITS)
CGS
TIE LINE
CGS
INDICATOR
SIGNAL
TRUNK
FIG. 11-1. ESS trunking plan.
Power is also supplied from the 48-volt battery of the No. 5 crossbar central
office. Cabinet T-0 gets its power from d-c bus "B", and cabinet T-l gets its
power from d-c bus "C" (see Fig. 1-19).
Each group of trunks (such as incoming, outgoing, etc.) is divided in half:
one half of the trunks are mounted in- cabinet T-0 and the other half in cabinet
T-l. Under this arrangement, a failure in either a-c bus or either d-c bus will
affect only one half of any group of trunks.
Sec. 11.1 Equipment Arrangements 191
TABLE 11-1. TRUNKS INITIALLY ASSIGNED IN THE MORRIS ESS
F-Spec.
Number
CPS*
No.
Drawing
Number
Quantity
Trunk
F-52644
180
ES-1A054-01
13
3
3
4
2
1
Outgoing to 3CL Switchboard
(Recording-Completing)
Outgoing to 3CL Switchboard
(Permanent Signal)
Outgoing to 3CL Switchboard (Partial Dial)
Outgoing to 3CL Switchboard
(Denied Service)
Outgoing to 3CL Switchboard (Repair and
Business Office Night Transfer)
Incoming from 3CL Switchboard (No-Test)
F-53323
271
ES-1A056-01
7
Three-Line Conference Circuit
F-52684
34
ES-1A061-01
5
Indicator Signaling
—
—
ES-1A060-01
39
25
39
21
Incoming from No. 5 Crossbar (Local)
Incoming from No. 5 Crossbar
(EAS and Toll Tandem)
Outgoing to No. 5 Crossbar (Local)
Outgoing to No. 5 Crossbar (EAS Tandem)
—
—
ES-1A055-01
3
Customer Group Service (CGS) Tie Lines
—
—
ES-1A059-01
2
2
Incoming from Test Cabinet
Outgoing to Test Cabinet
—
—
ES-1A057-01
5
10
Outgoing to 7A Desk (Information)
Outgoing to 7A Desk (Intercepting)
—
—
ES-1A065-01
10
Toll Termination
—
—
ES-1A055-01
1
PBX Toll Tie Line
CPS means Circuit Package Schematic.
11.2 METHOD OF OPERATION
In the ESS, as in other systems, trunk circuits have two major functions.
These are:
(1) To provide talking paths.
(2) To provide signaling links between the ESS and
other offices or switching points.
298
Trunk Circuits
Chap. 11
RECTIFIER
+ 16 B BUS
RECTIFIER
-16 B BUS
RECTIFIER
+ 16 C BUS
RECTIFIER
-16 C BUS
FUSE PANEL
FUSE PANEL
FUSE PANEL
IND SIG TRK UNIT
57 58 59
2 WIRE TRK UNIT
2 WIRE TRK UNIT
54 55 56
OGT TRK UNIT
3 TERM CONF TRK UNIT
2 WAY TRK UNIT
33
2 WAY TRK UNIT
INC OUTGOING & NO TEST TRK UNIT
HIGH CURRENT LINE TRK UNIT
2 WAY AUTO TRK UNIT
~IN-OUT TEST TRK UNIT
IDLE CKT TERMINATION TRK UNIT
i 9 10 11 12
^ * " L, £4-**
FIG. 1 1-2. Trunk cabinet, rear view and rear equipment.
Sec. 11.2
Method of Operation
299
CONCENTRATION
SWITCHING NETWORK
DISTRIBUTION
SWITCHING NETWORK
JUNCTOR
A SIDE Y B SIDE
* — X iii T i
X )( )(
-*- INDICATES CROSSPOINT v = "03
FIG. 11-3. Typical transmission path from a customer telephone set to a trunk.
The transmission path from a customer's telephone set is through the line
circuit, the concentrator trunk, the distribution switching network, and then to
the trunk circuit, as indicated in Fig. 11-3. For flexibility, several customers
have access to each concentrator trunk. The concentrator trunks are equally
divided, one half appearing on the A side of the distribution switching network
and the other half appearing on the B side. Trunks have appearances on either
the A or B side of the network, or both. Those trunks with only one appearance
on the distribution switching network are referred to as single-sided trunks;
those appearing on both sides of the network are called double-sided trunks.
11.2.1 Operator Call, Recording-Completing Trunk (Fig. 11-4)
When a customer dials the operator code zero, the signal distributor
grounds the trunk TS lead, which in turn causes a lamp to light at the 3CL
switchboard. When the operator answers the call, the trunk places a ground on
the A lead to the scanner. This ground informs the ESS that the call has been
answered. The talking path between the customer and the trunk circuit is then
completed through the distribution switching network.
11.2.2 Trunk Connection to Two Sides of Distribution Switching Network (Fig. 11-5)
Normally, when this trunk is used as an incoming or outgoing trunk,
it is connected to either the A side or the B side of the distribution switching
CONCENTRATION
SWITCHING NETWORK
DISTRIBUTION
SWITCHING NETWORK
3 CL
SWITCH-
BOARD
TELEPHONE
SET
LINE
CIRCUIT
[
-&r INDICATES CROSSPOINT
L>I3 I HIDU I UM
VG 1104
FIG. 11-4. Incoming or outgoing trunk to the 3CL switchboard, single-sided termination.
LINE CIRCUIT CONCEN-
TRATOR
TRUNK
3 CL
SWITCH-
BOARD
CONCENTRATION
SWITCHING NETWORK
RELAY CONTACT
INDICATES CROSSPOINT
DISTRIBUTION
SWITCHING NETWORK
FIG. 11-5. Incoming or outgoing trunk to the 3CL switchboard, double-sided termination.
300
Sec. 11.2
Method of Operation
301
* ORIGINAL CONNECTION
-*e- INDICATES CROSSPOINT
FIG. 11-6. Outgoing trunk from the 3CL switchboard arranged for no-test,
double-sided termination.
network. To reduce the possibility of rinding no paths, some trunks of each type
are terminated on both the A side and the B side of the distribution switching
network. The customer, through the concentration switching network, has
access to both sides of the distribution switching network. Fig. 11-5 shows a
connection between a customer on the A side and a trunk on the B side of the
distribution switching network.
11.2.3 No-Test Trunks (Fig. 11-6)
A group of no-test trunks originates at the 3CL switchboard. These
trunks are used by the operator to monitor or challenge on a line to determine
whether the line is busy or in trouble. These trunks have both an A side termina-
tion and a B side termination. The operator can, by dialing a code and then
302 Trunk Circuits Chap. 1 1
the directory number, cause the ESS to insert the no-test trunk into an already
established talking connection. The original connection between the called and
calling customers in the distribution switching network is then discarded, and a
transmission path from line 1 is established through a concentrator trunk to
the A side of the distribution switching network crosspoints and then to the B
side crosspoints. From here it goes to the B side of the no-test trunk. This trunk
also is coupled to the A side of the network. The transmission path then goes
through the A side of the distribution switching network crosspoints to the B
side crosspoints, and from there to the concentrator trunk to line 2. When the
operator disconnects, and the no-test connection is removed, a separate con-
nection is again established through the distribution switching network between
lines 1 and 2. If the dialed directory number is not busy, the only connection set
up is from the trunk through the distribution switching network to the con-
centrator trunk on either the A or B side.
11.2.4 Two-Way Trunk Circuit for PBX Tie Line (Fig. 11-7)
This trunk circuit is used to connect the ESS to a PBX tie line. The
trunk operates with standard E and M lead signaling circuits between the ESS
and a distant PBX. It performs the following major functions:
(a) Transmits signals to the distant PBX.
(b) Recognizes a seizure signal, dial pulsing signals, and supervisory
signals from the distant PBX.
(c) Provides a talking path from the distribution switching network to
the trunk repeating coil group.
(d) Removes the idle circuit termination when the talking path is set up.
Outgoing Call to Distant PBX
The trunk circuit is seized when a ground is placed on the TSA lead from the
signal distributor. A relay in the trunk circuit operates and changes the ground
on the M lead to battery. This constitutes a seizure signal to the connected CX
signaling circuit which lights a lamp at the distant PBX. On an answer condition
from the distant PBX, the associated CX signaling equipment places a ground
on the E lead to the trunk. The ground passes through the trunk to the scanner
A lead. It is recognized by the scanner as an answer signal. Now the system
sets up the talking path through the switching network. At the time the talking
Sec. 11.2
Method of Operation
303
PBX
EXTENSION
OR
ATTENDANT
CONCENTRATION
SWITCHING NETWORK
CONCEN'
TRATOR
TRUNK
DISTRIBUTION
SWITCHING NETWORK
LINE
CIRCUIT
-*•
JUNCTOR
A SIDE Y B SIDE
k
TO DISTANT
PBX
TO 4 WIRE TERMI-
NATING CIRCUIT
CARRIER TERMINAL |
CHANNEL
TO CX OR SX
SIGNALING CIRCUIT
INDICATES CROSSPOINT
FIG. 11-7. Two-way trunk with E and M lead signaling for PBX tie line,
single-sided termination.
path is set up, a ground is placed on the TSB lead from the signal distributor to
operate another relay in the trunk. This relay removes the idle circuit termination
from the trunk.
At the end of the call, if the distant end disconnects first, the ground is re-
moved from the E lead. This restores battery to the scanner A lead, and is
recognized as a disconnect signal. The signal distributor causes the M lead to
change from battery to ground by releasing the trunk relay. If the calling end
disconnects first, battery is removed from the M lead. This in turn causes a
disconnect signal at the distant PBX.
Incoming Call from Distant PBX
When the trunk is seized at the distant PBX, ground appears on the trunk E
lead. This ground is detected by the scanner as a seizure signal. When this
ground is interrupted by dialing from the distant end, the scanner recognizes
the interruptions as dial pulses. When dialing is finished, the ESS connects a
ringing current to the called extension and an audible ringing tone to the
304 Trunk Circuits Chap. 1 1
calling PBX. When the called extension answers, the ringing is tripped; now the
signal distributor grounds the TSB lead to operate a relay in the trunk to remove
the idle circuit termination. The signal distributor also grounds the TSA lead
to operate the supervisory relay in the trunk. The operation of this relay changes
the M lead potential from ground to battery. This is recognized at the distant
PBX as an answer signal.
When either extension hangs up, the connection is released. The ESS dis-
connects by releasing the trunk relays. This removes battery from the M lead
and indicates a disconnect to the distant end. When the distant end disconnects
first, ground is removed from the trunk E lead and replaced with battery. This
is recognized by the scanner as a disconnect signal.
11.2.5 Trunk Circuit to the No. 5 Crossbar Office (Fig. 11-8)
This trunk circuit is used to connect the ESS to the No. 5 crossbar
office. The trunk circuit operates with the standard No. 5 auxiliary incoming or
outgoing trunk circuits arranged to convert loop supervision to E and M lead
supervision. This trunk can terminate on one or both sides of the distribution
switching network. It performs the following major functions:
(a) Transmits seizure signals, dial pulses, and supervisory signals to the
No. 5 auxiliary trunk circuit.
(b) Recognizes seizure signals, dial pulses, and supervisory signals from
the No. 5 auxiliary trunk circuit.
(c) Provides a talking path from the ESS distribution switching network
to the No. 5 crossbar office auxiliary trunk circuit.
Outgoing Call
When the trunk is seized by the ESS, a ground is connected to the TS lead
from the signal distributor. This operates the trunk relay, which places ground
on the E lead toward the No. 5 crossbar equipment. A battery pulse is sent back
to the ESS via the M lead and then to the A lead to the scanner. This battery
pulse (Wink) on the A lead informs the ESS that the No. 5 crossbar equipment
is ready to receive pulses. At the same time that the seizure signal is transmitted,
the ESS sets up the talking path from the calling customer to the trunk circuit.
Dial pulses on the TS lead from the signal distributor now operate and release
the trunk relay at the dial pulse rate. Dial pulses are sent to the No. 5 crossbar
equipment over the E lead. When the called customer answers, battery is sent
back to the ESS over the M lead and then over the A lead to the scanner. This is
Sec. 11.2
Method of Operation
305
CONCENTRATION
SWITCHING NETWORK
DISTRIBUTION
SWITCHING NETWORK
JUNCTOR
A SIDE Y B SIDE
-X *-
-* — *-
, RELAY
' CONTACT
TO AUXILIARY
INCOMING
OR OUTGOING -
TRUNK IN NO. 5
CROSSBAR OFFICE
T C-
RO-
E O-
M o-
-*- INDICATES CROSSPOINT
SIGNAL
DISTRIBUTOR
FIG. 1 1-8. Incoming or outgoing trunk to No. 5 crossbar office with
E and M lead signaling, single-sided termination.
recognized as an answer signal. The battery is removed from the A lead to the
scanner when the called customer disconnects. The signal distributor now re-
leases the trunk relay. This removes the ground from the E lead and causes the
release of the No. 5 crossbar equipment. When the called or calling customer
hangs up, a disconnect signal is sent in the opposite direction.
Incoming Call
When the trunk circuit is seized by the No. 5 crossbar equipment, battery
appears on the M lead and then on the A lead to the scanner. After an interval
of time, the No. 5 crossbar equipment starts outpulsing. These dial pulses
(battery interruptions) are detected by the scanner on its A lead. After central
control has received the necessary information, it sets up the ringing connection
to the called customer. When the called customer answers, the talking path
between the ESS distribution switching network and the No. 5 crossbar office is
set up. Now the signal distributor causes a ground to be put on the E lead toward
the No. 5 crossbar office. This signal serves as an answer signal to the No. 5
crossbar equipment. Disconnect is handled in the same manner as described
for the outgoing call.
306 Trunk Circuits Chap. 1 1
11.3 MAINTENANCE
Because of the simplicity of the trunk circuits, maintenance is quite easy.
Trunks are taken out of service or restored to service via instructions to
central control from a teletypewriter at the administration center. The detailed
maintenance procedures for the trunks are covered in their respective circuit
descriptions (CD's). Test calls are made to the trunk circuits from the ESS
local test cabinet.
Chapter 12
The Administration Center
The Administration Center (AC) is the maintenance center for the ESS. Here
you receive all maintenance instructions for the system in the form of teletype
messages and alarm signals. A general view of the AC is shown in Fig. 12-1.
The administration center includes two teletype machines. Normally, all
trouble indications are recorded on one of these machines, and all traffic
information is recorded on the other. If necessary, however, one machine can
handle both the trouble indications and the traffic information. Either of these
two machines can be used in place of the other by operating certain keys on
the machine.
12.1 EQUIPMENT ARRANGEMENTS
The administration center is made up of a console and two cabinets, as
shown in Fig. 12-1. The cabinets are designated AC-0. On the console are
mounted the two No. 28 teletype machines. The lower part of the console
includes a typing reperforator for recording the message on teletype tape
(see Fig. 12-2).
Front Bay 0- Fig. 12-3
Bay 0, a front bay, contains a display panel, in the upper part. Lamps in
this panel indicate the status of all duplicated control circuits. A white lamp
indicates the unit that is in control; a unit in standby is not indicated. A red
lamp indicates a unit in trouble. Below the display panel is a strip of thirteen
transfer keys. You use these keys to transfer control to a duplicated unit, or to
make a duplicated unit busy, when the teletype order fails to perform this
function.
Below the control keys are five strips of ten alarm lamps each, and alarm
control keys. You use these for various office alarm conditions. To the left of
307
308
The Administration Center
Chap. 12
\. ,
I3&B3
fH&3 ' E
FIG. 12-1. Administration center, front view.
Sec. 12.1 Equipment Arrangements 309
these keys and lamps is a dial telephone set. By operating keys, you can connect
to any one of ten talking lines.
Bay also contains the power panel for the teletypewriter and the marginal
voltage control.
Rear Bay 1—Fig. 12-4
Bay 1 , at the rear, contains marginal voltage control relays, and control and
indicating relays. It also contains teletype control relays, and control and
indicating power circuits.
Front Bay 2— Fig. 12-5
Front bay 2 contains power rectifiers mounted at the top. Voltages of +22,
+ 16, and —16 volts are provided by duplicate rectifiers operated in parallel-
Under trouble conditions, you can remove one of the units. Voltages of +7.5
and —4.5 volts are provided with single rectifiers; these are used in test circuits.
The lower portion of this bay has the FSS exposure address and plate verifi-
cation unit.
Rear Bay 3— Fig. 12-6
Rear bay 3 contains the voltage monitoring circuit. This circuit consists of
four crossbar switches, a selector, a voltage detector, a voltage divider, and a
voltage reference transfer.
Figures 12-2 through 12-6 are shown on pages
310 through 314. The text of Section 12.2,
Method of Operation, starts on page 315.
310
The Administration Center
Chap. 12
TAPE HOLDER
FIG. 12-2. Typing reperforator and tape.
VG (202
Sec. 12.1
Equipment Arrangements
311
,-crrf
. y*';*ryY,iYiT?i?#P
%
« ■
■
■ HOUR CLOCK
POWER FOR
TELETYPEWRITER
AND MARGINAL
VOLTAGE UNIT
FIG. 12-3. Cabinet ACO, front view, Bay 0.
312
The Administration Center
Chap. 12
MARGINAL
y VOLTAGE
CONTROL
CONTROL AND
V INDICATING
RELAYS
POWER
TWY RELAYS
-^rrpnrmtmT^-v^^
FIG. 12-4. Cabinet ACO, rear view, Bay 1.
Sec. 12.1
Equipment Arrangements
313
, 1
if
j_^:
>
RECTIFIER
LOCATIONS
PLATE
y PREPARATION
CONTROL
PLATE
)>- PREPARATION
EQUIPMENT
TAPE
- CONNECTOR
JACK
FIG. 12-5. Cabinet ACO, front view, Bay 2.
314
The Administration Center
VOLTAGE
MONITOR
LEADS
.f
r
y\ \\y.v,y\ 1 J J
CONTROL
RELAYS
DIVIDERS
VOLTAGE
REFERENCE
RECTIFIER
LOCATIONS
VG 1206
FIG. 12-6. Cabinet ACO, rear view. Bay 3.
Chap. 12
Sec. 12.2 Method of Operation 315
12.2 METHOD OF OPERATION
Teletype Machines
Either of the No. 28 teletype machines can be used in place of the other by
operating keys at the machines. Machine No. 1 is normally used for trouble
reports. Machine No. 2 is normally used for traffic reports. When one machine
is out of service, all data (both trouble data and traffic data) are recorded on
the machine in service.
Some other functions of the teletype machines are listed below:
(1) Entering recent change orders on the barrier grid store (BGS).
These may be new customer and trunk order changes stored until
the flying spot store (FSS) plates are changed.
(2) Making up plate preparation orders for the flying spot store (FSS).
(3) Entering orders to make line and trunk circuits busy.
(4) Entering orders to transfer duplicate control circuits that operate
on a matching basis.
(5) Issuing orders to make these duplicate control circuits busy and to
routine them for locating trouble, as well as issuing orders to restore
the circuits to matching operation.
Dictionary
The dictionary is a book that explains the method of reading trouble records.
A few examples are given below. All trouble records are preceded by the symbol
A (trouble). The next three characters indicate the major unit. The code
used is as follows:
Code Explanation
A DC or DC 1 Central Control (CC)
▲ DF or DF 1 Flying Spot Store (FSS)
ADSOOorDSOl Scanner (S-O)l
address circuit duplicated
m. DS 10 or DS 11 Scanner 1 (s-l)J
▲ DD or DD 1 Signal Distributor (SD)
A DN or DN 1 Distribution Marker (DM)
▲ DK or DK 1 Concentration Marker (CM)
A DA or DA 1 PBX Announcing Drum
316
The Administration Center
Chap. 12
TELEPHONE
SET AND
CONNECTING
TRUNKS
TRANSFER
" KEYS
ALARM
LAMPS
AND
KEYS
FIG. 12-7. Administration center display panel and associated equipment.
Sec. 12.2 Method of Operation 317
Method of Operation
Code
Explanation
* DBO
Barrier Grid Store (BGS-0)
DB 1
Barrier Grid Store 1 (BGS-l)
, DB2
Barrier Grid Store 2 (BGS-2)
k DB3
Barrier Grid Store 3 (BGS-3)
Display Panel— Fig. 12-7
Each major circuit has two lamps at the display panel. The active unit
has its white lamp lighted. A unit in trouble has its red lamp lighted. A unit
in the stand-by condition has no lamp lighted.
Alarm Panel
There are five strips of ten alarm lamps and associated release keys. They
cover major alarms, minor alarms, power distribution alarms, and other alarm
conditions. These are described in detail in the circuit description for the
miscellaneous circuits. A general description of the ESS alarm system is given
in Chapter 15; the alarm panel is shown in Fig. 15-2.
Control Panel
A manual means of taking equipment out of stand-by operation is provided.
You can make any unit busy with a key. However, these keys are to be used
only when the teletypewriter order fails to function.
Program orders also change the active and stand-by units automatically.
Communication Center
A telephone handset and dial enable you to communicate with any one of
ten other locations by operating one of ten keys.
Voltage Monitoring
The voltage monitor circuit provides an automatic diagnostic tool that
monitors about 800 voltage checkpoints distributed throughout the ESS. Under
control of the system test program, it monitors the voltages at these checkpoints
on a routine basis. It takes about fifteen minutes to complete the monitoring
cycle, provided that the test program is not interrupted. If the voltage monitor
detects a difference between the voltage at the checkpoint and the reference
voltage in the monitor, a teletypewriter print-out tells you of the difference.
318 The Administration Center Chap. 12
The voltage monitor is also called into action when the system starts a
diagnostic program. When this occurs, the routine testing of the checkpoints
is stopped and the monitor is immediately told to check the voltages of the
circuit under test. The results of this check, OK or trouble, are given in a tele-
typewriter print-out. On completion of the diagnostic work, the program
directs the voltage monitor back to its routine voltage-checking job.
If the reference voltage supply in the monitor fails, it is automatically switched
to its stand-by supply. A lighted VMR lamp at the administration center indi-
cates the switch. By the use of a transfer and reset key, the reference voltage
supply can be controlled manually.
Records
The teletypewriter produces printed records of all alarm (trouble) conditions.
These records are to be filed daily in time sequence in a binder, which then
becomes the office record for the day. A similar binder is to be used for the
monthly record.
The traffic information which is recorded by the teletypewriter is kept by
the traffic department.
Defective Packages
The routine outlined in Specification X-63941 for handling defective packages
should be followed.
12.3 MAINTENANCE
Switching
The ESS has a built-in self-checking feature for all common-control circuits.
Line and trunk circuits must be checked periodically to ensure that they are
in working order. The heart of the self-checking feature is the matching circuits
in the two central control circuits.
The first mismatch causes an error signal to be printed with a record of the
equipment in trouble. A second mismatch causes a fault-checking test to
determine whether the active circuit or the stand-by circuit is in trouble. If
the active circuit is in trouble, the system places the stand-by circuit in control.
Then it starts a test on the circuit in trouble to locate the defective or faulty
package. In some cases, several packages may have to be replaced to find the
defective one.
Sec. 12.3 Maintenance 319
The parts of the signal distributor, scanner, and switching networks that
affect only one line or trunk are not duplicated, as failures in such parts should
not affect a group of equipment. The address equipments of the scanner, the
signal distributor, and the marker are duplicated, however, as trouble here
would involve a large number of customers. The duplicate equipment is matched
continuously, and an automatic transfer takes place under trouble conditions.
A diagnostic routine establishes the source of the trouble as one of several
packages in one limited area of the circuit.
The dictionary is used to interpret all teletypewriter messages. The trouble
record, when decoded, directs you to the cabinet and the specific location
within the cabinet where you will find the packages that include the defective
or faulty one. When you have replaced the specified packages, an order to the
teletypewriter requests a test of the major unit. If the test is successful, the
major unit is restored to the stand-by condition.
You must replace promptly any major unit that is in trouble, as a second
failure may affect service.
Ringing and Tone
The transfer of ringing supply units cannot be done by teletypewriter orders,
as programmed transfers cannot be made for these units.
The ringing and tone supply units have their own checking circuits. Unit
is the preferred unit. It is always in operation unless it develops trouble; when
this occurs, operation is transferred automatically to unit 1 . If unit 1 develops
two troubles and unit has only one trouble, operation is automatically
transferred to unit 0.
You also can use the manually-operated transfer key to put unit 1 in service
and to keep unit out of service. Don't leave this key operated after you have
finished work on unit 0, as the automatic transfer of the units is inhibited
while the key is operated.
Chapter 13
The Ringing and Tone Supply
Several different tones are needed to indicate the status of a call in any dial
telephone system. The ESS uses transistor oscillators to generate such tones.
A group of binary counters provides the interruption signals. These are mixed
with the tones in gated amplifiers to produce interrupted tones. The tone output
leads are distributed throughout the switching networks for access by the system.
13.1 EQUIPMENT ARRANGEMENTS
The ringing and tone supply cabinet, designated RT, consists of two
bays, a front (gate) bay and a rear bay. The front bay (see Fig. 13-1) contains
ringing and tone supply and its rectifier units. It also contains all lamps and
equipment common to both supply and supply 1. The rear bay (see Fig. 13-2)
contains ringing and tone supply 1 and its rectifier units.
13.2 METHOD OF OPERATION
Tone Generators— Figs. 13-3 and 13-4
Twelve transistor oscillators supply the tone signals for the ESS. Their
frequencies range from 430 cycles per second to 1,000 cycles. Eight of these
oscillators (see Fig. 13-3) supply the ringing tones. The remaining four (see
Fig. 1 3-4) are wired as two pairs, the output of each pair being a combination
of two frequencies. These supply the audible ringing tone, the dial tone, the
reorder tone, and the busy tone.
Interruption Timing— Fig. 13-5
The interruption timing supply consists of a group of binary counters and
amplifiers. It converts 1000-cycle sine-wave current to 1000-cycle square-wave
current. The square-wave current is used to trigger the binary counters. The
outputs of the counters are: 12.5 pps (pulses per second), 15 ipm (interrup-
tions per minute), 120 ipm, 60 ipm, and 62.5 ipm. Some of these outputs are
320
Sec. 13.2 Method of Operation 321
combined; all are amplified. The outputs of the NIG amplifiers (see Fig. 13-5)
are: 12.5 pps; 15 ipm and 12.5 pps; 15 ipm; 120 ipm; 60 ipm; and 12.5 pps
and 62.5 ipm. The outputs of the IG amplifiers are used for the synchronizing
signals to the central control.
Dial Tone— Fig. 13-4
The dial tone (a steady tone) is a combination of two frequencies, 560 cycles
and 690 cycles. It is supplied to fifteen tone points in the distribution switch-
ing network.
Busy Tone— Fig. 13-4
The busy tone is a combination of two frequencies, 560 cycles and 690 cycles,
interrupted at a rate of 60 ipm (0.5 second on, 0.5 second off). It is supplied to
fifteen tone points in the distribution switching network.
Reorder Tone— Fig. 13-4
The reorder tone is a combination of the same two frequencies, 560 cycles
and 690 cycles, interrupted at a rate of 120 ipm (0.3 second on, 0.2 second off).
It is supplied to fifteen tone points in the distribution switching network.
Audible Ringing Tone— Fig. 13-4
The audible ringing tone is a combination of two frequencies, 430 cycles and
454 cycles, interrupted at a rate of 15 ipm (2 seconds on, 2 seconds off). It is
supplied to five tone points in the signal switching network.
Ringing Tones— Fig. 13-3
The ESS serves eight-party lines on a selective ringing basis. Therefore it
needs eight different frequencies of ringing tones. Each ringing tone is a single-
frequency tone pulsed at 12.5 pps and interrupted at a rate of 15 ipm (2 seconds
on, 2 seconds off): The eight tones are supplied to forty tone points in the
signal switching network.
Revertive Ringing Tones— Fig. 13-3
Since the ESS serves two-party and eight-party lines, it needs ringing tones
for reverting calls. These tones are single-frequency tones pulsed at 12.5 pps
and interrupted at a rate of 62.5 ipm (0.48 second on and 0.48 second off).
The revertive ringing tones are supplied to eight tone points in the signal
switching network.
On the first ringing cycle, 0.96 second, the called party ringing tone is con-
nected to the line. On the second ringing cycle, the called party ringing tone is
322
The Ringing and Tone Supply
Chap. 13
SUPPLY "0" RELAYS
A.",«J
SUPPLY "0'
RECTIFIER UNITS
-'■• :- '•'
COMMON RELAYS
SUPPLY "0" FUSES
SUPPLY "0"
CAPACITORS
{
iid#ddt#9@i # d & • • • I
}
>
COMMON LAMPS
— COMMON FUSES
SUPPLY "0"
VOLTAGE ADJUSTORS
RELEASE KEY
SUPPLY "0"
CIRCUIT PACKAGES
y AND
COMMON CIRCUIT
PACKAGES
VG 1301
FIG. 13-1. Ringing and tone supply cabinet, front view of front bay (gate).
Sec. 13 . 2 Method of Operation 323
disconnected and the calling party ringing tone is connected. This alternating
of the ringing tones for the called party and the calling party is continued until
the called party answers, or until the connection times out and releases.
Local Test Cabinet Tones— Fig. 13-3
Eight tones are used by the ESS local test cabinet. Each tone is a single-
frequency tone pulsed at 12.5 pps. These tones are supplied over eight leads to
the local test cabinet.
CGS Signaling Tones— Fig. 13-3
Three steady tones (656 cycles, 810 cycles, and 1000 cycles) are needed for
CGS signaling in the ESS. These tones are supplied to a maximum of fifteen
indicator signaling trunks.
Alert Tones— Fig. 13-3
A steady tone of 591 cycles is used for the alert tone. It is supplied to twenty
tone points in the distribution switching network, and to ten leads to the
CGS auxiliary line circuits.
Synchronizing Signals— Fig. 13-5
Certain functions performed by the central control must be synchronized
by signals from the interruption timing circuit. Twenty such synchronizing
signals are supplied to the central control via the stand-by transfer.
Figures 13-2 through 13-5 are shown on pages
324 through 327. The text of Section 13.3,
Duplication and Transfer, starts on page 328.
324
The Ringing and Tone Supply
Chap. 13
RINGING & TONE J
SUPPLY »** ~\
• ■ • 11 1.
SUPPLY »0"
RECTIFIER UNITS
RINGING & TONE
v SUPPLY »0»
> AND EQUIPMENT
COMMON TO
SUPPLIES *0*fc"M*
VG 1302
FIG. 13-2. Ringing and tone supply cabinet, rear views of front bay (gate) and rear bay.
Sec. 13 . 2
Method of Operation
325
RINGING TONES
2 SEC ON, 2 SEC OFF
FROM
INTERRUPTION -<
TIMING SUPPLIES
0MR/1MR
OSR/ISR
.1 000-^(0)-
I000~(1)
TRANSFER
RELAYS
rEP
-^7
0T-/1T-
-7)A0
VDAC
R(0-7)A<
R(0-7)A2
R(0-7)A3
R(0-7)A4
REVERTING RINGING TONES
0.48 SEC ON, 0.48 SEC OFF
-X-
0T-/1T-
171 Bia=zig . to
SSN
CGS SIGNALLING TONES
STEADY
VDAC
3,5,7
T*
0T-/1T- 1 L p L„ R ( 3 ' 5 '
R(3, 5, 7)D0
LP
R(3, 5, 7)D1
—J LP V
R(3,5, 7)D2
, 7)D3
| R(3, S,7)D4
ALERT TONES
STEADY
"X"
0T-/IT-
0CR/1CR
DSN DISTRIBUTION SWITCHING NETWORK
SSN SIGNAL SWITCHING NETWORK
1ST INDICATOR SIGNAL TRUNK
VDAC VOLTAGE DETECTOR A-C
LP. RESISTANCE LAMP
GT GATED AMPLIFIER
OSC OSCILLATOR
R RESISTOR
HT (0-9)
•t{T}-
AT(0-9)
ATpO-19)
0T-/tT-
-* — r
TEST CABINET TONES
STEADY
-*-
R(0-7)B
OT -/IT-
FIG. 13-3. Ringing tone supply, block diagram.
TO
DSN
TO
AUX
LINE
CKT
FOR
CGS
TO
TEST
CAB
326
The Ringing and Tone Supply
Chap. 13
FROM
INTERRUPTION y
TIMING
SUPPLIES
TRANSFER
RELAYS AUDIBLE RINGING TONE
I 2 SEC ON, 2 SEC OFF
Y
— _
OT-/IT-
? \
, „ JR8A(0-4) TO
l-P — -SSN
DIAL TONE
STEADY
^— f V
0T-/1T-
DT (00-14) TO
— * 1 *
0T-/IT-
REORDER TONE
0.3 SEC ON, 0,2 SEC OFF
RT(00-14J TO
**DSN
BUSY TONE
0.5 SEC ON, 0.5 SEC OFF
0BT/1BT
>< r — f
0T-/1T-
| BT(00-14) TO
""DSN
DSN DISTRIBUTION SWITCHING NETWORK
SSN SIGNAL SWITCHING NETWORK
VDAC VOLTAGE DETECTOR A-C
LP RESISTANCE LAMP
GT GATED AMPLIFIER
OSC OSCILLATOR
R RESISTOR
FIG. 13-4. Tone supply, block diagram.
Sec. 13 . 2
Method of Operation
327
BC
250 PPS
H
T. TRIGGER AMPLIFIER
BC BINARY COUNTER(S)
NIG NONINVERTING GATE
IG INVERTING GATE
VDP VOLTAGE DETECTOR -PULSE
1000MO)/
62.5 PPS
016 SEC ON
064 SEC OFF
BC
12.5 PPS
30 IPM
15 IPM
BC
120 IPM
|\ RNGSOO/RNGS 10
iG^>=sr-
1
VDP
RNGS01/RNGS 11
12.5 PPS
15 IPM & 12.5 PPS
2 SEC ON
2 SEC OFF
IG
_LV
RTAOO/RTAIO
RTA01/RTA11
120 IPM
0.3 SEC ON
0.2 SEC OFF
S
|\ RDRT00/RDRT10
VDP
RDRT01/RDRT11
60 IPM
5 SEC ON
0.5 SEC OFF
|\ BSYT00/BSYT1O
BC
1_
VDP
NIG>
BSYT01/BSYT11
62 5 IPM & 12.5 PPS
0.48 SEC ON
0.48 SEC OFF
1000^(1)
0CR/1CR
0MR/1MR
OAR/1 A R
0RT/1RT
TO
>- TONE
SUPPLIES
0BT/1BT
TO
V RINGING TONE
SUPPLIES
0SR/1SR
IG^
_K
SROO/SRIO
■TO CENTRAL CONTROL VIA ST
SR01/SR11
FIG. 13-5. Interruption timing supply, block diagram.
328 The Ringing and Tone Supply Chap. 13
13.3 DUPLICATION AND TRANSFER
Duplicate interruption timing supplies, tone supplies, and ringing tone
supplies assure the ESS of tones in case the preferred supply should fail com-
pletely. The tone amplifiers for the local test cabinet are not duplicated, however.
Automatic transfer from supply to supply 1 occurs whenever supply
develops a trouble condition that is more serious than the trouble (if any) in
supply 1. Automatic transfer from supply 1 to supply occurs when supply 1
develops a trouble that is equal to or more serious than any existing trouble
in supply 0.
Manual transfer may be made at the administration center. However, since
the manual transfer overrides an automatic transfer, the manual transfer key,
RTS0/RTS1, should be kept operated no longer than needed. Manual transfer
is indicated at the ringing and tone supply cabinet by the lighted green lamp
MAN. The supply in service is indicated by the lighted green lamp or 1.
13.4 POWER
The power for the ringing and tone supply cabinet is supplied on a-c
power buses B and C (see Fig. 1-18 in Chapter 1), and on d-c power buses B
and C (see Fig. 1-19).
The d-c power bus B supplies power to ringing and tone supply 0; bus C
supplies power to supply 1. The d-c power is used to operate relays. A failure
on either d-c power bus may cause an automatic transfer. However, there will
be no break in the tone supply to the ESS.
The a-c power bus B supplies power to the rectifier units in ringing and tone
supply 0; bus C supplies power to the rectifier units in supply 1. There are two
rectifier units, — llv and +12v, in each supply.
Although the rectifier units are duplicated, there is no way to transfer their
outputs. Therefore, the outputs of the two —llv rectifier units are joined by
fuse CI, and the outputs of the two +12v rectifier units are joined by fuse C2.
By paralleling the outputs, the in-service ringing and tone supply is assured of
power regardless of which rectifier unit, in a pair, may fail. This arrangement
also assures power when either a-c power bus fails.
Sec. 13 . 5 Maintenance 329
13.5 MAINTENANCE
Maintenance on the in-service ringing and tone supply is not necessary,
because of duplication of the equipment, Lamps on the front bay will help you
in locating any trouble that occurs. The details of trouble analysis and trouble-
shooting are covered in Specification X-63952. The voltage of the outputs of
the rectifier units is checked periodically by the voltage monitor in the adminis-
tration center.
Chapter 14
Power Distribution
The electrical power to operate ESS equipment is distributed to the various
cabinets via the power distribution cabinet. This cabinet is located with the
switching equipment. It is the power control and distribution center for the ESS.
14.1 EQUIPMENT ARRANGEMENTS
The power distribution cabinet consists of one bay of equipment, desig-
nated PD-0; a front view of the cabinet is shown in Fig. 14-1, and a rear view
in Fig. 14-2.
The upper half of the bay contains equipment for distributing the a-c power
via the A, B, and C buses. A-C meters are provided for measuring frequency,
power, current, and voltage on each of the three buses. Below the meters are
three rows of circuit breakers and their associated toggle switches, one row for
each bus. Three neon power-on lamps indicate, when lighted, that power is on
each bus. The red alarm lamp lights when a circuit breaker operates to indicate
an overloaded circuit. The green guard lamp, when lighted, indicates that a
circuit breaker alarm circuit toggle switch is operated. The toggle switch is
used for two purposes: (a), to retire the alarm brought in when the circuit
breaker operates electrically; and (b) to prevent bringing in an alarm when the
circuit breaker is manually operated to OFF.
The lower half of the bay contains equipment for distributing the d-c power
via another set of A, B, and C buses. D-C meters are provided for measuring
current and voltage on each of the three buses. Below the meters are three rows
of fuses, one row for each bus. Three white power-on lamps indicate, when
lighted, that power is on each bus. The red alarm lamp lights when a fuse
blows to indicate an overloaded circuit. The green guard lamp, when lighted,
indicates that a fuse has blown and the guard feature has not been reset. When
the blown fuse has been removed, the alarm lamp is extinguished; however,
the guard lamp remains lighted until the reset button is operated.
330
Sec. 14 . 2 Method of Operation 331
14.2 METHOD OF OPERATION
14.2. 1 AC Power Distribution— Figs. 14-1, 14-3
Alternating current of 230 volts is supplied over the A, B, and C bus
leads from the ESS power plant. Each bus lead is connected to a horizontal
bus bar on the power distribution cabinet. Each "hot" bus bar has an associ-
ated ground bus bar. Each pair of bus bars serves up to twenty circuit breakers
(CB-). Each circuit breaker has an associated toggle switch (s-). Three neon
lamps, BUS A, BUS B, and BUS C, are lighted when a-c power is being supplied
to the bus bars.
When an a-c circuit is overloaded, the circuit breaker operates to cut off the
overloaded a-c circuit and to close a shunting circuit (through the associated
toggle switch) around the winding of the normally operated Kl relay. This
releases relay Kl, which closes a circuit to light the 230 VOLTS AC ALARM
lamp. Now operate the toggle switch to light the 230 VOLTS AC GUARD
lamp, and to extinguish the AC ALARM lamp. After the overload has been
removed, you can return the circuit to service by operating the circuit breaker
manually to ON.
When you have verified the absence of the overload, restore the toggle switch
to extinguish the AC GUARD lamp.
14.2.2 D-C Power Distribution— Figs. 14-1, 14-3
The —48 volts d-c power is supplied over the A, B, and C bus leads
from the No. 5 crossbar office battery supply. Each bus lead is connected to a
horizontal bus bar on the power distribution cabinet. Each bus bar serves up
to 22 fuses. Three lamps, BUS A, BUS B, and BUS C, are lighted when d-c power
is being supplied to the bus bars.
When a d-c circuit is overloaded, the fuse blows and closes the circuit
to light the 48 VOLTS DC ALARM lamp. It also operates the K2 relay, which
locks and lights the 48 VOLTS DC GUARD lamp.
When you remove the blown fuse, the DC GUARD lamp remains lighted,
but the DC ALARM lamp is extinguished. After the circuit overload has been
removed, you can return the circuit to service by installing a new fuse.
When you have verified the absence of the overload, momentarily operate
the 48 VOLTS DC GUARD RESET key to release the K2 relay and extinguish
the DC GUARD lamp.
The three figures for Chapter 14 are shown on pages 332, 333, and 334.
332
Power Distribution
Chap. 14
CYCLES 56-64
s
230 V A-
A
-c
^
-1
BUS
A
O
BUS
B
O
BUS
C
O
GUARD ALARM
O O
A-C
METER
TRFR
BUS
A» •
BUS B
OFF •
^
• BUS
C
S
CIRCUIT BREAKERS -
CIRCUIT BREAKER ALARM
CUT-OFF TOGGLE SWITCHES
AMPERES 0-60-
48V D-C
A
V.
BUS BUS BUS ALARM
ABC GUARD ALARM RESET
o o o o o o
D-C METER TRFR
BUS A • • BUS B
OFF • • BUS C
HBfifi
KILOWATTS 0-30
- AMPERES 0-100
— VOLTS 0-300
AC BUS A
AC BUS B
AC BUS C
VOLTS 0-75
> FUSE PANELS
FIG. 14-1. Power distribution cabinet, front view.
Chap. 14
Power Distribution
333
A-C METERS
BUS SEL SWITCH
230 VOLT A-C
BUS BARS
A-C METERS
BUS SEL SWITCH
D-C METER
A-C GRD
BUS BARS
D-C METER
D-C BUS BARS
VG 1402
FIG. 14-2. Power distribution cabinet, rear view.
334
Power Distribution
Chap. 14
CIRCUIT
"BREAKERS
TO ESS
POWER -<
PLANT
TO
LOAD
AC GRD BUS BAR "A"
AC BUS BAR "B"
AC BUS LEAD"B
AC GRD BUS BAR "B"
AC BUS BAR "C"
AC BUS LEAD"C"
TO
LOAD
TO
,-LOAD
TO
»LOAD
TO NO.5
CROSSBAR
POWER
PLANT
TOGGLE
SWITCHES")
GUARD
(GREEN)
_l r r^
— | DCB
TO ALARM CIRCUIT
| VW — '
DC GUARD RESET
KEY (NON LOCKING)
DENOTES RELAY
CONTACTS
FIG. 14-3. A-C and D-C power distribution.
Chapter 15
The Alarm System
The ESS has an alarm system that indicates trouble conditions when they
occur within the cabinets and in the power plant. Some of the alarms are brought
in directly from the equipment in trouble; others are brought in when troubles
are detected during the system fault-checking routine. All of these alarms give
a visible and audible signal; and in most cases the teletypewriter prints a
trouble record.
The alarm lamps are located at the cabinets, at the end of the line-up of
cabinets, and at the administration center. The audible signals are located at
strategic points in the office.
The alarm system includes two fire-wire loops. A failure in either of these
loops causes an emergency alarm to be sounded. One fire-wire loop is installed
in the network cabinets; a failure in this loop will turn off the network cabinet
air-conditioning blower fan and sound the emergency alarm. The second fire-
wire loop is installed in the other ESS cabinets; a failure in this loop will turn
off the room air-conditioning blower fans and sound the emergency alarm.
The alarm keys, lamps, and associated equipment are located at the adminis-
tration center. The lamps indicate which equipment is in trouble and which
equipment is in service. The keys are used to release and group the alarms.
Some of the keys are used to control the cabinet air-conditioning equipment.
A major audible alarm indicates troubles that require immediate attention.
It is given by a loud-sounding single-stroke tone bar. A minor audible alarm
indicates troubles of lesser importance. It is given by a loud-sounding bell.
Power plant failures are indicated by a loud-sounding gong. The emergency
alarm is a loud-sounding horn.
The ESS maintenance center is located at the administration center. However,
by operating the alarm grouping key (AG), the ESS alarms can be switched to
335
336
The Alarm System
Chap. 15
3 CL
SWITCHBOARD
ZONE 2-1
EMERGENCY ALARM
SD-90437-01
ALARM SENDING
E
ALARM RECEIVING
SD-95418-01
OFFICE ALARM
SD-25671-01
m
H
H
H
MISCELLANEOUS ESS ALARM
LAMPS AT 3CL SWITCHBOARD
ALARM TRANSFER
ES-1A066-01
CONTROL AND
ES-1A045-01
NDICATING
ESS AUDIBLE ALARMS
FIG . 15-1. Floor layout of alarm systems and alarm zones.
the No. 5 crossbar maintenance center, which is located at the master test frame.
The operation of the AG key also permits the ESS alarm lamps to be lighted at
both the administration center and the 3CL switchboard.
Coded audible signals are used to identify the zone in which an emergency
alarm exists in the ESS and the No. 5 crossbar system. Exit pilot lamps are
located on each floor. The floor layout of both alarm systems and the alarm
zones are shown in Fig. 15-1.
Chap. 15
The Alarm System
337
AREA LIGHTED --
TRANSLUCENT DESIGNATION STRIP
i 1 i 1 i j i 1 i i i i i i
TLO TLI OSM MV TMB EXP OCD
130V D
MN MN
I 1 I 1
SCT
MJ
AR
MN
AR
PF
AR
DCG ACG
ALT
MN
^^
^
^
ALT
MJ
PDF NAF NVF NVA NVB NVC
MJ MJ
1 1
VMR
TRANS
i — -\
i i
FA
1 i
AT
1 i
RSF
DNS
i 1
i i
DNF
1
, ,
ABS
i i
NTL
i 1
,
NTH
AA
Q
) " J
T— T
1
RESET
ALARM LAMPS MOUNTED BEHiN0 DOTTED AREAS
VG 1502
FIG . 1 5-2. Trouble-indicating lamps and control keys at the administration center.
The ESS trouble-indicating lamps and the control keys are located at the
administration center; they are arranged in a panel, as shown in Fig. 15-2. The
function of each lamp and key is given in the list on pages 338 through 341,
which follows the order shown on the designation strips.
338 The Alarm System Chap. 15
Top Lamp Strip
TLO ) TEST LAMPS. These lamps light to indicate the state of a particular
TLlj spot in the barrier grid tube: i. e., to show whether the spot is a
"zero" or a "one."
OSM (*) ONE-SPOT MONITOR. This lamp lights whenever a particular signal
that is being read by the system is a "one." This signal may be
a flip-flop output, a scanner point, or a particular spot in a barrier
grid tube.
MV (*) MARGINAL VOLTAGE. This lamp lights whenever a marginal
voltage test is being made in the system.
TMB (*) TRUNK MADE BUSY. This lamp lights when any trunk in the
system has been "made busy" by means of the teletypewriter.
EXP (*) EXPOSURE CONTROL. This lamp lights to indicate the operation of
the shutters in the FSS when the plates are being prepared.
OCD OPEN CABINET DOOR. This lamp lights when any cabinet door
in the system is opened.
130V 130-VOLT MINOR ALARM. This lamp lights when the 130-volt d-c
MN
battery voltage varies from the voltage limits of the floating charge.
D DIESEL POWER MINOR ALARM. This lamp lights to indicate that
MN
power is being supplied by the emergency diesel power plant.
Second Lamp Strip, and the Keys below the Lamps
SCT SECOND TROUBLE. This lamp lights when a second trouble exists
in the system. This occurs when a stand-by unit is in trouble at the
same time that its in-service duplicate unit is in trouble.
MJ MAJOR ALARM. This lamp lights when a trouble in the system
requires immediate attention.
MJ (key) MAJOR ALARM RELEASE. This nonlocking key, when operated,
silences the major tone bar, but does not extinguish the lamp.
After a fixed interval, the ESS program causes the lamp to be
AR
♦These lamps are monitors; no audible alarm is given when any of these lamps is lighted.
Chap. 15 The Alarm System 339
extinguished, provided no other major alarm condition occurs
during the interim period.
MN MINOR ALARM. This lamp lights to indicate the presence of a
trouble not of major importance.
MN (key) MINOR ALARM RELEASE. This nonlocking key, when operated,
AR
silences the minor alarm bell.
PF POWER FAILURE. This lamp lights when any of the major
power alarms indicates a failure.
PF (key) POWER FAILURE ALARM RELEASE. This nonlocking key, when
AR
operated, silences the PF alarm gong.
DCG DIRECT-CURRENT GUARD. This lamp lights when a fuse blows
in the power distribution cabinet. A D-C Guard Reset key (non-
locking) in the power distribution cabinet must be operated after
replacing the fuse. This will re-activate the alarm system and
extinguish the DCG lamp.
ACG ALTERNATING-CURRENT GUARD. This lamp lights when a circuit
breaker opens. Whenever a circuit breaker is open, the switch
below the circuit breaker must be operated manually to the
opposite position. This action allows the remaining circuit
breakers to function with the alarm system.
AG (key) ALARM GROUPING. This locking key, when operated, causes the
ESS alarm system to be switched to the No. 5 crossbar alarm
system, and the ESS alarm lamps appearing at the administration
center to be switched to the 3CL switchboard.
ALT ALTERNATOR MINOR ALARM. This lamp lights (1), when a
high-output or a low-output voltage condition exists; or (2),
when there is a transfer of the motor drive from a regular unit
to a stand-by unit.
FCT FAN OR COMPRESSOR TRANSFER. This lamp lights (1), when
the motor of either the network or the room air-conditioning fan
is transferred to the stand-by unit; or (2), when the regular or
stand-by compressor fails.
340 The Alarm System Chap. 1 5
Third Lamp Strip
ALT ALTERNATOR MAJOR ALARM. This lamp lights (1), when any
alternator fuse blows; (2), when an alternator fails; or (3), when
an a-c drive motor fails.
MJ
PDF POWER DISTRIBUTION FAILURE. This lamp lights when a circuit
breaker opens, or when a fuse blows in the power distribution
cabinet.
NAF NO AIR FLOW. This lamp lights when no air flows in the switching
network or room air-conditioning ducts.
NVF NO VOLTAGE FAILURE. This lamp lights when one or more of
the fuses supplying the "no voltage" relays (NVA, NVB, or NVC)
has blown.
NVA NO VOLTAGE A BUS. This lamp lights when there is no voltage
on the— 48v A bus.
NVB NO VOLTAGE B BUS. This lamp lights when there is no voltage
on the— 48v B bus.
NVC NO VOLTAGE C BUS. This lamp lights when there is no voltage
on the— 48v C bus.
130V 130- VOLT MAJOR ALARM. This lamp lights when the 130-volt d-c
MJ
battery voltage varies from the high or low voltage limits.
D DIESEL POWER MAJOR ALARM. This lamp lights when the diesel
power plant is called to start.
Fourth Lamp Strip, and the Keys below the Lamps
VMR VOLTAGE MONITOR REFERENCE. This lamp lights to indicate
that the normally in-service reference voltage supply unit has
failed, and that the stand-by unit has been switched into service.
VMR (key) VOLTAGE MONITOR REFERENCE TRANSFER. This nonlocking
TRANS
key is used to transfer the operation from the normally in-service
reference voltage supply unit to the stand-by unit.
RESET (key) RESET. (See VMR lamp and VMR TRANS key above.) This non-
locking key is used to reset or transfer the operation from the
Chap. 15 The Alarm System 341
stand-by reference voltage supply unit back to the unit that is
normally in service.
FA FUSE ALARM. This lamp lights when a fuse blows, when a circuit
breaker opens, or when the power is turned off in a major unit
power cabinet.
AT AIR TEMPERATURE. This lamp lights when the air temperature in
a particular cabinet rises above 105° F.
RSF ROOM SUPPLY FAN. This guard lamp lights when the RSF key (see
below) is operated to control the air-conditioning fans.
RSF (key) (See RSF lamp above.) This locking key is used to control the
air-conditioning fans if the fire-detection wire opens from a
cause other than a fire.
DNS DISTRIBUTION NETWORK SHUTOFF. This guard lamp lights
when the DNS key (see below) is operated to shut down the fan
when testing is required in the switching network cabinets.
DNS (key) (See DNS lamp above.) This locking key is used to shut off the
fan in the switching network cabinets.
DNF DISTRIBUTION NETWORK FAN. This guard lamp lights when the
DNF key (see below) is operated to control the air-conditioning
fans.
DNF (key) (See DNF lamp above.) This locking key is used to control the
air-conditioning fans if the fire-detection wire opens from a cause
other than a fire.
ABS ALARM BATTERY SUPPLY. This lamp lights when an alarm
battery fuse blows.
NTL NETWORK TEMPERATURE LOW. This lamp lights when the
temperature in the network cabinets is less than 74° F.
NTH NETWORK TEMPERATURE HIGH. This lamp lights when the
temperature in the network cabinets is above 74° F.
AA (key) ADVANCE ACTIVATOR. This non-locking key is used to start
certain programs within the system after instructions have been
inserted by means of the teletypewriter.
Chapter 16
Customer Group Service and
Bridged Extension Service
Customer Group Service, or CGS, is the term used in the electronic switching
system for PBX, wiring plan, and key telephone services.
With CGS, the customer lines terminate directly in the ESS in the Morris
central office. Calls to and from these lines are switched automatically in the
ESS. This differs from other systems in which the calls for service of this type
are switched on the customer premises, either automatically or by an attendant
there. All incoming calls to ESS customers having CGS can be completed
automatically by direct inward dialing.
Customer group service is furnished by the ESS on either an attended or an
unattended basis, as described in Sections 16.1 and 16.2 below.
Bridged Extension Service in the ESS includes a new feature not available in
any of the present dial telephone systems. It permits a customer having exten-
sion telephones to dial a call to another extension on his line. This feature,
which is available to individual and party-line customers for business or resi-
dence service, is described in Section 16.3.
16.1 UNATTENDED CGS
Members of an unattended CGS group may call each other by dialing
a two-digit or three-digit code, or a seven-digit directory number, as described
in subsection 16.1.1. Unattended CGS also provides facilities for "add-on,"
"hold," and "pick-up" features.
76 . 7 . 7 Method of Operation
Calls to customers or operators outside the CGS group can be made
in the usual manner from any station in the group by dialing a seven-digit
342
Sec. 16.1 Unattended CGS 343
directory number, a three-digit service code, or the "zero" operator code.
Additional telephone functions that are available in an unattended CGS
installation are outlined in the following paragraphs.
CGS Line Connections
The lines served by CGS have "class of service" indications to identify them
in the ESS. Special translation features indicate which line is associated with
each station number. The lines within a CGS group may call each other in
either of two ways: (1), by dialing the digit "1" followed by the CGS station
number; or (2), by dialing the seven-digit directory number associated with the
called station.
"Add-On"
Another station can be added to an established connection by dialing the
digit "1" followed by the number of the station to be added. The "add-on"
station may be within the CGS group, or it may even be an external station
obtained by dialing a seven-digit directory number, a three-digit service code,
or the "zero" operator code. The indications received on a call of this kind are
listed in Table 16-1, on page 344.
"Hold"
An established CGS connection can be held by dialing the digit "2." The
held connection can be recalled later by dialing the digit "1" followed by the
CGS station number from which the holding "2" had previously been dialed
(your own number).
"Pick-Up"
A call coming in to any station in a CGS group can be picked up by another
station within the group by dialing the digit "3" followed by the digit "1" and
the number of the station that is being rung.
16.2 ATTENDED CGS
In attended CGS installations, an attendant's set is provided on the
customer premises to handle calls that are not completed automatically by
direct inward dialing. Also, certain outgoing calls will require the service of an
attendant. There are two systems for signaling the attendant's telephone set:
an audible system and a visible system. The signals to the attendant for each
344 Customer Group Service and Bridged Extension Service Chap. 16
TABLE 16-1. INDICATIONS RECEIVED ON "ADD-ON" CALLS
THE
STATION TO BE ADDED IS
Encountered
Within the ESS office
"Zero" Operator
Outside of the ESS office
Called station
is busy
2 busy tones
—
A 591 -cycle tone
for V4 to Vi second
All circuits or
paths are busy
4 reorder tones
4 reorder tones
A 591 -cycle tone
for Va to '/i second
Called station
does not answer
A 591 -cycle tone
for V* to '/i second
—
A 591 -cycle tone
for Va to Vi second
TABLE 16-2. VISIBLE AND AUDIBLE SIGNALS TO THE CGS ATTENDANT
Illuminated
Designation
Spoken
Announcement
Meaning
ALERT
(A steady tone)
Action required on a waiting call.
INC
"Incoming"
A new call from outside the CGS.
BUSY
"Busy"
The called CGS station is busy.
READY
"Ready"
A CGS station formerly busy becomes idle, and is now
being held for connection to a waiting call.
DA
"No Answer"
An idle CGS station has not answered after 45 seconds
of ringing.
STA
"Station"
A new call from a station within the CGS; a call from a
tie line associated with the CGS; or a recall from an
established connection.
REORD
"Try Again"
The CGS attendant should redial a call just dialed, since
a condition of "trunk busy" or "paths busy" was en-
countered on the previous dialing.
Note: The codes dialed by the CGS attendant for service connections are shown in Table 16-3.
Sec. 16.2 Attended CGS 345
system are listed in Table 16-2. The codes to be dialed by the CGS attendant
are described in Table 16-3, on page 346.
16 . 2 . 1 Equipment Arrangements
When the CGS attendant's set is to be signaled on the visible basis,
an auxiliary line circuit is required for each CGS attendant's telephone set
[see Fig. 16-2 and (a) of Fig. 16-1]. The auxiliary line is connected in series
with the conductor loop to the attendant's telephone set. In addition, a lamp
control circuit, shown in Fig. 16-4 on page 350, is required in the attendant's
telephone set to give lamp indications. A second pair of conductors is needed
for this function.
When the CGS attendant's set is to be signaled on the audible or "announce-
ment" basis [see (b) of Fig. 16-1], duplicate announcement systems are pro-
vided (one regular and one stand-by), as shown in Fig. 16-3. The repertory of an-
nouncements consists of: "Incoming," "Busy," "Ready," "No Answer,"
"Station," and "Try Again." These announcements are connected to the line
through the announcement trunk on the distribution switching network in
the ESS.
Each announcement cabinet contains a motor-driven magnetic drum with
eight tracks as shown on Fig. 16-3. Facilities are provided for recording and
monitoring on the magnetic drums.
Both machines operate continuously. If the first machine fails, the second
machine is connected automatically without interruption of service.
16 . 2 . 2 Method of Operation
Calls to customers or operators outside the CGS group can be
made in the usual manner without the assistance of the CGS attendant by
dialing a seven-digit directory number, a three-digit service code, or a "zero"
operator code. If assistance is required, the CGS attendant may be signaled
by dialing the digits "10".
Calls from one CGS station to another station within the same group may
be made by dialing the digit "1" followed by the one-digit, two-digit, or three-
digit station number of the called station. (Such a dialing sequence is known as
346 Customer Group Service and Bridged Extension Service Chap. 16
TABLE 16-3. CODES DIALED BY THE CGS ATTENDANT
Code
Connection Requested
(a) Connect to the "zero" operator, (b) Flash the toll operator.
To answer an "alert" signal.
Hold the present connection.
Pickup; to be followed by "1 " X* of the CGS station being picked up.
(a) Check a busy CGS station every 10 seconds for "busy;"
if "busy" for 30 seconds, alert the attendant.
(b) Continue ringing for another 45 seconds on "no answers."
(c) Connect the attendant, the "zero" operator, and a station to a
conference trunk ("0" call).
(d) Connect a call to a previously busy CGS station.
(e) Connect a call to a CGS station (station off-hook).
'10"
Return to a "hold" connection. Relight the lamp or repeat the
announcement just sent.
'11'
Disconnect on a call
'1"X*
(a) Connect to or transfer a call to a CGS station.
(b) On "0" operator calls, permits a double connection in order
that a call may be announced. (Requires that the CGS
attendant dial "11" to be disconnected.)
X*"ll"
Connect to a service code, X* "1 1."
ABX-XXXX*
Connect to, or transfer, a call to a directory number.
"5583"
Close the attended CGS, and set up the night connections
(followed by a dialed list of night numbers).
"5584"
To open an attended CGS and to release the night connections.
"5585"
To close an attended CGS and to set up the night connections
from a prearranged list.
"559"
Tie-line preference code.
"5999"
To close an attended CGS because of a lamp signal failure,
or other failure.
"598"
To open an attended CGS which was closed because of a lamp
signal failure or other failure, which has now been cleared.
*The letter "X" repres
ents an unstated number.
Sec. 16.2
Attended CGS
347
a "IX" call, where the "X" represents any number of one, two, or three digits.)
Where an associated group station service is provided within a large attended
CGS, an intragroup call may be made by dialing a "IX" number, where "X"
represents a one-digit private number within the group.
On calls within an attended CGS, an audible ringing signal is received by the
calling station, and tone ringing is sent to the called station.
If the called CGS station is busy, the calling station receives a busy tone,
which is a combination of two audible frequencies interrupted at a rate of 60
ipm. If the call can not be completed because all circuits or paths are busy, the
calling station receives a reorder tone, which is a combination of two audible
frequencies interrupted at a rate of 120 ipm. If the called station does not
answer, ringing is continued until the calling station hangs up or until a period
of five minutes has elapsed, whichever occurs first. If it is desired to ring the
.CONDUCTOR LOOP
CUSTOMERS PREMISES
ATTENDANTS TELEPHONE SET
L
FTT
LAMP CONTROL CIRC
UIT I-
AUXILIARY
LINE
CIRCUIT
MORRIS CENTRAL OFFICE
ESS
INDICATOR
SIGNAL
TRUNK
(a) VISIBLE SYSTEM
.CONDUCTOR LOOP
CUSTOMER'S PREMISES
ATTENDANTS TELEPHONE SET
MORRIS CENTRAL OFFICE
ANNOUNCEMENT TRUNK
ANNOUNCEMENT FRAME
(REGULAR AND STAND-BY)
(b) AUDIBLE SYSTEM
FIG. 16-1. Attended CGS, block diagram.
348
Customer Group Service and Bridged Extension Service Chap. 16
FIG. 16-2. Attendant's telephone set.
called station further, it will then be necessary to originate a new call; that is,
to repeat the dialing.
If a customer fails to hang up at the end of a call, this failure results in his
line being held busy and out of service.
"Add-On," "'Hold" and "Pick- Up"
"Add-on," "hold," and "pick-up" services are provided in the same manner
as for unattended CGS.
16 . 2 . 3 Maintenance
The maintenance of CGS service is similar to the maintenance of
other equipment using ESS package units. The package units in trouble are
replaced, and the defective package units are repaired at some central point.
Sec. 16.2
Attended CGS
349
The announcement trunks and the magnetic drum amplifiers associated with
them are similarly maintained by replacing defective units with good units.
The magnetic drums are tested and recorded as covered in maintenance instruc-
tions KS-16592, Recorder-Reproducers, and ES-1A053-01, sheet B3, An-
nouncement System.
TRANSFER
RELAYS
RECORDING
AND
MONITORING
EQUIPMENT
DRIVE MOTOR
REPRODUCER
TRANSFORMER
FIG. 16-3. Announcement system.
350
Customer Group Service and Bridged Extension Service Chap. 1 6
I
^""■Wk-J,"
V
LAMP CONTROL UNIT
POWER UNIT
FIG. 16-4. Lamp control unit and power unit.
TABLE 16-4. RINGING CODES FOR BRIDGED EXTENSION SERVICE
Station or extension
to be called
Code to be dialed
Rings sounded by
the tone ringer
Main Station
"11"
1
First Extension
"12"
2
Second Extension
"13"
3
Third Extension
"14"
4
Note: Up to eight rings can be provided.
Sec. 16.3 Bridged Extension Service 351
16.3 BRIDGED EXTENSION SERVICE
In the ESS, any telephone extension can be dialed from any other
extension on the same line. The way in which this can be done is explained
as follows.
Suppose that you (the customer) have one main telephone with three ex-
tension telephones. To ring another extension on your line, remove the handset
from the cradle of any of your telephones and dial the digit "1" followed by
"1," "2," "3," or "4," for the extension you are calling. (If you are on a party
line, you will need to dial an additional digit, your party code.)
After you have completed your dialing, hang up your phone to allow the
tone ringer on the dialed extension to ring. Your own tone ringer and the tone
ringers of all the other extensions on your line will ring also. The ringing will
be coded according to the number you have dialed. If you have dialed "13,"
for example, three rings will be sounded. Table 16-4 shows the rings available
from one main telephone with three extension telephones. Up to eight rings
can be provided in bridged extension service.
When the ringing stops, it indicates that the other (called) extension has
been answered. You can now pick up your own handset and proceed with
your conversation.
If the other extension does not answer within a reasonable time, remove
your handset from the cradle for a few seconds to clear the line and stop the
ringing. Then replace the handset on its cradle.
Appendix
Glossary of ESS Technical Terms
The introduction of electronic switching has created a need for appropriate
terms to signify its new concepts, circuits, and other innovations. This glossary
defines the new words and designations used in this book, as well as a number
of technical expressions previously established but not yet in general use. Many
of these definitions have been approved and adopted by the Nomenclature
Committee of the AT&T Company and Bell Telephone Laboratories.
active: (1) The state of a major unit when
it is handling customer traffic or switch-
ing functions. (2) The condition of a
circuit or device when it is producing an
enabling output.
address: Information (usually a number)
that designates a location in a storage
device or equipment unit.
administration center: The part of the
ESS that includes the manual means for
controlling the system. It also includes
certain automatic test equipment, as well
as a recorder for maintenance and traffic
information.
analog: A signal or quantity in one
language or medium that corresponds to
a signal or quantity in another language
or medium.
AND-gate: A switching circuit whose out-
put is a "1" if all of its inputs are in the
"1" state (see "bit"). If any of its inputs
is a "0," its output is a "0."
announcement system: Used with cus-
tomer group service (CGS); it informs the
CGS attendant, via voice announcements,
of the status of a call.
automatic plate processor: A machine
used to develop and process the photo-
graphic information plates used in the
flying spot store.
barrier grid store: A store in which the
memory medium is a barrier grid tube.
binary number system: A number sys-
tem that uses two symbols (usually de-
noted by and 1), with two as its base;
just as the decimal number system uses
ten symbols (0 through 9) with ten as
its base.
bistable: Having two distinct states of
stability.
bit: The binary unit of information. It is
represented by one of two possible condi-
tions, such as: the digit or 1 ; an electri-
cal charge or no electrical charge; or
transparent or opaque spots on a photo-
graphic plate.
buffer circuit: An isolating circuit used
between two other circuits. The signal
distributor is a form of buffer. It accepts
high-speed signals from the central con-
trol and transmits them to devices of
slower speed in trunk circuits.
352
Appendix
Glossary of ESS Technical Terms
353
central control: The part of the ess
that controls the operation of the other
parts through the interpretation of data
in accordance with predetermined in-
structions.
CGS: See "customer group service."
circuit package: A small replaceable
unit, usually in the form of a printed-
wiring board, containing mounted com-
ponents constituting one or more circuits.
clamping: The function of holding some
point of a circuit to a particular voltage.
coaxial cable: A transmission line con-
sisting of two conductors concentric
with, and insulated from, each other.
computer: A machine capable of per-
forming logical operations on data
stored within or presented to it.
concentration marker: The part of the
ESS that uses marking techniques to con-
trol the operation of the concentration
switching network.
concentration switching network:
The switching network used to inter-
connect unequal numbers of communi-
cation channels.
customer group service (cgs): The term
used to indicate PBX service, wiring
plan, or key telephone customer service.
diagnostic test program: A test pro-
gram used to locate faulty circuit opera-
tions within a unit.
digit, least significant: The digit that,
when changed, least affects the magni-
tude of a number. For example, the
units (last) digit in a decimal number is
the least significant, as in 9345.
digit, most significant: The digit that,
when changed, most affects the magni-
tude of a number. For example, in any
decimal number the first number is the
most significant, as in 5892.
diode: A two-electrode device that is a
good conductor for one polarity and a
poor conductor for the opposite polarity.
directed scan: (Also see "supervisory
scan.") A one-at-a-time operation, not
occurring in normal sequential scanning,
in response to a specific order.
distribution marker: The part of the
ESS that uses marking techniques to con-
trol the operation of the distribution
switching network.
distribution switching network: The
switching network used to interconnect
approximately equal-sized groups of
communication channels.
double-rail: See "twin-rail."
electrostatic storage tube: A cathode-
ray tube having a mica-plate target on
which electrostatic charges (minute de-
posits of electrons) are stored or re-
moved.
enable pulse: A pulse that permits a unit
or circuit to become operative.
error correction: A method of detecting
and correcting single-bit errors in pro-
gram and translation information.
extended area service: Customer calling
distance extended beyond the local area.
firing of a tube: (See "gas diode.") The
breakdown of the gap in a gas-discharge
tube.
flip-flop: A device capable of assuming
two stable states (set or reset) and storing
a bit of information. It remains in either
state until a signal changes it to the
other state.
354
Glossary of ESS Technical Terms
Appendix
flying spot store: A store in which a
cathode-ray tube is used to gain access
to a photographic memory medium.
gas diode: A two-element unit in which
the gas breaks down (the tube fires)
when a required voltage is applied across
the electrodes. The gas discharge creates
an electrical path to transmit the speech
current or to control a connection.
interlock: An electromechanical safety
arrangement that shuts off the high-
voltage supply when certain gates and
doors of cabinets are opened.
junctor: The connecting link between the
A and B sides of the distribution switch-
ing network.
logic: The science of the formal principles
of reasoning.
magnetic core: A toroidal device capable
of storing information by means of its
two directions of polarization.
memory element: Apparatus having the
faculty of retaining one bit of informa-
tion. A relay, a flip-flop, or a spot on a
barrier grid, tube or photographic plate
may act as a memory element.
module: (As used in the switching net-
work.) A plug-in type of package con-
taining components connected together
to form a switch or other circuit.
network : A system of interconnected ele-
ments consisting of such devices as in-
ductors, resistors, capacitors, gas diodes,
etc.
off-hook: The condition that indicates
the active state (loop closed) of a cus-
tomer line.
on-hook: The condition that indicates
the idle state (loop open) of a customer
line.
order: A command or instruction given by
one unit of equipment to another speci-
fying certain functions to be performed.
Such specific functions may be: transfer,
operate, expose, read, write, etc.
OR-gate: A switching circuit whose out-
put is a "1" if any of its inputs is a "1"
(see "bit"); otherwise, a "zero." (Also
see "AND-gate.")
paralleling unit: A unit used to isolate
the outputs of two rectifiers operating in
parallel into a common load; such a unit
contains alarm circuits to indicate the
failure of a rectifier.
parity check: A check on the validity of
a "word." One method is to check the
number of "l's" in a word; for example,
whether the number of "l's" is odd or
even.
photoelectric multiplier tube: A photo-
tube in which the initial photoemission
current is multiplied many times before
being extracted at the anode.
program: An organized set of instruc-
tions.
raster: A predetermined pattern of scan-
ning lines or spots that provide a uniform
covering of a specified area.
read: To extract the information stored
in a memory device.
regenerate: To replace a charge to over-
come decay effects, including any loss of
charge caused by the reading itself.
register: A functionally associated set of
memory elements with or without its
controls and access; a word repository.
See Chapters 8 and 10 for types of
registers.
Appendix
Glossary of ESS Technical Terms
355
remote line concentrator: An outside
plant unit, remotely situated, which ac-
commodates many customer lines and
concentrates them into comparatively
few trunks to the central office.
reset: (Also see "set.") (1) To restore a
storage device to a prescribed state. (2) A
flip-flop reset in one of its two stable
states, namely, the "reset" or "zero"
state.
scanner: The part of the ess that provides
the central control with information ac-
cess to lines, trunks, and test points.
semiconductors : Materials which lie be-
tween metals and insulators in their
ability to conduct electricity.
sequential : A manner of action, or opera-
tion, of equipment in which instructions,
or orders, are set up in a sequence (fol-
lowing a specific space or time pattern),
and are fed consecutively to equipment
during the progress of a switching func-
tion.
serial: A type of action, or operation,
whereby a number or signal is handled
in an orderly arrangement of one item
following another.
set: (Also see "reset.") (1) To place a
storage device in a prescribed state. (2) A
flip-flop set in one of its two stable states,
namely, the "set" or "one" state.
shutter: A mechanical device used to stop
the transmission of light from the photo-
graphic lens inside the flying spot store.
signal distributor: The part of the ess
that provides access from the central
control to one of a large number of out-
puts.
signal switching network: A switching
network interconnecting tone sources
and trunks to supply the tones and
ringing frequencies.
significant: See "digit."
single-rail: (Also see "twin-rail.") A
method of representing the state of a bit,
in which a "1" is represented by a voltage
on a single lead and a "0" is represented
by the absence of a voltage on that lead.
skew ringing connection : A connection
set up when both the calling customer
trunk and the called customer trunk are
on the same side (as contrasted with the
normal opposite sides) of the distribution
switching network.
stages: As used with the distribution
switching network, they are stages 1
through 6 of an electrical transmission
path.
stand-by: The state of a unit when it is
not handling customer switching func-
tions, but ready and able to do so. Units
in the stand-by state may perform check-
ing operations or be matched against the
active units.
stand-by transfer: The part of the ess
that switches duplicated major units be-
tween the active state and the stand-by
state.
store: A unit or device in which informa-
tion is kept until the system is ready to
use it.
supervisory: (Also see "supervisory
scan.") An action or operation that per-
forms a service of inspecting or directing
other actions or operations.
supervisory scan: (Also see "directed
scan.") A one-at-a-time operation, oc-
curring in normal sequential scanning, to
detect disconnects, requests for service,
or routine test results.
356
Glossary of ESS Technical Terms
Appendix
switching networks: The concentration
switching network, the signal switching
network, and the distribution switching
network are collectively called the
switching networks.
time division: A method of allocating a
different time interval for the transmis-
sion of various signals over a common
medium.
tone ringer: Located in the station tele-
phone set, the tone ringer responds to the
different frequencies used with single-
party, two-party, and eight-party lines.
tracking regulator: A voltage regulator
that maintains a preset voltage difference
between its input and output terminals.
transistor: An electronic semiconductor
device with three or more electrodes. It is
used for rectifying and/or amplifying
signals.
trouble: The state of a unit when it is not
available for service: that is, when it is
in neither an active nor a stand-by
condition.
twin-rail: {Also see "single-rail.") A
method of representing the state of a bit,
in which a "1" is represented by a voltage
on one wire of a pair and the absence of
a voltage on the other wire; these voltage
states are reversed to represent a "0."
Sometimes called "double-rail."
word: A set of characters associated to
express system information. (The term
"word" may be prefixed by an adjective
describing the nature of the characters,
as "binary word.")
write: To insert information into a mem-
ory device.
Straley, R De
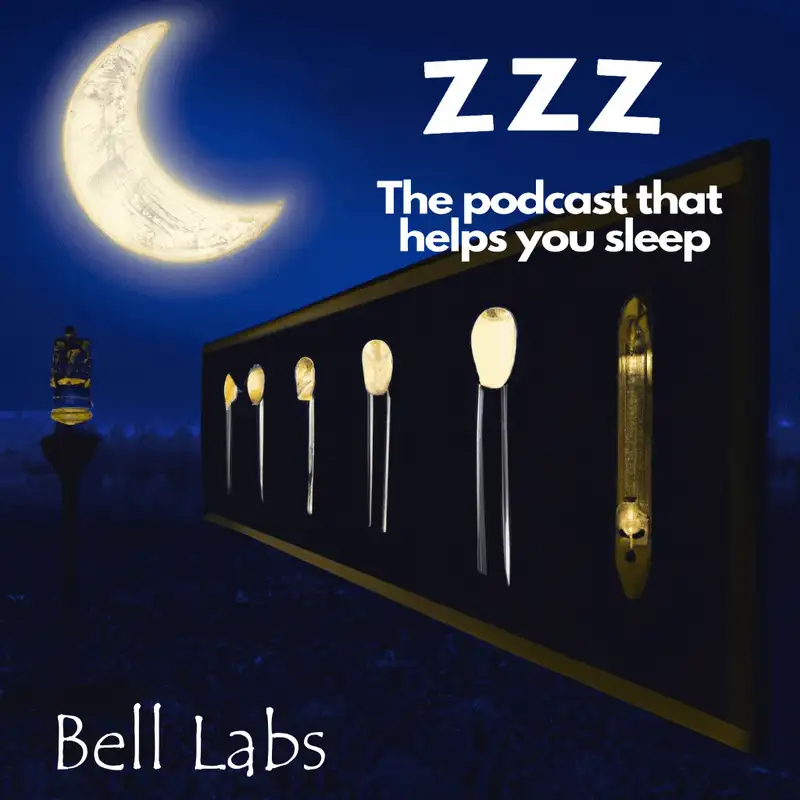